Цикл статей:
Глава 1 — Введение. Цели и задачи исследований.
Глава 2 — Мероприятия по повышению эксплуатационного ресурса крестовин рельсовых пересечений
Глава 3 — Разработка методической базы создания крестовин с запасом металла на износ
Глава 4 — Выбор уравнения для описания формы продольного профиля с запасом металла на износ в пределах зоны перекатывания.
Глава 5 — Сравнительный анализ эффективности работы крестовин с запасом металла на износ и крестовин традиционных конструкций. Заключение.
Анализ современного уровня развития техники и технологий, обеспечивающих реальные повышения эксплуатационных ресурсов объектов техники стрелочного хозяйства, позволил нам выделить три основных направления в решении проблемы увеличения эксплуатационного ресурса крестовин:
- Наплавка крестовин;
- Припуск на самонаклёп;
- Запас металла на износ.
Первое направление обращает на себя внимание своей парадоксальностью. Сегодня никто не сомневается в эффективности наплавки крестовин. Технология наплавки отработана и широко применяется на железных дорогах общего пользования как единая, четко отлаженная система. Но поскольку она практически пе находит применения на путях необщего пользования, мы вынуждены еще раз заострить на неё внимание специалистов, от которых зависит решение этой проблемы.
Наплавка крестовин
Исследования показали, что ремонт крестовин наплавкой позволяет значительно увеличить их долговечность. Наплавку обычно производят для устранения трещин в отливке или восстановления первоначальных очертаний поверхности катания, нарушенных вследствие износа или пластических деформаций, выходящих за пределы установленных допусков. На линиях, где обращаются поезда с высокими осевыми нагрузками, каждая крестовина за время эксплуатации ремонтируется наплавкой несколько раз, начиная с момента, соответствующего примерно одной трети расчетного срока службы.
Учитывая важность продления срока службы крестовин и обеспечения их высокой эксплуатационной надежности, па основании результатов испытаний разработаны технические условия наплавки крестовин из аустенитной марганцовистой стали с использованием наиболее эффективной технологии.
По мере повышения осевых нагрузок срок службы этих элементов сокращается еще больше. Испытания показали, что срок службы глухих пересечений с большим углом входа при осевой нагрузке 30 т соответствует 135 — 270 млн. т брутто пропущенного тоннажа, а при нагрузке 35,4 т — 27 млн. т. [85]
Срок службы крестовин определяется уровнем динамического воздействия и качеством выполнения работ по текущему содержанию и ремонту. Литые сердечники крестовин из аустенитной марганцовистой стали трудно наплавлять, но они обладают высокой работоспособностью. Достаточная вязкость металла повышает стойкость к ударным воздействиям. Повышенная склонность к упрочнению наклепом и высокая износостойкость делают этот сплав предпочтительным для изготовления крестовин. В то же время для этой стали характерны сравнительно низкий предел выносливости, высокое содержание углерода и легирующих компонентов. Вследствие этого на поверхности катания крестовины происходят интенсивные пластические деформации, особенно в начальный период работы. С увеличением осевых нагрузок эти деформации могут развиваться значительно быстрее и выходить за предельные допускаемые величины еще до того, как произойдет упрочнение наклепом поверхности катания крестовины.
Из аустенитной марганцовистой стали трудно отливать крестовины сложной конфигурации. Узкий температурный диапазон твердения способствует образованию дефектов в процессе литья, что в условиях эксплуатации приводит к образованию трещин. Однако высокая ударная вязкость этой стали позволяет сохранить их целостность и работоспособность даже при наличии больших трещин. Так как трещины развиваются медленно, их можно своевременно выявлять и устранять непосредственно в пути, что позволяет экономить затраты на ремонт. С другой стороны, ремонт крестовин непосредственно в пути может оказаться затруднительным из-за термической нестабильности аустенитной структуры металла. Чтобы сердечник не стал хрупким вследствие образования карбида, необходимо ограничить подведение тепла. Кроме того, высокая интенсивность движения на грузонапряженных линиях может затруднить предоставление окон для проведения наплавки с соблюдением требуемой технологии. Поспешный ремонт, в результате которого нарушается структура металла или перегревается сердечник, может привести к преждевременному разрушению наплавленного металла или излому сердечника.
