- Сравнительные полигонные и эксплуатационные испытания остряков
- Работы по внедрению двухстороннего термического упрочнения остряков
- Выводы
- ОБЩИЕ ВЫВОДЫ
- Список Литературы
Цикл статей:
Глава 1 — Введение. Цели и задачи исследований.
Глава 2 — Анализ причин отказов стрелочных переводов и их элементов
Глава 3 — Материалы и методика исследования
Глава 4 — Сравнительные исследования комплекса физико- механических свойств остряков из сталей марок 76хсф и м73в
Глава 5 — Разработка технологических основ двухстороннего поверхностного упрочнения остряков
Глава 6 — Работы по промышленному внедрению стали 76ХСФ и технологии двухстороннего термического упрочнения остряков
Сравнительные полигонные и эксплуатационные испытания остряков
С целью оценки уровня потребительских свойств остряков из стали марки 76ХСФ, упрочненных индукционной закалкой с выгибом, проведены сравнительные полигонные испытания на экспериментальном кольце ВНИИЖТ (ЭК ВНИИЖТ). На ЭК ВНИИЖТ испытывали два остряка из стали 76ХСФ, подвергнутые индукционной закалке с выгибом по скорректированному режиму охлаждения (давление воздуха при охлаждении снижено и составляет 0,05-0,2 МПа в зависимости от сечения остряка). Твердость поверхности катания таких остряков — НВ 400-410.
Для оценки эксплуатационной стойкости остряков из стали марки 76ХСФ без термического упрочнения проводятся сравнительные эксплуатационные испытания на Западно-Сибирской (ПС-1) и Северной (ПС-8) железных дорогах. Твердость опытных остряков составляет НВ 350-370.
Основными критериями оценки уровня потребительских свойств остряков являются их долговечность и надежность. В процессе полигонных и эксплуатационных испытаний проверяется сопротивление остряков износу, выгибу и образованию трещин и выкрашиваний (особенно в острой части остряка).
Результаты испытаний для опытных остряков сравнивали с результатами для остряков из стали М73В, термообработанных по серийной технологии, эксплуатировавшихся в приближенных условиях.
На рис. 5.1 представлен внешний вид опытных остряков, уложенных на ЭК ВНИИЖТ. Полигонные испытания остряков проводились в комплекте с рамными рельсами в «ячейке» из-за отсутствия возможности испытания на ЭК правого стрелочного перевода в сборе. Движение осуществлялось в пошерстном направлении. Средние статические осевые нагрузки подвижного состава составляли 270 кН на ось, скорость движения опытного поезда 70 км/ч. Программа сравнительных полигонных испытаний представлена в разделе ПРИЛОЖЕНИЯ.
После пропуска 31, 4 млн. т. брутто (при среднесетевом нормативе 320 млн. т. брутто) один остряк вышел из строя по причине образования трещины в головке и шейке. Поверхность излома, полученная при вскрытии трещины на прессе представлена на рис. 5.2. Размер трещины в направлении от поверхности катания в глубь остряка составил 86 мм (см. рис. 5.2).
Трещина расположена на расстоянии 2325 мм от острого конца в сечении — с шириной головки 35 мм. Трещина расположена на участке остряка между шпалами на расстоянии 258 мм от ближайшей стрелочной подушки.
Лабораторное исследование показало, что основными причинами образования поперечной трещины стали:
- низкое металлургическое качество стали (наличие в очаге разрушения неметаллических включений обогащенных кремнием, кальцием и алюминием);
