- Прокаливаемость остряков из сталей марок 76ХСФ и М73В
- Механические свойства остряков из сталей 76ХСФ и М73В
- Макро- и микроструктура остряков из сталей марок 76ХСФ и М73В
- Исследование неметаллических включений в сталях 76ХСФ и М73В
- Сравнительные испытания на износ
- Испытания на циклическую долговечность
- Выводы
Цикл статей:
Глава 1 — Введение. Цели и задачи исследований.
Глава 2 — Анализ причин отказов стрелочных переводов и их элементов
Глава 3 — Материалы и методика исследования
Глава 4 — Сравнительные исследования комплекса физико- механических свойств остряков из сталей марок 76хсф и м73в
Глава 5 — Разработка технологических основ двухстороннего поверхностного упрочнения остряков
Глава 6 — Работы по промышленному внедрению стали 76ХСФ и технологии двухстороннего термического упрочнения остряков
Анализ возможности повышения толщины закаленного слоя на стали М73В
Одним из путей повышения прочности остряков по сечению и увеличения его сопротивления изгибающим нагрузкам является увеличение толщины закаленного слоя в головке остряка.
Совместно со специалистами ОАО «МСЗ» были проведены эксперименты по увеличению толщины закаленного слоя на остряках из стали М73В в рамках существующей технологии их термической обработки путем повышения температуры индукционного нагрева под закалку с 850 до — 1050°С.
Результаты исследования механических свойств в сравнении с требованиями ТУ 32 ЦТВР-463-81 приведены в таблице 3.1.
Таблица 3.1 Механические свойства и ударная вязкость закаленного слоя остряков
Образцы | а, МПА | 2, МПА | 5% | У, МПА | KCU, МДЖ/м2 |
---|---|---|---|---|---|
«1050 иС» | 1142 | 809 | 13 | 45 | 0,41 |
«850 °С» | 1203 | 818 | 12 | 45 | 0,37 |
ТУ | |||||
32ЦТВР 463-81 | 1078 | 735 | 8 | 20 | 0,22 |
Примечание. В таблице приведены средние значения механических свойств и ударной вязкости, определенные по результатам 10 испытаний. Погрешность результатов не превышает 10 %.
Анализ данных табл. 3.1 показывает, что существенного влияния увеличения температуры нагрева под закалку на уровень механических свойств не наблюдается.
Исследование твердости поверхности катания остряков показало, что средняя по результатам 10 замеров твердость остряка с температурой закалки 1050 °С составила HB 396, а с температурой закалки 850 °С — HB 388.
Исследование влияния повышения температуры нагрева под закалку на глубину упрочненного слоя с твердостью не менее HRC 31 показало, что в полном сечении остряка (68,4 мм) глубина закаленного слоя составила: для 1050 °С — 10,5 мм по оси, 14,0 мм по рабочей выкружке и 15,0 мм по внешней выкружке; для 850 иС — 8,5 мм по оси, 12,5 мм по рабочей выкружке и 12,0 мм по внешней выкружке. Однако стабильного повышения глубины закаленного слоя по всей длине остряка, в сечениях различной ширины получить не удалось.
Увеличение температуры нагрева под закалку отрицательно сказалось на микроструктуре упрочненного слоя. Как показали результаты металлографических исследований, размер зерна в поверхностных слоях увеличился с 9 по 4 балл стандартной шкалы ГОСТ 5639; в микроструктуре некоторых образцов, нагретых до 1050 °С , был обнаружен видманштеттов феррит как следствие перегрева (рис. 3.1). Как в опытных, так и в серийных остряках в закаленном слое был обнаружен мартенсит, микротвердость которого составила 5900 МПа при микротвердости основной структуры упрочненного слоя — сорбита закалки — 3420 МПа. Опытные остряки характеризуются более высокой плотностью распределения участков мартенсита в закаленном слое (рис. 3.2).
Микроструктура в закаленном слое опытного и серийного остряков
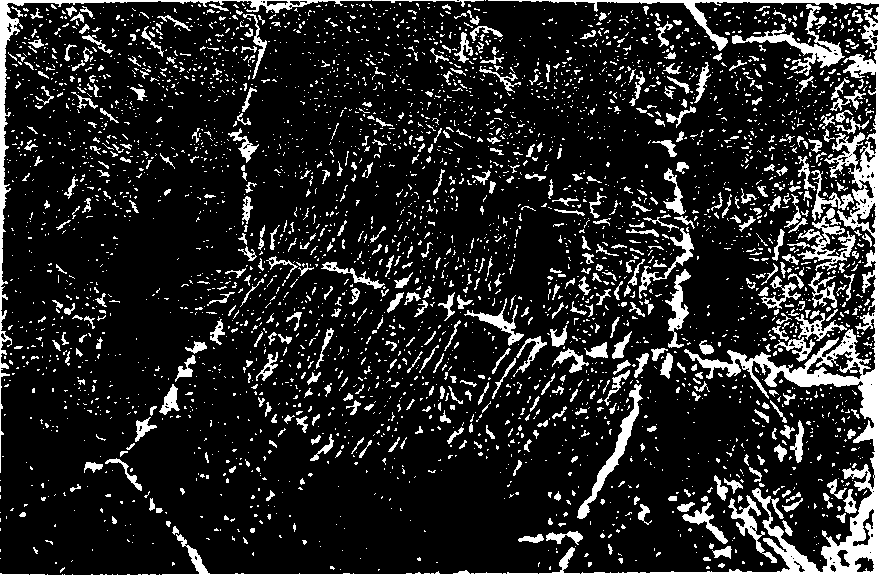
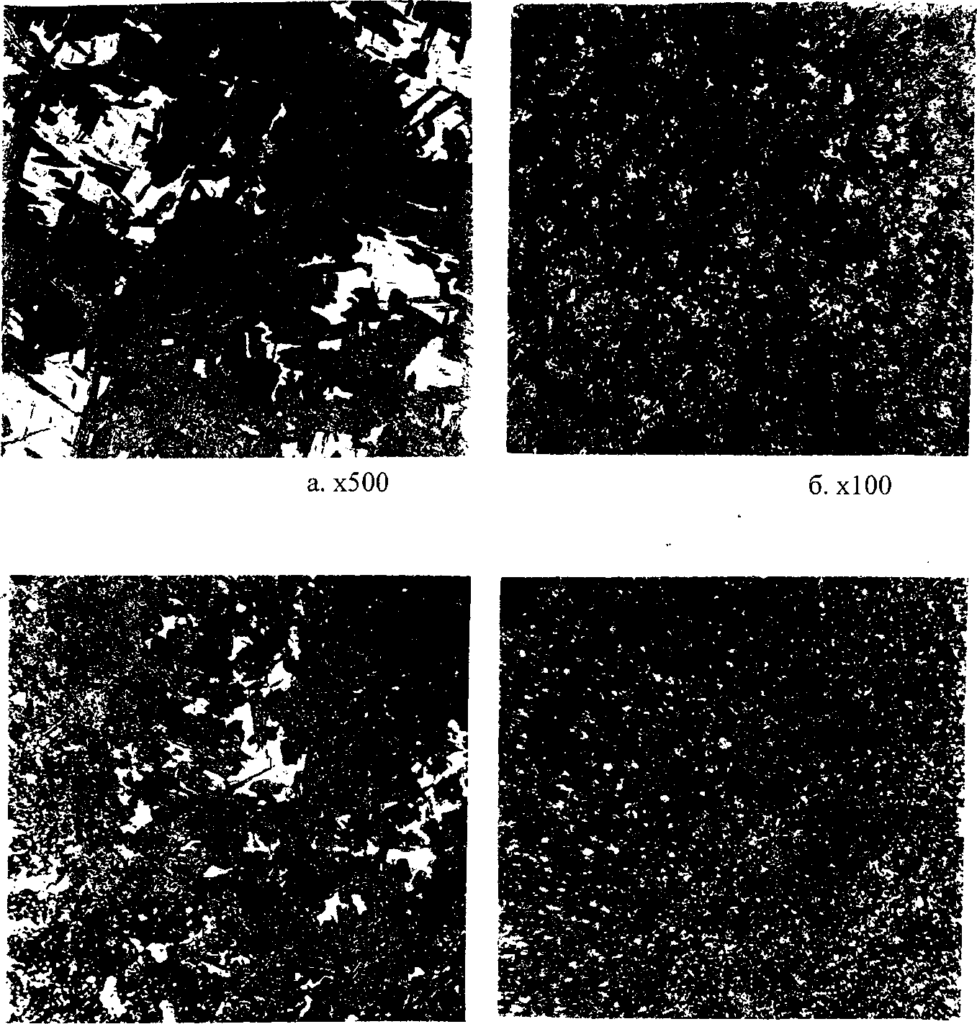
Таким образом, результаты проведенных экспериментов дают основание утверждать, что изменение отдельных параметров режима термической обработки не могут привести к реальному устойчивому повышению твердости поверхности, глубины закаленного слоя и прочностных характеристик по сечению остряка по причине недостаточной прокаливаемости стали серийной марки и фактической выработки ресурса ее упрочнения в рамках используемой технологии термической обработки.