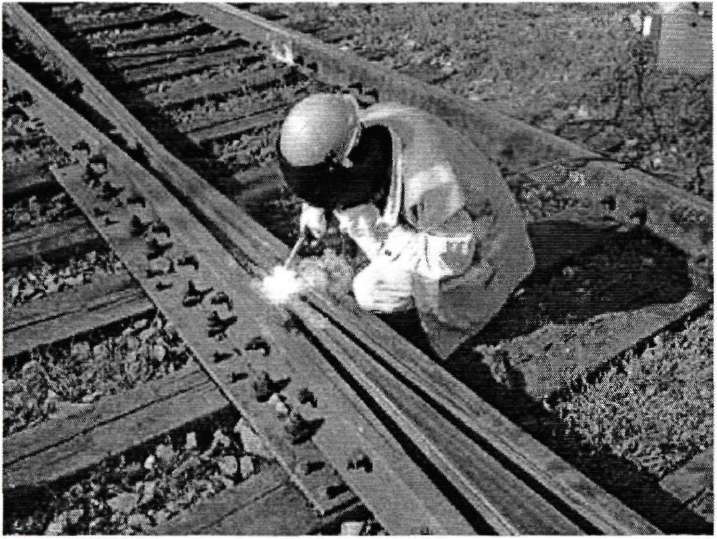
При высоких осевых нагрузках интенсивные пластические деформации аустенитной марганцовистой стали происходят даже после ее упрочнения взрывом. Поэтому большая часть пластических деформаций происходит в первый период эксплуатации вплоть до момента, пока не произойдет механическое упрочнение поверхности катания крестовины под воздействием колес подвижного состава. В связи с этим в указанный период требуются большие объемы работ по шлифованию вновь уложенных или отремонтированных крестовин. Несвоевременное шлифование приводит к образованию наплывов металла и местных неровностей, что способствует возникновению трещин.
Для наплавки лежащих в пути крестовин из аустенитной марганцовистой стали обычно применяют электродуговую сварку металлическим электродом в защитной среде. Этот способ сварки достаточно простой, может выполняться с использованием портативных технических средств и практически нечувствителен к условиям окружающей среды (рис. 2.1). В последние годы широко применяется более эффективный способ электродуговой сварки электродом, покрытым защитным слоем флюса, который используют для наплавки крестовин непосредственно в пути и в стационарных условиях в рельсосварочных цехах.
Для определения наиболее эффективной технологии наплавки крестовин на ряде железных дорог были проведены исследования. Рассматривались результаты лабораторных и эксплуатационных испытаний технологических процессов наплавки, а также характеристики применяемых на этих дорогах материалов. В результате обобщения и анализа полученной информации были сформулированы требования к качеству наплавки, выполнение которых увеличивает эксплуатационную стойкость и срок службы крестовин на линиях с высокими осевыми нагрузками.
В качестве основных требований выдвинуты:
- периодическое обучение операторов для повышения квалификации;
- использование комбинированных источников электроснабжения;
- периодическое шлифование поверхности катания крестовин;
- выработка критериев определения периодичности наплавки крестовин, исключающих необоснованные затраты;
- тщательная подготовка крестовин к ремонту;
- сведение к минимуму теплового воздействия на наплавляемые поверхности;
- тщательный контроль за температурой и деформацией крестовины;
- снятие напряжений в наплавляемых слоях.
Следует шире использовать методы и материалы, позволяющие сократить затраты времени на ремонт крестовин. Применение воздушно- дуговой строжки для снятия поврежденного металла, электродуговой наплавки электродом с защитным слоем флюса, устройств подачи порошковой или цельной проволоки позволяет ускорить процесс наплавки. Для эффективной реализации предложенных требований необходимо провести экономический анализ по каждой линии. В нем следует учесть такие основные факторы, как конструкция стрелочного перевода или глухого пересечения, структура и объем перевозок, а также численность персонала, занятого на текущем содержании пути.
На основании представленных железными дорогами эксплуатационных данных была проведена оценка срока службы новых крестовин до первой наплавки и периодичности последующих. Так, первую наплавку упрочненных крестовин из аустенитной марганцовистой стали в среднем выполняют после пропуска 50 млн. т пропущенного тоннажа, последующие через 30 млн. тонн.