- расслоение между закаленным слоем и неупрочненной сердцевиной (рис. 5.2), обусловленное выгибом остряков перед закалкой и последующей механической правкой, создающей неблагоприятную эпюру внутренних остаточных напряжений.
Последнее обстоятельство говорит о том, что для остряков из стали 76ХСФ односторонняя индукционная закалка с выгибом не применима.
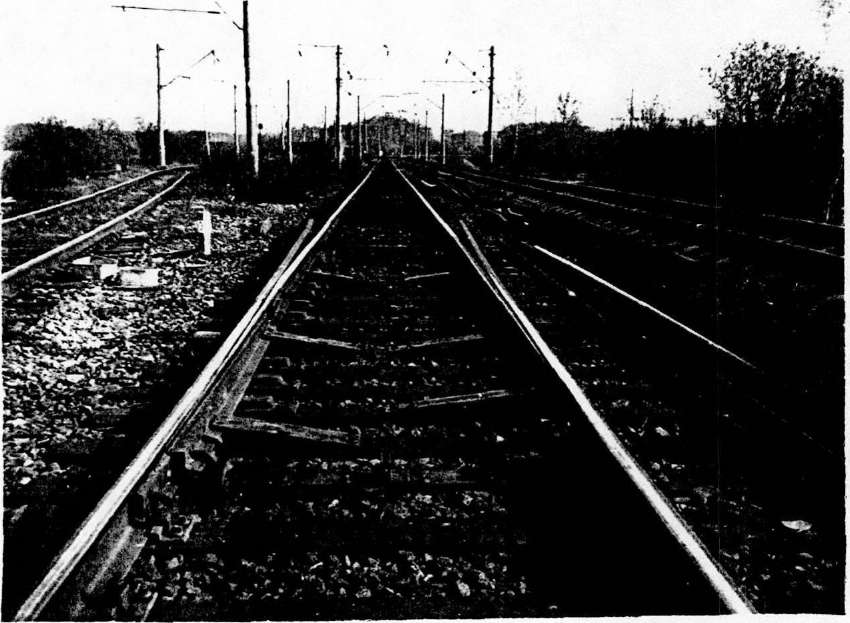
Испытания опытных остряков в «ячейке» на ЭК ВНИИЖТ
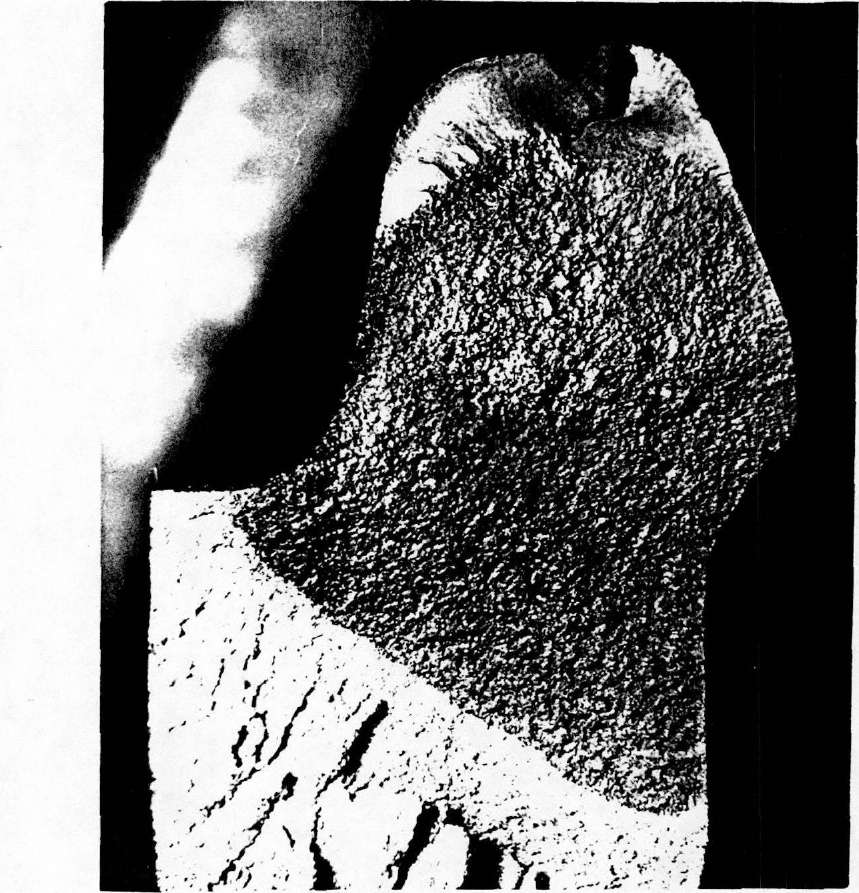
Внешний вид излома остряка после вскрытия трещины
Вертикальный износ исследованного остряка не превышает 1,0 мм в сечении шириной 50 мм. По длине остряка износ имеет равномерный характер,без седловин и местных неровностей. В корневом конце остряка, в стыке, на поверхности катания обнаружено выкрашивание — дефект 0.17.1. по классификации дефектов рельсов НТД/ЦП-1-9. На момент изъятия остряка размеры выкрашивания составили:
- Максимальная глубина — 2,1 мм;
- Длина (вдоль направления прокатки) — 7,5 мм;
- Ширина — 22,3 мм.
По требованиям НТД/ЦП-1, 2, 3 -93 рельс с дефектом 17.1. таких размеров при отсутствии других повреждений не считается дефектным.
Изъятый остряк был заменен на серийный остряк из стали М73В. Испытания второго опытного остряка были продолжены.
На момент пропуска по нему 40,6 млн. т. брутто вертикальный износ по всей длине не превышал 1,0 мм. Волнообразных неровностей и седловин на поверхности катания не обнаружено. Также не обнаружено одностороннего наката и выкрашивания в острой части остряка. Вертикальный износ серийного остряка по всей поверхности катания не превышает 2,0 мм.
После пропуска 40,6 млн. т. брутто неприлегание опытного остряка к первой стрелочной подушке составляет 2,0 мм, далее по всей длине остряка не более 1,0 мм, т. е. не превышает норму, установленную в ТУ 32 ЦП — 114.
Неприлегание серийного остряка к первой стрелочной подушке составило 3,0 мм, далее — 2,0 мм.
Однако, после пропуска 58,3 млн. т. брутто второй опытный остряк был изъят по причине образования дефекта 0.17.1 (выкрашивание закаленного слоя в корневой зоне), размеры которого на момент изъятия составили: максимальная глубина — 6,3 мм; ширина — 57,3 мм; длина — 9,7 мм.
Остряк серийного производства так же имел дефект 0.17.1. следующих размеров: максимальная глубина — 2,5 мм; ширина 22,5 мм; длина — 10 мм.
Таким образом, результаты испытаний показали, что вертикальный износ опытного остряка ниже серийного; дефект 0.17.1, обнаруженный как в опытном так и в серийном остряке, характеризуется большими размерами в случае опытного остряка, что объясняется повышенной твердостью поверхности катания опытного остряка из-за недостаточной корректировки режима охлаждения стали, легированной хромом. И опытный, и серийный остряки в процессе испытаний подвергаются короблению, что обусловлено неблагоприятной эпюрой внутренних остаточных напряжений, возникающих в результате выгиба перед закалкой и последующей механической правки. Однако опытный остряк характеризуется большей стойкость против выгиба, чем серийный. Это обусловлено повышением прочностных характеристик и жесткости изделия в целом за счет легирования хромом.