Прокаливаемость остряков из сталей марок 76ХСФ и М73В
Экспериментальное определение прокаливаемости
Как указывалось ранее, повышение толщины закаленного слоя в головке остряка является одним из аспектов увеличения прочностных свойств и повышения эксплуатационной стойкости изделия.
Результаты определения прокаливаемости сталей марок М73В и 76ХСФ на цилиндрических образцах представлены на рис. 3.3.
Анализ кривых распределения твердости (рис. 3.3), построенных с учетом полей допусков (по десяти образцам для каждой марки стали), показывает, что прокаливаемость стали 76ХСФ, оцененная по твердости полумартенситной зоны (590 НУ10(Н11С 53) [96]), составляет 8-10 мм против 5-6 мм для стали М73В (твердость полумартенситной зоны — 590 НУю (НЯС 53) [96]), то есть превышает прокаливаемость стали серийной марки в 1,6 раза. В пределах закаленного слоя на .одинаковом расстоянии от охлаждаемого торца цилиндрических образцов твердость стали 76ХСФ превышает твердость стали стандартной марки с учетом полей допусков (рис. 3.3), что говорит о более высокой закаливаемости стали с повышенным содержанием хрома, при данных условиях охлаждения образцов.
Кривые прокаливаемости опытной и серийной марки стали
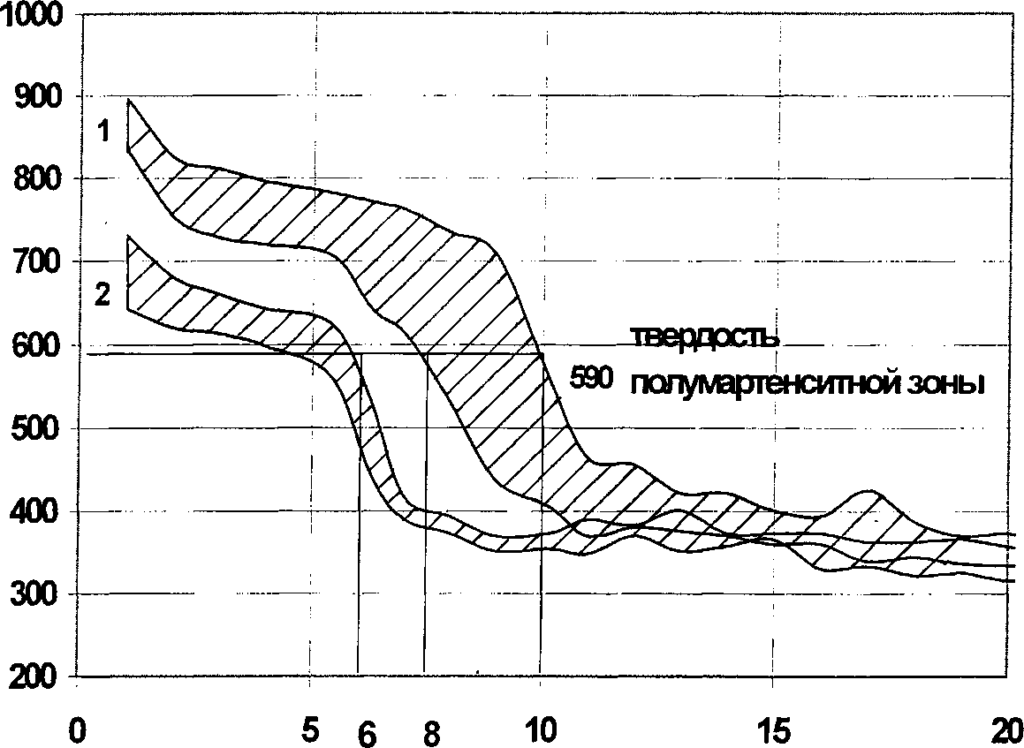
1- 76ХСФ; 2- М73В
Увеличение прокаливаемости и закаливаемости, полученное в результате эксперимента на торцевых образцах из стали 76ХСФ, дало основание для пересмотра режима закалки остряков из стали 76ХСФ.
Ввиду невозможности определения скорости потока воздуха при охлаждении поверхности остряков, в данной работе для оценки интенсивности закалочного охлаждения используется давление воздуха на входе в спрейерное устройство при неизменных суммарной площади отверстий на выходе спрейера 757 мм и расстоянии от спрейера до охлаждаемой поверхности 10-12 мм.
Во избежание образования участков мартенсита в закаленном слое головки остряков давление охлаждающего воздуха было снижено с 0,4 МПа (серийный режим) до 0,05-0,2 МПа (опытный режим) в зависимости от ширины сечения при сохранении остальных параметров режима (мощность индуктора, температура нагрева, скорость перемещения тележки) на прежнем уровне. Опытный и серийный режимы закалки представлены на рис. 3.4.
Оценка прокаливаемости расчетным методом
Результаты расчетов распределения скорости охлаждения по сечению головки (теплотехническая модель — цилиндр диаметром 64 мм) и подошвы (теплотехническая модель — пластина толщиной 20 мм) остряка, выполненных конечно-разностным методом с использованием программы Temps представлены на рис. 3.5.
В табл. 3.2 и 3.3 приведены результаты расчета идеального критического диаметра, а в табл. 3.4 и 3.5 результаты расчета прокаливаемости для сталей М73В и 76ХСФ, соответственно. Расчет проведен по методике американского стандарта SAE-J406. Внешний вид кривых прокаливаемости для цилиндрических образцов приведен на рис.3.6.