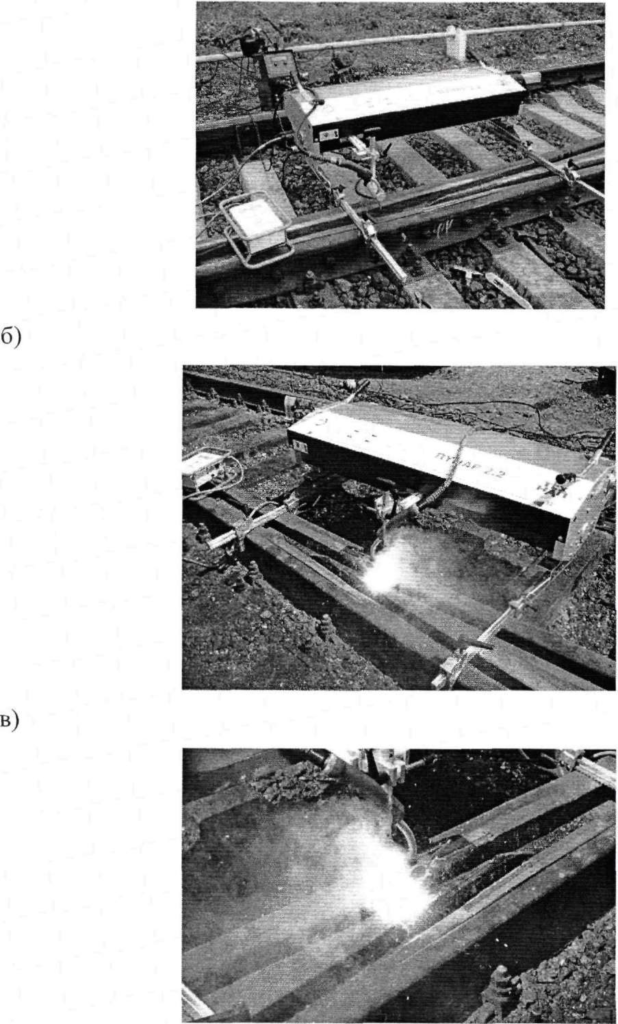
По результатам исследования и анализа информации сделаны следующие выводы:
- около 75 % ремонтов крестовин наплавкой производится из-за образования трещин и выкрашивания металла на поверхности катания;
- так как на грузонапряженных линиях возникают проблемы с выделением окон для ремонта крестовин, в этих случаях целесообразно наплавку производить заранее, на рельсосварочных предприятиях.
- эксплуатационные характеристики крестовин, наплавленных в стационарных условиях, эквивалентны характеристикам новых литых крестовин.
Для стационарной наплавки крестовин непосредственно в пути на дорогах Российской Федерации применяется прибор «Пунар» (рис. 2.2) на износ в наиболее изнашиваемой зоне крестовины. При разработке форм продольного профиля крестовин с запасом на износ одной из приоритетных задач было упрощение конечных формул, описывающих форму продольного профиля.
Технология содержания крестовин в значительной степени зависит от конструкции стрелочных переводов, глухих пересечений и применяемых материалов. Совершенствование конструкции позволяет снизить затраты на содержание и изменить набор технологических операций. На объемы и виды ремонта крестовин оказывают влияние условия эксплуатации. На ряде линий пропускная способность исчерпана, на других близка к этому, так что задержки поездов из-за путевых работ обходятся слишком дорого, поэтому работы по ремонту крестовин в пути приходится ограничивать. Во всех случаях необходимо найти оптимальное, наиболее экономичное сочетание эксплуатационных расходов и капитальных затрат.
Наиболее распространенной сейчас является наплавка непосредственно в пути, хотя эффективна наплавка и в стационарных условиях или в пути на специальных пунктах. К восстановлению наплавкой допускаются крестовины, вертикальный износ усовиков и сердечников которых находится в пределах 6 — 8 мм для главных путей, 8 — 10 мм для приемо-отправочных и 10 — 12 мм для прочих путей. Наплавлять крестовины рекомендуется не более двух раз. Успех от наплавки будет только в том случае, если после ее завершения сердечнику и усовику придать проектное профильное очертание, обеспечивающее спокойный пропуск колес без возбуждении больших дополнительных динамических сил. Несколько выше получается дефектостойкость наплавленного металла, если его наклеп поездами в течение нескольких первых после наплавки дней производится при скоростях до 60 км/ч. В среднем одна наплавка крестовины продлевает срок службы крестовинного узла на 20-30 % [45].