Эксплуатационные испытания остряков из стали 76ХСФ без термического упрочнения, предварительные результаты которых приведены в актах испытаний в разделе ПРИЛОЖЕНИЯ, показывают, что износостойкость опытных остряков без термической обработки сопоставима с износостойкостью серийных поверхностно закаленных остряков, а в некоторых случаях даже превышает ее. Пример: прямой остряк из хромистой стали (уложен на станции’Зебляки, СП №8, пропущенный тоннаж 2,0 млн. т. брутто) не имеет бокового износа в контрольных сечениях; контрольный остряк (уложен на станции Межог, СП №7, пропущенный тоннаж 2,0 млн. т. брутто) имеет боковой износ в сечениях 20 и 50 мм — 2,0 и 1,0 мм соответственно.
На остряковые рельсы из новой марки стали разработаны технические условия № 0921-038-01124328-96 «Рельсы остряковые» (раздел ПРИЛОЖЕНИЯ).
Работы по внедрению двухстороннего термического упрочнения остряков
По результатам проведенной работы, на остряки из сталей марок М73В и 76ХСФ, упрочненные двухсторонней закалкой, разработаны и утверждены технические условия № 1132-075-01124328-98 «Остряки для стрелок, упрочненные двухсторонней закалкой с нагрева токами высокой частоты» (раздел ПРИЛОЖЕНИЯ) и оформлен патент [122].
Для внедрения технологии двухсторонней закалки остряков разработана конструкторская документация на установку для индукционной закалки по предлагаемому методу. Первоначально планировалась конструкция установки, представленная на рис. 5.3. Однако с целью получения наиболее технологичной конструкции опытно-промышленной установки, сооружаемой на базе серийной установки в цехе термической обработки НСЗ, была проведена переработка конструкторской документации. В новом варианте оборудования остряк фиксируется для закалки в вертикальном положении, а не на боку.
Несмотря на внесенные в конструкцию установки изменения, основные технологические узлы закалочного оборудования остаются прежними и включают в себя (см. рис. 5.3): приводную тележку (1) для подачи остряка в зону закалки и пост индукционного нагрева остряков (2) под закалку потоком сжатого воздуха.
На тележке закреплены опоры (3) для размещения закаливаемого остряка.
Две крайние опоры выполнены нерегулируемыми и снабжены фальш- приставками, являющимися продолжением рабочих поверхностей головки и подошвы остряка и предназначены для размещения опорных следящих роликов (4) трансформаторных блоков поста. Промежуточные опоры выполнены регулируемыми по высоте и снабжены выдвижными скалками, являющимися упорами для подошвы рельса при его установке.
Пост двухстороннего нагрева рельса включает два трансформаторных блока (5), несущих оппозиционно расположенные контурные индукторы (6) для нагрева головки и подошвы рельса.
Каждый трансформаторный блок состоит из стойки, несущей подпружиненные в направлении рельса горизонтальные салазки со свободно вращающимися относительно вертикальных осей роликами, взаимодействующими с рабочей поверхностью головки или подошвы рельса, и вертикальную подпружиненную относительно стойки каретку со свободно вращающимися относительно горизонтальных осей роликами, взаимодействующими с боковыми поверхностями головки или подошвы рельса, имеющей возможность вертикального перемещения относительно салазок. На каретке закреплен высокочастотный трансформатор с контурным индуктором и воздушным спрейером. Система свободно вращающихся роликов с вертикальными и горизонтальными осями взаимодействующих с рабочими поверхностями головки и подошвы рельса позволяет поддерживать постоянный зазор между контуром индукторов и нагреваемыми поверхностями рельса, что обеспечивает равномерность закаленного слоя по длине рельса и исключает его деформацию.
Работа на оборудовании осуществляется следующим образом:
Обрабатываемый остряк укладывается на опоры тележки, выведенной из зоны поста нагрева в зону загрузки. Промежуточные опоры тележки должны быть предварительно отрегулированы по высоте под естественную кривизну остряка. На крайних опорах концы остряка зажимаются посредством прихватов после того, как рельс своей подошвой подведен до контакта с выдвижными вертикальными скалками промежуточных опор. После зажима рельса скалки убираются из зоны нагрева подошвы рельса. Затем горизонтальные салазки поста нагрева раздвигаются, а тележка подается в зону поста до положения, когда фалыпприставка крайней опоры окажется в зоне роликов салазок. Салазки освобождают и они под действием противовеса, выполняющего роль пружины, сводятся своими роликами к рельсу до контакта с поверхностями головки и подошвы остряка. При этом вертикальные каретки должны быть приподняты для прохода фалыпприставки под горизонтальными роликами кареток. Когда каретки освобождают, они опускаются до контакта своими роликами боковых поверхностей головки и подошвы остряка. Оборудование готово к работе.

Включается водяное охлаждение трансформаторов с индукторами, подача сжатого воздуха в спрейеры и нагрев рельса. После определенной выдержки нагрева начального участка рельса включается подача тележки с рельсом и осуществляется его закалка потоком сжатого воздуха.
На основе проведенных исследований и конструкторской разработки на НСЗ сооружена опытно-промышленная установка по двухсторонней закалке остряков. Внешний вид установки приведен на рис. 5.4. На данной установке проведена отработка режима упрочнены остряки для последующих полигонных и эксплуатационных испытаний. Акт об экспериментальном запуске установки в работу представлен в разделе ПРИЛОЖЕНИЯ.
Приведенный на рис. 5.5 вид макроструктуры остряка из стали М73В после двухсторонней закалки показывает, что в результате термического упрочнения по новой технологии в головке и подошве остряка образуются упрочненные слои. Глубина слоя по оси головки составила 7 мм, глубина слоя в подошве -4 мм.
Таким образом, применение технологии двухсторонней закалки без предварительного выгиба, обеспечивающей создание в головке и подошве остряков упрочненных слоев, формирование в головке и подошве эпюры внутренних остаточных напряжений сжатия, устраняющей предпосылки к выгибу остряков в эксплуатации, позволит повысить срок службы остряков, что приведет к снижению расходов на эксплуатационное содержание стрелочных переводов.