Табл 3.2 Расчет идеального критического диаметра (Боо) стали М73В
Элемент | Массовая доля, % | Коэффициент — множитель, 1ГЭ | |
Пределы | Среднестатистические значения | ||
С | 0,67-0,78 | 0,73 | 0,296 |
Мп | 0,75-1,05 | 0,95 | 4,167 |
0,18-0,45 | 0,34 | 1,238 | |
№ | н.б. 0,25 | 0,12 | 1,044 |
Сг | н.б. 0,30 | 0,1 | 1,346 — |
Си | н.б. 0,30 | 0,14 | 1,05 |
V | 0,03-0,06 | 0,05 | 1,09 |
Таблица 3.3 Расчет идеального критического диаметра (Бю) стали 76ХСФ
Элемент | Массовая доля, % | Коэффициент — множитель, ]ГЭ | |
Пределы | Среднестатистические значения | ||
С | 0,69-0,80 | 0,76 | 0,292 |
Мп | 0,70-1,00 | 0,74 | 4 |
0,50-0,70 | 0,54 | 1,42 | |
№ | н.б. 0,25 | 0,12 | 1,044 |
Сг | 0,35-0,55 | 0,48 | 1,972 |
Си | н.б. 0,30 | 0,14 | 1,05 |
V | 0,050,09 | 0,07 | 1,12 |
Расчетные кривые прокаливаемости торцовых образцов
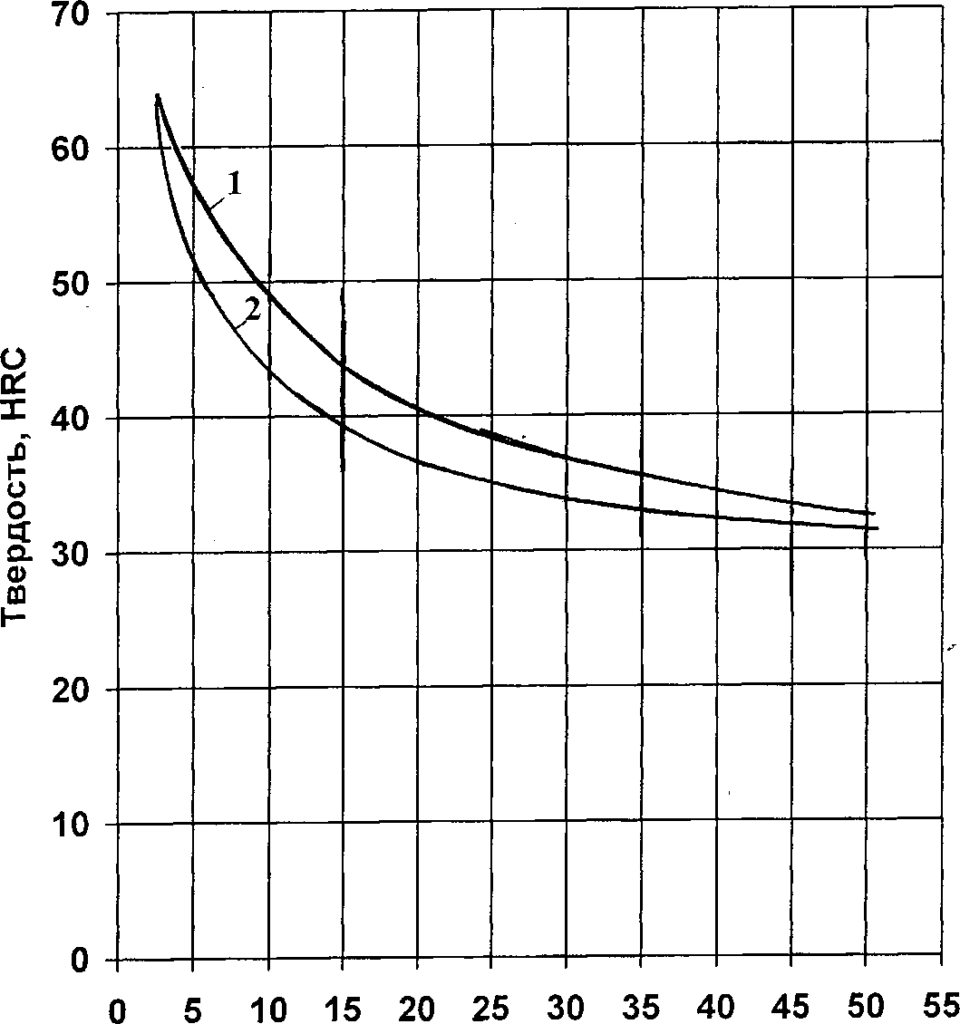
1 — 76ХСФ; 2-М73В
Результаты расчетной оценки распределения твердости в сечении головки и подошвы остряка для двух марок сталей, проведенной на основе полученных выше данных, представлены в табл. 3.6,3.7,3.8и3.9. На рис. 3.9 и 3.10 представлены расчетные кривые распределения твердости в головке и подошве остряков из сталей марок М73В и 76ХСФ
Сопоставление расчетной оценки прокаливаемости сталей М73В и 76ХСФ на стандартных цилиндрических образцах (рис. 3.6) и результатов экспериментального определения прокаливаемости по методу торцовой закалки (рис. 3.3) показывает удовлетворительную для решения поставленных в работе задач точность предложенной расчетной методики. Глубина прокаливаемости стали 76ХСФ, оцененная по твердости зоны, содержащей в структуре 50% мартенсита (590 НУ]0 (НЯС 53) [96]), составляет 8-10 мм по результатам эксперимента и 8 мм по результатам расчета. Для стали М73В (твердость зоны, содержащей 50% мартенсита — 590 НУю (НЯС 53) [96]) глубина прокаливаемости составляет — 5-6 мм по экспериментальным данным и 5 мм по результатам расчета.
Зависимость продолжительности охлаждения в интервале 800 — 500 от расстояния от охлаждаемого торца [96]
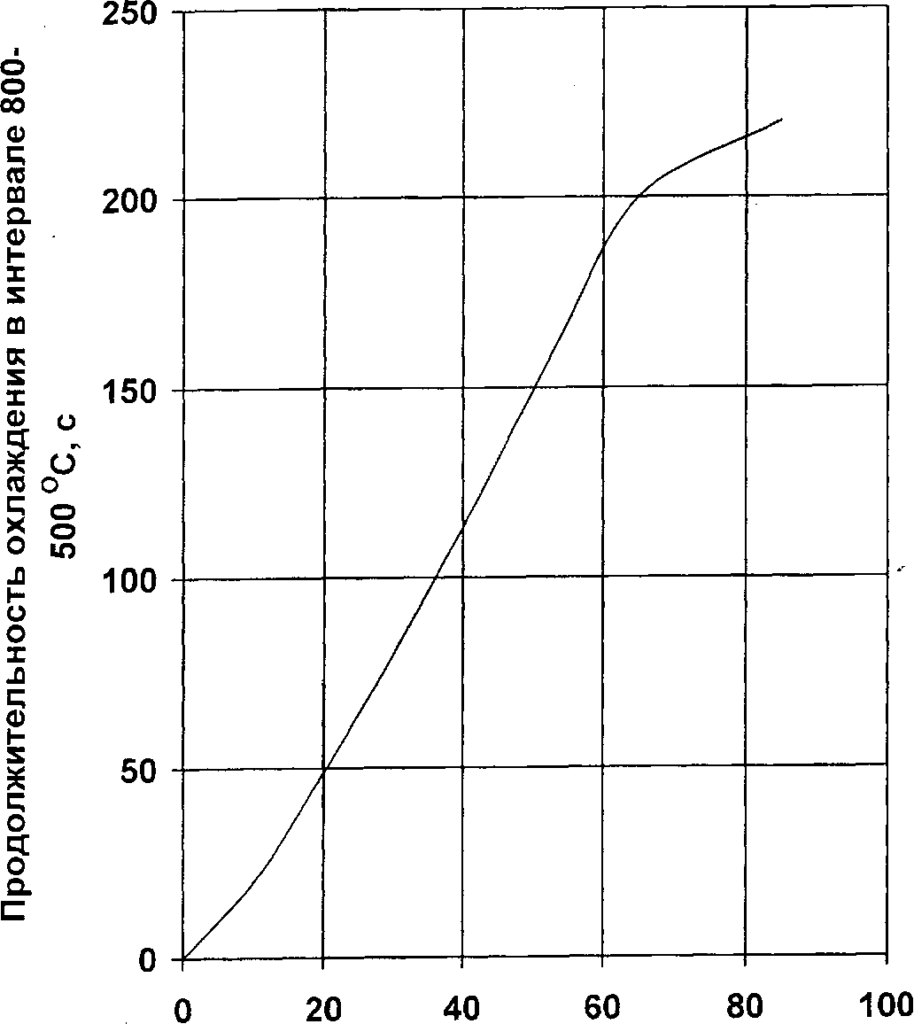
Расчетная оценка твердости по сечению головки остряка из стали М73В
Торцовый образец на прокаливаемость по ГОСТ 5657 | Теплотехническая модель реального изделия | ||
Расстояние от торца, мм | Скорость охлаждения, °С/сек | Твердость, же | Расстояние до зоны с твердостью БЕД при закалке с охлаждением потоком воздуха (а «750 Вт/(м2К) |
6,0 | 47 | 48,5 | — |
7,5 | 31 | 45,3 | — |
9,0 | 21 | 43,6 | — |
10,5 | 17 | 42,3 | — |
12,0 | 13 | 41 | — |
13,5 | 10 | 40,1 | — |
15,0 | 8 | 39,5 | — |
18,0 | 7 | 38,2 | 1 |
24,0 | 5 | 36,9 | >6 |
Торцовый образец на прокаливаемость по ГОСТ 5657 | Теплотехническая модель реального изделия | ||
Расстояние от торца, мм | Скорость охлаждения, °С/сек | Твердость, тс | Расстояние до зоны с твердостью НИД при закалке с охлаждением потоком воздуха (а «750 Вт/(м2К) |
6 | 47 | 48,5 | — |
7,5 | 31 | 45,3 | — |
9 | 21 | 43,6 | — *г |
10,5 | 17 | 42,3 | — |
12 | 13 | 41 | — |
13,5 | 10 | 40,1 | — |
15 | 8 | 39,5 | — |
18 | 7 | 38,2 | — |
24 | 5 | 36,9 | >1 |
Анализ распределения твердости в головке и подошве остряков из стали марок М73В и 76ХСФ (рис. 3.9, 3.10) показывает, что при закалке сжатым воздухом при скорости его подачи на головку — 80 м/с и на подошву — 60 м/с твердость на поверхности катания остряка составляет НЯС 42 для стали 76ХСФ и БИС 39 для стали М73В; твердость на поверхности подошвы — НЯС 39 для стали 76ХСФ и НЯС 37 для стали М73В.
