- Введение
- Состояние Вопроса
- Анализ и статистика причин отказов подкладок с подушкой
- Результаты сравнительных испытаний подкладок с подушкой различных конструкций
- Металлографические исследования подкладки с подушкой в сечениях изломов
- Разработка методов расчета подкладки с подушкой, улучшение конструкции подкладки с подушкой
- Технико-экономическое обоснование эффективности применения подкладки с подушкой цельнолитой конструкции
- Заключение
- Список Литературы
Введение
Актуальность темы исследования определяется потребностями экономического роста нашей страны, требующего ускоренного развития транспорта.
Чтобы обеспечить возрастающие железнодорожные перевозки, создать условия для наиболее эффективного использования всех преимуществ железнодорожного транспорта, поднять скорости движения и веса поездов, необходимы опережающие темпы развития пути, его усиления и совершенствования [1].
В этом плане особое место занимают проблемы совершенствования таких элементов верхнего строения, как соединения и пересечения рельсовых путей [2]. Это объясняется их конструктивными особенностями, обусловливающими специфику взаимодействия с подвижным составом и особенности движения поездов по ним.
В развитии конструкций стрелочных переводов железных дорог России нужно отметить тенденцию к внедрению более мощных элементов переводов — остряков и крестовин, которые, в свою очередь, требуют надежного прикрепления их к основанию [3].
В настоящее время на дорогах магистрального железнодорожного транспорта эксплуатируется около 166 тысяч стрелочных переводов. Используется несколько десятков видов стрелочной продукции. Годовая потребность замены конструкций, выработавших свой ресурс, составляет 5,5 — 8,5 тысяч переводов, 6 — 7 тысяч полу-стрелок (ремкомплектов), 5 — 6 тысяч отдельных крестовин.
Важное место в подготовке технических средств к реализации программ ОАО «РЖД» по освоению перевозок занимает подготовка стрелочного хозяйства, так как на каждый километр развернутой длины путей магистральных железных дорог России приходится в среднем 1,3 стрелочных перевода [4]. Их конструкции и технология использования должны отвечать потребностям перевозочного процесса.
Разработка стрелочных переводов представляет собой комплекс работ, в которых участвуют 2 исследовательские, 7 конструкторских организаций и более 10 заводов-изготовителей. Возглавляет разработки лаборатория «Стрелочное хозяйство» научного центра «Путевая инфраструктура и вопросы взаимодействия колесо-рельс» Акционерного общества «Научно-исследовательский институт железнодорожного транспорта» (АО «ВНИИЖТ»).
Стрелочные переводы, работающие на российских железных дорогах в настоящее время, в основном удовлетворяют потребностям перевозочного процесса, однако с учетом времени, необходимого на подготовку стрелочного хозяйства к реализации перспективных задач, уже сегодня необходимо приступить к разработке и постановке на производство новых конструкций и модельных рядов стрелочной продукции [5].
Современный стрелочный перевод — это сложное изделие, состоящее из нескольких подсистем. Основными из них являются: металлические части, элементы скреплений, основание, приводы, переводные механизмы, системы замыкания подвижных элементов и контроля их положения, системы, обеспечивающие работу стрелочного перевода в зимних условиях.
В мировой железнодорожной практике проблеме стрелочных переводов уделяется большое внимание [6]. Это связано с тем, что стрелочные переводы являются наиболее дорогостоящими и сложными компонентами путевой инфраструктуры.
Целью проектирования новых стрелочных переводов (или других видов стрелочной продукции) является разработка конструкций, обеспечивающих выполнение требований безопасности, комфортабельности и заданных показателей эксплуатационной надежности.
Для создания высокоэффективных конструкций стрелочных переводов нужна современная элементная база и база комплектующих.
Принципиальные вопросы создания элементной базы для стрелочных переводов нового поколения решаются при разработке высокоскоростных стрелочных переводов и съездов. Но многие вопросы требуют дальнейшей отработки.
В настоящее время ставится цель повышения эффективности работы инфраструктуры. Для этой цели должны быть созданы путевые конструкции с ресурсом до 2,5 млрд. т брутто пропущенного груза. Для такого пути необходимы соответствующие ему стрелочные переводы.
Если исходить из того, что система обслуживания пути и его ремонтов должны работать с использованием известных технологий и машинных комплексов, то для такого пути нужны стрелочные переводы с ресурсом не менее 500 и 750 млн. т брутто.
Постановка задачи создания стрелочного перевода с ресурсом 500 млн. т брутто реальна. В настоящее время имеются необходимые конструктивные наработки и комплектующие. Соответствующие технологические возможности у российских стрелочных заводов есть. Ресурс в 750 млн. т брутто может быть достигнут после получения комплектующих способных обеспечить такой ресурс. В первую очередь, это относится к прокатным остряковым и другим рельсовым элементам. Предстоит также серьезная работа по элементной базе, в первую очередь, имеются в виду элементы скреплений.
Одной из основных причин расстройств рельсовой колеи на стрелочном переводе в зоне стрелки является выход из строя прикрепления рельсовых элементов к основанию, которое осуществляется с помощью подкладок с подушками. Совершенствование способов прикрепления позволит увеличить ресурс элементов стрелки, уменьшить расстройства рельсовой колеи на стрелках и тем самым снизить затраты на закупку и обслуживание стрелочных переводов, поэтому выбранная тема является важной и актуальной.
В настоящей работе представлены исследования, направленные на улучшение качеств важной компоненты элементной базы — стрелочных подкладок с подушкой (стрелочных башмаков).
Степень разработанности темы
Впервые теоретико-экспериментальный анализ нагруженности узлов, включающих в себя подкладки с подушкой, был дан в работе Петербургского государственного университета путей сообщения Императора Александра I. Полученные с помощью предложенного авторами метода расчетные напряжения коррелировали с результатами измерений в пути, однако расчетная модель подкладок с подушкой (пластина постоянной толщины, загруженная равномерно распределенной по поверхности нагрузкой) не позволяет оценивать влияние формы подкладок с подушкой на уровень напряжений в конкретных ее точках [7]. Поэтому для совершенствования подкладок с подушкой необходимо создание моделей подкладок с подушкой более точно моделирующих напряженно-деформированное состояние с учетом особенностей конструкции. Такие модели позволят использовать методы оптимизационного проектирования подкладок с подушкой, основанные на анализе фактических причин их отказов [8].
Большие работы по созданию новых и совершенствованию серийных стрелочных переводов проводились научными коллективами во Всероссийском научно-исследовательском институте железнодорожного транспорта (ВНИИЖТе) под руководством докторов технических наук Н.Н. Путри, Г.Г. Желнина, кандидатов технических наук А.М. Тейтеля, Л.Г. Крысанова, инженером В.Г. Донцом; в Петербургском государственном университете путей сообщения Императора Александра I (ПГУПС), бывшим Ленинградским институтом инженеров железнодорожного транспорта имени академика В. Н. Образцова, (ЛИИЖТе) под руководством профессоров, докторов технических наук С.В. Амелина, В.Ф. Яковлева, М.П. Смирнова, кандидатов технических наук В.И. Абросимова, Л.Н. Фролова; в Днепропетровском Государственном Техническом Университете Железнодорожного Транспорта (ДИИТе) — сотрудниками кафедры, возглавлявшейся профессором М.А. Фришманом, а затем профессором В.В.
Рыбкиным. Проектные работы по созданию и совершенствованию стрелочных переводов проводились коллективом Проектно-технологического конструкторского бюро по пути и путевым машинам (ПТКБ ЦП) под руководством кандидата технических наук Н.Н. Елсакова и инженеров Ю.Н. Петрова, А.К. Гучкова, С.О. Сурина.
Цель работы
Цель настоящей работы заключается в том, чтобы, опираясь на современные подходы, разработать метод получения эффективных и экономичных технических решений по конструкции подкладок с подушкой для стрелок стрелочных переводов массовых конструкций, позволяющий получить эффект при минимальных затратах на их реализацию. При этом, полученные решения должны сохранять генеральные технологические схемы изготовления элементов, применяемые на российских стрелочных заводах. Весь эффект должен достигаться за счет повышения инженерного уровня технических решений. Эти решения должны способствовать улучшению качества стрелочных переводов, снижению затрат материалов на их изготовление и расходов в эксплуатации.
Достижение цели включает в себя разработку конкретных задач исследования.
Задачи исследования
Задачами исследования являются: анализ эксплуатационных качеств элементов прикрепления остряков и рамных рельсов к основанию на основе прямых динамико-прочностных испытаний, анализ причин отказов подкладок с подушкой в эксплуатации, металлографические исследования подкладки с подушкой в сечениях изломов с целью определения причин появления и развития дефектов, разработка методов расчета напряженно-деформированного состояния подкладки с подушкой и получение на основании этих исследований оптимального технического решения, формирование предложений по использованию разработанного варианта.
Научная новизна работы
Научная новизна работы состоит в том, что в ходе исследования впервые выполнены экспериментальные и теоретические разработки по исследованию влияния конструкции скреплений на стрелке стрелочного перевода на их ресурс.
Получены сравнительные результаты динамико-прочностных испытаний подкладок с подушкой различных конструкций для определения их напряженно — деформированного состояния под воздействием поездов с учетом особенности разных технологий изготовления.
Представлен анализ сроков службы элементов прикрепления остряков и рамных рельсов к основанию.
Построена вероятностная модель работы металлических подкладок с подушкой стрелок стрелочных переводов, хорошо согласующаяся с результатами опытной эксплуатации, которая позволяет рассчитывать распределение отказов подкладок с подушкой в зависимости от характеристик металла, из которого они изготовлены, начальной затяжки прикрепителей и спектра напряжений, возникающих от поездной нагрузки.
Получены зависимости отказов подкладок с подушкой с помощью разработанной методики, которая дает возможность планировать замену подкладок на стрелочных переводах при смене основных металлических частей.
При исследовании выявлены новые виды дефектов причин отказов подкладок с подушкой.
Для выявления причин излома подкладок с подушкой был произведен химический анализ и металлографические исследования подкладки с подушкой в сечениях изломов.
Значимость работы
Теоретическая и практическая значимость работы обусловлена разработанным в диссертационном исследовании методическим подходом, основанным на применении математического моделирования и экспериментальных исследований, позволяющих получать практически полезные технические решения по разработке подкладок для стрелочных переводов нового поколения.
Методология исследования включает в себя методы:
- методы математической статистики, с помощью которых были получены сроки службы подкладок с подушкой;
- тензометрический метод исследования напряженного состояния подкладок;
- металлографический метод исследования, с помощью которого были выявлены причины излома подкладок с подушкой
- метод математического моделирования, с помощью которого была решена задача получения усовершенствованной конструкции подкладки с подушкой, позволяющей повысить ресурс стрелок стрелочных переводов за счет улучшенных прочностных характеристик.
Состояние Вопроса
Долгосрочной Программой развития ОАО «РЖД» до 2025 и Стратегией научно-технологического развития холдинга на период до 2025 года и на перспективу до 2030 года (Белая книга) предусмотрено повышение скоростей движения и весов поездов как в грузовом, так и в пассажирском движении, что требует усиления инфраструктуры железных дорог, в том числе и верхнего строения пути.
Важным направлением увеличения пропускной и провозной способности железнодорожных линий является повсеместное внедрение тяжеловесного движения, в том числе пропуск сдвоенных поездов.
Чтобы обеспечить возрастающие железнодорожные перевозки, создать условия для наиболее эффективного использования всех преимуществ железнодорожного транспорта, поднять скорости движения и вес поездов, необходимы опережающие темпы развития пути, его усиления и совершенствования. Одной из важнейших задач в этом аспекте является выбор конструкций стрелочных переводов железных дорог России. На современном этапе необходимо отметить тенденцию к внедрению более мощных элементов переводов, в свою очередь, требующих надежного прикрепления их к основанию.
В настоящее время работы по созданию новых стрелочных переводов ведутся специалистами лаборатории научного центра «Путевая инфраструктура и вопросы взаимодействия колесо-рельс» АО «ВНИИЖТ» под руководством профессора Б.Э. Глюзберга, кандидатом технических наук М.И. Титаренко; кафедрой «Транспортное строительство» РУТ МИИТ, возглавляемой профессором А.А. Локтевым, кандидатом технических наук В.В. Королевым.
В современных условиях одним из самых актуальных направлений являются исследования по увеличению ресурса и стабильности работы стрелочных переводов и их элементов [9].
Важными элементами, определяющими ресурс и стабильную работу стрелочных переводов, являются скрепления. В зоне стрелки такими элементами являются подкладки с подушками, на которые опираются остряки стрелочного перевода. Подкладки с подушкой, изготавливаются с использованием различных технологий (рисунок 1.1). Назначение подкладок с подушкой — передача нагрузки от подвижного состава на брус и создание условий перемещения подошвы остряков при переводе их из одного положения в другое [10].
1 — шуруп;
2 — подкладка;
3 — приварная подушка;
4 — упругая клемма;
5 — остряк;
6 — рамный рельс;
7 — клеммный болт;
8— гайка;
9 — упругая шайба;
10 — клемма;
11 — реборда


Рисунок 1.1 — Схема закрепления подкладки с подушкой на стрелке стрелочного перевода
Подкладки с подушкой, прикрепленной к подкладке на заклёпках, являлись на протяжении длительного времени единственной конструкцией, применявшейся на стрелочных переводах всех типов и марок (рисунки 1.2-1.3). Обладая проверенными эксплуатационными качествами, подкладки с подушкой на заклёпках имеют недостатки, связанные с расстройством заклёпочных соединений, что приводит к отказам в работе подкладок с подушкой и заклёпочных соединений [11, 76].
Освоение новых технологий дало возможность использовать для изготовления подкладок с подушкой штамповку и сварку.
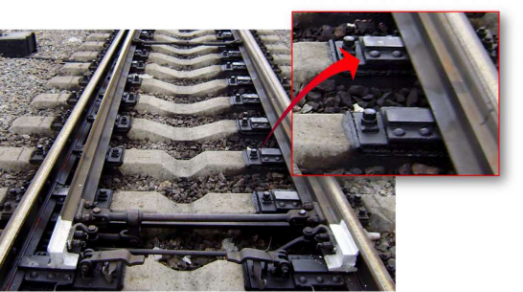
Рисунок 1.2 — Конструкция стрелки стрелочного перевода, оснащенная подкладками с подушкой на заклёпках
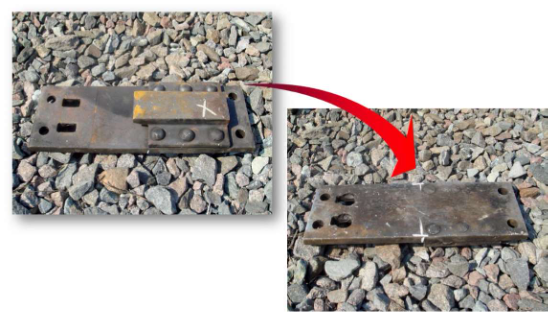
Рисунок 1.3 — Подкладка с подушкой, изготовленная с использованием технологии на заклепках
Внедрение технологии штамповки позволяет изготовить подкладку с подушкой из одной монолитной заготовки (рисунки 1.4-1.5). Такие подкладки с подушкой дешевы в изготовлении, однако использование технологии горячей штамповки для изготовления подкладок с подушкой связано с образованием надрывов металла и концентраторов напряжений в зоне среза металла подкладки с подушкой. Надрывы металла и концентраторы напряжений приводят к преждевременному отказу подкладок.
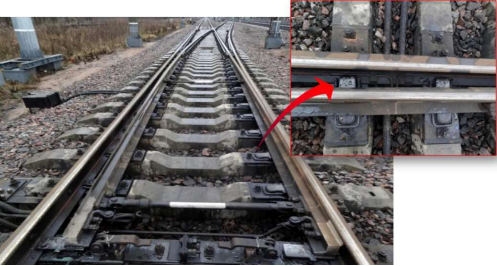
Рисунок 1.4 — Конструкция стрелки стрелочного перевода, оснащенная подкладками с выштампованной подушкой
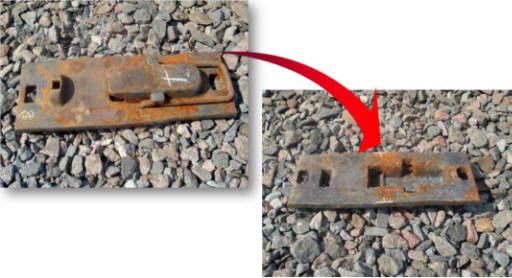
Рисунок 1.5 — Подкладка с подушкой, изготовленная с использованием технологии горячей штамповки
Альтернативой применения заклепочных соединений и технологии горячей штамповки являются сварочные технологии.
При использовании технологии сварки подкладка с подушкой изготовляется из двух сваренных между собой элементов (подкладки и подушки). Реализованы два способа сварки: сварка через отверстия в подкладке (рисунки 1.6-1.7), что связано с ослаблением подкладки, и продольная сварка без ослабления подкладки (рисунки 1.8-1.9). Надрыв металла при просекании отверстий в подкладках, ослабление сечений подкладки за счёт отверстий и наличие сварных зон приводят к снижению прочностных и эксплуатационных качеств подкладок. Использование продольной сварки не связано с ослаблением сечений подкладки, что уменьшает предпосылки к преждевременному выходу их из строя.