Припуск на самонаклеп
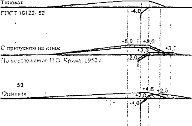
Позитивным шагом в увеличении сроков службы крестовин примерно на 20-25% послужило применение в них припуска на самонаклеп в виде незначительного (на 2-3 мм) возвышения продольного профиля крестовины в
пределах участка между её практическим центром (п.ц.к.) и сечением сердечника, равным 40 мм с отводами этого возвышения к границам зоны перекатывания. [55]
Первоначально в 1952 году продольный профиль для сборных крестовин с литым сердечником имел вид, представленный на рис. 2.3а. В соответствии с этим профилем уровень поверхности катания сердечника соответствовал уровню катания по верху головки рельса от хвостовой части до сечения 20 мм, далее он понижался к сечению 12 мм до отметки 4 мм и еще далее понижался до уровня дна желоба в сечении МЦК (математический центр крестовины) [31]. Продольный профиль усовиков (по линии врезки), начиная от нулевого уровня, т.е. уровня верха головки рельса в горле крестовины имел постепенное повышение до +5,0 мм против сечения МЦК, далее это повышение сохранялось до сечения, расположенного против толщины сердечника 20 мм, и затем повышение опускалось на исходный уровень нулевой отметки в сечении, расположенном против толщины сердечника 35 мм. Уклон отвода повышения усовика па участке от горла до сечения МЦК составлял 0,007. Отвод повышения усовика на участке от сечения 20 мм до сечения 35 мм сердечника выполнялся с уклоном 0,030.
Такое исполнение продольного профиля крестовины просуществовало довольно долго вначале в качестве отраслевого стандарта, а затем оно было узаконено Государственным стандартом ГОСТ 10122-62. Исследованиями, однако, были выявлены существенные недостатки типового продольного профиля. Первый из них заключался в том, что этот профиль предусматривал хорошие условия перекатывания колес по крестовине только в первоначальный период, однако уже вскоре происходит смятие и износ тонких сечений сердечника и узких опорных площадок усовиков в зоне перекатывания, и вследствие этого резко ухудшается траектория перекатывания колес в зоне перехода с усовика на сердечник, приобретая здесь не плавные очертания, а вид локальной впадины или синусоидальной неровности. Второй недостаток заключался в практической невозможности получения проектного профиля на заводском станочном оборудовании. И третий недостаток состоял в том, что, стремясь соблюсти проектный продольный профиль и обеспечить проектный радиус боковой выкружки головки г = 13 мм от поверхности катания к боковой грани сердечника на всем протяжении сердечника, проектировщики и изготовители создали в результате мало работоспособный сердечник в тонких его сечениях, особенно от зоны сечения 20 мм до сечения 12 мм (см. рис. 2.4). Таким образом, выявилась необходимость совершенствования продольного профиля ГОСТ 10122-62.
Суть предложения заключалась в припуске металла на износ 3 мм (против обычного профиля) как на усовике так и на сердечнике в зоне от начала врезки усовиков (у горла) до сечения сердечника, равного полной ширине головки рельса. Предложение было осуществлено на крестовинах типа Р43 марки 1/9 с литым сердечником типа общей отливки с изнашиваемыми частями усовиков. Однако эта конструкция не нашла практического применения, по причине образования в процессе износа более неблагоприятной траектории перекатывания, чем на типовой крестовине. Наблюдения за работой этих крестовин показали, что предложение не учитывает весьма важной особенности развития неровности на крестовине. Особенность заключается в том, что износ крестовины и развитие неровности имеет ярко выраженный локальный характер с наибольшей глубиной в тонких сечениях сердечника 10-30 мм.