Расчет показал, что при переходе к стали 76ХСФ глубина упрочненного слоя в головке увеличивается на 57% и составляет 11 мм против 7 мм для стали М73В. В подошве глубина упрочненного слоя возрастает на 67% и составляет 5 мм против 3- мм для стали М73В.
Таким образом, результаты расчета прокаливаемости, проведенного по комплексной методике, включающей определение скоростей охлаждения в сечении головки и подошвы остряка путем решения дифференциального уравнения теплопроводности Фурье методом конечно-разностной аппроксимации. — расчет распределения твердости по длине стандартных цилиндрических образцов методом коэффициентов-делителей стандарта 8АЕ 1406 (США) ^построение кривых распределения твердости в головке и подошве остряка, показывают перспективность использования стали 76ХСФ для производства остряков.
Механические свойства остряков из сталей 76ХСФ и М73В
Сравнительное исследование механических свойств и твердости проводили на остряках из сталей марок М73В и 76ХСФ как после закалки ТВЧ, так и без термической обработки. Результаты испытаний представлены в табл. 3.10. Так же в табл. 3.10 приведены нормативные значения механических свойств и твердости, регламентированные требованиями соответствующих ГОСТ и ТУ. ТУ 32 ЦТВР-463-81 «Остряки для стрелок, уравнительных приборов, башмакосбрасывателей и рельсы подвижных сердечников крестовин, закаленные с нагрева токами высокой частоты» разработаны на остряки, упрочняемые индукционной закалкой с выгибом.
Таблица 3.10 Механические свойства и ударная вязкость остряков из сталей 76ХСФ и М73В
76ХСФ, ТВЧ. | 1170 | 835 | 6,4 | 18,1 | 0,12 | 400-410 |
76ХСФ, без Т/О | 1100 | 765 | 5,8 | 16,5 | 0,08 | 350-370 |
М73В, ТВЧ | 1142 | 795 | 11,0 | 40,9 | 0,31 | 340-370 |
М73В, без Т/О | 963 | 560 | 8,3 | 24,3 | 0,15 | 260-280 |
ГОСТ 9960-85 | 900 | — | 5,0 | — | — | — |
ТУ 32 ЦТВР 463 — 81 | 1078 | 735 | 8,0 | 20,0 | 0,22 | 321-388 |
Анализ данных табл. 3.10 показывает, что характеристики прочности и твердость поверхности остряков из стали 76ХСФ без термического упрочнения сопоставимы с аналогичными характеристиками остряков из серийной марки стали М73В, упрочненных индукционной закалкой, и превосходят свойства серийных остряков без термообработки: поверхностная твердость на 32-34 %, временное сопротивление на 14 %, предел текучести на 39 %. Это дает основание для проведения эксплуатационных испытаний остряков из стали 76ХСФ без термической обработки в одинаково жестких с серийными термообработан- ными остряками условиях эксплуатации. Твердость и прочностные характеристики хромистых остряков после индукционной закалки превышают уровень аналогичных свойств остряков из стали М73В после упрочнения: поверхностная твердость на 12 — 17 %, временное сопротивление и предел текучести на 5 %.
Ресурс упрочнения стали 76ХСФ позволяет получить более высокие значения твердости, временного сопротивления и предела текучести при переходе на другие режимы охлаждения сжатым воздухом (увеличение давления воздуха в спрейерном устройстве) или замене воздуха водо-воздушной смесью. Однако установленный предел твердости поверхности катания и прочностных свойств определяется требованиями к пластичности и сопротивлению хрупкому разрушению остряков.
На рис. 3.11 приведены результаты сравнительного исследования распределения твердости в головке остряков из сталей 76ХСФ и М73В термически упрочненных и без термообработки.
Анализ данных рис. 3.11 показывает как увеличение глубины упрочненного слоя с 7 мм (для остряков из стали М73В) до 13 мм (для остряков 76ХСФ), так и повышение максимальной твердости в пределах закаленного слоя с 375 HB до 410 HB в остряках из стали 76ХСФ.
Результаты проведенных исследований показывают возможность значительного повышения поверхностной твердости, глубины и прочностных свойств закаленного слоя при изготовлении остряков из стали 76ХСФ [117, 118, 119].
На рис. 3.12 приведены кривые распределения твердости в рельсах разных производителей, изготовленных и термоупрочненных по различным технологиям. Данные рис. 3.12 показывают высокий уровень твердости остряков, изготовленных по новой технологии в сравнении с широким спектром существующих технологий термоупрочнения рельсов.
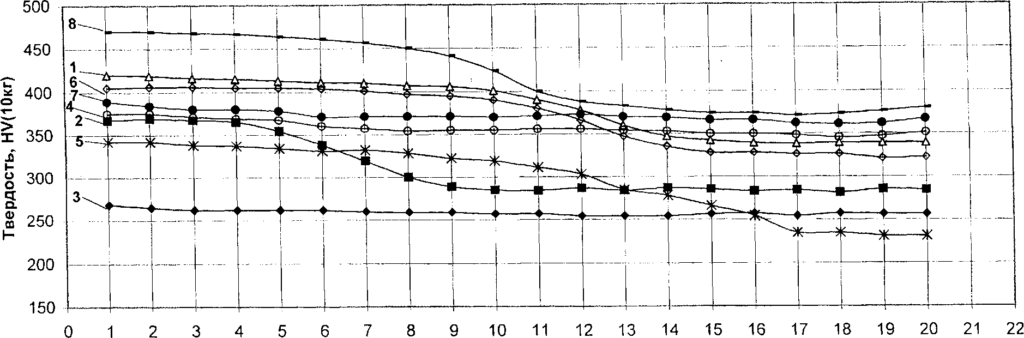
- — сталь 76ХСФ, 0,44% Сг, ТВЧ, РВОЗД=0,2 МПа, НСЗ;
- — сталь М73В, ТВЧ, РВОЗД=0,4 Мпа, НСЗ;
- — сталь М73В, без т/о, ДСЗ (г. Днепропетровск);
- — сталь 76ХСФ, 0,44%Сг, без т/о, НСЗ,
- — сталь М76Т, ТВЧ, охлаждение водо-возд. смесью, «Азовсталь»
- — сталь с 0,45% Сг, двухстор. зак-ка возд. с нагрева
- ТВЧ, 8У8Со (Канада)
- — сталь М76В, объем, зак-ка в масло, НТМК
- — сталь М76В, двухстор. зак-ка быстродвижущимся потоком воды
Макро- и микроструктура остряков из сталей марок 76ХСФ и М73В
Макроструктура остряков из сталей марок М73В и 76ХСФ представлена на рис. 3.13. Конструкция серийного индуктора, использовавшегося при закалке опытных и серийных остряков с выгибом (рис. 3.14), позволяет получать закаленный слой по поверхности катания и выкружкам остряка.
Результаты исследования микроструктуры в различных зонах головки закаленных остряков приведены на рис. 3.15, 3.16.
Анализ данных рис. 3.15 показывает, что в пределах упрочненного слоя головки (до 12 мм от поверхности катания) структура металла остряка из стали 76ХСФ представляет собой троостосорбит закалки (микротвердость Н50=3970- — 4395 МПа) с разрозненными участками феррита, расположенными равномерно в пределах закаленного слоя в виде отдельных конгломератов (рис. 3.15 а). В пределах закаленного слоя в головке остряка из серийной марки стали М73В структура представлена сорбитом закалки (микротвердость Н50=3300-3700 МПа) с разорванной сеткой феррита по границам зерен (рис. 3.16 а).