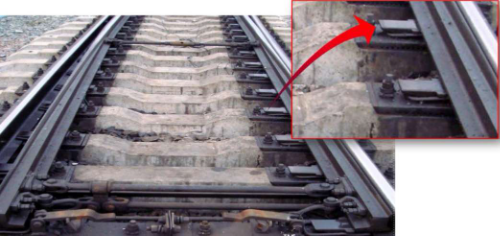
Рисунок 1.6 — Конструкция стрелки стрелочного перевода, оснащенного сварными подкладками с подушкой
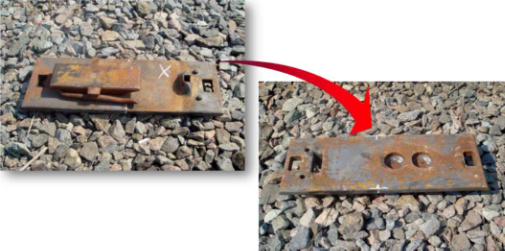
Рисунок 1.7 — Подкладка с подушкой, изготовленная с использованием технологии сварки
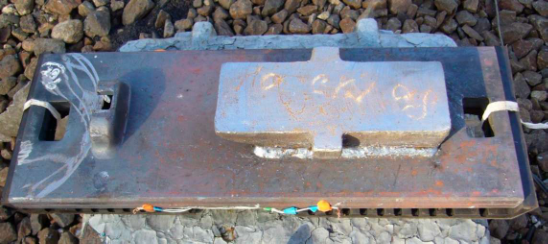
Рисунок 1.8 — Подкладка с подушкой, изготовленная с использованием технологии продольной сварки (вид сверху)
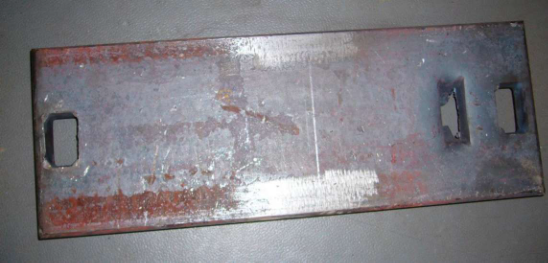
Рисунок 1.9 — Подкладка с подушкой, изготовленная с использованием технологии продольной сварки (вид снизу)
В странах Евросоюза используются различные подкладки с подушкой. Например, подкладки с массивной подушкой, приваренной к подкладке продольными швами и подкладки с подушкой, изготовленные методом литья (рисунки 1.10-1.11) [12, 13].
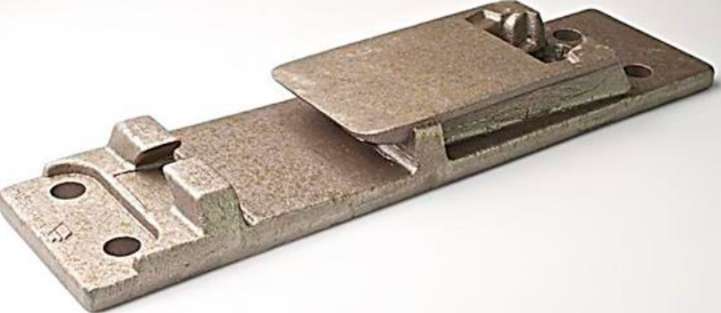
Рисунок 1.11 — Подкладка с подушкой европейского производства, изготовленная методом литья
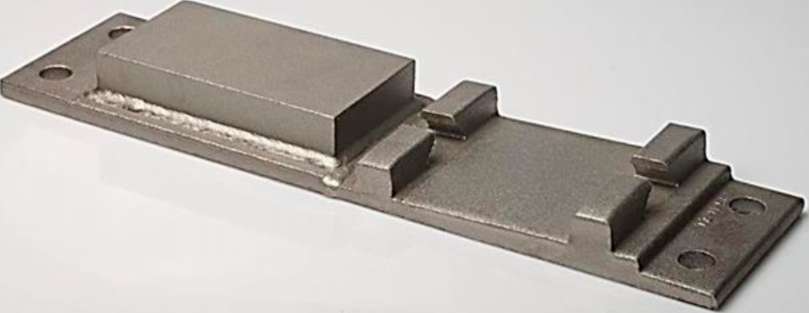
Рисунок 1.10 — Подкладка с массивной подушкой, приваренной к подкладке продольными швами
Некоторые подкладки с подушкой европейского производства изготовлены из чугуна с шаровидным графитом и оснащены внутренним фиксатором рамного рельса (рисунок 1.12) [14, 15]. Внутренняя сторона рамного рельса закрепляется упругой скобой через подушку подкладки с подушкой. Данный вид скрепления улучшает прикрепление рамного рельса к подкладке с подушкой, а упругая пластина служит амортизатором для горизонтальных поперечных сил.
В ряде случаев подушки покрываются антикоррозионным, молибденовым покрытием (рисунок 1.13) [16] или пластинами из не нуждающейся в смазке износостойкой бронзы F66 (С^п8) с графитовыми вставками или без них (рисунок 1.14) [17]. Существуют подкладки с подушкой, оснащённые специальным съёмным вкладышем для улучшения скольжения (рисунок 1.15) [18].
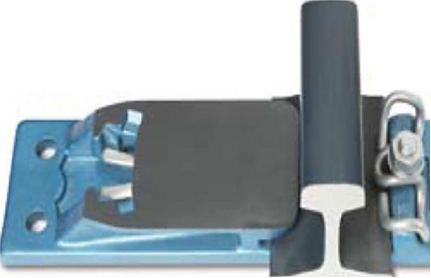
Рисунок 1.12 — Подкладка с подушкой, изготовленная методом литья из чугуна с шаровидным графитом
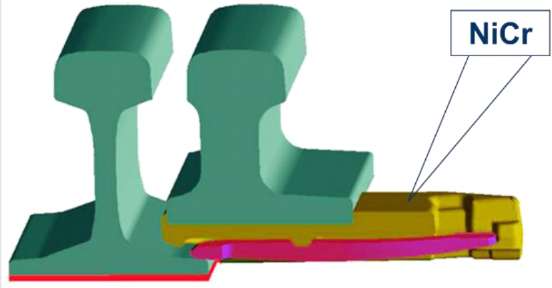
Рисунок 1.13 — Подушка подкладки с напылением из хрома и никеля
Дополнительные покрытия подкладок с подушкой служат для уменьшения переводных усилий (трение) подошвы остряка и повышают износостойкость поверхностей, по которым перемещаются остряки.
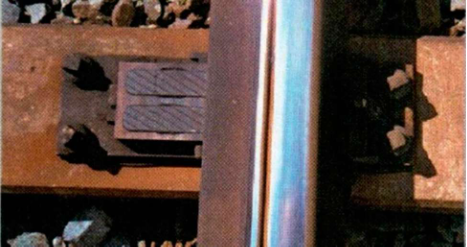
Рисунок 1.14 — Вставки в подушку подкладки «экоглисс» для снижения трения при переводе стрелки
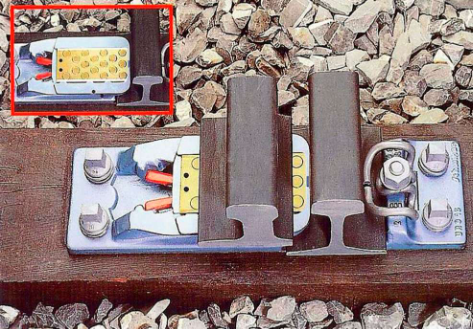
Рисунок 1.15 — Подкладка с подушкой, оснащённая специальным съёмным вкладышем для улучшения скольжения, без смазывающих веществ во время эксплуатации
Главная цель разработок — повышение ресурса стрелок стрелочных переводов. Цель настоящей работы заключается в том, чтобы, опираясь на современные подходы, разработать метод получения эффективных и экономичных технических решений по совершенствованию подкладок с подушкой для стрелок стрелочных переводов, позволяющий получить эффект увеличения ресурса стрелок при минимальных затратах на реализацию этих решений. При этом, полученные решения должны сохранять технологические схемы изготовления элементов. Весь эффект должен достигаться за счет повышения уровня технических решений [19]. Эти решения должны способствовать улучшению качества стрелочных переводов, снижению затрат материалов на их изготовление и расходов в эксплуатации.
Достижение цели включает в себя разработку конкретных задач, которые иллюстрирует рисунок 1.16:
- анализ сроков службы элементов прикрепления остряков и рамных рельсов к основанию, анализ причин отказов подкладок с подушкой;
- металлографические исследования подкладок с подушкой в сечениях, в которых в эксплуатации возникают изломы и дефекты;
- сравнительные динамико-прочностные и полигонные испытания подкладок с подушкой различных конструкций;
- разработка методов расчета подкладок с подушкой и получение на основании расчета нового технического решения;
Анализ и статистика причин отказов подкладок с подушкой
Дефекты подкладок с подушкой
Классификация дефектов подкладок с подушкой
В процессе эксплуатации отказы подкладок с подушкой на заклёпках происходят по причине ослабления заклепочных соединений, трещин и изломов подкладок, проходящих через отверстия под заклёпки в зоне внутренней кромки подошвы рамных рельсов, смятия и износа подушек.
Появление и развитие дефектов подкладок с подушкой на заклёпках, приводит не только к отказам в работе самих подкладок с подушкой, но и препятствуют переводу остряков стрелок. Используемая при их изготовлении технология не полностью обеспечивает эксплуатационную стойкость скреплений, отвечающую современным эксплуатационным требованиям [20].
На рисунке 2.1 показан типичный излом подкладок с подушкой на заклёпках.
Под воздействием динамических сил, передаваемых на подкладки от рельсов, отказ подкладок с подушкой, изготовленных с использованием технологии сварки, происходит из-за трещин и изломов в зоне внутренней кромки подошвы рамных рельсов от сварных швов ближайшего к кромке рамного рельса отверстия, или в зоне термического влияния сварных швов [21].
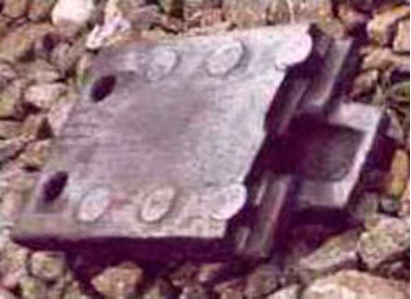
Рисунок 2.1 — Излом подкладки с подушкой на заклёпках
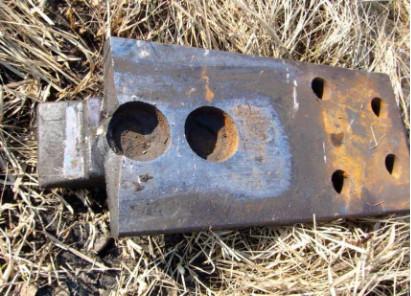
Рисунок 2.2 — Излом подкладок с подушкой, изготовленных с использованием сварки через отверстия в подкладке
На рисунке 2.2 показан типичный излом подкладок с подушкой, изготовленных с использованием сварки через отверстия в подкладке.
В процессе эксплуатации отказ подкладок с подушкой, изготовленных методом горячей штамповки, происходит по причине трещин и изломов подкладок по внутренней кромке рамных рельсов в зоне среза и выдавливания металла для формирования носовой части подушки подкладки, из-за воздействия сил, передаваемых от остряка и рамного рельса на подкладку в месте резкого изменения сечения подкладки [22].
На рисунке 2.3 показан типичный излом подкладок с подушкой, изготовленных методом штамповки.
Выше перечисленные повреждения подкладок с подушкой приведены в «Классификаторе дефектов и повреждений элементов стрелочных переводов» [23], который был разработан лабораторией «Стрелочное хозяйство» ОАО «ВНИИЖТ», утвержден распоряжением ОАО «РЖД» № 1653р и введен в действие с 1 сентября 2012 года, в разделе «Дефекты в подкладках с подушками», где приведены основные дефекты подкладок с подушками, наименование дефектов и повреждений элементов, основные причины их появления и развития, расположение дефектов по длине элемента, обозначение, схематическое изображение дефекта (ДПС 100 К, ДПС 100 Ш, ДПС 100 С1) [24, 25].
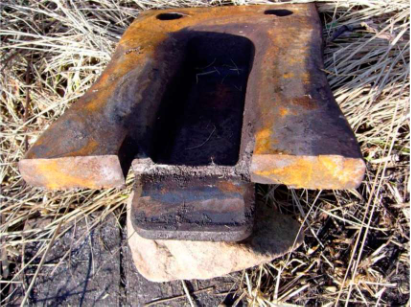
Рисунок 2.3 — Излом подкладок с подушкой, изготовленных методом горячей штамповки
В таблице 2.4 представлен раздел «Дефекты в подкладках с подушками» из классификатора дефектов и повреждений элементов стрелочных переводов [23].
Наименование дефектов и повреждений элементов и основные причины их появления и развития | Обозначение | Схематическое изображение дефекта |
---|---|---|
Изломы и трещины в подкладке с подушкой на заклепках | ДПС 100 К | ![]() |
Изломы и трещины в подкладке с подушкой изготовленной методом штамповки | ДПС 100 Ш | ![]() |
Изломы и трещины в подкладке с подушкой изготовленной с использованием сварки через отверстия в подкладке | ДПС 100 С1 |
Характер дефектов у подкладок с подушкой на заклепках, изготовленных методом штамповки и с использованием сварки, схож. Это дефекты усталостного происхождения. Основными причинами изломов являются: воздействия сил, передаваемых от остряка и рамного рельса на подкладку, ослабления заклепочных соединений у подкладок с подушкой на заклепках, в месте резкого изменения сечения подкладок с подушкой, изготовленных методом горячей штамповки, трещины и изломы в сварных швах у подкладок с подушкой, изготовленных с применением сварки [26].
Классификация новых дефектов подкладок с подушкой
В последнее время на дорогах стали выявляться новые виды дефектов подкладок с подушкой, которые не были внесены в «Классификатор дефектов и повреждений элементов стрелочных переводов» [27].
На рисунке 2.5 показан новый вид дефекта подкладки с приварной подушкой, обнаруженный при обследовании стрелочных переводов на Московской железной дороге [28].

Рисунок 2.5 — Новый вид дефекта подкладки с приварной подушкой
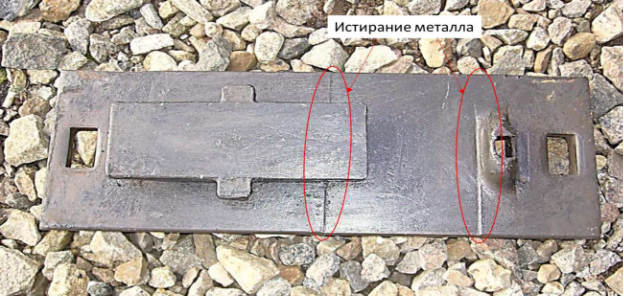
Рисунок 2.6 — Новый вид дефекта подкладки с приварной подушкой — истирание металла под рельсом
Наиболее вероятная причина отказов «нового» вида у подкладок с подушкой, изготовленных с использованием технологии сварки, — нарушение технологии режима сварки, наличие неметаллических включений, трещин в месте сварного шва.
Еще один вид дефекта подкладки с приварной подушкой — истирание металла под рельсом (рисунок 2.6) [29].
В данном случае причина отказов по этому виду дефектов — недостаточная износостойкость металла подкладки.
Выявленные виды дефектов должны быть внесены в очередную редакцию классификатора дефектов и повреждений элементов стрелочных переводов при его следующей корректировке [30]. В таблице 2.7 представлены предлагаемые характеристики новых видов дефектов подкладок с подушкой: наименование дефектов и повреждений элементов и основные причины их появления и развития, расположение дефектов по длине элемента, обозначение, схематическое изображение дефекта, согласно существующего «Классификатора дефектов и повреждений элементов стрелочных переводов» для дальнейшего внесения дополнения при переработки для новой редакции нормативного документа.
Наименование дефектов и повреждений элементов и основные причины их появления и развития | Расположение дефектов по длине элемента | Обозначение | Схематическое изображение дефекта |
---|---|---|---|
Излом зоны сварного шва в отверстии в подкладке с подушкой | — | ДПС 101 С1 | |
Истирание металла под рельсом на подкладках с подушкой | — | ДПС 161 |
Основной способ обнаружения большинства дефектов на стрелочных переводах — внешний осмотр и прямые измерения. Только часть дефектов, возникающих в рельсовых элементах переводов, может выявляться с помощью существующих ультразвуковых дефектоскопов [31]. Интенсивность роста дефектов в основном зависит от силового воздействия подвижного состава на путь и состояния перевода. Поэтому задача по снижению дефектности переводов — своевременно выполнять на переводах ремонтно-профилактические работы, выдерживать требуемые нормы содержания колеи. Необходимо также своевременно устранять различные просадки и неровности, приводящие к росту динамических сил [32].
Для планирования работ по замене дефектных элементов, необходимо своевременно вносить дополнения и изменения в «Классификатор дефектов и повреждений элементов стрелочных переводов». Это позволит своевременно планировать замену этих элементов и совершенствовать систему обслуживания переводов в целом [33].
Методика анализа показателей эксплуатационной надежности подкладок с подушкой
Применительно к стрелочным переводам, надежность следует понимать, как способность обеспечивать безопасное и комфортабельное движение по ним подвижного состава с установленными скоростями при существующей системе их содержания и ремонтов в течение установленного срока службы.
Каждый элемент стрелочного перевода целесообразно рассматривать как невосстанавливаемый, так как, в отличие от рельсов, элементы стрелочных переводов устанавливаются в путь отдельно, а не партиями, и решение об изъятии их из пути принимается также отдельно для каждого элемента.
Надежность невосстанавливаемых систем (элементов) может быть охарактеризована распределением наработки элементов до отказа, вероятностью их безотказной работы, интенсивностью отказов и средним ресурсом [34, 35, 36]. Первые три показателя в силу вероятностных условий нагружения в процессе работы в пути и детерминированных свойств каждого элемента после его изготовления, не постоянны в различные периоды эксплуатации.
Для получения показателей надежности сбор данных по отказам подкладок с подушкой велся согласно методике эксплуатационных наблюдений за работой стрелочных переводов. Данные сплошной смены металлических частей стрелочных переводов не анализировались, так как не связаны с показателями надежности подкладок. Данные выхода элементов в результате возникновения случаев особого учета в анализе также не использовались [37, 38].
Для получения статистического материала была рассмотрена информация по отказам подкладок с подушкой стрелочных переводов, изъятых из пути в 2013-2018 гг. на Дальневосточной, Забайкальской, Восточно-Сибирской, Красноярской, Южно-Уральской, Западно-Сибирской, Куйбышевской, Октябрьской, Горьковской, Московской, Северо-Кавказской и Северной железных дорогах, при грузонапряженностях до 100 млн. ткм брутто на км в год, осевых нагрузках — до 21,7 тс, скоростях по основному направлению — до 100, по ответвленному — до 40 км/ч.
При первичной обработке данных из таблиц, содержащих информацию об отказах элементов, полученных с дистанций пути, выбирались данные, удовлетворяющие требованиям, описанным выше. Данные по подкладкам с подушкой в зависимости от наработки до изъятия группировались по интервалам А1 = 50 млн. т брутто.