В 1966 г. профессора ЛИИЖТа Яковлев В.Ф., Амелин C.B., Смирнов М.П. совместно с ПТКБ ЦП МПС (Елсаков H.H.) предложили новый продольный профиль крестовины с припуском «на самонаклеп» металла. Притом наклеп металла предусматривался только в зоне тонких сечений сердечника (рис. 2.3-в). Суть предложения заключалась в том, что для «самонаклепа» сердечника (без потери его высоты в зоне сечения 40 мм) авторами было предложено изменить продольный профиль сердечника крестовины, создав дополнительный запас металла в зоне локального износа. Предложенный профиль характеризовался тем, что сердечник в зоне сечений от 20 до 30 мм повышался относительно существующего проектного положения на величину 2.0 * 2.5 мм, имея прямолинейные отводы к практическому острию и сечению 60 мм.
С позиций теории износа идея припуска «на самонаклеп» заключается в том, что используется свойство высокомарганцовистой стали (из которой изготавливаются литые сердечники и крестовины) к упрочнению при нагрузке обжатия. Металл поверхностных слоев в тонких сечениях сердечника под действием высоких контактных нагрузок формируется и упрочняется, и в результате после смятия верхних поверхностных слоев при выходе на генеральный уровень катания колеса подвижного состава взаимодействуют уже с более плотным износостойким металлом. Таким образом обеспечивается повышение срока службы сердечников крестовин.
По профилю с припуском «на самонаклеп» в 1971 г. была изготовлена опытная партия крестовин типа Р65 марки 1/11 и уложена в путь для испытаний. Анализ траекторий перекатывания колес по крестовине, имеющей припуск на наклеп показал, что новый профиль не вызывает увеличения сил взаимодействия по сравнению с новыми крестовинами имеющими типовой профиль. Результаты расчетов сил взаимодействия системы «колесо-рельс» при движении подвижного состава по неровностям типовой крестовин и крестовин с припуском на наклеп, выполненные на ЭВМ подтвердили, что с точки зрения силовой оценки припуск на наклеп не ухудшает условий взаимодействия колес и крестовин в зонах неровностей, образующихся при перекатывании колес с усовиков на сердечник.
В период проведения испытаний крестовин с припуском «на наклеп» в 1967 г. было выдвинуто еще одно предложение нового продольного профиля руководителем стрелочной лаборатории ВНИИЖТ к.т.н. H.H. Путрей. В этом предложении была сохранена идея «припуска на самонаклеп» в сердечнике и несколько изменен профиль повышения усовика до + 8,0 мм в сечениях 12 мм и 20 мм сердечника с отводами этого повышения от сечения 12 мм к началу врезки литых усовиков и от сечения 20 мм к сечению сердечника, равному полной ширине головки рельса. Это предложение не получило практического внедрения, однако в результате в 1972 г. появилась новая редакция отраслевого стандарта на продольный профиль крестовин ГОСТ 10122-72, которая предусматривала его исполнение по варианту (рис. 2.3-г). По этой редакции, которая была внесена и в рабочие чертежи, предусматривалось делать повышение усовика величиной + 5,7 мм против сечения 20 мм сердечника с отводом его к началу врезки литых усовиков и сечению 35 мм сердечника. Продольный профиль сердечника остался неизменным по сравнению с ГОСТ 10122-62. По профилю стандарта ГОСТ 10122-72 крестовины изготавливались вплоть до 1978 г., когда был введен новый отраслевой стандарт ОСТ 32.11-78 (рис. 2.3-д), имеющий лишь отличия по ординате в наивысшей точке повышения сердечника +6,3 мм против сечения 20 мм сердечника, вместо прежней ординаты +5,7 мм. Кроме того, исполнение по профилю 1978 г. предусматривало улучшение поперечного профиля сердечника в тонких сечениях (от сечения 20 мм до 12 мм) посредством замены радиусной выкружки г 13 мм при переходе от плоскости катания к боковому рабочему канту на г = 5 мм, за счет чего работоспособность тонких сечений сердечника конечно увеличилась.
Оба профиля 1972 г. и 1978 г. имели положительное качество в том, что улучшали по сравнению с профилем ГОСТ 10122-62 плавность отвода усовиков в сторону горла, однако оба эти профиля не предусматривали припуска «на наклеп» сердечника в тонких его сечениях, повышающего работоспособность этих сечений, в чем и состоял главный недостаток этих профилей.