Выводы
- Технология закалки ТВЧ с выгибом не применима к острякам из стали 76ХСФ, так как приводит к образованию расслоения между закаленным слоем и сердцевиной, которое инициирует развитие поперечной усталостной трещины в процессе эксплуатации.
- Перспективной технологией упрочнения остряков из низколегированной стали является технология двухсторонней закалки ТВЧ, исключающая выгиб остряка.
- По результатам эксплуатационных испытаний износостойкость остряков из стали 76ХСФ без термического упрочнения сопоставима с износостойкостью серийных остряков после индукционной закалки. При этом «хромистые» остряки характеризуются большей стойкостью против выгиба в процессе эксплуатации вследствие более высокой прочности по всему сечению и менее жесткого режима правки.
- На основе проведенных экспериментальных исследований на НСЗ построена опытно-промышленная установка по двухсторонней закалке остряков. Проведена отработка режима двухсторонней закалки.
ОБЩИЕ ВЫВОДЫ
- Проведен анализ повреждаемости остряков в эксплуатации, показавший, что основными видами повреждений остряков являются боковой износ (интенсивность до 10 мм/10 млн. т. брутто), выгиб (величина неприлегания подошвы остряка к стрелочным подушкам до 14,5 мм при норме 1 мм), образование и выкрашивание гребнеобразного наплыва в острой части (пропущенный тоннаж до образования дефекта 15-20 млн. т. брутто).
- Установлено, что практикуемая в настоящее время технология индукционной закалки остряков с выгибом не обеспечивает их прямолинейности. Последующая механическая правка приводит к формированию неблагоприятной эпюры внутренних остаточных напряжений (растягивающие напряжения в головке или подошве остряка до 150 МПа), приводящей в свою очередь к выгибу остряков в эксплуатации.
- Представлено расчетное обоснование возможности развития поверхностных трещин при индукционном нагреве с выгибом. Показано, что при закалке остряка типа Р65 длиной 12600 мм с выгибом в процессе нагрева в поверхностном слое головки реализуются растягивающие напряжения, общий уровень которых составляет 770 МПа (420 МПа от механического изгиба, 350 МПа от действия температурного поля индуктора). Данные напряжения превышают предел текучести всех используемых марок сталей (М73В — 560 МПа, М76В — 600 МПа, 76ХСФ — 760 МПа) и приводят к развитию трещин в головке глубиной до 4,8 мм от имеющих место на поверхности катания волосовин.
При двухстороннем индукционном нагреве под закалку без выгиба величина растягивающих напряжений в поверхностном слое головки составляет 300 МПа, что не создает условий для развития поверхностных трещин от волосовин.
4. В целях повышения стойкости остряков против износа и выгиба необходимо увеличение глубины закаленного слоя в головке, твердости и прочностных свойств по сечению изделия. Эксперименты по увеличению температуры нагрева под закалку с 850 до 1050 °С показали, что на стали серийной марки М73В это не представляется возможным вследствие ее недостаточной прокали- ваемости и фактической выработки ресурса упрочнения в рамках существующей технологии термообработки.
5. Применена новая марка стали для остряков 76ХСФ с содержанием хрома 0,35 — 0,55 %, характеризующаяся по сравнению со сталью серийной марки М73В: повышением прокаливаемости на торцовых образцах в 1,6 раза; увеличением глубины упрочненного слоя в головке остряков с 7 до 13 мм; повышением временного сопротивления, предела текучести и твердости поверхности для термически упрочненных остряков на 5, 5 и 17 % соответственно (в сравнении с закаленными серийными остряками) и для нетермообработанных остряков (в сравнении с остряками из стали М73В без термобработки) на 14, 39 и 34 % соответственно. При этом уровень указанных свойств для остряков из стали 76ХСФ без термического упрочнения и закаленных остряков из стали: М73В соизмерим, что делает перспективным применение остряков из 76ХСФ без термической обработки.
6. Эксплуатационные испытания «хромистых» остряков без термического упрочнения на Западно-Сибирской и Северной железных дорогах показали, что их износостойкость сопоставима с износостойкостью серийных остряков после индукционной закалки, а сопротивление выгибу превышает аналогичную характеристику для серийных остряков, вследствие более высокого уровня прочностных свойств по сечению.
7. Результаты стендовых (усталостных) и полигонных испытаний «хромистых» остряков, упрочненных по серийной технологии, показали, что индукционная закалка с выгибом не применима к острякам из новой марки стали вследствие образования расслоения между закаленным слоем и сердцевиной в головке остряка.
8. По результатам проведенных исследований влияния термической обработки на физико-механические свойства остряков сформулированы основные требования к технологии термической обработки остряков из новой марки стали:
- закалка остряков из стали 76ХСФ может осуществляться только по двухсторонней схеме закалочного нагрева и охлаждения;
- при закалке остряков из стали 76ХСФ давление охлаждающего воздуха должно быть снижено до 0,05-0,20 МПа в зависимости от ширины сечения головки.
- Разработана новая технология двухсторонней закалки остряков, исключающая операцию упруго-пластического выгиба и ее отрицательные последствия за .счет двухстороннего нагрева и охлаждения остряка, обеспечивающих компенсацию термических напряжений и деформаций и сохраняющих его прямолинейность.
- По результатам исследования влияния двухсторонней закалки на свойства образцов остряков показано, что предлагаемая технология обеспечи-. вает прямолинейность на выходе и наличие внутренних остаточных напряжений сжатия в головке и подошве остряка до 150 МПа. ‘
- Проведенными исследованиями показано, что технология двухсторонней закалки универсальна и применима ко всем маркам сталей, используемым при производстве остряков, включая сталь 76ХСФ.