Методика получения аналитических зависимостей
В качестве входной информации при определении аналитических функций, аппроксимирующих статистические зависимости основных показателей надежности подкладок с подушкой, использовались зависимости, полученные в результате статистической обработки исходных данных.
Применение классических методов теории надежности для определения основных показателей надежности элементов стрелочных переводов, характеризующих работу элементов, таких как: наработка до отказа, вероятность безотказной работы, среднее время безотказной работы (ресурс), интенсивность отказов — приводит к большим количественным, а во многих случаях и качественным погрешностям [39].
Для решения задачи часто применяют кусочные модели с аппроксимацией зависимостей показателей надежности на каждом отдельном участке самостоятельной зависимости. [40, 41] Основными недостатками кусочных моделей являются интуитивный выбор их основных параметров и вытекающие отсюда трудности в сопоставлении данных о работе исследуемых элементов или конструкций в различных условиях работы. Затруднительно прогнозирование изменений показателей надежности при изменении их конструкции или условий эксплуатации, а также использование кусочно-линейных и кусочно- экспоненциальных зависимостей в аналитических преобразованиях, в случаях построения статистических моделей надежности.
И классические и кусочно-линейные модели имеют недостатки, не дающие возможности эффективно использовать их для анализа работы подкладок с подушкой. Для этих целей была использована модель на основе специальных функций, предложенных в лаборатории «Стрелочное хозяйство» ВНИИЖТа [42, 43].
Модель описывает изменение каждого показателя надежности за весь период работы подкладок с подушкой в виде единой непрерывной аналитической функции с областью определения аргумента 0 <t <Ттах. На каждом из этапов работы вид зависимости для показателей надежности близок к характерному для этого этапа. Границы переходов между этапами работы элементов или конструкций получаются для модели на основе объективных показателей соответствия, т.е. совокупности исходных данных, минимального значения суммы квадратов отклонений фактических данных от получаемых с помощью модели (признак наиболее распространенного метода аппроксимации экспериментальных зависимостей — метод наименьших квадратов). Модель обеспечивает получение наилучшего приближения не для какого-нибудь одного из показателей надежности, но одновременно для всех рассматриваемых показателей надежности, за счет использования данных за весь период эксплуатации элементов и объективного получения границ переходов от начального к стабильному и от стабильного к завершающему периодам эксплуатации.
Ее основой является зависимость для интенсивности отказов Ь^), которая дает возможность реализовать практически любую зависимость интенсивности отказов от наработки.
В соответствии с этой моделью период службы элементов характеризуется тремя основными этапами:
- начальный с ранними отказами из-за дефектов материалов или производственных дефектов;
- стабильный период работы со «случайными» отказами, как правило, связанными с особенностью работы конкретного элемента;
- период интенсивных отказов, связанных с накопившимися повреждениями и предельным износом элементов.
Каждый из коэффициентов зависимости L(t) (формула в системе (2.3)) имеет четкий физический смысл, значительно облегчающий анализ изменения интенсивности отказов в процессе наработки (рисунок 2.8):
- а — скорость изменения интенсивности отказов на основном этапе эксплуатации;
- b — интенсивность отказов на начальном этапе эксплуатации; ti и to — точки перехода между этапами работы элементов; k01 и k02 — показатели скорости изменения интенсивности отказов в начальный период эксплуатации;
- k11 иk12 — показатели скорости изменения интенсивности отказов в завершающий период эксплуатации;
- t — показатель, связанный с наработкой элемента до отказа.
Так как все эти характеристики получены объективно, они могут служить для анализа влияния условий работы подкладок с подушкой на показатели надежности, для прогностических исследований, для предпроектных расчетов и т. д. [44, 45].
По исходным статистическим данным определяется зависимость L(t) и проводится аппроксимация по зависимости L(t) (2.3). На этом этапе определяются коэффициенты a, b, k01, k02, кц, k12, t0 в численном выражении. Далее вычисляются аналитические и статистические зависимости остальных уравнений, входящих в систему (2.3).
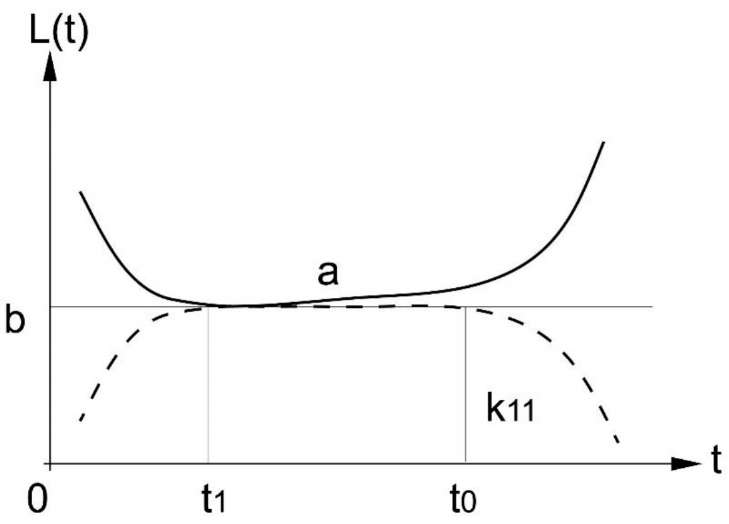
Рисунок 2.8 — Зависимость интенсивности отказов от наработки
Статистика отказов подкладок с подушкой
На рисунках 2.9-2.10 показаны графики изменений показателей надежности подкладок с подушкой: изготовленные с использованием технологии горячей штамповки, изготовленные с использованием технологии на заклепках, изготовленные с использованием технологии сварки, отказавших в промежуток времени с 2013 по 2018 годы, полученные по данным с дорог. Там же приведены их аналитические аппроксимации.
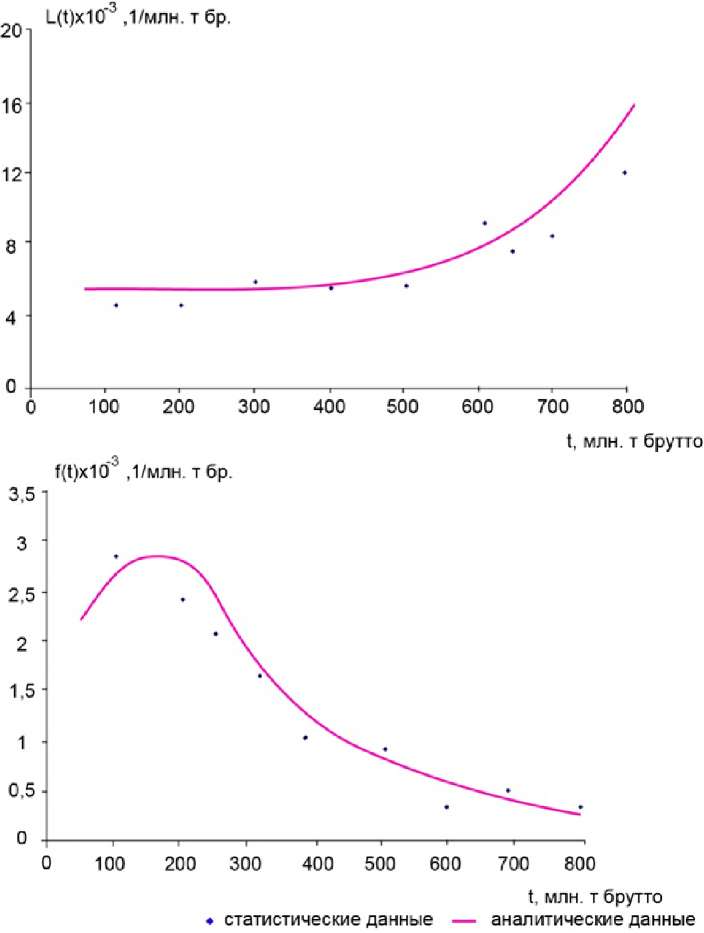
Рисунок 2.9 — Графики показателей надежности подкладок с подушкой, изготовленных с использованием технологии горячей штамповки, изъятых из пути по дефектам за 2013-18 гг.: а) вероятность безотказной работы подкладок с подушкой, б) интенсивность отказов подкладок с подушкой, в) плотность распределения наработки до отказа подкладок с подушкой
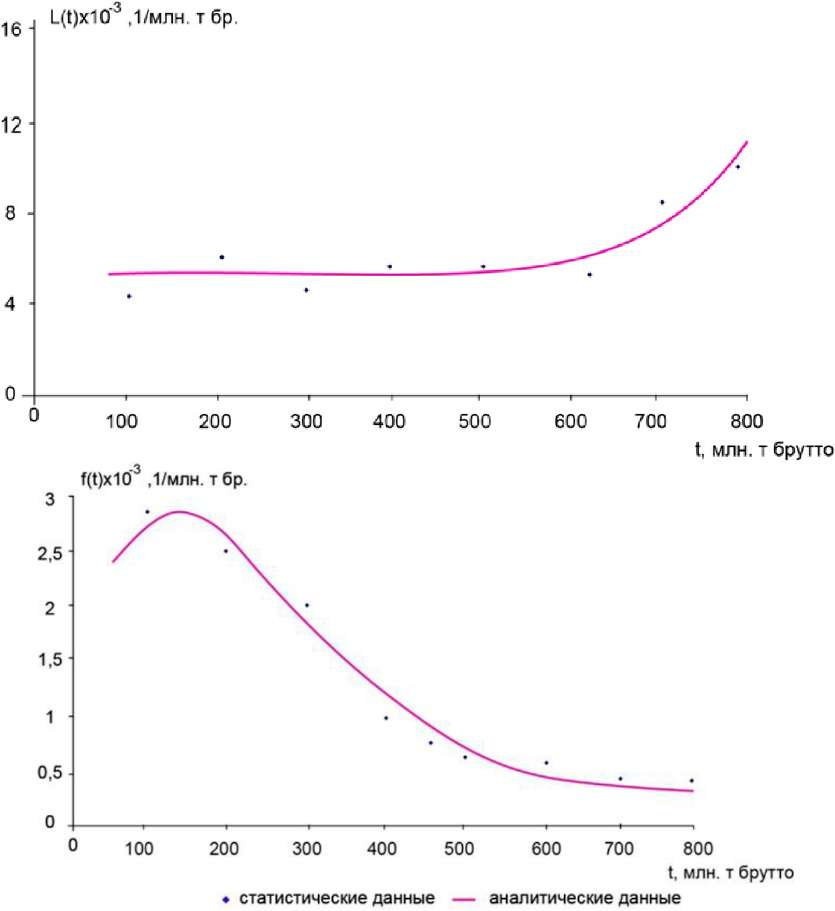
Рисунок 2.10 — Графики показателей надежности подкладок с подушкой, изготовленных с использованием технологии на заклепках, изъятых из пути по дефектам за 2013-2018 гг.: а) вероятность безотказной работы подкладок с подушкой, б) интенсивность отказов подкладок с подушкой, в) плотность распределения наработки до отказа подкладок с подушкой
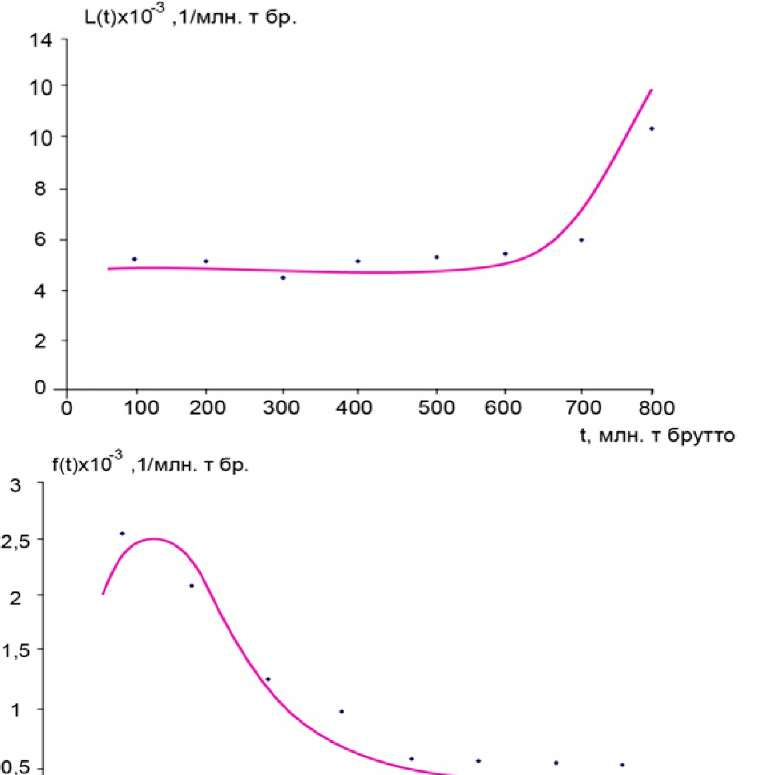
Рисунок 2.11 — Графики показателей надежности подкладок с подушкой изготовленные с использованием технологии сварки, изъятых из пути по дефектам за 2013-2018 гг.: а) вероятность безотказной работы подкладок с подушкой, б) интенсивность отказов подкладок с подушкой, в) плотность распределения наработки до отказа подкладок с подушкой
Интенсивность отказов подкладок с подушкой с начала эксплуатации стрелочных переводов до прохода по ним 500-600 млн. т брутто близка к постоянной. Это подтверждают результаты аналитической аппроксимации вероятности безотказной работы и интенсивности отказов подкладок с подушкой, представленные на рисунках 2.9 — 2.11.
Повышение интенсивности отказов подкладок с подушкой начинается после пропуска по стрелочному переводу около 500 млн. т брутто. Практически значимое возрастание начинается после прохода 500-600 млн. т брутто. После достижения этой
наработки наблюдается резкое возрастание интенсивности отказов подкладок с подушкой, имеющее характер, близкий к экспоненциальному. Несмотря на то, что фактическая интенсивность отказа подкладок с подушкой (с учетом доли отказавших в одиночном порядке элементов) даже после наработки свыше 600 млн. т меньше, чем остряков, экспоненциальный характер нарастания интенсивности отказов свидетельствует об исчерпании ресурса подкладок с подушкой. Использовать их после наработки 500 млн. т брутто не целесообразно.
В настоящее время ставится задача создания пути с ресурсом 1,5 млрд. т. Для этого конструкция стрелочных переводов должна, отвечая требованиям перевозочного процесса, обеспечивать минимум затрат на ведение путевого хозяйства. Обслуживание и замена стрелочных переводов должны быть адаптированы к существующим ремонтным схемам и системе текущего содержания пути. Ремонтные схемы по замене стрелочных переводов привязаны к периодичности замены элементов верхнего строения пути [46, 47]. Требования к конструкции стрелочных переводов в рассматриваемой задачи могут быть сформулированы следующим образом.
Учитывая высокую первоначальную стоимость замены стрелочных переводов, их конструкция должна обеспечивать кратность замены металлических частей перевода в периоды между капитальными ремонтами пути и привязку к действующим схемам его ремонтов. Затраты на обслуживание стрелочных переводов между их заменой должны быть минимальны. Конструкция элементов стрелочных переводов также должна обеспечивать кратность замены между периодами замены всего перевода [48].
Показатели надежности элементов, а также ресурс их основных элементов существенным образом зависят от условий эксплуатации, в первую очередь, от скоростей движения поездов, грузонапряженности, осевых нагрузок и состояния ходовых частей подвижного состава.
Для сохранения соответствия конструкции стрелочных переводов существующей системе обслуживания и действующим ремонтным схемам при изменении условий эксплуатации, в частности, при повышении осевых нагрузок подвижного состава, необходимо, чтобы в этих условиях показатели надежности подкладок с подушкой стрелочных переводов были не ниже, чем у существующих стрелочных переводов в современных условиях.
Влияние осевых нагрузок на отказы подкладок с подушкой стрелочных переводов наиболее массовых конструкций исследовалось по отказам элементов стрелочных переводов на дорогах ОАО «РЖД». Для получения результатов исследованы данные по отказам 180 подкладок с подушкой разных конструкций. Исследовалась работа стрелочных переводов на участках со средними статическими осевыми нагрузками 7,4; 10,9; 11,3; 12,2; 16,0; 16,3; 17,9 и 20,7 т [49, 50, 51].
Обработка полученных данных позволила получить корреляционные зависимости для основных показателей надежности подкладок с подушкой, что дало возможность экстраполировать результаты эксплуатации для условий работы при высоких осевых нагрузках.
Исходя из того, что для сохранения ремонтных схем вероятность безотказной работы и интенсивность отказов на момент замены стрелочных переводов должны быть такие же, как и в настоящее время, получим необходимое увеличение ресурса элементов стрелочных переводов.
При повышенных нагрузках следует усилить конструкцию подкладок с подушкой, что целесообразнее всего сделать за счет изменения конструкции и технологии их изготовления.
Распределение отказов подкладок с подушкой по видам дефектов (причины отказов)
Уровень напряжений, возникающих в подкладках с подушкой, превышает наибольшие напряжения, допускаемые для рельсовых элементов. В результате этого в эксплуатации в подкладках с подушкой могут возникать и развиваться дефекты, приводящие к их отказам [52].
На дорогах России имеют место три вида дефектов подкладок с подушкой, служащие причиной их отказов: дефект ДПС 100 К в виде излома и трещины в подкладке с подушкой на заклепках; дефект ДПС 100 Ш — изломы и трещины в подкладке с подушкой, изготовленной методом штамповки; дефект ДПС 100 С1 — изломы и трещины в подкладке с подушкой, изготовленной с использованием сварки через отверстия в подкладке [53].
Общий анализ отказов подкладок с подушкой показал, что их отказы зависят от интенсивности движения поездов и пропущенного тоннажа по прямому и по боковому направлениям. Получение статистически значимых зависимостей при разгруппировке по направлениям движения и пропущенного тоннажа для подкладок с подушкой затруднено из-за общего малого числа их отказов.
Полученные данные по отказам подкладок с подушкой различных конструкций на стрелочных переводах приведены на рисунках 2.12 — 2.14.
Наработка до отказа подкладок с подушкой зависит от интенсивности движения поездов и пропущенного тоннажа. Так, средняя наработка до отказа подкладок с подушкой по данным, приведенным на рисунках 2.12 — 2.14, составляет для стрелочных переводов соответственно 316,2 млн. т брутто.