И, наконец, в 1983 г. был введен в действие новый продольный профиль по отраслевому стандарту ОСТ 32.51-83 (рис. 2.3-е). Этот профиль учел, наконец, все недостатки первоначального продольного профиля 1950-х и 60- х годов. В том числе, не только была уположена плавность отвода усовиков на участке от сечения 20 мм сердечника до начала врезки литых усовиков, где продольный уклон составил менее 0,007, но одновременно в этом профиле был предусмотрен припуск «на самонаклеп» сердечника в соответствии с предложением ЛИИЖТ.
Несколько позднее появился отраслевой стандарт ОСТ 32.51-83с (рис. 2.3-ж) с криволинейным очертанием профиля усовика, который более правильно отражал реальную форму усовика, с учетом заводской технологии строжки.
В конце 80-х годов прошлого века вышел ГОСТ 28370-89 [73] (рис.2.3- з). Этот профиль незначительно отличается от предыдущего ОСТ 32.51-83с. Он зарекомендовал себя как наиболее работоспособный по сравнению с предшествующими профилями ОСТ 32.1 1-78 и ГОСТ 10122-62.
В настоящее время крестовины для железных дорог Российской Федерации выпускаются с продольным профилем согласно ОСТ 32.89-97 (рис. 2.5), пункт 3.4, которого содержит «поверхность катания сердечника представляет собой плавную кривую с максимальным возвышением в сечении сердечника 20 и 30 мм. Форма поверхности катания крестовины обеспечивается технологией изготовления» [80].
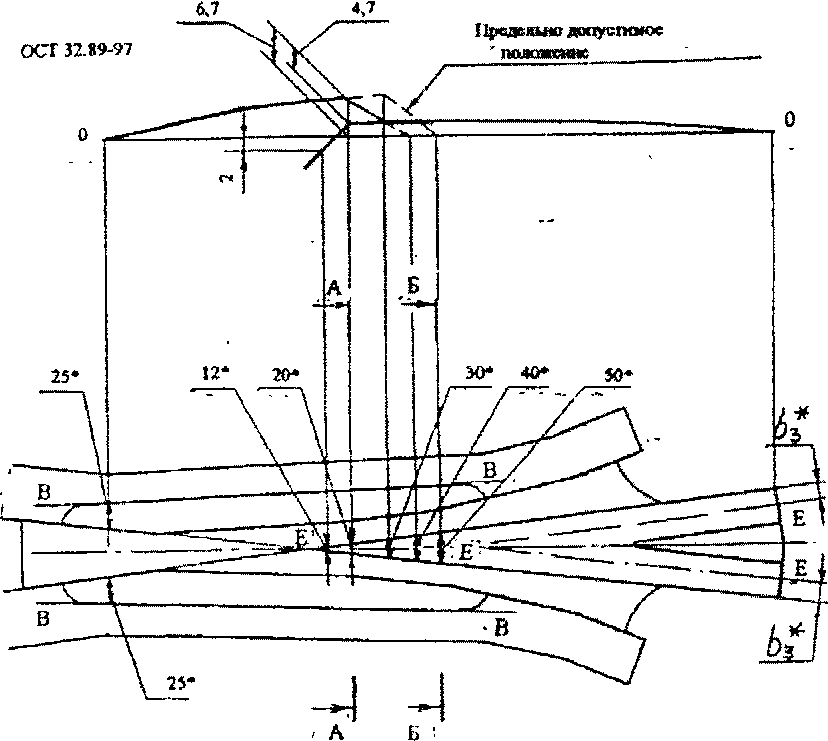
Рисунок 2.5 — Продольный профиль крестовины согласно ОСТ 32.89-97
Это условие не соблюдается, и продольный профиль сердечника серийно выпускаемых крестовин наибольшее возвышение имеет в сечениях более мощных, чем 30 мм (рис. 2.6), что приводит к неравномерному износу поверхности катания, образованию локальных неровностей и появлению отмеченных дефектов [7].