Подобное изменение морфологии феррита характерно для низколегированных хромом сталей [99]. Структура переходной зоны и сердцевины для двух марок сталей практически идентична: грубодисперсный сорбит с участками перлита в переходной зоне и пластинчатый перлит в сердцевине (рис. 3.15 б, в, 3.16 6, в).
Исследование тонкого строения микроструктур опытных и серийных остряков проводили с использованием РЭМ системы «СатеЬах» при увеличениях х4000 и х10ООО. Результаты исследования, представленные на рис. 3.17, показывают что при идентичности морфологии исследованных структур, наблюдаются отличия в их дисперсности. Так средняя величина межпластиночного расстояния в пределах упрочненного слоя для стали 76ХСФ составляет 0,15 мкм, а для стали М73В — 0,2 мкм.
Межпластиночное расстояние в перлите сердцевины составляет 0,3 мкм для стали 76ХСФ и 0,4 мкм для стали М73В. Получение в хромистой стали более тонкодисперсной структуры объясняется закономерностями влияния хрома на кинетику диффузионного распада аустенита. Увеличивая устойчивость ау- стенита против распада в критическом интервале температур, хром способствует снижению температуры диффузионного распада, что и приводит к получению феррито-цементитной смеси с большей степенью дисперсности [94, 95].
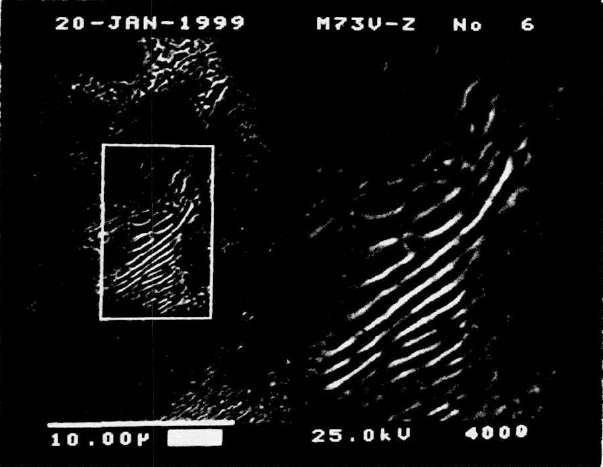
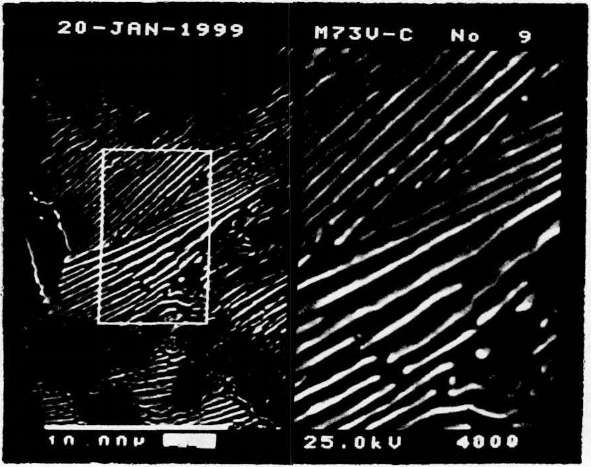
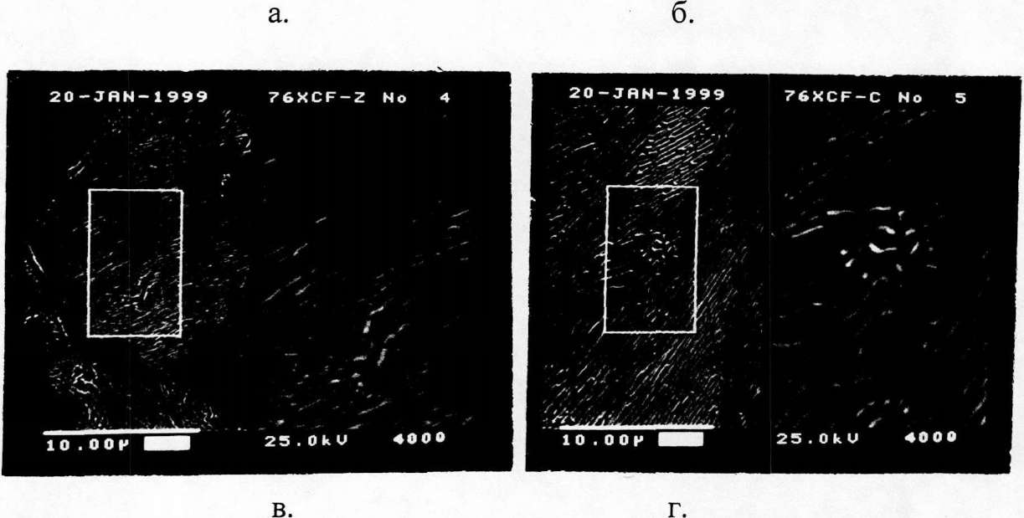
а — М73В, закаленный слой; б — М73В, сердцевина; в — 76ХСФ, закаленный слой; г — 76ХСФ, сердцевина Увеличение х4000 (левый снимок), х 10000 (правый снимок)
Исследование неметаллических включений в сталях 76ХСФ и М73В
Результаты анализа неметаллических включений для сталей М73В и 76ХСФ представлены в табл. 3.11.
Сравнительный анализ данных табл. 3.11 показывает, что по степени загрязненности представленными в таблице включениями сталь 76ХСФ, выплавленная в электродуговой печи на ОАО «КМК», характеризуется более низким качеством, чем сталь серийной марки, выплавленная мартеновским способом. Так средняя длина сульфидной строчки составляет 33,949 и 46,320 мкм; средние суммарные площади, занимаемые включениями данного типа, 117,58 и 160,18 мкм2 для сталей М73В и 76ХСФ соответственно. Загрязненность оксидами алюминия стали новой марки меньше, чем серийной: суммарная площадь включений 196,80 мкм2 для 76ХСФ против 342,09 мкм2 для М73В. Загрязненность оксисульфидами для опытной марки стали существенно выше, чем для серийной. Средняя суммарная площадь включений данного типа составляет 2 2 566,67 мкм для стали 76ХСФ против 21,53 мкм для стали М73В. Загрязненность глобулярными оксидами стали 76ХСФ превышает загрязненность стали М73В практически в 2 раза (средняя суммарная площадь включений — 267,98 мкм2 для 76ХСФ и 126,99 мкм2 для М73В).
Таблица 3.11 Результаты сравнительных исследований неметаллических включений в остряках из сталей М73В и 76ХСФ
Тип включений | М73В, | 76ХСФ | ||
Средняя длина включений, мкм | Средняя суммарная площадь включе- 2 НИИ, мкм | Средняя длина включений, мкм | Средняя суммарная площадь включений, мкм2 | |
Сульфиды строчечные | 33,949 | 117,58 | 46,32 | 160,18 |
Оксиды алюминия | 41,244 | 342,09 | 121,86 | 196,8 |
Оксисульфиды | 10,311 | 21,532 | 60,774 | 566,67 |
Оксиды глобулярные | 13,796 | 126,99 | 20,794 | 267,98 |
СЛ Сталь 76ХСФ выплавлена в электродуговой печи.На рис. 3.18 представлен внешний вид неметаллических включений, характерных для стали 76ХСФ.
Таким образом, проведенное исследование неметаллических включений в сталях опытной и серийной марок показало, что сталь 76ХСФ (плавка 61255-5 ОАО «КМК» в электродуговой печи) характеризуется повышенной по сравнению с серийной маркой М73В (плавка 892-С ОАО «КМК» в мартеновской печи) загрязненностью неметаллическими включениями. Это дает основания ожидать невысокую контактно-усталостную прочность остряков из опытной марки стали.
Сравнительные испытания на износ
Результаты сравнительных испытаний на износ по методу Амслера представлены на рис. 3.19. Анализ данных рис. 3.19 показывает, что при одинаковых условиях испытаний после 70 тысяч оборотов вращения роликов износ роликов из стали 76ХСФ с твердостью HRC 44 составил 0,185 г; износ роликов из стали М73В с твердостью HRC 37 — 0,630 г; износ роликов из стали 76ХСФ с твердостью HRC 37 — 0,602 г.