Выводы
1. Наблюдения за работой подкладок с подушкой показывают, что главным фактором, определяющим отказы подкладок с подушкой, является их конструкция.
2. В ходе исследований выявлено несколько дефектов подкладок с подушкой, которые не включены в «Классификатор дефектов и повреждений элементов стрелочных переводов».
Наиболее вероятная причина отказов «нового» вида у подкладок с подушкой, изготовленных с использованием технологии сварки, — нарушение технологии режима сварки, наличие неметаллических включений, трещин в месте сварного шва.
3. Другой «новый» вид дефекта стрелочных башмаков — истирание металла под рельсом. В данном случае причина отказов по этому виду дефектов — недостаточная износостойкость металла подкладки.
Наработка до отказа подкладок с подушкой зависит от интенсивности движения поездов и пропущенного тоннажа. Так, средняя наработка до отказа подкладок с подушкой по данным составляет 316,2 млн. т брутто. Средняя наработка до одиночного изъятия из пути подкладок с подушкой за период с 2013 года по 2018 год имела колебания от 300 до 350 млн. т брутто.
4. Проведенный анализ позволяет сделать вывод, что дефекты возникают в местах недостаточной прочности конструкций. Для исследования напряженного состояния подкладок с подушкой в местах возникновения дефектов необходимо провести сравнительные динамико-прочностные испытания подкладок с подушкой, изготовленных по различным технологиям.
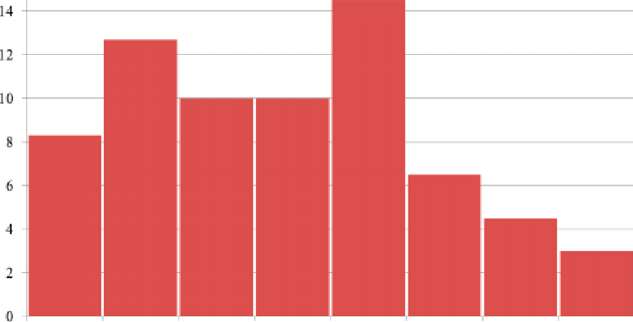
Рисунок 2.12 — Распределение наработки до отказов подкладок с подушкой, изготовленных с использованием технологии на заклепках
Рисунок 2.13 — Распределение наработки до отказов подкладок с подушкой, изготовленных с использованием технологии сварки
Рисунок 2.14 — Распределение наработки до отказов подкладок с подушкой, изготовленных с использованием технологии сварки горячей штамповки
Результаты сравнительных испытаний подкладок с подушкой различных конструкций
Методика проведения испытаний
Испытания по определению напряженно-деформированного состояния подкладок с подушкой проводились на Московской железной дороге.
Испытываемые элементы устанавливались на стрелочном переводе проекта 2750.
Перед проведением испытаний состояние стрелочного перевода было приведено в соответствие с нормативными документами по текущему содержанию пути.
Испытания проводились под воздействием графиковых поездов, обращающихся по месту укладки стрелочного перевода. Скорости поездов по основному пути — 80 км/ч, по ответвлению — до 50 км/ч.
Подвижной состав: грузовые вагоны — порожние и груженые с различной загрузкой, вплоть до нормативной загрузки. Локомотивы ВЛ10 и ВЛ11.
Испытания подкладок с подушкой проводились в два этапа. На первом этапе испытаниям подвергались подкладки с подушкой, работавшие в составе эксплуатируемого стрелочного перевода.
По результатам этого этапа определялись места расположения наиболее нагруженных подкладок в каждой характерной зоне по условиям работы — передача нагрузки от колеса через рамный рельс, — передача нагрузки от колеса частично через рамный рельс и частично через остряк, — передача нагрузки от колеса через остряк.
На втором этапе в места, определенные по результатам выполнения первого этапа, устанавливались испытываемые подкладки с подушкой, и проводились измерения напряжений в наиболее нагруженных сечениях этих подкладок.
В испытаниях фиксировались напряжения в наиболее нагруженных сечениях подкладок с подушками.
Для проведения измерений использовалось тензометрическое оборудование. Запись производилась на цифровые носители информации. Объем фиксируемой информации соответствовал получению значений с вероятностью непревышения, соответствующей правилам расчета пути на прочность.
Каналы измерения формировались на базе вторичного измерительного преобразователя (усилителя) Spider 8 производства фирмы HBM совместно с модулями SR-55, включенных на пределе « +3В» и линией связи длиной 50 м кабелем СЭК. Класс точности 6, при доверительной вероятности — 0,997. Универсальный измерительный усилитель Quantum (MX 840 A).
Измерения напряжений производились с помощью тензорезисторов, располагаемых в наиболее нагруженных точках сечений подкладок. Использовались тензорезисторы типа 1-LY41-10|120, база 0,01 м, К=2,08+1%, R-120 Ом + 0,3%. Тензометрическая установка, с помощью которой проводились измерения на подкладках с подушкой, трех типов и расположение тензорезисторов показано на рисунках 3.1-3.2.
Обработка результатов испытаний производилась с получением наибольших наблюдавшихся значений напряжений от воздействия локомотивов и вагонов по каждому измерительному каналу. Объем анализируемой информации не менее 100 циклов нагружения.
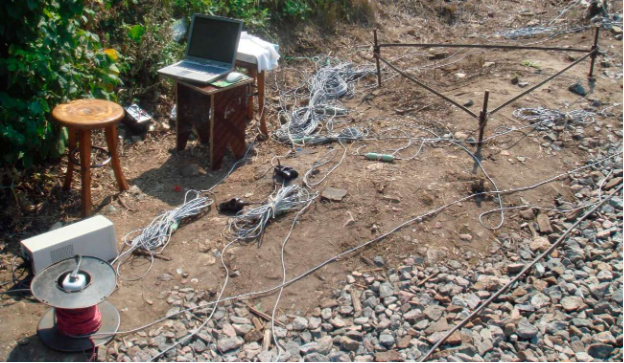
Рисунок 3.1 — Тензометрическая установка во время проведения динамико- прочностных испытаний подкладок с подушкой трех различных конструкций
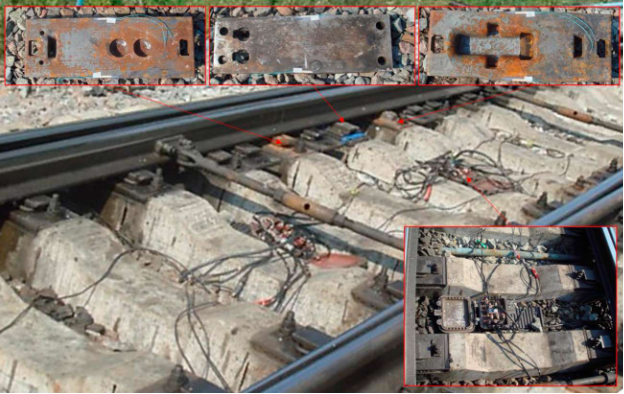
Рисунок 3.2 — Расположение тензорезисторов на подкладках с подушкой во время динамико-прочностных испытаний
Характеристика условий испытаний подкладок с подушкой
Объектами испытаний являлись подкладки с подушкой для стрелок стрелочных переводов типа Р65. Цель испытаний — оценка напряжённого состояния подкладок с подушкой от воздействия подвижного состава.
Испытаны подкладки с подушками (для стрелок) следующих видов:
- Подкладка с подушкой, изготовленная с использованием технологии горячей штамповки (рисунок 3.3)
- Подкладка с подушкой, изготовленная с использованием технологии на заклепках (рисунок 3.4)
- Подкладка с подушкой, изготовленная с использованием технологии сварки
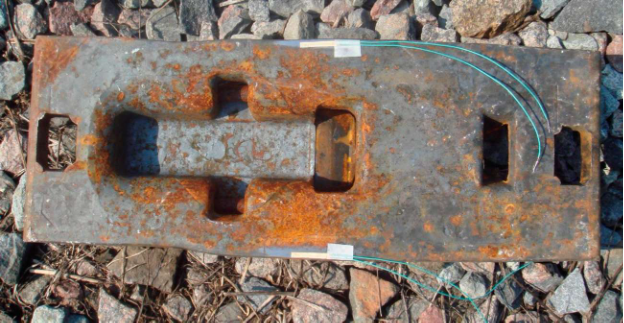
Рисунок 3.3 — Конструкция подкладки с подушкой, изготовленной с использованием технологии горячей штамповки, подготовленная к динамико-прочностным испытаниям
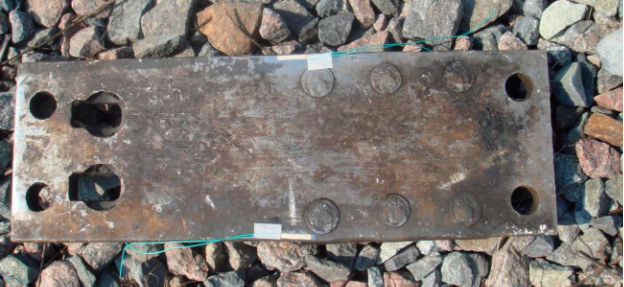
Рисунок 3.4 — Конструкция подкладки с подушкой, изготовленной с использованием технологии на заклепках, подготовленная к динамико-прочностным испытаниям
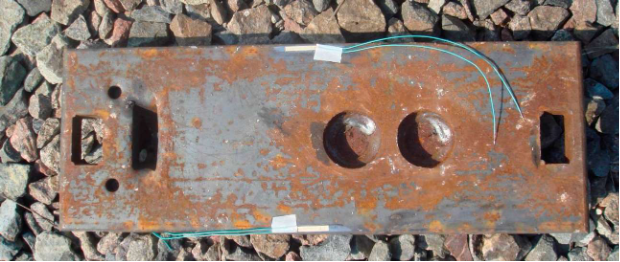
Рисунок 3.5 — Конструкция подкладки с подушкой, изготовленной с использованием технологии сварки, подготовленная к динамико-прочностным испытаниям
Результаты испытаний подкладок с подушкой для стрелок
При установке подкладок с приварной и штампованной подушкой на стрелочном переводе они прикрепляются к брусьям с помощью закладных болтов, а подкладка с подушкой на заклепках с помощью приспособлений, имитирующих закрепление закладными болтами.
Затяжка закладных болтов вызывает упругий выгиб подкладки вверх, при этом в наиболее нагруженном сечении подкладки с подушкой возникают напряжения, по знаку противоположные напряжениям, возникающим от воздействия подвижного состава, проходящего по стрелочному переводу. В результате этого циклы напряжений в наиболее нагруженных сечениях подкладок с подушкой имеют знакопеременный характер, что отрицательно сказывается на их эксплуатационной стойкости.
Для определения величин напряжений, возникающих от затяжки закладных болтов, производились записи напряжений в подкладке в процессе затяжки. Образец осциллограммы напряжений в наиболее нагруженном сечении подкладки с подушкой приведен на рисунке 3.6.
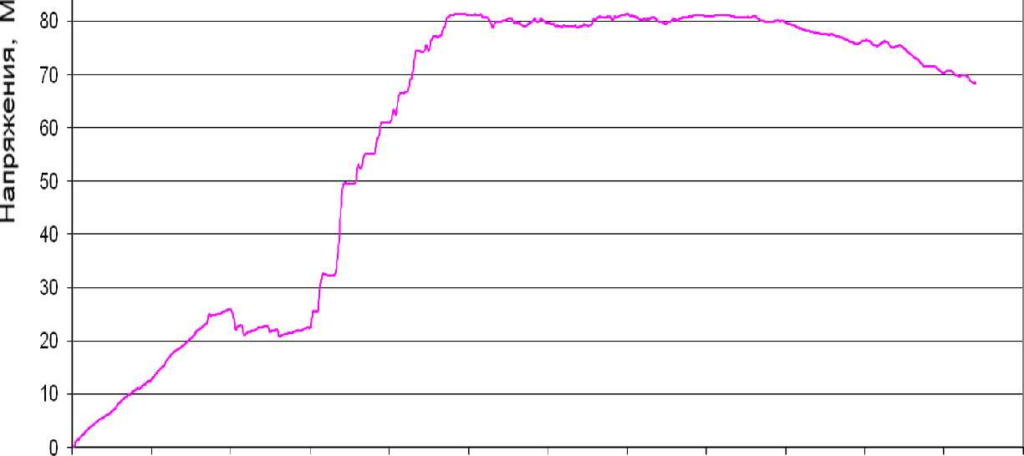
0 5 10 15 20 25 30 35 40 45 50 55 60 Время, с
Рисунок 3.6 — Осциллограмма напряжений при затяжке в подкладке с подушкой, приваренной к подкладке через 2 отверстия на брусе № 9
Измерения проводились на каждой подкладке с подушкой. Затяжка и разгрузка болтов выполнялась при установке каждой из подкладок с подушкой троекратно. Максимальные напряжения в подкладках с подушкой от затяжки закладных болтов различаются для подкладок с подушкой различной конструкции и составляют от 32 МПа до 80 МПа.
В соответствии с методикой на первом этапе испытаний подкладок с подушкой в зоне стрелки было установлено место наиболее нагруженных подкладок с подушкой. Эпюра стрелки стрелочного перевода с обозначениями нумерации брусьев представлена на рисунке 3.7.
Как видно из осциллограмм напряжённого состояния подкладок с подушкой (рисунки 3.8 — 3.10), наиболее нагруженными оказались подкладки с подушкой, изготовленные с использованием технологии сварки, от острия остряка брусе №9. Если на брусьях №4 и №14 максимальные значения напряжений в подкладках с подушкой, изготовленных с использованием технологии сварки, от воздействия проходящих поездов не превышали соответственно 140 и 160 МПа, то на брусе №9 они достигали уровня 200 МПа.
После определения на стрелке места наибольшей нагрузки, приходящейся на подкладку с подушкой (брус №9 от острия остряка), вместо подкладки с подушкой, изготовленной с использованием технологии сварки, на то же место, для оценки напряжённого состояния, была уложена подкладка с подушкой, изготовленная с использованием технологии горячей штамповки, затем подкладка с подушкой, изготовленная с использованием технологии на заклепках.
Общие результаты измерений напряжений в подкладках с подушкой сведены в таблицу 3.1.
Как видно из осциллограмм, наибольшие величины напряжений в пластинах, указанных подкладок с подушками, возникающих от локомотивных и вагонных нагрузок, достигают соответственно 240 и 250 МПа (рисунки 3.11 и 3.12).
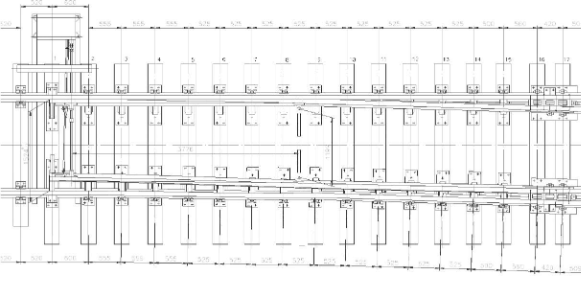
Рисунок 3.7 — Эпюра стрелки стрелочного перевода
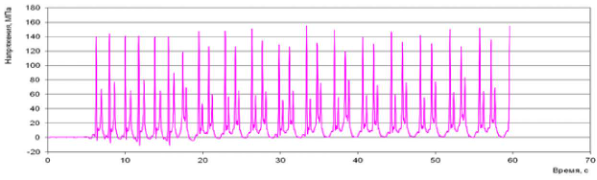
Рисунок 3.8 — Осциллограмма напряжений в подкладке с подушкой, изготовленной с использованием технологии сварки, на брусе № 4
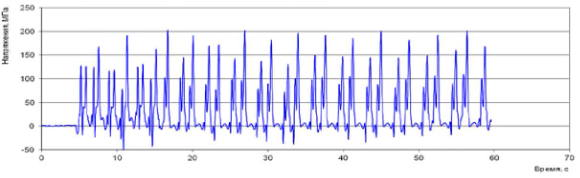
Рисунок 3.9 — Осциллограмма напряжений в подкладке с подушкой, изготовленной с использованием технологии сварки, на брусе № 9
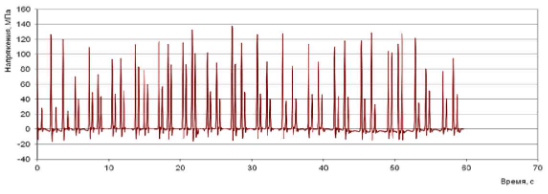
Рисунок 3.10 — Осциллограмма напряжений в подкладке с подушкой, изготовленной с использованием технологии сварки, на брусе № 14
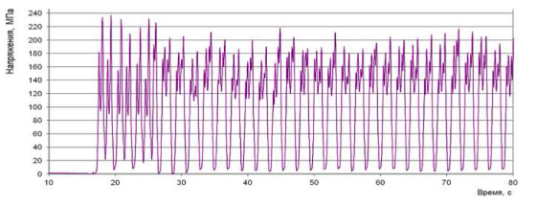
Рисунок 3.11 — Осциллограмма напряжений в подкладке с подушкой, цельной конструкции, изготовленной по технологии горячей штамповки, на брусе № 9
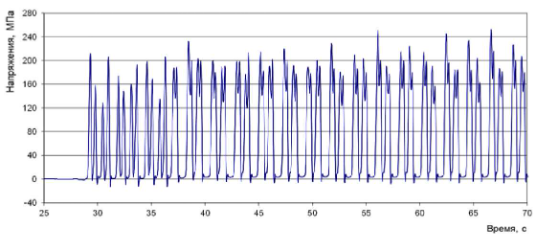
Рисунок 3.12 — Осциллограмма напряжений в подкладке с подушкой, изготовленной с использованием технологии на заклепках, на брусе № 9
Вид подкладки с подушкой | Наибольшее напряжение, МПа | Напряжение от затяжки прикрепителей, МПа |
---|---|---|
Подкладка с подушкой, изготовленная с | ||
использованием технологии на заклепках | 250,0 | -50,0 |
Подкладка с подушкой цельной | ||
конструкции, изготовленная по | ||
технологии горячей штамповки | 240,0 | -80,0 |
Подкладка с подушкой, изготовленная с | ||
использованием технологии сварки | 200,0 | -32,0 |
Из данных таблицы 3.1 видно, что из трех видов испытанных подкладок с подушкой наиболее предпочтительными являются подкладки с подушкой, изготовленные с использованием технологии сварки. Наибольшие напряжения в них составляют 200 МПа, напряжения от затяжки — 32 МПа, средний коэффициент асимметрии циклов нагружения с учетом напряжений от затяжки минус 0,20.