Специалистами ТТГУПС были проведены исследования 30 серийных крестовин проекта 2768 ВВ производства Новосибирского стрелочного завода, упрочненных взрывом. Измерения показали, что 55 % крестовин в сечении сердечника 12 мм имеют высоту сердечника от -0,5 до +1,5 мм относительно головки рельсовых усовиков при норме -2 мм с допусками + 1,5 мм и -0,5 мм по ОСТ 32.89-97.
Установлено, что увеличение высоты сердечника в сечении 12 мм в указанных пределах положительно сказывается на износостойкости и дефектостойкости крестовины в начальный период ее работы (рис. 2.6). Полученные данные позволили рекомендовать увеличить высоту сердечника в сечении 12 мм на 2 мм, а для предупреждения возникновения локальных неровностей на сердечнике в более мощных сечениях дополнительно ввести контроль высоты сердечника в сечении 60 мм на уровне 1 мм выше головки рельсовых усовиков (рис. 2.7).
В 2004 г. на главные пути Октябрьской дороги уложили пять опытных крестовин проекта 2768 ВВ с продольным профилем, предложенным ПГУПСом, изготовленных Новосибирским стрелочным заводом [7].
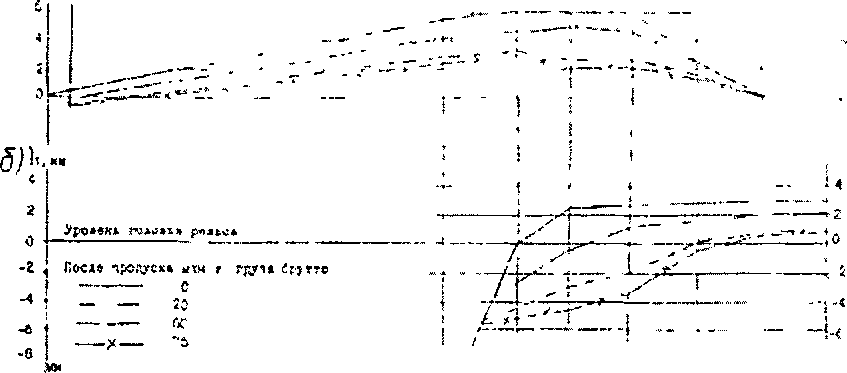
Рисунок 2.6 — Изменение продольного профиля поверхности крестовин типа Р65 марки 1/11 проекта 2768 ВВ по мере наработки тоннажа: а) усовик прямого направления на расстоянии ‘А ширины литой части головки от боковой рабочей грани; б) сердечник по оси симметрии
Сравнительный анализ профилей опытной партии крестовин и крестовин серийного производства после пропуска 75 млн. т груза брутто в аналогичных условиях эксплуатации показал, что на крестовинах серийного производства уклоны неровностей составляют 11-26%. По мере дальнейшей наработки уклоны неровностей в сечениях сердечника 30-40 мм увеличиваются, и на 50 % крестовин обследованной партии образуется дефект ДС. 14.2.
На опытных крестовинах уклоны продольного профиля сердечника в зоне перекатывания на усовик не превышают 9-12 %о, что связано со снижением интенсивности износа в зоне сечений 30-40 мм. Дефекты на поверхности катания сердечника и усовиков отсутствуют.
Л аким образом, предложенные изменения продольного профиля сердечника позволяют продлить срок службы крестовин стрелочных переводов типа Р65 марки 1/11 в 1,3-1,5 раза при эксплуатации их на железобетонных брусьях. На промышленных железных дорогах, где чаще стрелочные переводы укладываются на деревянных брусьях, этот показатель будет выше за счет уменьшения контактных напряжений между колесами подвижного состава и поверхностью крестовины, вызванных жесткостью подрельсового основания. [7]
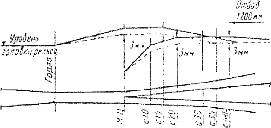
Запас металла на износ
В 60-х годах прошлого века по предложению В.Ф. Яковлева [48] на ряде дорог в пути были уложены крестовины, у которых поверхность катания приподнята на 3 мм (рис. 2.8) по сравнению с нормальным профилем. Профиль крестовины с припуском на самонаклёп.