- На основании экспериментальных исследований разработаны и оформлены технические условия на остряки из стали 76ХСФ и остряки, упрочненные двухсторонней закалкой (см. раздел ПРИЛОЖЕНИЯ).
- Разработана конструкторская документация на установку по двухсторонней закалке остряков и оформлен патент. На Новосибирском стрелочном заводе сооружена опытно-промышленная установка по двухсторонней закалке остряков. Проведена отработка технологического режима закалки. Полученные остряки характеризуются наличием упрочненных слоев в головке и подошве.
Новая марка стали и технология двухсторонней закалки одобрены Департаментом пути и сооружений (письмо № ЦПТ-9/51 от 04.11.98) и Межведомственной рельсовой комиссией (г. Новосибирск, 1997 г.)
Список Литературы
- Симон A.A., Столярова Т.А. Некоторые вопросы дальнейшего повышения эффективности применения стрелочных переводов// Труды ЛИИЖТ.- 1971.-вып. 328.-С. 134-143.
- ТУ 32 ЦП-114-77.Соединения и пересечения путей железных дорог. Общие технические условия. — 62 с.
- Материалы Межведомственной рельсовой комиссии, Новосибирск, 1997 г.-5 с.
- Волошко Ю.Д., Орловский А.Н. Как работают стрелочные переводы под поездами,- М.: Транспорт, 1987. — 120 с.
- Фришман М.А. Как работает путь под поездами. — М.: Транспорт, 1969.- 117 с.
- Правила технической эксплуатации железных дорог Союза ССР — М.: Транспорт. 1987. — 141 с.
- Безопасность движения // ЦНИИТЭИ МПС — 1997, вып. 5 — С. 37.
- C.B. Амелин. Стрелочные переводы для высокоскоростной’линии // Путь и путевое хозяйство. — 1993. — №1. — С. 12-16.
- Донец В.Г., Киселева Т.Н. Эксплуатационная стойкость остряков стрелочных переводов в условиях метрополитена // Надежность стрелочных переводов,- М.: Транспорт, 1988.- С. 95-100.
- Титаренко М. И. Исследование работы стрелочных переводов типа Р75//Надежность стрелочных переводов.- М.: Транспорт, 1988. — С. 51-58.
- H.A. Колонина стрелочные переводы на железобетонных брусьях // Надежность стрелочных переводов.- М.: Транспорт, 1988. — С. 59-69.
- Киселева Т.Н., Великанов A.B. Исследование усталостной прочности подошвы остряков // Вестник ВНИИЖТ.-1979.- N3. С. 49-50.
- Классификация дефектов и повреждений элементов стрелочных переводов. Каталог дефектов и повреждений элементов стрелочных переводов. Признаки дефектных и остродефектных элементов стрелочных переводов // Дополнения к НТД/ЦП-1,2,3-93. — М.: Транспорт, 1996. — 64 с.
- Классификация дефектов рельсов. Каталог дефектов рельсов. Признаки дефектных и остродефектных рельсов // НТД/ЦП-1,2,3-93. — М.: Транспорт, 1993.- 63 с.
- Шур Е.А. Конструктивная прочность стали и термическая обработка железнодорожных рельсов: Автореф. дис. …докт. техн. наук. — М., 1980. — 33 с.
- Шур Е.А. Структура и контактно-усталостная прочность стали // МиТОМ.-1978. — N8. — С. 37-43.
- Ларкин A.B. Основные направления повышения качества производства стрелочной продукции для железных дорог России: Автореф. дис. … канд. техн. наук. — М., ВНИИЖТ. — 1998. — 30 с.
- Гордюк Ю.В. Способ закалки рельсов и стрелочных остряков и за-. кал очный стенд для осуществления способа. Авторское свидетельство №121464 // Бюллетень изобретений. — 1959. — №15. — С. 28-29.
- ГОСТ9960. Рельсы остряковые. Технические условия. — М.: Издательство стандартов, 1986. — 12 с.
- ГОСТ 24182. Рельсы железнодорожные широкой колеи типов Р75, Р65 и Р50 из мартеновской стали. Технические условия. — М.: Издательство стандартов , 1980. — 16 с.
- ГОСТ 21014. Прокат черных металлов. Термины и определения дефектов поверхности. — М.: Издательство стандартов, 1989. — С. 3 — 7.
- Качество поверхности металла / Строганов А.И., Хасин Г.А., Черни- ченко А.И., Дробышевский A.C. — М.: Металлургия, 1985. — 126 с.
- Кривоногое В.Г. Исследование особенностей численного решения задач термопластичности и ползучести применительно к оценке прочности термонапряженных конструкций: Автореферат дис. … канд. техн. наук. — М., МИИГА. — 1983,- 22 с.
- Оптимизация технологии зональной термической обработки методами математического моделирования / В.А. Петушков, В.Г. Кривоногов, В.В. Дым- ченко // Тез. 9-ой Всесоюзной научн. — техн. конф. «Применение токов высокой частоты в электротермиии». — Л.: ВНИИТВЧ, 1981. — С. 39-40. (ротапринт).
- Конечно — элементные модели расчета железнодорожного пути на прочность и устойчивость // Сб. научн. статей по ред. Э. П. Исаенко. — М.: Гудок, 1997.-С. 19-38.
- Шур Е.А. Повреждения рельсов — М.: Транспорт, 1971. — 109 с.
- Конюхов А.Д. Остаточные напряжения в железнодорожных рельсах // Остаточные напряжения и прочность железнодорожных рельсов / Сб. трудов ЦНИИ МПС. — М.: Транспорт. — 1973. — Вып. 491. — С. 10-26.