Наихудшие результаты получены для подкладок с подушкой, изготовленных с использованием технологии на заклепках. Наибольшие напряжения составляют 250 МПа, напряжения от затяжки — 50 МПа, средний коэффициент асимметрии циклов нагружения с учетом напряжений от затяжки минус 0,20.
Неблагоприятными являются и условия работы подкладок с подушкой, изготовленные по технологии горячей штамповки. Наибольшие напряжения составляют для этих подкладок 240 МПа, напряжения от затяжки достигают — 80 МПа, средний коэффициент асимметрии циклов нагружения достигает с учетом напряжений от затяжки минус 0,36.
Выводы
В результате выполненных динамико-прочностных испытаний можно сделать следующие основные выводы.
- Серийно выпускаемые подкладки с подушкой всех видов для стрелок имеют неудовлетворительную эксплуатационную стойкость и нуждаются в доработке.
- Отказы подкладок с подушкой возникают в эксплуатации из-за трещин и изломов пластины подкладки в местах расположения кромки подошвы рамного рельса со стороны остряка или близких к этому месту сечениях, возникают также отказы в виде отрыва подушки из-за нарушения технологии ее приварки кольцевыми швами.
- Причины отказов — недостатки конструкции (совпадение мест концентрации напряжений из-за резкого изменения геометрических характеристик сечения, расположения отверстий в наиболее нагруженной зоне) и технологии изготовления (расположение термических узлов в местах концентраторов напряжений, некачественная сварка, некачественная штамповка).
- Из трех видов испытанных подкладок с подушкой (стрелочных башмаков) наиболее предпочтительными являются подкладки с подушкой с использованием технологии сварки. Наибольшие напряжения составляют 200 МПа, напряжения от затяжки — 32 МПа, средний коэффициент асимметрии циклов нагружения — минус 0,20.
- Наихудшие результаты получены для подкладок с подушкой, изготовленных с использованием технологии на заклепках. Наибольшие напряжения составляют 250 МПа, напряжения от затяжки — 50 МПа, средний коэффициент асимметрии циклов нагружения — минус 0,20.
- Неблагоприятными являются и условия работы подкладок с подушкой, изготовленные по технологии горячей штамповки. Наибольшие напряжения составляют 240 МПа, напряжения от затяжки достигают — 80 МПа, средний коэффициент асимметрии циклов нагружения достигает — минус 0,36.
Из испытанных вариантов подкладок с подушкой к внедрению рекомендуются подкладки с подушкой, изготовленные с использованием технологии сварки.
Для выявления причин зарождения и развития трещин, приводящих к излому всех трех ранее рассмотренных конструкций подкладок с подушкой, целесообразно провести металлографические исследования подкладок с подушкой в сечениях изломов.
Металлографические исследования подкладки с подушкой в сечениях изломов
Для выявления причин зарождения и развития трещин, приводящих к излому подкладок, были проведены металлографические исследования излома подкладки с подушкой [54]. Исследование проводилось подкладки с подушкой, изъятой из пути с наиболее распространённой конструкцией стрелочного перевода типа Р65 марки 1/11 проекта 2750.
Характеристика объекта исследования
Объект исследования: подкладка с подушкой 2768.01.010
Забоин, трещин, а также волосовин, раскатанных пузырей, загрязнений и прочих дефектов проката на поверхности подкладки не обнаружено.
В месте контакта подушки с подкладкой, на подушке и на подкладке обнаружены потёртости (рисунок 4.1). Потёртости возникли в результате излома сварного шва, соединяющего подкладку с подушкой, вследствие чего жесткость соединения снизилась и увеличилась степень подвижности подушки относительно подкладки под воздействием циклических нагрузок.
Излом имеет усталостный характер с фокусом трещины в зоне кольцевого сварного шва и зоной долома поперек подкладки (рисунки 4.2, 4.3).
По ручьям излома можно предположить, что трещина зародилась под действием циклических изгибающих нагрузок от кольцевого сварного шва в месте, где сварной шов испытывает наибольшие растягивающие напряжения. Далее трещина распространялась по зоне термического влияния (ЗТВ) сварного шва по металлу подкладки. После распространения трещины на 2/3 кольцевого сварного шва, произошло максимальное ослабление рабочего сечения конструкции, и трещина стала развиваться поперек подкладки.
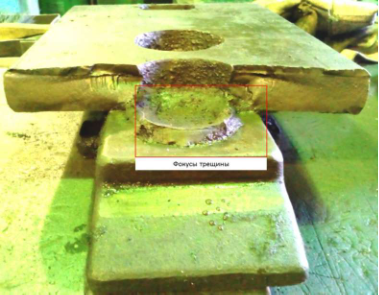
Рисунок 4.1 — Следы потертости в месте прилегания подушки к подкладке
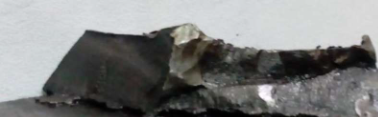
Рисунок 4.2 — Подкладка с подушкой с изломом подкладки
Методика металлографического исследования подкладки с подушкой
Исследования зоны сварного соединения проводились с использованием следующего оборудования: сканирующего автоэмиссионного электронного микроскопа; сканирующего зондового микроскопа; оптического металлографического микроскопа; энергодисперсионного детектора.
В процессе наблюдений был выбран режим съемки с ускоряющим напряжением 12-15 кВ и током пучка 10 мкА, что позволяло добиться убедительного контраста при достаточном разрешении.
Для исследований были подготовлены образцы — рисунок 4.5, которые вырезались алмазным кругом из композитного стержня.
После получения приблизительно плоской поверхности, образцы шлифовались наждачной бумагой разной дисперсности, помещенной для этого на плоском основании вращающегося круга полировочного станка. После шлифования образцы полировали на вращающемся тканевом круге с алмазной суспензией до получения зеркальной поверхности. После полирования, микрошлиф промывался водой, затем спиртом и просушивался фильтровальной бумагой.
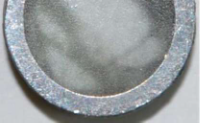
Рисунок 4.5 — Образец для микроскопических исследований
Химический состав
Определение химического состава проведено по ГОСТ Р 54153-2010 и представлено в таблице 4.1.
Маркировка | Массовая доля элементов, в процентах | |||||||
C | Mn | Si | P | S | & | м | ||
1 | 0,16 | 0,55 | 0,23 | 0,018 | 0,023 | 0,06 | — | 0,02 |
2 | 0,19 | 0,48 | 0,22 | 0,024 | 0,024 | 0,12 | 0,08 | 0,22 |
Результаты исследований химического состава металла, из которого изготовлена подкладка с подушкой свидетельствуют о том, что химический состав исследованных образцов подушки и подкладки соответствует требованиям ГОСТ 380-2005 для Ст3сп.
Результаты микроструктурных исследований
В микроструктуре сварного шва в исследованных сечениях вне зоны фокуса трещины наблюдаются дефекты в виде пор (рисунок 4.7). В микроструктуре сварного шва в зоне фокуса трещины наблюдается расслоение сварного шва (рисунок 4.8).
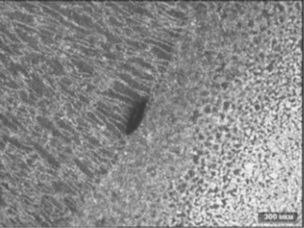
Рисунок 4.7 — Дефект сварки в виде поры в кольцевом сварном шве со стороны подушки
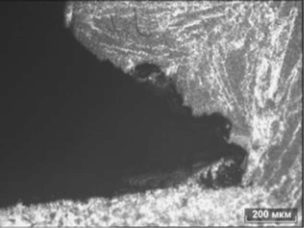
Рисунок 4.8 — Структура в зоне фокуса трещины
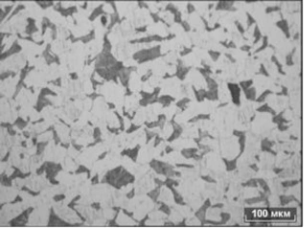
Рисунок 4.9 — Микроструктура основного металла подушки
В месте контакта подкладки с подушкой у поверхности металла наблюдается деформация зеренной структуры, возникшая в результате высокой степени подвижности подушки относительно подкладки под действием циклических нагрузок.
Микроструктура основного металла подкладки и подушки — феррито-перлит (рисунки 4.9-4.10). Наблюдается зона термического влияния сварки с характерной для нее структурой — мелкодисперсный феррит игольчатой формы (рисунок 4.11).
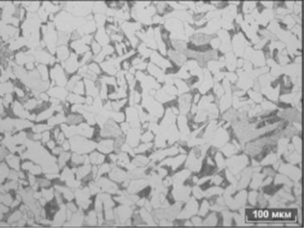
Рисунок 4.10 — Микроструктура основного металла подкладки
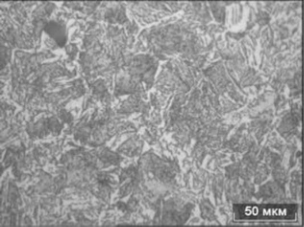
Рисунок 4.11 — Микроструктура металла подкладки в зоне термического влияния сварного шва
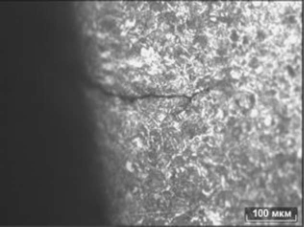
Рисунок 4.12 — Микротрещины, распространяющиеся от излома сварного шва по металлу подкладки
В микроструктуре подкладки в зоне термического влияния сварки наблюдается распространение микротрещин, возникших в процессе распространения магистральной трещины по сварному шву (рисунок 4.12).
Предположительно, под действием циклических изгибающих нагрузок одна из микротрещин образовала магистральную трещину, распространяющуюся по металлу подкладки.
Выводы
- Химический состав исследованных образцов подушки и подкладки соответствует требованиям ГОСТ 380-2005 для Ст3сп.
- Причиной излома является недостаточная циклическая прочность сварного шва.
- В микроструктуре подкладки в зоне термического влияния сварки наблюдается распространение микротрещин.
- Улучшение прочностных и эксплуатационных характеристик подкладок с подушкой может быть достигнуто за счет:
- применения металла с более высокими прочностными характеристиками;
- изменения конструкции подкладок за счет увеличения толщины пластины подкладки и (или) введения специальных конструктивных решений (например, разгружающих выкружек), уменьшающих концентрацию напряжений;
- изменения технологии изготовления подкладок путем ликвидации технологических отверстий и удаления термических узлов от мест расположения концентраторов напряжений;
- применения принципиально новых подкладок за счет технических решений. Для улучшения конструкции подкладок с подушкой целесообразно провести расчет подкладки с подушкой с помощью математического моделирования.
Разработка методов расчета подкладки с подушкой, улучшение конструкции подкладки с подушкой
Изломы подкладок с подушкой имеют общие характерные особенности. Линия излома во всех случаях пересекает неоднородность формы подкладки с подушкой, которая представляет собой концентратор механических напряжений и располагается вдоль внутренней кромки рамного рельса. Для подкладки с подушкой с заклёпочным соединением концентраторами являются отверстия под заклёпки. В подкладке с подушкой, изготовленной методом горячей штамповки, в качестве концентратора выступает острый угол отверстия, оставшегося после штамповки. Для сварной подкладки с подушкой концентратором является отверстие для сварки.
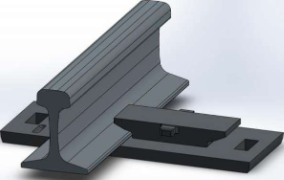
Рисунок 5.1 — Узел стрелочной подкладки с подушкой
Изломы характерны для усталостного разрушения, т.е. разрушения, вызванного постепенным накоплением повреждённости в материале. Такой вид разрушения весьма чувствителен к эффекту концентрации напряжений. Типичным сценарием усталостного разрушения является накопление повреждённости на концентраторе напряжений, последующее зарождение усталостной трещины на этом концентраторе и распространение трещины по основному сечению элемента до полного его разрушения.
Дальнейший анализ напряжённого состояния и оценка прочности подкладки с подушкой выполнены на примере сварной подкладки с подушкой.
Анализ напряжённого состояния и оценка прочности подкладки с подушкой
Узел, в составе которого работает подкладка с подушкой, состоит из бруса, резиновой прокладки, подкладки, подушки и опирающихся на них рамного рельса и остряка.
С точки зрения механики подкладка представляет собой пластину на упругом основании [78]. Аналитический расчёт таких деталей затруднён, поскольку требует в общем случае решения системы из 10 дифференциальных уравнений с 10 неизвестными, основным из которых является уравнение прогибов тонкой плиты вида, где а и Ь — размеры плиты в плане, О — жёсткость плиты, У(х,у) — функция прогибов плиты, д(х,у) — функция внешних нагрузок, р(х,у) — функция реактивного отпора основания, зависящая от функции прогибов [55, 79].
Для расчёта подобных элементов применяются упрощенные расчётные схемы. Учитывая сложную геометрию подкладок, можно считать, что приближённый аналитический расчёт подкладок нецелесообразен, так как эффект упрощений не позволит с достаточной точностью описать поведение подкладки. Более перспективным выглядит применение современных численных методов анализа. Для решения задачи был выбран алгоритм, который позволяет получить решение, удовлетворяющее уравнениям механики деформируемого твёрдого тела с любой заранее заданной точностью, не прибегая к упрощениям геометрии и применяя малое число иных упрощений.
Анализируя условия работы подкладки, можно выделить следующие существенные особенности:
- наличие упругого основания, существенно влияющего на напряжённо- деформированное состояние (НДС) подкладки;
- наличие предварительной затяжки крепёжных элементов, в результате чего в подкладке имеется НДС в отсутствии внешней нагрузки;
- циклическое нагружение подкладки при прохождении подвижного состава.
Упругое основание подкладки обусловлено наличием резиновой прокладки между подкладкой и брусом. Требования к жёсткости этой прокладки устанавливаются ГОСТ Р 56291-2014 и составляют 50-150 МН/м [56, 68, 69, 70]. Более точно поведение упругой прокладки можно описать, учитывая нелинейную жёсткость прокладки, которая возрастает с ростом нагрузки. В [57, 77], в частности, приводятся результаты испытаний прокладок рельсовых скреплений на сжатие.
Зависимость «нагрузка-перемещение» носит существенно нелинейный характер и с достаточной точностью описывается зависимостью вида:
Р = к • ш3,
где Р — нагрузка на прокладке (комплекте прокладок), к — коэффициент жёсткости, w — осадка (вертикальное перемещение) прокладки. Более точно жёсткость может быть описана в терминах удельного давления р:
р=р•к•ж
Дальнейший анализ напряжённого состояния и оценка прочности подкладки с подушкой выполнены на примере сварной подкладки с подушкой.
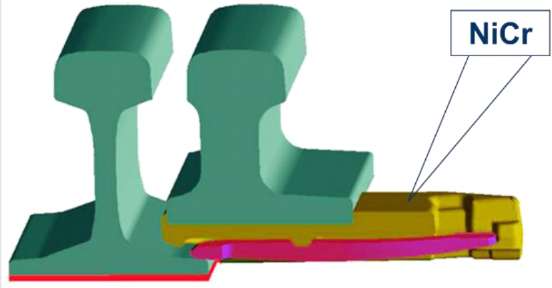
где F — площадь контактной поверхности прокладки. Нелинейная жёсткость прокладки может быть определена как:
Выражение может использоваться при моделировании для определения величины локальной жёсткости упругого основания. Коэффициент к’ при этом может быть определён из эксперимента.
Предварительная затяжка крепёжных болтов осуществляется при установке подкладки в рабочее положение. Для этого гайки на двух закладных болтах М22 затягиваются моментом 300 Нм. Создаваемое затягом осевое усилие в каждом из болтов может быть оценено по приближённой формуле [58], где М — момент затяжки,й — номинальный диаметр болта, Р — осевое усилие. Подсчитанное по формуле (5.4) для указанных выше параметров значение осевого усилия составляет 68,2 кН.
В соответствии с ГОСТ 16277-93 [59] подкладки раздельного скрепления изготавливаются из полос, прокатанных из стали Ст4 различных степеней раскисления по ГОСТ 380 [60]. Допускается изготовлять подкладки из полос, прокатанных из стали Ст3 различных степеней раскисления с массовой долей углерода не менее 0,16 % (при этом нормируется, что суммарное количество углерода и 1/4 марганца должны составлять не менее 0,28 %).
Механические характеристики сталей Ст3 и Ст4 приведены в таблице 5.1 [6163].
Сталь | оод, МПа | об, МПа | 5, % | 0-1, МПа |
---|---|---|---|---|
Ст3сп | 195-255 | 370-530 | 22-27 | 195 |
Ст3пс | 195-245 | 370-480 | 23-26 | 191-213 |
Ст3кп | 185-235 | 360-460 | 24-27 | 175 |
Ст4пс | 235-265 | 410-530 | 19-24 | 196-235 |
Ст4кп | 225-255 | 400-510 | 19-25 | 196-225 |
Учитывая условия работы подкладки, её прочность должна оцениваться сразу по двум критериям: по критерию прочности при статическом нагружении и по критерию циклической прочности. [80, 81] При этом прочность необходимо обосновывать в предположении действия наиболее неблагоприятного сочетания усилий на конструкцию на каждом цикле.
Для оценки усталостной долговечности необходима кривая усталости, задающая соотношение между количеством циклов до разрушения и амплитудой напряжений симметричного цикла. Кривая может быть восстановлена по имеющимся данным с использованием уравнения Веллера [64], постулирующего линейное соотношение в полулогарифмических координатах, где оа — амплитуда напряжений симметричного цикла, N — число циклов для разрушения, а и Ь — подбираемые параметры уравнения. Для подбора двух параметров уравнения Веллера необходимо иметь две точки с известными соотношениями между напряжениями и числом циклов.
В качестве первой такой точки принимается временное сопротивление аВ, которое, очевидно, вызывает разрушение за один цикл.