Рисунок 2.8 — Профиль крестовины с припуском на самонаклёп
Предполагалось, что такой припуск металла явится запасом на износ, благодаря чему крестовины будут служить значительно дольше.
Наблюдения за крестовинами, произведенные бюро пути ЛИИЖТа, показали, что их износ происходил по длине неравномерно. Наиболее интенсивно изнашивался сердечник в сечении 20 мм (см. с 20 на рис. 1). Такой неравномерный износ приводил к образованию местной впадины на поверхности катания рельсовой нити, так называемой геометрической неровности пути.
Глубина и форма впадины зависят от величины вертикального износа, а также от конструкции и марки крестовины. Преодолеваемая колесом впадина зависит также от формы и степени износа бандажа и от положения его в плане.
Рисунок 2.8 — Профиль крестовины с припуском на самонаклёп При проходе колеса по изношенной крестовине происходит явление, подобное просадкам или толчкам, при которых, как известно, наблюдаются усиленные расстройства пути.
Наблюдения показали, что в связи с наличием припуска, практически являющегося «горбом» на поверхности катания рельсовой нити, такие крестовины изнашивались больше, чем с обычным продольным профилем.
Так, при пропуске первых 3-4 млн. тонн брутто груза износ сердечников и усовиков происходил в 2 — 4 раза интенсивнее, чем в крестовинах нормального профиля. Явление более интенсивного износа их продолжается и при дальнейшей эксплуатации.
В среднем интенсивность износа по высоте на каждый 1 млн. тонн брутто груза составила в крестовинах с обычным профилем по сердечникам 0,055 мм и по усовикам 0,062 мм, а в крестовинах с приподнятой поверхностью катания — по сердечникам 0,070 мм и по усовикам — 0,100 мм.
Причина неудачи заключалась в том, что форма возвышения не учитывала неравномерность распределения интенсивности износа в пределах самого участка перекатывания. В средней его части вертикальный износ металла происходил быстрее, чем по границам зоны перекатывания с образованием впадины. Колесу подвижного состава, входящему на этот участок, приходилось преодолевать сначала неровность типа «бугор».
Обобщая разделы 2.1, 2.2, 2.3, следует подчеркнуть, что описанные в них направления повышения сроков службы крестовин являются не взаимоисключающими, а взаимодополняющими друг друга. Своевременно ставить вопрос о получении суммарного эффекта в достижении поставленной цели от одновременного использования всех трех рассматриваемых направлений.
Однако в отличие от первых двух направлений, по которым накоплен многолетний опыт эксплуатации, третье из них находится в стадии становления и не готово к массовому использованию. Тем актуальнее выполнение внедренческой программы, предусматривающей последовательную разработку трех этапов:
- I. Научное обоснование продольных и поперечных профилей крестовин с запасом металла на износ для промышленных железных дорог.
- Проектирование, изготовление и эксплуатационные испытания опытных образцов стрелочных переводов с крестовинами, имеющими запасы металла на износ.
- Доработка конструкций крестовин по результатам испытаний до уровня, соответствующего требованиям их серийного производства.
В данном отчёте представлены результаты законченного I этапа исследований, выполненного автором в рамках тематики кафедры, направленной на повышение сроков службы крестовин заводских стрелочных переводов и глухих пересечений.
Выводы по главе
- Наиболее распространенным мероприятием по повышению эксплуатационного ресурса крестовин является наплавка непосредственно в пути, хотя эффективна наплавка и в стационарных условиях или в пути на специальных пунктах. Одна наплавка увеличивает ресурс крестовины на 2030 %.
- Применение припуска на самонаклеп усовиков и сердечников в зоне перекатывания колес позволяет увеличить эксплуатационный ресурс крестовины в среднем на 20-25%. Последние предложения ПГУПС [7] по проектированию продольного профиля с припуском на самонаклеп позволили увеличить срок службы в 1,5 раза.
- Мероприятие по увеличению эксплуатационного ресурса крестовины, связанное с создание дополнительного запаса металла на износ в наиболее изнашиваемой зоне является наиболее неизученным. Но именно запас металла на износ, по мнению автора, является наиболее перспективным направлением в разработке конструкции крестовины, обладающей эксплуатационным ресурсом вдвое большим, по сравнению с традиционными конструкциями.