- Влияние технологии на остаточные напряжения в объемно- закаленных рельсах / А. Д. Конюхов, Д. М. Рабинович, И. Я. Винокуров и др. // Сталь.-1969.-№6.-555 с.
- Шур Е.А., Пан A.B. Рельсы будущего // Железнодорожный транспорт. — 1998. — №4. — С. 57-60.
- Шур Е.А, Конюхов А.Д. Влияние остаточных напряжений в закаленных рельсах на возникновение и распространение усталостных трещин при циклическом изгибе // Остаточные напряжения и прочность железнодорожных рельсов. Сб. трудов ЦНИИ МПС. — М.: Транспорт. — 1973. — Вып. 491. — С. 2936.
- Шахунянц Г. М., Никонов А. М. Остаточные напряжения в закаленных рельсах Р65 // Остаточные напряжения и прочность железнодорожных рельсов. Сб. трудов ЦНИИ МПС. — М.: Транспорт. — 1973. — Вып. 491. — С. 2729.
- Екобори Т. Физика и механика разрушения и прочность твердых тел. — М.: Металлургия, 1971. — 167 с.
- Носков М. М., Раузин Я. Р. О контактной усталости и износостойкости рельсовой стали // Вестник ВНИИЖТ. — 1967. — №4. — 46 с.
- Kepple R. К., Mattson R.L. Paper.// Amer. Soc. Mech. Eng. — 1969. — №2.
- Кудрявцев И.В. О влиянии остаточных напряжений на усталостную прочность стали. — М.: Машгиз. — 1959. — 5 с.
- Гликман JT. А. Устойчивость остаточных напряжений и их влияния на механические свойства металла и прочность изделия // Качество поверхности и долговечность деталей машин. — НИС — ЛИЭН. — 1956. — С. 145.
- Aida S., Kimura D., Ito T. Residual Stress in the rail // Yavato Techn. Report. — 1963. — №244. — P. 85-123.
- Технологическая инструкция по выправке вертикального выгиба остряков стрелочных переводов № ЦП-1-97. — М. — 1997, 16 с.
- Легейда В.Н. Разработка новых технологических параметров термического упрочнения железнодорожных рельсов с индукционного нагрева: Авто- реф. дис. .. .канд. техн. наук. — Днепропетровск, ИЧМ. — 1992. — 20 с.
- Производство и термическая обработка железнодорожных рельсов / Под ред. В.В.Лемпицкого и Д.С.Казарновского.- М.: Металлургия, 1972. — 272 с.
- Поляков В.В., Великанов A.B. Основы технологии производства железнодорожных рельсов. — М.: Металлургия, 1990. — 416 с.
- Лошкина H.A. Уточнение состава стали и усовершенствование термической обработки железнодорожных рельсов: Автореф. дис. …канд. техн. наук. Днепропетровск, ИЧМ. — 1971. — 24 с.
- Коротких Н.К. Особенности разрушения термоупрочненной рельсовой стали при циклическом нагружении: Автореф. дис. …канд.техн. наук. Новокузнецк, СМИ. — 1982г. — 24 с.
- Лошкина H.A., Великанов А.Б., Рабинович Д.М. Повышение работоспособности объемно-закаленных рельсов путем корректировки химического состава и технологии термической обработки // Труды ВНИИЖТ.- 1971.- вып. 434. — С.129-135.
- Упрочнение углеродистой стали микролегированием и термомеханической обработкой / К.И. Тушинская, Л.И. Тушинский, Л.Б. Тихомирова и др. / Труды ВНИИЖТ.-1968. — вып. 71. — 112 с.
- Носков М.М., Раузин Я.Р. Пути повышения контактной выносливости рельсовой стали//Труды ВНИИЖТ.-1971. — вып. 434. С.70-79.
- Шур Е.А., Бычкова Н.Я., Марков Д.П., Кузьмин Н.Н. Износостойкость рельсовых и колесных сталей // Трение и износ, Том 16, №1, С. 80-90.
- Великанов А.В. Причины повреждаемости в пути закаленных рельсов из легированных сталей // Вестник ВНИИЖТ. — 1980. — №6. — С. 51-54.
- Вологдин В. П. Поверхностная закалка индукционным способом. — М.: Металлургиздат, 1939. -244 с.
- Вологдин В. П. Поверхностная индукционная закалка. — М.: Оборон- гиз, 1947.-291 с.
- Шепеляковский К. 3. Упрочнение деталей машин поверхностной закалкой при индукционном нагреве. — М.: Машиностроение, 1972. — 287 с.
- Шепеляковский К. 3. Поверхностная и объемно — поверхностная закалка стали как средство упрочнения ответственных деталей машин и экономии материальных ресурсов // МиТОМ. — № 11. — 1993. — С. 8 — 14.
- Головин Г. Ф., Замятнин М. М. Высокочастотная термическая обработка. — Л.: Машиностроение, 1968. -228 с.
- Кидин И. Н. Физические основы электротермической обработки металлов и сплавов. — М.: Металлургия, 1969. — 376 с.
- Лозинский М.Г. Промышленное применение индукционного нагрева. М.: АН СССР, 1958. — 472 с.
- Слухоцкий А.Е., Рыскин С.Е. Индукторы для индукционного нагрева. Л.: Энергия, 1974. — 264 с.
- Головин Г. Ф., Замятнин М. М. Высокочастотная термическая обработка. — Л.: Машиностроение, 1990. — 239 с.
- Термическая обработка в машиностроении // Справочник под ред. Ю.М. Лахтина, А.Г. Рахштадта. — М.: Машиностроение, 1980. — 783 с.