В качестве второй точки принимается предел выносливости, не вызывающий разрушение на полной базе циклов. В качестве полной базы циклов при испытании на усталость принимаются 107 циклов [65], однако перелом на кривой усталости происходит уже на базе (1 ^ 3)-106 циклов и рекомендуется принимать в качестве базы циклов, соответствующей пределу выносливости величину 2-106 циклов [66]. Таким образом, вторая точка определяется соотношением.
оа, МПа 400

500000 1000000 1500000 2000000 2500000 3000000
Рисунок 5.2 — Кривая усталости стали Ст3кп.
Для моделирования поведения подкладки с подушкой под нагрузкой разработана математическая модель, включающая в себя подкладку, приварную подушку и элемент рельса. Моделирование произведено алгоритмом линейного программирования методом подбора в программном комплексе АКБУБ версии 19.0 (рисунок 5.3) [71, 72].
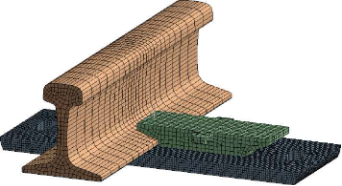
Рисунок 5.3 — Общий вид конечноэлементной математической модели в препроцессоре ПК АШУБ
Принимая из таблицы 5.1 наиболее консервативные значения характеристик аВ = 360 МПа ио.1 = 175 МПа, которые соответствуют стали Ст3кп, получаем для параметров уравнения Веллера значения а = 360 МПа и Ь = 29,4 МПа. На рисунке 5.2 показана восстановленная по этим параметрам кривая усталости в прямых координатах.
Для учёта неравномерности упругого основания под подкладкой, основание подкладки разделено на несколько отдельных поверхностей, на которые независимо назначаются граничные условия: усилия прикладываются не по всей поверхности, а только в тех местах, которые контактируют с ребристой резиновой прокладкой, для чего разделение поверхностей выполнено совпадающим с расположением рёбер прокладки [73].
Моделирование поведения подкладки с подушкой под нагрузкой, изготовленной с применением сварки
Моделирование производится для двух постановок:
- Задача №1. Предварительная затяжка крепёжных элементов. В рамках постановки определяется НДС подкладки при затяжке крепёжных элементов — двух болтов М14, крепящих подкладку к брусу. Нагрузки на рельс и остряк отсутствуют.
- Задача №2. Максимальная нагрузка на подкладку. В рамках этой постановки затянутые болты фиксируются в тех положениях, в которых они оказались при затяжке, а на систему прикладывается максимальная нагрузка, которая соответствует переходу колеса с рельса на остряк.
Для корректного учёта работы упругого основания в первой задаче итерационно определяется распределение его жёсткости. Методика подбора заключается в следующем: на первой итерации на все поверхности, имеющие свойства упругого основания, прикладывается одинаковая жёсткость основания 5 Н/мм3. Далее производится расчёт и определяется суммарное реактивное усилие, действующее на каждую поверхность. Жёсткость каждой поверхности корректируется в соответствии с формулой (5.4) и производится следующая итерация расчёта. Итерации повторяются до тех пор, пока все жёсткости основания в модели не перестают изменяться более чем на 1 %. После того как достигнута сходимость решения по распределению жёсткостей, определяется напряжение в местах, где производился экспериментальный замер, и сравнивается с результатами эксперимента. В случае, если значения не совпадают, производится корректировка константы в выражении (5.4) и итерационный процесс повторяется.
На рисунке 5.4 приведена иллюстрация процесса сходимости жёсткости оснований [74, 75].
Н/мм3 б
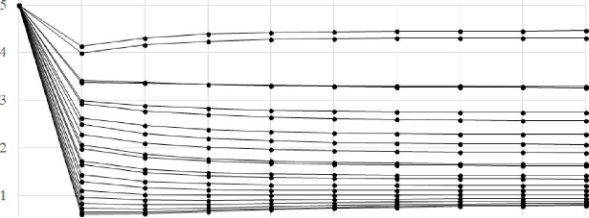
0 1 2 3 4 5 6 7 8 9 № итерации
Рисунок 5.4 — Итеративный процесс сходимости жёсткостей основания
После достижения сходимости по распределению жёсткостей и совпадению с результатами экспериментальных замеров, производится расчёт второй задачи. При этом используется значение константы в выражении (5.4), которое было определено в ходе калибровки первой задачи, а итерации, необходимые для достижения сходимости по распределению жёсткостей, повторяются. После этого значения напряжений также сравниваются с результатами экспериментальных измерений.
В результате проведённой калибровки на эксперимент значение константы к’ составило 1,50 Н1/3/мм5/3.
На рисунках 5.5, 5.6 показаны итоговые распределения жёсткостей упругого основания для случаев затяжки креплений и прохождения состава.
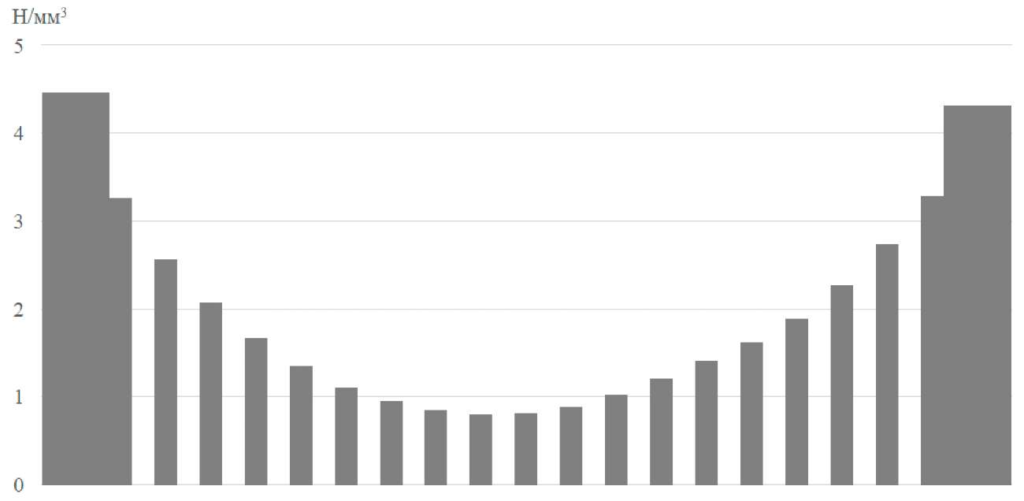
Рисунок 5.5 — Распределение жёсткостей основания для случая затяжки креплений
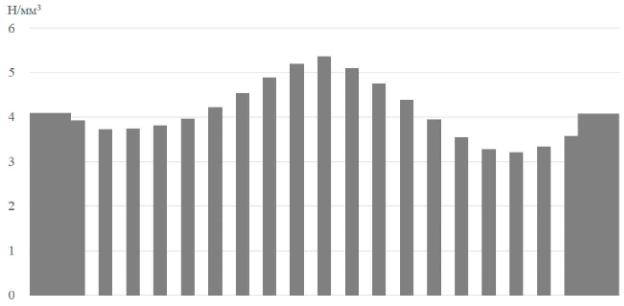
Рисунок 5.6 — Распределение жёсткостей основания для случая прохождения состава
На рисунке 5.7 приведены расчётные распределения ориентированных по направлению замера напряжений, вдоль ребра, на котором проводился замер в эксперименте. Зона расположения тензометров отмечена вертикальными точечными линиями.
Рисунок 5.7 — Распределение напряжений по нижнему внешнему ребру подкладки: пунктир — затяжка креплений, сплошная линия — прохождение состава; вертикальными линиями обозначена зона наклейки тензометров
В таблице 5.2 приведены результаты проведённой калибровки и верификации модели подкладки.
Расчётный случай | Затяжка болтов скреплений | Прохождение состава |
---|---|---|
Модель | 76 МПа | 239 МПа |
Эксперимент | 80 МПа | 200 МПа |
Расчет напряжений подкладок с подушкой, показал, что наибольшие напряжения для подкладок с подушкой сварной конструкции достигают максимальной величины в 239 МПа, что отличается от полученных в прямых испытаниях напряжений менее, чем на 6,3 % (полученные в испытаниях, напряжения для подкладок той же конструкции составили 200 МПа).
Таким образом можно сделать вывод: полученные из расчета и прямых испытаний величины напряжений близки по значениям, следовательно,
разработанная математическая модель адекватно отражает напряженное состояние подкладок с подушкой в зонах их наибольшей нагруженности.
На основании приведённых в таблице 5.2 значений, модель подкладки на упругом основании может считаться адекватной действительности. Значения напряжений в области замера выше полученных в эксперименте, что может быть с тем, что в расчёте учитывается максимальная расчётная нагрузка на подкладку.
На рисунке 5.7 приведены распределения эквивалентных по Мизесу напряжений в подкладке при затяжке соединений. Эквивалентные по Мизесу напряжения определяются соотношением.
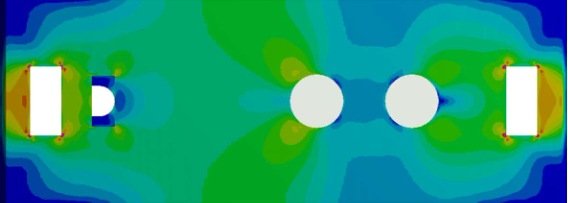
Рисунок 5.7 — Распределение эквивалентных напряжений по подкладке при затяжке соединений
В качестве основного цикла нагружения рассматривается непропорциональный цикл, в котором одно состояние соответствует подкладке, нагруженной только затяжкой крепежа, а другое — подкладке, нагруженной проходящим составом. То есть, один цикл нагружения соответствует переходу от НДС задачи №1 к НДС задачи №2.
Оценка предельных амплитуд цикла выполняется на основании условия Гудмана, которое для углеродистых сталей даёт оценку [67].
На рисунке 5.9 показано распределение эквивалентных (приведённых к симметричному циклу) амплитуд напряжений.
Рисунок 5.9 — Распределение амплитуд напряжений эквивалентного симметричного цикла в подкладке базовой конструкции На рисунках 5.10, 5.11 показано распределение обобщённых (по условию статической и циклической прочности) коэффициентов запаса.
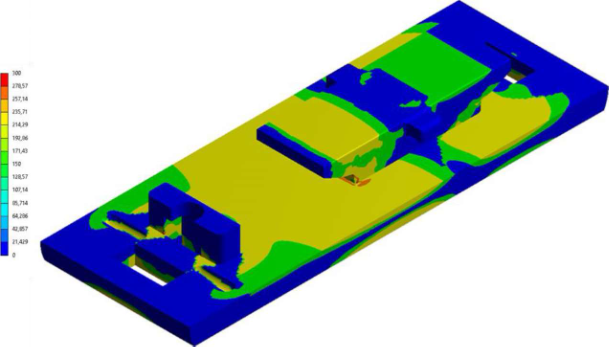
Рисунок 5.10 — Распределение обобщённых коэффициентов запаса в подкладке базовой конструкции (изометрия)
Коэффициент запаса меньше единицы соответствует невыполнению одного из условий прочности — статической или циклической. В первом случае он представляет собой отношение действующих эквивалентных напряжений к допускаемым, а во втором — отношение эквивалентной амплитуды к пределу выносливости. Из рисунка 5.11 видно, что коэффициент запаса со значением менее единицы локализован вблизи центрального отверстия для сварки.
Как видно из рисунка 5.11 опасные зоны подкладки, полученные в результате моделирования, полностью совпадают с картиной разрушения на рисунке 2.2. Таким образом подтверждается основной вывод анализа характера разрушения — разрушение происходит в результате накопления усталостных повреждений материала на концентраторах напряжений. Минимальное значение числа циклов до разрушения составляет величину 1,5 -106 циклов.
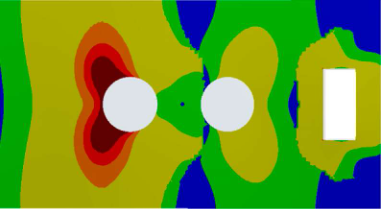
Рисунок 5.11 — Распределение обобщённых коэффициентов запаса в подкладке базовой конструкции (подошва подкладки)
Зоны с наименьшим числом циклов до разрушения расположены на нижней поверхности подкладки на контуре центрального отверстия. В этом месте происходит зарождение усталостной трещины, которая распространяется по всему сечению подкладки с дальнейшим ростом числа циклов до полного её разделения на части.
Оптимизация конструкции подкладки с подушкой должна быть направлена на обеспечение долговечности конструкции подкладок при действующим в эксплуатации нагружении. Однако, при этом требуется соблюдение ряда условий:
- неизменность положения крепёжных элементов;
- неизменность положения высоты подошвы рельса;
- неизменность положения высоты подошвы остряка;
- неизменность габаритов в плане.
При этом должны удовлетворяться условия прочности и надёжности:
- обеспечение статической прочности;
- обеспечение циклической прочности;
- обобщённый коэффициент запаса > 20 %.
Оптимизируемыми параметрами является набор геометрических размеров, не ограниченных вышеописанными условиями:
Целевая функция имеет вид: Х0= агдтах п(Х), где n -коэффициент запаса прочности.
В результате расчетов по разработанной методике был получен усовершенствованный вариант подкладки с подушкой.
Моделирование поведения подкладки с подушкой под нагрузкой с удалением из подкладки отверстий для приварки подушки
Наиболее простым вариантом модификации конструкции является удаление из подкладки отверстий для приварки подушки. Приварка подушки в таком исполнении осуществляется двумя продольными швами вдоль длинных сторон подушки (рисунок 5.13).
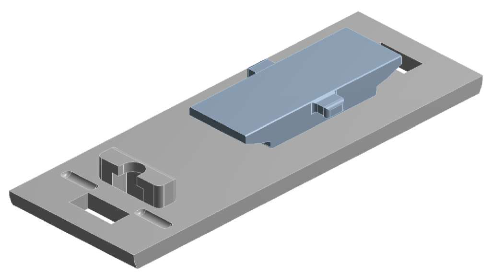
Рисунок 5.13 — Подкладка с приварной подушкой без отверстий в подкладке
Для подкладки такой конструкции были произведены расчёты аналогичные расчёту подкладки исходной конструкции. На рисунке 5.14 приведено распределение эквивалентных амплитуд напряжений. Максимальное значение эквивалентной амплитуды составляет 147 МПа (в подкладке базовой конструкции 277 МПа) и не превосходит предела выносливости материала.
Моделирование поведения подкладки с подушкой с разной шириной подушки под нагрузкой
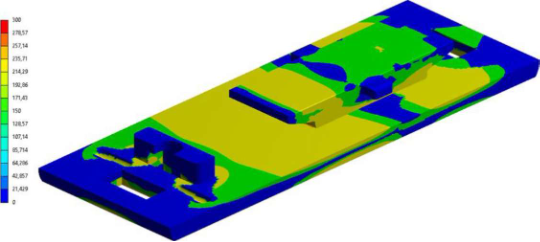
Рисунок 5.15 — Распределение обобщённых коэффициентов запаса для подкладки без отверстий (изометрия)ий
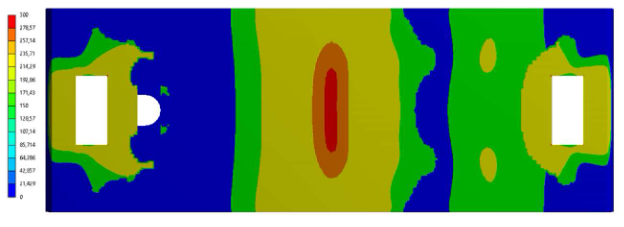
Рисунок 5.16 — Распределение обобщённых коэффициентов запаса для подкладки без отверстий (подошва подкладки)
Полученная конструкция удовлетворяет критериям прочности, однако коэффициент запаса в ней относительно мал. Анализируя картину напряжений на рисунке 5.14, можно установить, что основной причиной малого коэффициента запаса является малая площадь контакта подушки и подкладки. Подушка в такой конструкции действует на подкладку подобно штампу и для понижения уровня эквивалентных амплитуд, необходимо увеличить ширину контактной зоны между подушкой и подкладкой (рисунок 5.17).
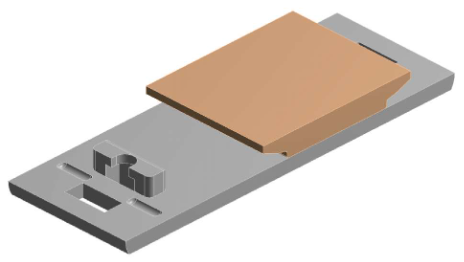
Рисунок 5.17 — Подкладка с приварной подушкой шириной во всю подкладку
На рисунках 5.19, 5.20 приведено распределение обобщённых коэффициентов запаса в подкладке с подушкой во всю ширину подкладки. Минимальное значение коэффициента запаса для такой конструкции составляет 1,05.
Значение коэффициента запаса превосходит единицу (условия прочности выполнены), однако минимальное его значение меньше, чем для подушки исходной конструкции без отверстий для сварки. Причиной этого является концентрация контактных напряжений под границей контактной зоны на краях подкладки.
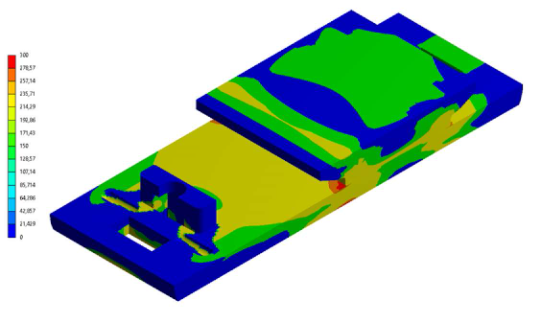
Рисунок 5.19 — Распределение обобщённых коэффициентов запаса для подкладки без отверстий с подушкой во всю ширину подкладки (изометрия)
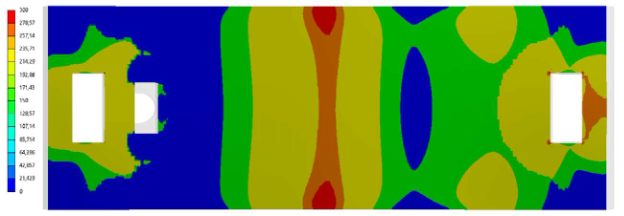
Рисунок 5.20 — Распределение обобщённых коэффициентов запаса для подкладки без отверстий с подушкой во всю ширину подкладки (подошва подкладки)
Для устранения этого недостатка ширина подушки должна быть уменьшена до той величины, когда зона концентрации напряжений под границей контактной зоны не окажется целиком в пределах ширины подкладки (рисунок 5.21).