Как видно из приведенных выше данных, в рамках проведенного эксперимента износостойкость образцов «хромистых» остряков без термической обработки примерно одинакова с износостойкостью образцов остряков из серийной марки стали М73В после индукционной закалки. Это дает основание для проведения эксплуатационных испытаний «хромистых» остряков без термического упрочнения.
На рис. 3.20 показан внешний вид поверхности износа роликов из остряков трех испытанных типов. В соответствии с классификацией режимов износа, представленной в [109], износ всех испытанных роликов проходил в интенсивном режиме (severe [109]). Как показало исследование поверхности роликов, износ носил контактно-усталостный характер.
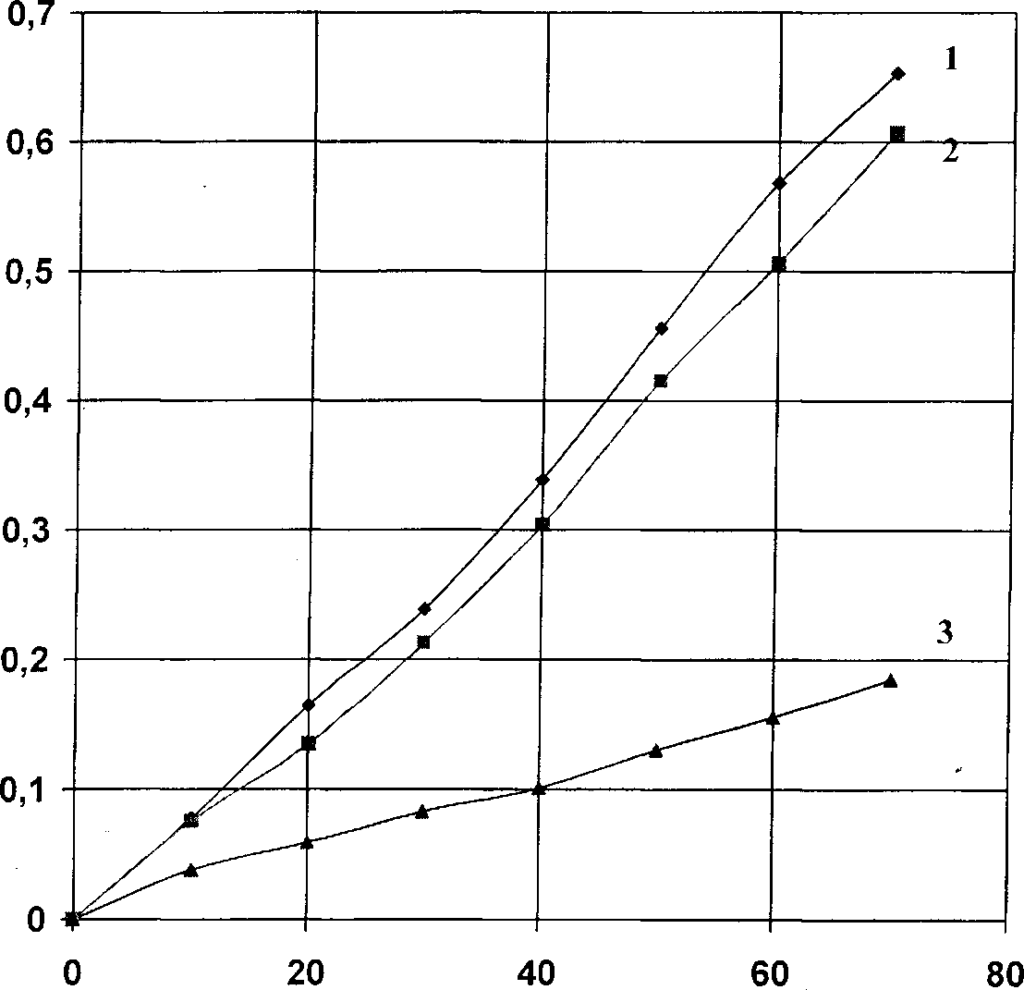
1 -М73В,Ш.С 37; 2-76ХСФ, ИКС 37; 3 — 76ХСФ, ШС 44;
Результаты сравнительных испытаний на износ по методу Амслера Режим испытаний: продольное проскальзывание — 10%; нагрузка 950 Н; без смазки.
Сравнительный визуальный анализ поверхностей износа роликов из сталей М73В и 76ХСФ показал, что наибольшему контактно-усталостному разрушению подверглась поверхность роликов из стали М73В с твердостью HRC 37. Наибольшей износостойкостью, по результатам проведенного эксперимента, характеризуются ролики из стали 76ХСФ с твердостью HRC 44.
Испытания на циклическую долговечность
Сравнительные усталостные испытания проводились по идентичному для всех образцов режиму. Максимальная внешняя нагрузка Pmax была выбрана таким образом, что максимальный уровень напряжений в зоне растяжения остряка был одинаков для всех образцов, что обеспечило возможность сравнения сопротивлений усталостному разрушению различных образцов по числу циклов нагружения, пройденных ими до разрушения.
Схема постановки полнопрофильной пробы остряка длиной 1200 мм на опоры пульсатора головкой вниз представлена на рис. 3.21.
Испытания проводили на образцах: №1 — сталь 76ХСФ, без Т/О; №2 — сталь 76ХСФ, закалка ТВЧ по стандартному режиму (РВОЗД=0,4 МПа); №3 — сталь 76ХСФ, закалка ТВЧ по скорректированному режиму (РВОзд=0,05 — 0,20 МПа); №4 — сталь М73В, закалка ТВЧ по стандартному режиму (Рвозд^ 0,4 МПа).
Для определения величины напряжений, возникающих в исследуемом сечении, и соответствующего выбора нагрузки было проведено тензометрирование. Тензометрические датчики производства ЦНИИСК длиной 20 мм и сопротивлением 200 Ом наклеивали на поверхность катания остряка в испытуемом сечении. Результаты тензометрирования представлены на рис. 3.22.
Анализ данных рис. 3.22 и сравнение средних величин напряжений в расчете на 10 кН/сеч нагрузки, которые составили:
для образца №1 (ширина головки 36 мм) — 15,6 МПа;
Результаты тензометрического анализа остряков
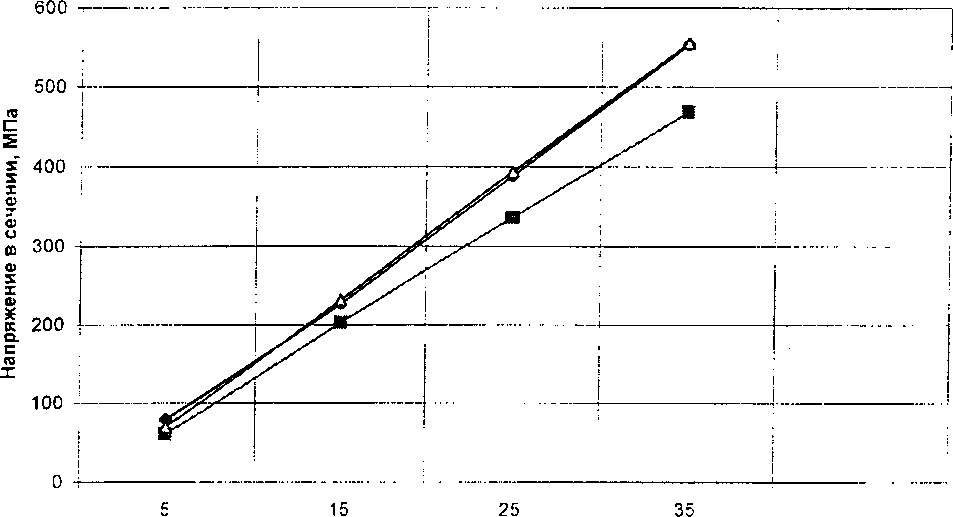
для образца №2 (ширина головки 40 мм) — 13,5 МПа; для образца №4 (ширина головки 30 мм) — 15,7 МПа показывает, что, несмотря на различную ширину сечений испытываемых образцов (30, 36 и 40 мм), разброс уровней напряжений, возникающий в исследуемом сечении остряков при одинаковой нагрузке находится в пределах допустимой ошибки эксперимента.