- Ахматов A.C., Фокин Н.Ф. Влияние нагрева стали ТВЧ на ее износ // Трение и износ в машинах, т. 1, АН СССР, 1947. — 412 с.
- Алексеенко В.В., Лифшиц С.Л. Индукционный нагрев при термической обработке стали. — М.: Оборонгиз, 1953. — 263 с.
- Леванов В.Л., Кущ Э.В. Усталостная прочность зубчатых колес, закаленных с нагревом ТВЧ // Промышленное применение ТВЧ. — М.: Машиностроение, 1968.-С. 86-91.
- Термически упрочненные рельсы / Под. Ред. А.Ф. Золотарского. — М.: Транспорт, 1976. — 264 с.
- Щапов Н.П. Поверхностное упрочнение деталей подвижного состава и пути // Труды ВНИИЖТ.- 1954. — вып. 82. — С.4 — 9.
- Свойства рельсов, подвергнутых закалке с индукционного нагрева /- Д.С. Казарновский, B.C. Точиленко, А.Н. Заннес и др. // Производство железнодорожных рельсов и колес. — 1973. — вып. 1. — С. 65 — 69.
- Вологдин В.П. Поверхностная индукционная закалка токами высокой частоты. — С.: Металлургиздат, 1941. — 18 с.
- Геллер В. Производство рельсов в Англии, США, Канаде и Японии и тенденции улучшения их качества // Черные металлы. — № 17. — 1970. — С. 3640.
- Binzeisler Н., Schmedders Н., Wick К. Moderne Schienener zeugung bei der «Thyssen Stahl AG» // Thyssen Technische Berichte. — №1. — 1988. — S. 147159.
- Rail Engineering International. — №3. — P. 25-30.
- Дьяченко A.3., Кац P.3., Швецова M.H. Поверхностная закалка рамных рельсов и остряков // Путь и путевое хозяйство. — 1969. — №12.- С. 35-36.
- Производство, качество и стойкость железнодорожных рельсов. — М.: Металлургия, 1966.-С. 162-172.
- Неоднородности структуры закаленного слоя при поверхностной закалке рельсов / А.П. Бабич, В.Е. Сапожков, H.H. Разинькова и др. // Производство железнодорожных рельсов и колес. — 1978. — вып. 6. — С. 45 — 48.
- Исследование структуры и свойств рельсов, закаленных по всей длине с индукционного нагрева / Раузин Я.Р., Великанов A.B., Гордюк Ю.В., Шур Е.А. // Сталь. — 1965. — №12. — С. 1122-1126.
- Hoffman G. Oberflachenvergutung von Normalschienen durch induktive mittelfrequenz-Erwarmtung // Deutsche Eisenbahntechnik. — 1959. — ig. 7. — №1, S. 37-43.
- Некоторые вопросы поверхностной закалки железнодорожных рельсов по всей длине / Головин Г.Ф., Кущ Э.В., Смирнов В.И., Сучкоусов В.П.// Применение токов высокой частоты в электротермиии. — JL: Машиностроение, 1968.-С. 128-136.
- Прямой метод измерения остаточных напряжений в термически обра- — ботанных рельсах / Головин Г.Ф., Кущ Э.В., Мещеряков И.В., Смирнов В.И. // Промышленное применение токов высокой частоты. — М. — Л.: Машиностроение, 1966. — вып. 7. — С. 240-245.
- Головин Г.Ф. Остаточные напряжения, прочность и деформации при поверхностной закалке токами высокой частоты. — Л.: Машиностроение, 1973. — 144 с.
- Конюхов А.Д. Изменение остаточного напряженного состояния головок рельсов при эксплуатации // Труды ЦНИИ МПС. — 1966. — вып. 314. — С. 195-201.
- Скворцов О.С., Шварц Ю.Ф. Искривляемость концов объемно закаленных рельсов // Вестник ВНИИЖТ. — 1972. — №1. — С. 36-38.
- Головин Г.Ф., Зимин Н.В. Технология термической обработки металлов с применением индукционного нагрева. — Л.: Машиностроение, 1979. — 120 с.
- Щапов Н.П., Маханек А.С. Способ упрочнения рельса против излома // Авторское свидетельство №54425, 1939. — 1 с.
- Совершенствование технологии двухплоскостной правки и исследование влияния основных технологических факторов на напряженное состояние объемно закаленных рельсов / М.И. Федоров, Д.М. Рабинович, И.Я Винокуров, и др. // Повышение надежности верхнего строения пути и земляного полотна — С.: Средне-Урал. кн. изд., 1969. — С. 14-17.
- Induction heating keeps BSC Cumbria relies on sensible heat as only energy source // Steel Times. — 1988. — V. 216. — №5. — P. 255.
- Perr-in J.L. High strength rails with optimised residual stresses // Wheel/rail interface, IHHA Conference Proceedings, Moscow. — 1999. — P.245-253.
- Федин B.M. Закономерности объемно-поверхностного упрочнения деталей железнодорожного транспорта: Дис. …док. техн. наук.- М., ВНИИЖТ, 1996.-445 с.
- Великанов А.В. О принципах легирования высокоуглеродистых конструкционных сталей // МиТОМ. — 1980 . — №7. — С. 14-18.
- Бейн Э. Влияние легирующих элементов на свойства стали. — М.: Ме- таллургиздат, 1945. — 330 с.
- Гуляев А.П. Прочность стали и проблема легирования // МиТОМ. — 1961. — №7. — С. 23.
- Гуляев А.П. Теория предельного легирования // МиТОМ. — 1965. — №8. — С. 20.
- Браун М.П. Влияние легирующих элементов на свойства стали. — Киев: Гостехиздат УССР, 1962. — 189 с.
- Браун М.П. Комплекснолегированные конструкционные стали. — Киев: Наукова думка, 1965. — 292 с.