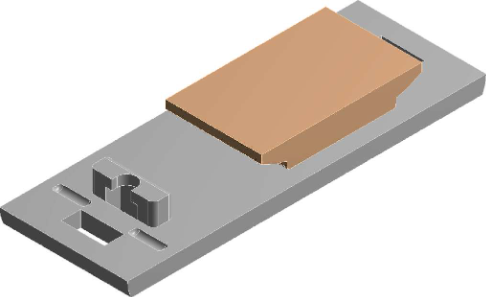
Рисунок 5.21 — Подкладка с приварной подушкой зауженной на 50 мм
Максимальное значение эквивалентной амплитуды составляет 123 МПа, что меньше, чем во всех других конструкциях подкладки с подушкой.
На рисунках 5.23, 5.24 приведено распределение обобщённых коэффициентов запаса в подкладке без отверстий с подушкой шириной на 50 мм уже ширины подкладки. Минимальное значение коэффициента запаса для такой конструкции составляет 1,27.
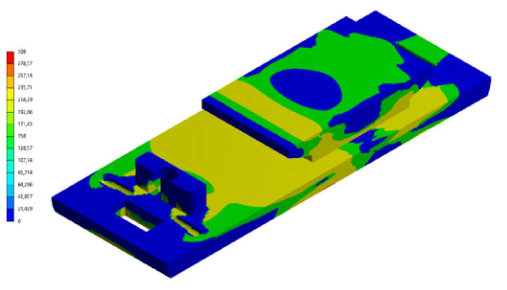
Рисунок 5.23 — Распределение амплитуд напряжений эквивалентного симметричного цикла для подкладки без отверстий с подушкой шириной на 50 мм меньше ширины подкладки (изометрия)
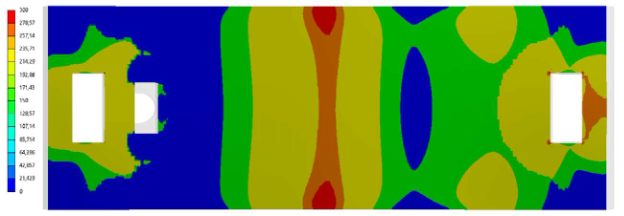
Рисунок 5.24 — Распределение обобщённых коэффициентов запаса для подкладки без отверстий с подушкой шириной на 50 мм меньше ширины подкладки (подошва подкладки)
Как видно из рисунка 5.24 значение коэффициента запаса не только превосходит единицу, но и минимальное его значение превосходит пороговую величину 1,25. Указанная конструкция подкладки является оптимальной среди рассмотренных, удовлетворяя всем требованиям оптимизированной конструкции.
Моделирование поведения подкладки с подушкой цельнолитой конструкции под нагрузкой
Другим перспективным способом модификации конструкции является переход на цельнолитую конструкцию, в которой подкладка и подушка являются одной деталью (рисунок 5.25).
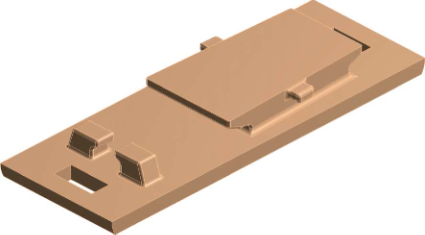
Рисунок 5.25 — Литая подкладка с зауженной подушкой
На рисунках 5.26, 5.27 приведено распределение эквивалентных амплитуд напряжений в цельнолитой подкладке с зауженной подушкой. Максимальное значение эквивалентной амплитуды составляет 148 МПа и не превосходит предела выносливости материала.
На рисунках 5.28, 5.29 представлены обобщённые коэффициенты запаса для цельнолитой подкладки с зауженной подушкой. Коэффициенты запаса в целом превосходят единицу, а минимальное значение составляет 1,15.
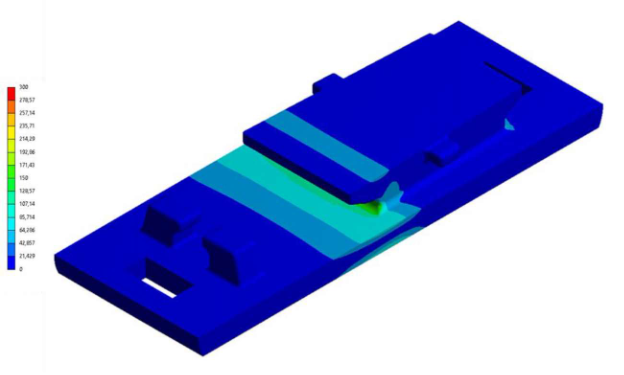
Рисунок 5.26 — Распределение амплитуд напряжений эквивалентного симметричного цикла для цельнолитой подкладки с зауженной подушкой(изометрия)
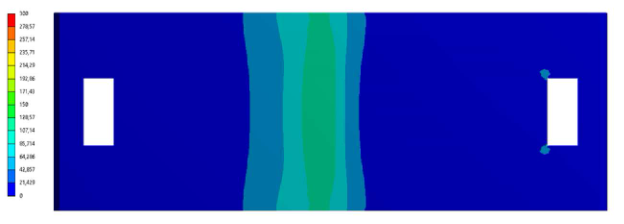
Рисунок 5.27 — Распределение амплитуд напряжений эквивалентного симметричного цикла для цельнолитой подкладки с зауженной подушкой(подошва подкладки)
Как видно из рисунков 5.27, 5.29 наиболее нагруженной зоной в цельнолитой конструкции является зона перехода подушки в подкладку. Минимальное значение коэффициента запаса находится именно в этой зоне. Минимальная величина коэффициента запаса относительно невелика, что свидетельствует о том, что подкладка с зауженной подушкой не является оптимальной конструкцией. С другой стороны, минимальная величина коэффициента запаса на подошве составляет 1,44, что открывает возможность повышения надёжности конструкции за счёт увеличения подушки (рисунок 5.30).
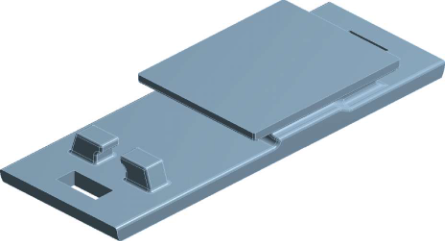
Рисунок 5.30 — Литая подкладка с широкой подушкой
На рисунках 5.31, 5.32 приведено распределение эквивалентных амплитуд напряжений для цельнолитой подкладкой с широкой подушкой. Максимальное значение эквивалентной амплитуды составляет 134 МПа и не превосходит предела выносливости материала.
На рисунках 5.33, 5.34 представлены обобщённые коэффициенты запаса для цельнолитой подкладки с широкой подушкой. Коэффициенты запаса, как для конструкции с зауженной подушкой, превосходят единицу, а минимальное значение составляет 1,22.
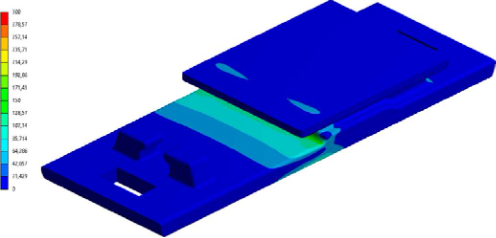
Рисунок 5.31 — Распределение амплитуд напряжений эквивалентного симметричного цикла для цельнолитой подкладки с широкой подушкой(изометрия)
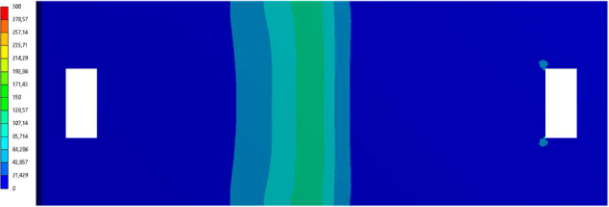
Рисунок 5.32 — Распределение амплитуд напряжений эквивалентного симметричного цикла для цельнолитой подкладки с широкой подушкой(подошва подкладки)
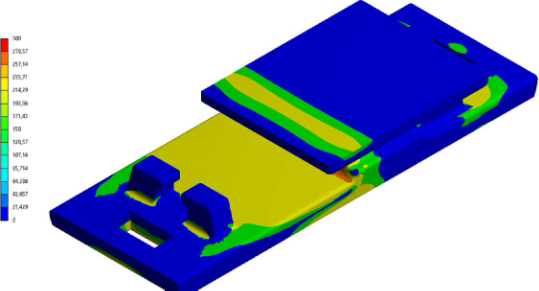
Рисунок 5.33 — Распределение амплитуд напряжений эквивалентного симметричного цикла для цельнолитой подкладки с широкой подушкой(изометрия)
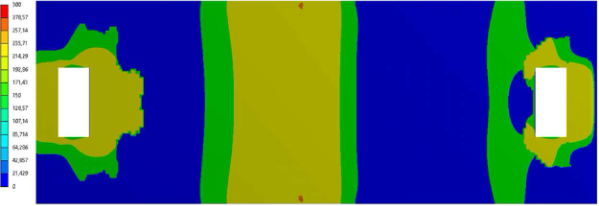
Рисунок 5.34 — Распределение амплитуд напряжений эквивалентного симметричного цикла для цельнолитой подкладки с широкой подушкой (подошва подкладки)
Конструкция цельнолитой подкладки с широкой подушкой в целом удовлетворяет предъявляемым требованиям и является оптимальной среди рассмотренных цельнолитых конструкций.
Выводы
- Для исследования напряженно-деформированного состояния подкладок с подушкой с целью совершенствования ее геометрических размеров был разработан метод, позволяющий подробно рассматривать все особенности геометрии сечений подкладки с подушкой.
Для непосредственных расчетов подкладки с подушкой был использован программный пакет ANSYS, поскольку этот программный комплекс позволяет реализовать модели подкладок с подушкой с необходимой для практических целей точностью. - Расчет напряжений, с использованием программного пакета ANSYS для подкладок с подушкой, показал, что наибольшие напряжения для подкладок с подушкой сварной конструкции достигают максимальной величины в 239 МПа, что отличается от полученных в прямых испытаниях напряжений менее, чем на 6,3 % (полученные в испытаниях напряжения для подкладок той же конструкции составили 200 МПа). Таким образом можно сделать вывод: полученные из расчета и прямых испытаний величины напряжений близки по значениям, следовательно, разработанная математическая модель адекватно отражает напряженное состояние подкладок с подушкой в зонах их наибольшей нагруженности.
- Сходимость результатов исследования напряжений в подкладках непосредственно в пути и на модели позволяет поставить задачу проектирования рациональной конструкции подкладки с подушкой за счет изменения ее геометрии с применением разработанной модели.
- Целевая функция совершенствования подкладки с подушкой сформирована исходя из требований увеличения прочности при сохранении системы ограничений.
Ограничениями служат граничные условия и размеры, определяющие расположения подкладки с подушкой на стрелке стрелочного перевода.
Соответственно размеры подкладки с подушкой должны быть выполнены в пределах размеров существующих в эксплуатации подкладок с подушкой, при этом материал для изготовления идентичен материалу, из которого изготавливают подкладки с подушкой существующих конструкций [82, 83]. - В результате моделирования был получен усовершенствованный вариант цельнолитой подкладки с подушкой.
Технико-экономическое обоснование эффективности применения подкладки с подушкой цельнолитой конструкции
Результаты исследований доказывают, что внедрение в эксплуатацию подкладок с подушкой цельнолитой конструкции позволит увеличить их ресурс, а также ресурс ремкомплекта для стрелочного перевода как минимум на 10-15 %.
Технико-экономическое обоснование эффективности применения подкладки с подушкой цельнолитой конструкции, выполнено в соответствии с действующими в ОАО «РЖД» методическими рекомендациями:
- Методикой определения стоимости жизненного цикла и лимитной цены подвижного состава и сложных технических систем железнодорожного транспорта, утвержденной распоряжением ОАО «РЖД» от 27.12.2007 г. №2459р [84];
- Методическими рекомендациями по обоснованию эффективности инноваций на железнодорожном транспорте, утвержденными руководителем Департамента технической политики МПС 26.04.1999 г. № ЦТех0-11 [85].
Расчет экономии годовых текущих расходов при использовании новых подкладок с подушкой цельнолитой конструкции
Экономия годовых текущих расходов при использовании новых подкладок с подушкой цельнолитой конструкции, по сравнению с используемыми в настоящее время (базовыми) обуславливается увеличением ресурса ремкомплекта для стрелочного перевода.
Наработка до отказа подкладок с подушкой зависит от интенсивности движения поездов и пропущенного тоннажа. Так, средняя наработка до отказа подкладок с подушкой составляет 316,2 млн. т брутто. Средняя наработка до одиночного изъятия из пути подкладок с подушкой за период с 2013 года по 2018 год имела колебания от 300 до 350 млн. т брутто.
Срок службы подкладок с подушкой и ремкомплекта для стрелочного перевода рассчитывается по формуле:
Тсл = Тр / Г год, лет
- где Ггод — среднегодовой грузопоток линии, млн. т;
- Тр — средний ресурс подкладок с подушкой, млн. т.
Для линии со среднегодовым грузопотоком 75 млн. т средний срок службы (ресурс) базовых подкладок с подушкой составит:
Тсл = 316,2 / 75 = 4,2 года.
При использовании новых подкладок с подушкой цельнолитой конструкции, и соответствующем увеличении ресурса на 15 %, средний срок службы составит:
Тсл = 316,2*1,15 / 75 = 4,85 года.
Стоимость замены ремкомплекта стрелочного перевода, обусловленного выходом из строя подкладок с подушкой, составляет в среднем по сети железных дорог ОАО «РЖД» порядка 520 тыс. руб. с учетом стоимости самого ремкомплекта и трудозатрат по его замене.
Исходя из этого могут быть определены годовые текущие расходы по замене ремкомплекта стрелочного перевода, обусловленного выходом из строя подкладок с подушкой, по формуле:
Згод = Ззам / Тсл (6.2)
Среднегодовые текущие расходы по замене ремкомплекта стрелочного перевода составят:
- для базового варианта (подкладка с подушкой, изготовленная с использованием технологии на заклепках):
Збгод = 520 / 4,2 = 123,81 тыс. руб.
- для нового варианта (подкладка с подушкой цельнолитой конструкции)
Знгод = 520 / 4,85 = 107,2 тыс. руб.
Экономия годовых текущих затрат по замене ремкомплекта стрелочного перевода составит:
Эг = ΔЗгод = Збгод — Знгод = 123,81 — 107,2 = 16,61 тыс. руб. на один ремкомплект.
Исходя из существующего наличия на сети железных дорог ОАО «РЖД» , 6 — 7 тысяч полустрелок (или в среднем 6,5 тыс. полустрелок) и количества ремкомплектов на каждую стрелку, суммарная экономия годовых текущих затрат по их заменам составит:
ΣЭг = Эг * N * 2 = 16,61 * 6,5 *103 *2 = 215930 тыс. руб. или 215,93 млн. руб.
Расчет стоимости жизненного цикла стрелочных переводов с цельнолитыми подкладками с подушкой
В настоящее время в отечественной и зарубежной практике все более широкое применение при заключении договоров на поставку сложных технических систем железнодорожного транспорта и при выборе наиболее выгодного предложения при организации конкурсных закупок и тендеров используются такие понятия, как «стоимость (затраты) жизненного цикла» (Life Cycle Cost — LCC) и «управление надежностью, эксплуатационной готовностью, ремонтопригодностью и безопасностью» (RAMS — Reliability, Availability, Maintainability, Safety).
Применение понятий LCC и RAMS обусловлено, в первую очередь, произошедшим в последнее время изменением взаимоотношений между железными дорогами и промышленностью. На современном этапе промышленность берет на себя полную ответственность за разработку изделий и систем. Железная дорога ограничивается выдачей технических требований и гарантиями предоставления данных о системном поведении продукции в течение срока службы (т.е. о затратах жизненного цикла, эксплуатационной готовности). Кроме того, многие железные дороги ориентируются на экономический эффект, определяемый на основе интегрированных оценок расходов в течение всего срока службы используемых изделий и устройств, при разработке и внедрении своих инвестиционных программ. В настоящее время показатель LCC и эксплуатационная готовность становятся основными критериями при оценках в принятии решений по инвестированию, в том числе при строительстве железных дорог.
Для указанных понятий характерно то, что количественные требования и критерии поведения изделия в эксплуатации определяются для реальных условий эксплуатации на весь предусмотренный срок службы и используются в качестве основных показателей при выборе наилучшего варианта осуществления инвестпроектов.
Основной целью определения стоимости жизненного цикла является оценка и/или оптимизация стоимости изделия с учетом срока службы, расходов на обслуживание и ремонт при удовлетворении установленных требований к техническим характеристикам, безопасности, надежности, ремонтопригодности и прочих требований.
Достижение этих целей во многом зависит от надежности отдельных компонентов изделия и возможности обеспечения устойчивой работы техники уже на начальных стадиях ее разработки и создания.
На современном этапе главным критерием выбора направления инвестирования становится не только первоначальная стоимость основных средств, но и величина затрат, связанных с ее эксплуатацией и техническим обслуживанием на протяжении всего срока службы.
Процесс оптимизации в идеальном случае должен начинаться при зарождении идеи по созданию нового изделия и учитывать все затраты, которые предстоит осуществить на протяжении его (изделия) срока службы. Все решения, принимаемые относительно конструирования и изготовления изделия, могут оказать влияние на его рабочие характеристики, требования к безопасности, надежности, ремонтопригодности, материальному обеспечению технического обслуживания и текущего ремонта и т.д. и в конечном итоге определяют его цену и затраты, связанные с приобретением и эксплуатацией.
При сравнении вариантов применения различных типов технических средств выбор осуществляется по минимуму стоимости жизненного цикла при соблюдении требований по техническим параметрам, а также надежности, эксплуатационной готовности, ремонтопригодности и безопасности.