Рассчитанные по результатам тензометрирования и в соответствии с известным соотношением:
где Р — нагрузка, кН/сеч;
1 — расстояние между опорами, мм; \У — наименьший момент сопротивления сечения, см3 наименьшие моменты сопротивления испытуемого сечения составили: для образца №1 — 171,47 см3; для образца №2 -185,19 см3; для образца №3 — 171,47 см3; для образца №4 — 159,24 см3;для образца №5 — 159,24 см .
С учетом вышеозначенных факторов, а так же принимая во внимание возможное изменение величины возникающих при испытании напряжений, обусловленное наличием каких-либо концентраторов на поверхности головки остряков, определить вклад которых в общий уровень напряжений при циклическом нагружении не представляется возможным (неровности поверхности, задиры от строжки и т.п.), испытания проводили при одинаковом для всех образцов предельно допустимом (соответствующем напряжению, приблизительно равному 0,7а0.2) уровне максимальной нагрузки — 30 тс/сечение.
На рис. 3.23 и в табл. 3.12. представлены результаты усталостных испытаний остряков. Количества циклов нагружения до разрушения определены по одному образцу для каждого случая, испытанному при одинаковых условиях нагружения.
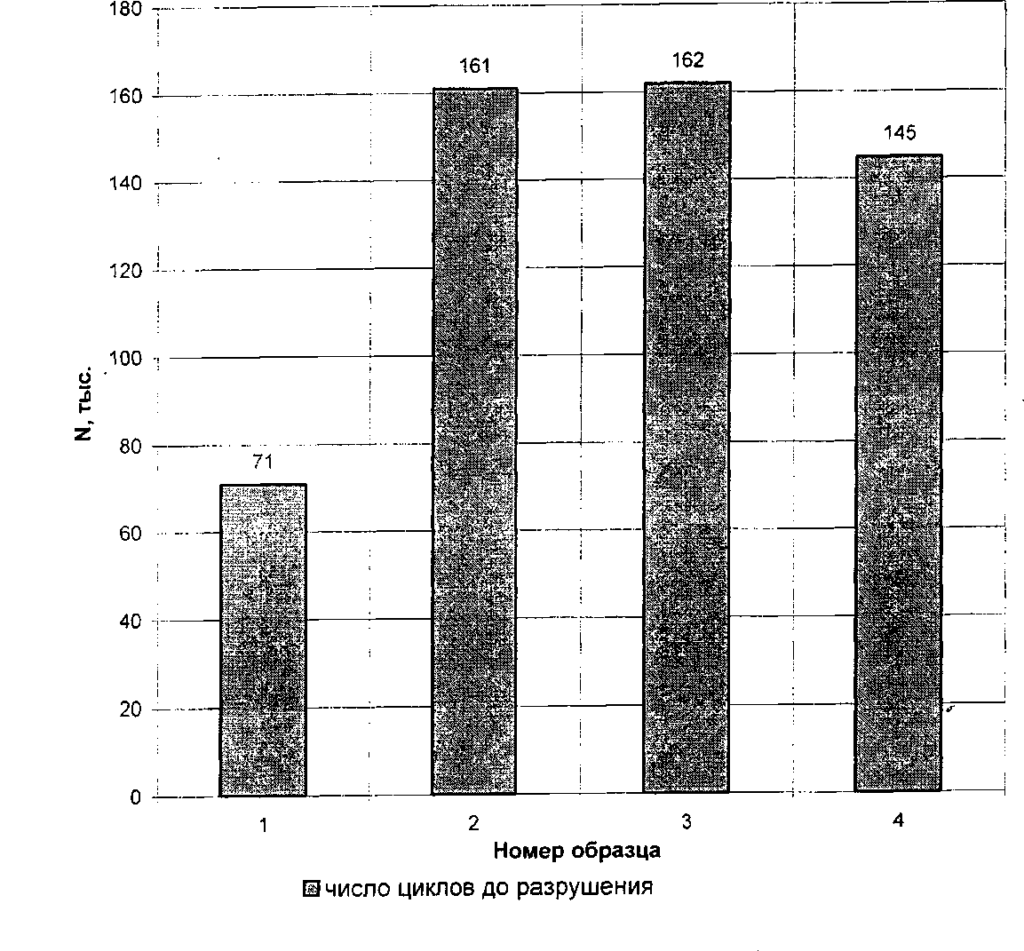
Результаты сравнительных усталостных испытаний остряков
- — сталь 76ХСФ, без термической обработки;
- — сталь 76ХСФ, закалка ТВЧ по стандарт, режиму (РВОзД=0,4 МПа);
- — сталь 76ХСФ, закалка ТВЧ по скорректированному режиму (РВ03ДЮ,2 МПа);
- — сталь М73В, закалка ТВЧ по стандартному режиму (РВозД=0,4 МПа)
Таблица 3.12 Характеристики образцов и количество циклов до разрушения при максимальной нагрузке 30 тс/сечение
№ образцов | Марка стали и термическая обработка | Ширина головки испытуемого сечения, мм | Наименьший момент сопротивления \У, см3 | Число циклов до разрушения, тыс. | Наибольшее значение напряжения, МПа |
1 | 76ХСФ без т/о | 36 | 171,47 | 71 | 468 |
2 | 76ХСФ закалка по стандартному режиму | 40 | 185,19 | 161 | 433 |
3 | 76ХСФ закалка по измененному режиму, Р =1 1 воздуха 1 атм | 36 | 171,47 | 162 | |
4 | М73В Закалка по стандартному режиму | 30 | 159,24 | 145 | 471 |
Анализ приведенных данных показывает, что наибольшими значениями циклической долговечности при заданном уровне нагрузки характеризуются образцы: №2 — сталь 76ХСФ, термообработка по стандартному режиму и №3 — сталь 76ХСФ, термообработка по скорректированному режиму (снижено давление воздуха до 0,20 МПа). Количество циклов до разрушения образцов №2 и 3 превысило на 12% соответствующую характеристику для остряков, изготовленных по серийной технологии (№4). Однако, следует учесть, что наиболее оптимальными характеристиками обладает образец остряка №3. Корректировка режима термической обработки (снижение давления охлаждающего воздуха с 0,4 до 0,2 МПа) позволила получить твердость поверхности НВ 400 — 415, способную обеспечить высокую износостойкость поверхности катания при отсутствии хрупкого разрушения. Твердость поверхности катания образца №2 (закалка сжатым воздухом под давлением 0,4 МПа) составляет около НВ 600, что не допустимо с точки зрения хрупкой прочности изделия.
Внешний вид изломов полнопрофильных остряковых проб после испытания на усталость приведен на рис. 3.24 — 3.27. Анализ изломов показывает наличие усталостной трещины, развивающейся от поверхности катания вглубь головки остряка. Остряк, изготовленный по серийной технологии (рис. 3.27), имеет более грубый излом с характерными бороздами в отличии от опытных остряков (рис. 3.24 — 3.26), изломы которых имеют более дисперсное строение. При исследовании изломов опытных остряков №2 (сталь 76ХСФ, закалка по серийному режиму) и №3 (сталь 76ХСФ закалка по скорректированному режиму) обнаружено расслоение между закаленным слоем и сердцевиной (см. рис. 3.25 и 3.26). В процессе циклического нагружения, данное расслоение, являясь концентратором напряжений, привело к развитию усталостной трещины в головке. Сама зона усталостного развития трещины совпадает с закаленным слоем в головке остряка.
Наличие описанного расслоения в остряках из стали 76ХСФ обусловлено неблагоприятным напряженным состоянием в поверхностных слоях головки, формирующимся в процессе закалки с выгибом. Повышенные характеристики упругости остряка из новой марки стали при тех же геометрических параметрах выгиба остряка на закалочном стенде (длина остряка, стрела прогиба) приводят к увеличению растягивающих напряжений в головке и образованию расслоения после охлаждения остряка сжатым воздухом.