- Делле В.А. Легированная конструкционная сталь. — М.: Металлургиз- дат, 1953.-243 с.
- Садовский В.Д., Чупракова Н.П. Труды института металлофизики и металлургии, вып. 6, УФАИ СССР, 1945.
- Гольдштейн Я.Е. Низколегированные стали в машиностроении, 1963. -271 с.
- Гудремон Э. Специальные стали. — М.: Металлургия, 1966. — т. 1. — С. 512-734.
- Меськин В. С. Основы легирования стали. — М.: Металлургиздат, 1959.-688 с.
- Качанов H. Н. Прокаливаемость стали. — М.: Металлургия, 1978. -190 с.
- Вязников Н. Ф. Легированная сталь. — М.: Металлургиздат, 1963. -271 с.
- Пикеринг Ф. Б. Физическое металловедение и разработка сталей. — М.: Металлургия, 1982. — 182 с.
- Стародубов К. Ф. , Борковский Ю. 3., Некрасова С. 3. Влияние легирующих элементов на кинетику распада аустенита конструкционных «сталей // Упрочняющая термическая обработка проката. — М.: Металлургия, 1966. — Вып. 24. — С. 29-40.
- Раузин Я.Р. Термическая обработка хромистой стали. — М.: Машиностроение, 1978. — 277 с.
- RapatzF., Mirt О. / Stahl u. Eisen. — 1954. — H. 19. — S. 1195-1202.
- Узлов И.Г., Мирошниченко Н.Г. Термическое упрочнение проката. — М.: Металлургия, 1969. — Вып. 30. — С.
- Исследования по производству рельсов из легированных сталей разного состава /Э.П. Колосова, В.И. Сырейщикова, Е.А. Муравьев и др. // Производство железнодорожных рельсов и колес: Сб. научн. трудов. Харьков, 1977. — С. 64-67.
- Изыскание составов сталей и исследования основных параметров технологии производства рельсов высокой прочности / Д.С. Казарновский, H.H. Разинькова, А.П. Бабич и др. //
- Производство железнодорожных рельсов и колес: Сб. научн. трудов. Харьков. — 1977. — вып. 5. — С. 49-54.
- Разработка, освоение и внедрение низколегированной стали для железнодорожных рельсов тяжелых типов/Д.С. Казарновский, М.А. Гершгорн, Ф.Ф. Свириденко и др.// Сталь, 1965, №4, С. 355-357.
- Линев С.А. Результаты эксплуатационных испытаний опытных рельсов // Труды ЦНИИ МПС — 1966. — вып. 314. — С. 20-89.
- Комплексная методика оценки прокаливаемости применительно к рельсовым маркам стали / Б.К. Ушаков, В.М. Федин, А.И. Борц // Тезисы докладов конф. аспирантов и молодых ученых по проблемам железнодорожного транспорта. — М.: ГУП ВНИИЖТ, 2000. — С. 23 — 24.
- Люты В. Закалочные среды. Справочник. — Челябинск: Металлургия, 1990.-90 с.
- Zakharov S., Komarovsky I., Zharov I. Wheel flange/rail head wear- simulation // Wear. — 1998. — v. 215. — P. 18-24.
- Clayton P. Tribological aspects of wheel-rail contact: A review of recent experimental research // Wear . — 1996. — v. 191. — P. 170-183.
- Bolton P.J., Clayton P. Rolling-sliding wear damage in rail and tyre steels //Wear — 1984.-v. 93,- P. 145-165.
- Danks D., Clayton P. Comparison of the wear process for eutectoid rail steels: Field and laboratory tests // Wear — 1987. — v. 120. — P. 233-250.
- Krause H., Poll G. Wear of wheel-rail surfaces // Wear — 1986. — v. 113.- P. 103-122.
- Школьник Л.М. Методика усталостных испытаний. — М.: Металлургия, 1978. — 304 с.
- Шведков Е.Л. Элементарная математическая статистика в экспериментальных задачах материаловедения. — Киев: Наукова думка, 1975. — 111 с.
- Новицкий П.В., Зограф И.А. Оценка погрешностей результатов измерений. — Л.: Энергоатомиздат, 1985. — 247 с.
- Борц А.И., Федин В.М. Влияние легирования хромом на механические свойства остряков стрелочных переводов // 4-е Собрание металловедов России. Сб. материалов. Ч II. — Пенза, 1998. — С. 32 — 33.
- Борц А.И. Легирование хромом как средство повышения эксплуатационной стойкости остряков стрелочных переводов // Проблемы железнодорожного транспорта. — М, 1999. — С. 13 — 18.
- Федин В.М., Борц А.И. Остряки стрелочных переводов: перспективы повышения срока службы // III Всероссийская научн. — практ. конф. Современные технологии в машиностроении — 2000. Сб. материалов. Ч II. — Пенза, 2000. -С.185- 187.
- Конструкционные стали / Под ред. Н.Т. Гудцова // Справочник. — М., 1947.-482 с.
- Борц А.И., Кривоногов В.Г. Математическая оценка возможности развития поверхностных трещин при термической обработке остряков // Про- — блемы железнодорожного транспорта. — М, 1999. — С. 4 — 8.
- Борц А.И., Федин В.М. Двухсторонняя закалка как средство повышения прочностных свойств и улучшения технологии производства остряков стрелочных переводов// 4-е Собрание металловедов России. Сб. материалов. Ч II.-Пенза, 1998.-С. 48 -49, 161
- Способ термической обработки остряковых и рамных рельсов и устройство для его осуществления / В.М. Федин, Б.К. Ушаков, A.M. Никитин и др. // Патент РФ №2135607 — 1998. — 3 с.