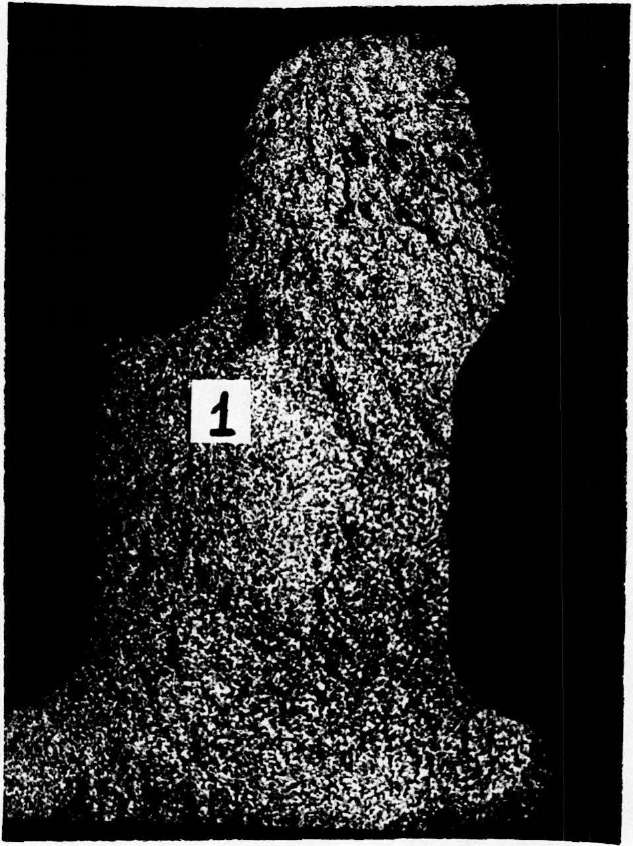
Поперечный усталостный излом образца №1 (сталь 76ХСФ без термической обработки)
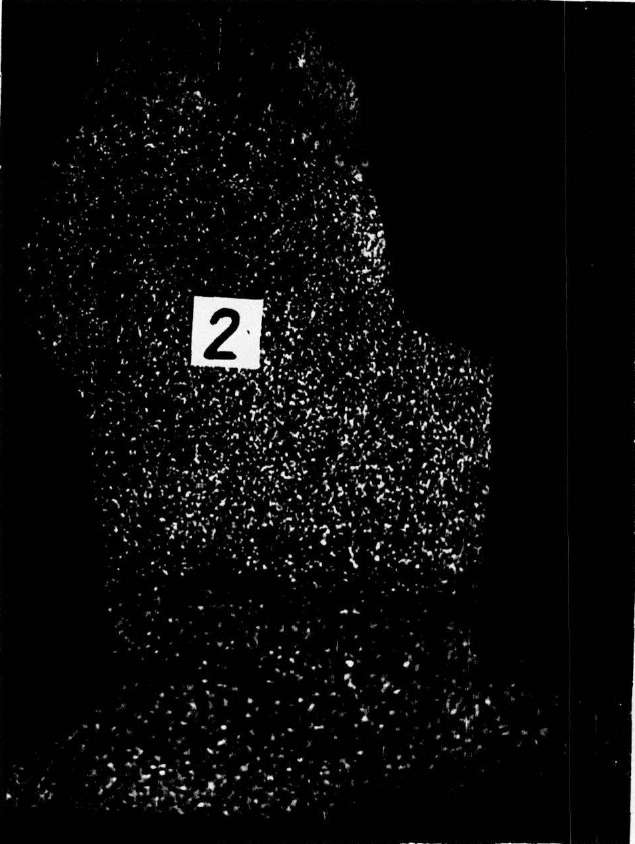
Поперечный усталостный излом образца №2 (сталь 76ХСФ, закалка по серийному режиму, Рвозд = 0,4 МПа)
Таким образом, проведенные испытания по оценке циклической долговечности остряков из сталей М73В и 76ХСФ показали увеличение циклической долговечности термически упрочненных остряков из стали 76ХСФ на 12% по сравнению с остряками из стали М73В. Однако проведенные испытания выявили наличие расслоения между закаленным слоем и сердцевиной остряков из стали 76ХСФ, упрочненных индукционной закалкой с выгибом. Последнее обстоятельство позволяет сделать вывод, что закалка с предварительным упру- гопластическим выгибом остряка не применима к острякам из новой марки стали. Остряки из стали 76ХСФ должны подвергаться двухсторонней поверхностной закалке без выгиба с минимальной последующей правкой.
Выводы
- Эксперименты по повышению температуры нагрева под закалку с 850 до 1050 °С показали, что изменение режима термической обработки в сочетании с серийной маркой стали М73В не может привести к значительному и равномерному по всей длине остряка повышению твердости поверхности, глубины закаленного слоя и прочностных характеристик по сечению остряка по причине недостаточной прокаливаемости стали серийной марки и ее низких прочностных характеристик. Это является подтверждением необходимости перехода на новую марку стали.
- Результаты исследования прокаливаемости методом торцовой закалки показали: прокаливаемость стали 76ХСФ составляет 8-10 мм против 5-6 мм для стали М73В, то есть превышает прокаливаемость стали серийной марки в 1,6 раза. На расстоянии 5 мм от торца образцов твердость стали 76ХСФ превышает твердость стали М73В в среднем на 150 HV]0.
- Результаты расчетной оценки прокаливаемое™ сталей 76ХСФ и М73В по комплексной методике, моделирующей условия двухстороннего охлаждения сжатым воздухом, показали возможность получения в головке и подошве остряков упрочненных слоев, толщина которых составляет: для стали 76ХСФ — 11 и 5 мм, для стали М73В — 7 и 3 мм в головке и подошве соответственно, т.е. при переходе к стали 76ХСФ глубина слоя в головке увеличивается на 57%, глубина слоя в подошве — на 67%.
- Временное сопротивление, предел текучести и твердость поверхности катания остряков из стали 76ХСФ без термического упрочнения сопоставимы с аналогичными характеристиками остряков из серийной марки стали, упрочненных индукционной закалкой, и превосходят свойства серийных остряков без термообработки: поверхностная твердость на 32-34 %, временное сопротивление на 14 %,-предел текучести на 39 %. Остряки из стали 76ХСФ без термической обработки могут эксплуатироваться в одинаково жестких с серийными термообработанными остряками условиях.
- После индукционной закалки экспериментальными исследованиями установлено увеличение глубины упрочненного слоя с 7 мм (для остряков из стали М73В) до 13 мм (для остряков 76ХСФ) и повышение максимальной твердости в пределах закаленного слоя с НВ 375 до НВ 410 в остряках’из стали 76ХСФ.
6. Микроструктура закаленного слоя остряка из стали 76ХСФ представляет собой троостосорбит закалки (микротвердость Н50=3 970-43 95 МПа) с разрозненными участками феррита. Микроструктура закаленного слоя остряка из стали М73В представлена сорбитом закалки (микротвердость Н5о=3300- 3 700 МПа) с разорванной сеткой феррита по границам зерен. Межпластиночное расстояние в закаленном слое для стали 76ХСФ — 0,15 мкм, для стали М73В — 0,2 мкм. Микроструктура сердцевины остряков из сталей 76ХСФ и М73В представлена пластинчатым перлитом с межпластиночными расстояниями 0,3 и 0,4 мкм соответственно.
7. Результаты оценки износостойкости сталей М73В и 76ХСФ по методу Амслера показали, что износостойкость стали 76ХСФ сопоставима с износостойкостью стали М73В при одинаковой твердости роликов НЯС 37, что дает основания для проведения эксплуатационных испытаний остряков из стали 76ХСФ без термического упрочнения.
- Циклическая долговечность остряков из 76ХСФ, подвергнутых индукционной закалке с выгибом превысила на 12 % циклическую долговечность серийных остряков. Однако обнаруженное на поперечном изломе расслоение между закаленным слоем и сердцевиной говорит о невозможности применения закалки ТВЧ с выгибом к острякам из стали 76ХСФ, что обуславливает необходимость разработки технологии двухсторонней закалки.
- По результатам оценки прокаливаемое™ опытной марки стали и исследований влияния термической обработки на микроструктуру стали 76ХСФ разработаны основные требования к технологии термической обработки остряков из новой марки стали:
- термическая обработка должна осуществляться только по схеме двухстороннего нагрева и охлаждения без выгиба;
- давление охлаждающего воздуха должно обеспечивать скорость охлаждения поверхностных слоев головки и подошвы, необходимую для формирования микроструктуры сорбита или троостосорбита закалки на заданной глубине и обеспечивающую компенсацию термических напряжений и деформаций в остряке.