В данной работе проведено всестороннее исследование существующих технологий крепления элементов стрелочных переводов и перспективной, подкладки с подушкой цельнолитой конструкции. Поэтому важно оценить влияние новой технологии с точки зрения стоимости жизненного цикла за весь срок службы системы (стрелочного перевода).
Стоимость жизненного цикла (СЖЦ) технического средства — ремкомплекта стрелочного перевода с применением подкладок с подушкой цельнолитой конструкции, — включает в себя затраты единовременного и текущего характера за срок службы стрелочного перевода, т.е. расходы на первоначальное приобретение и эксплуатацию в течение жизненного цикла.
СЖЦ (LCC — Life Cycle Cost) определяется как с учетом, так и без учета фактора времени (дисконтирования).
С учетом дисконтирования СЖЦ рассчитывается по формуле:
СЖЦ (LCC) = Цпр +E (Згодt — Лt) · @t , (6.3)
- где Цпр — цена приобретения ремкомплекта;
- Згод t — годовые эксплуатационные расходы по сравниваемым вариантам применения подкладок с подушкой базовой и новой;
- Лг — ликвидационная стоимость объекта, тыс. руб.
Поскольку ликвидационную стоимость на данном этапе исследования определить затруднительно, в расчете она не учитывается. При этом необходимо отметить, что ликвидационная стоимость включает в себя как затраты по ликвидации объекта (трудозатраты на демонтаж, транспортировку и т.п.), так и доходы — например, от реализации металлолома. at — коэффициент дисконтирования; t — текущий год эксплуатации; Т — конечный год эксплуатации.
Без учета фактора времени СЖЦ определяется из выражения:
СЖЦ (LCC) = Цпр + Згод * Т (6.4)
Стоимость жизненного цикла согласно Методике [1] рассчитывается на единицу продукции — в данном случае, один ремкомплект.
Для сравниваемых вариантов затраты за жизненный цикл стрелочного перевода, равного 25 годам, составят:
— для базового варианта (подкладка с подушкой, изготовленная с использованием технологии на заклепках):
СЖЦб = 520 + 123,81 * 25 = 3615,25 тыс. руб.
— для нового варианта (подкладка с подушкой цельнолитой конструкции):
СЖЦн = 520 +107,2 * 25 = 3200 тыс. руб.
На рисунке 6.1 приведены данные о СЖЦ сравниваемых конструкций.
3700
3600
3500
3400
3300
3200
3100
3000
2900
Рисунок 6.1 — Стоимость жизненного цикла стрелочных переводов с подкладками с подушкой
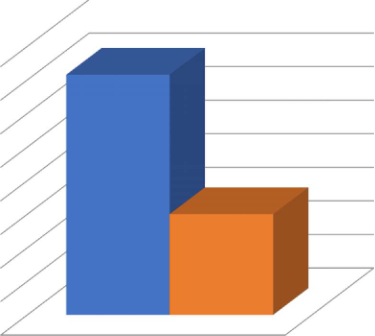
СИНИЙ СЖЦ СП (с подкладками с подушкой, изготовленная с использованием технологии на заклепках)
ОРАНЖЕВЫЙ СЖЦ СП (с подкладками с подушкой цельнолитой конструкции)
Эффективность применения новой технологии крепления стрелочного перевода может быть оценена показателем экономии стоимости жизненного цикла по сравнению с базовой (существующей).
Экономия стоимости жизненного цикла стрелочного перевода за счет внедрения новых подкладок с подушкой цельнолитой конструкции, составит:
ΔСЖЦ = СЖЦб — СЖЦн = 3615,25 — 3200 = 415,25 тыс. руб.
за срок службы стрелочного перевода 25 лет.
Выводы
- Результаты проведенных в диссертационной работе исследований доказывают, что внедрение в эксплуатацию подкладок с подушкой цельнолитой конструкции, позволит увеличить их ресурс, а также ресурс ремкомплекта для стрелочного перевода как минимум на 10-15 %. Это и явилось экономика образующим фактором при оценке эффективности предлагаемой технологии крепления элементов стрелочных переводов.
- Рассчитанная экономия годовых текущих затрат на ремонт (замену) ремкомплектов стрелочного перевода, обусловленный выходом из строя сравниваемых подкладок с подушкой, составляет 16,61 тыс. руб. в расчете на один ремкомплект или 215,93 млн. руб. для условий сети ОАО «РЖД».
- Расчет экономии затрат жизненного цикла также показал эффективность применения новой технологии. Экономия стоимости жизненного цикла стрелочного перевода составит 415,25 тыс. руб. за срок его службы 25 лет.
Заключение
- Поставлена и решена задача повышения ресурса стрелок стрелочных переводов за счет усовершенствования прикрепления рельсовых элементов стрелки к основанию, а именно подкладки с подушкой.
- Главным фактором, определяющим эксплуатационные качества подкладок с подушкой, является их конструкция.
- Выявлены дефекты, которые не включены в «Классификатор дефектов и повреждений элементов стрелочных переводов».
- Наработка до отказа подкладок с подушкой зависит от интенсивности движения поездов и пропущенного тоннажа. Так, средняя наработка до отказа подкладок с подушкой по данным составляет 316,2 млн. т брутто. Средняя наработка до изъятия из пути подкладок с подушкой за период с 2013 года по 2018 год имела колебания от 300 до 350 млн. т брутто.
- В результате анализа данных по отказам и динамико-прочностных испытаний получен вывод, о том, что серийно выпускаемые подкладки с подушкой всех видов для стрелок имеют неудовлетворительную эксплуатационную стойкость и нуждаются в доработке.
- По результатам металлографических исследований получено, что причиной излома является недостаточная циклическая прочность сварного шва, кроме того, в микроструктуре металла подкладки в зоне термического влияния сварки наблюдается распространение микротрещин.
- Изломы подкладок с подушкой имеют общие характерные особенности. Линия излома во всех случаях пересекает место изменения формы подкладки с подушкой, которое представляет собой концентратор механических напряжений и располагается вдоль внутренней кромки рамного рельса.
- Улучшение прочностных и эксплуатационных характеристик подкладок с подушкой может быть достигнуто за счет:
- применения металла с более высокими прочностными характеристиками;
- изменения конструкции подкладок с подушкой за счет увеличения толщины пластины подкладки и (или) введения специальных конструктивных решений (например, разгружающих выкружек), уменьшающих концентрацию напряжений;
- изменения технологии изготовления подкладок с подушкой, путем ликвидации технологических отверстий и удаления термических узлов от мест расположения концентраторов напряжений;
- применения принципиально новых подкладок с подушкой за счет новых технических решений, в частности за счет применения литой конструкции.
9. Для исследования напряженно-деформированного состояния подкладок с подушкой с целью совершенствования ее геометрических размеров разработан метод, позволяющий рассматривать все особенности геометрии сечений и работы под нагрузкой подкладки с подушкой.
Непосредственные расчеты подкладок с подушкой выполнены с использованием программного пакета ANSYS, позволяющего выполнить расчеты подкладок с необходимой для практических целей точностью.
Целевая функция совершенствования подкладки с подушкой сформирована исходя из требований увеличения прочности при сохранении системы ограничений.
10. В результате моделирования получен усовершенствованный вариант цельнолитой подкладки с подушкой.
Разработанная конструкция подкладки с подушкой, отличается тем, что подушка имеет соотношение a/b, равное 250/200, где а — является длиной подушки, b — шириной подушки, и пропорциональна размеру самой подкладки.
11. Внедрение в эксплуатацию подкладок с подушкой цельнолитой конструкции позволит увеличить их ресурс, а также ресурс ремкомплекта для стрелочного перевода как минимум на 10-15 %. Это и является экономика образующим фактором при оценке эффективности предлагаемой технологии крепления элементов стрелочных переводов.
Рассчитанная экономия годовых текущих затрат на ремонт (замену) ремкомплектов стрелочного перевода, обусловленный выходом из строя сравниваемых подкладок с подушкой, составляет 16,61 тыс. руб. в расчете на один ремкомплект или 215,93 млн. руб. для условий сети ОАО «РЖД».
Расчет экономии затрат жизненного цикла также показывает эффективность применения новой технологии. Экономия стоимости жизненного цикла стрелочного перевода составит 415,25 тыс. руб. за срок его службы 25 лет.
12. Для регистрации полезной модели, полученной в результате в ходе исследований, поданы документы для получения свидетельства на полезную модель «Цельнолитая подкладка с подушкой».
13. Перспективой дальнейшей разработки темы диссертационного исследования является проведения аналогичных работ для других элементов стрелочных переводов. При этом могут быть использованы подходы и методы, разработанные в данной диссертации.
Список Литературы
- Глюзберг, Б.Э. Стрелочное хозяйство российских железных дорог: проблемы и перспективы / Б.Э. Глюзберг // РСП Эксперт. — 2015. — №3. — С. 36-37.
- Глюзберг, Б.Э. Модернизация и совершенствование стрелочных переводов / Б.Э. Глюзберг // Железнодорожный транспорт. — 2015. — №7. — С. 54-57.
- Глюзберг, Б.Э. Перспективы развития стрелочной продукции для российских железных дорог / Б.Э. Глюзберг // Материалы Международной 9-ой Всероссийской научно-практической конференции «Внедрение современных конструкций и передовых технологий в путевое хозяйство». — М.: МГУПС, 2015. — С. 34 — 38.
- Глюзберг, Б.Э. Актуальные проблемы стрелочного хозяйства / Б.Э. Глюзберг // Железнодорожный транспорт. — 2017. — №7. — С. 45-48.
- Королев, В.В. Высокоскоростные стрелочные переводы нового поколения / В.В. Королев // Международный научно-практический семинар, посвященный 100-летию со дня рождения профессора С.В. Амелина Сб. мат. н.-т. конф. ПГУПС. СПб. 2009. — С. 30-32.
- Мониторинг стрелочных переводов // Ж.-д. трансп. за рубежом. Сер.З: ЭИ / ЦНИИТЭИ МПС. 2003. Вып. 2. С. 27-31: ил. — International Railway Journal. 2002. №8. р.27-28.
- Басовский, Д.А. Используемые расчетные схемы при оценке напряженно- деформированного состояния стрелочных переводов / Д.А. Басовский, А.Н. Марчук, В.И. Шулындин // Материалы международного научно-практического семинара, посвященного 100-летию со дня рождения профессора С.В. Амелина. ПГУПС. СПб, 2009. — С.104 — 109.
- Королев, В.В. Напряженное состояние элементов скоростного стрелочного перевода / В.В. Королев // Развитие железнодорожного транспорта в условиях реформ: сб. науч. тр. конф. ВНИИЖТ. М: Интекст, 2003. — С. 231-235.
- Глюзберг, Б.Э. Подход к анализу надежности соединений и пересечений рельсовых путей / Б.Э. Глюзберг // Особенности системы ведения рельсового хозяйства на российских ж.д. Труды АО «ВНИИЖТ» М.: ООО «РАС», 2017. — С. 101-107.
- Глюзберг, Б.Э. Определение показателей надежности для невосстанавливаемых элементов путевых конструкций / Б.Э. Глюзберг, А.М. Калачев, М.И. Титаренко // Вестник ВНИИЖТ. — 2001. — № 2. — С. 25-27.
- Федулов, И.Т. Дополнительные башмаки [подкладки] на стрелочном переводе / И.Т. Федулов, Ю.А. Торопов // Путь и путевое хозяйство. — 2001. — № 11. — С. 37.
- Новые конструкции элементов стрелочных переводов и глухих пересечений: // Ж.д. мира. 2004. №4. С.60-64: ил. — Railway Age. 2002. №8. р.22, 27, 41; №9. р.87-91; Railway Track & Structures. 2003. №1. р.15-17.
- Совершенствование элементов стрелочных переводов // Ж.д. мира. 2003. №2. С. 63-65: ил. — International Railway Journal. 2002. №3. p.24-25.
- Новые конструкции стрелочных переводов // Ж.д. мира. 2003. №3. С.74- 76: ил. — Railway Track & Structures. 2000. №5. р.14-17.
- Шишкина, И.В. Этапы проектирования технических средств инфраструктуры для российских железных дорог / И.В. Шишкина, Н.В. Зверкова, Л.А. Елесина // Студент инновации России. — 2017. — №2. — С.12 — 17.
- Новые материалы и конструкции стрелочных переводов // Ж.-д. трансп. за рубежом. Сер.4: ЭИ/ВНИИАС МПС России. Отд-ние информ. (ЦНИИТЭИ). 2003. Вып.4 С. 26-27. — Railway Age. 2002. №8. p.22, 27, 41 (англ.); Railway Track & Structures. 2003. №1. p.27-28 (англ.).
- Gerber U., Wolfgang F. Belastung von Weichen mit starrer Herzstbckspitze // ZEV rail Glasers Annalen. 2007. № 5. S. 202-214.
- Thiele, R. Vogel & Plu, tscher. DB-Anwenderfreigabe fbr MessReg CDM // Der Eisenbahningenieur. 2007. № 3. S. 75.
- Ермаков, В.М. Комплексная система реализации ресурсосбережения в современных условиях работы железнодорожного пути [Текст]: дис. … док. тех. наук: ПГУПС / Ермаков Виктор Михайлович. — М., 2000. — 435 с.
- Глюзберг, Б.Э. Рельсовые элементы стрелочных переводов / Б.Э. Глюзберг, М.И. Титаренко, В.В. Королев // Железнодорожный транспорт. — 2011. — № 1. — С. 19-21.
- Глюзберг, Б.Э. Основные причины отказов рельсовых элементов стрелочных переводов / Б.Э. Глюзберг, М.И. Титаренко, В.В. Королев // «Улучшение качества и условий эксплуатации рельсовых и рельсовых скреплений» Сб. науч. док. по мат. 128-го заседания НП «Рельсовая комиссия», Москва, 2012.
- Королев, В.В. Дефекты элементов стрелочных переводов / В.В. Королев // Внедрение современных конструкций и технологий в путевое хозяйство: сб. мат. н.-т. конф. РОАТ, М. 2009. С. 37-41.
- Глюзберг, Б.Э. Классификатор дефектов и повреждений элементов стрелочных переводов / Б.Э. Глюзберг, А.Ю. Абдурашитов, В.В. Королев // ОАО «РЖД». — М.: Центр «Транспорт», 2012. — 96 с.
- Королев, В.В. Новый классификатор дефектов и повреждений стрелочных переводов / В.В. Королев // «Улучшение качества и условий эксплуатации рельсовых и рельсовых скреплений» Сб. науч. док. по мат. 128-го заседания НП «Рельсовая комиссия», Москва, 2012.
- Классификация дефектов и повреждений элементов стрелочных переводов. Доп. к РТМ 32/ЦП-1-75. Каталог дефектов и повреждений элементов стрелочных переводов. Доп. к РТМ 32/ЦП-2-75. Признаки дефектных и остро дефектных элементов стрелочных переводов. Доп. к РТМ 32/ЦП-3-75: нормативно- технический материал / МПС СССР. Гл. упр. пути; СССР. МПС. Гл. упр. пути. М.: Транспорт, 1981. — 47 с.
- Шишкина, И.В. Основные причины отказов рельсовых элементов стрелочных переводов / И.В. Шишкина, Р.О. Яковлев, А.В. Мазанкин, Е.В. Мазанкина, Д.А. Казаков // Студент инновации России. — №2 (6). — 2018. — С.23-30.
- Королев, В.В. Новый классификатор дефектов и повреждений стрелочных переводов / В.В. Королев // Безопасность движения поездов: сб. мат. н.-т. конф. МИИТ. 2009.
- Королев, В.В. Дефекты элементов стрелочных переводов / В.В. Королев // Путь и путевое хозяйство. — 2013. — №8. — С.13-16.
- Королев, В.В. Новые виды отказов подкладок с подушками и подкладок с упорами / В.В. Королев // «Внедрение современных конструкций и технологий в путевое хозяйство» Сб. мат. 7-ой н.-т. конф. МГУПС МИИТ, М.: ИЦ «АИСНт» 2014. — С. 53-65.
- Королев, В.В. Совершенствование системы учета дефектов элементов стрелочных переводов / В.В. Королев // Путь и путевое хозяйство. — 2016. — №7. — С. 14-16.
- Шишкина, И.В. Неразрушающий контроль рельсовых элементов стрелочных переводов на железных дорогах России / И.В. Шишкина, С.А. Голубков, Д.О. Макухин, О.Д. Никифоров, П.С. Макаров, А.А. Французов // Студент инновации России. — 2017. — №4. — С. 35-44.
- Глюзберг, Б.Э. Стратегия исследований и разработок в области стрелочного хозяйства / Б.Э. Глюзберг // Путь и путевое хозяйство. — 2011. -№ 2. — С. 11-14.
- Королев, В.В., Шишкина И.В. Система учета дефектов элементов стрелочных переводов / В.В. Королев, И.В. Шишкина // «Внедрение современных конструкций и технологий в путевое хозяйство» Сб. мат. 9-ой н.-т. конф. МГУПС МИИТ, М.: ИЦ «АИСНт» 2016. — С. 188-193.
- Bateman, D. Upgrading S&C for the future // The Permanent Way Institution. 2002. Vol. 140. № 4. р. 347-353.
- Bonaventura, С. S. Increasing speed through turnouts // Railway Track & Structures. 2004. N 7. p. 20-23.
- Davis, D. D. Railroad switch design and failure mode analysis // Railway Track & Structures. 2003. N 6. р. 19-21.
- Глюзберг, Б.Э. Стрелочные переводы / Б.Э. Глюзберг, М.Ф. Вериго, В.Г. Альбрехт, А.М. Тейтель // Труды ЦНИИ МПС. Вып.546, М.,1976.
- Титаренко, М.И. Анализ работы стрелочных башмаков / М.И. Титаренко, В.В. Королев // «Внедрение современных конструкций и технологий в путевое хозяйство» Сб. мат. 5-ой н.-т. конф. МГУПС МИИТ, М.: ИЦ «АИСНт». 2012. — С. 109-110.
- Хвостик, М.Ю. Мониторинг повреждаемости рельсов типа Р65 при различных условиях эксплуатации на сети железных дорог России / М.Ю. Хвостик, Л.А. Джанполадова, И.В. Шишкина, Г.А. Берестень // «Повышение эффективности устойчивости содержания железнодорожного пути» Труды ОАО «ВНИИЖТ» ВМГ Принт, Москва, 2014. — С. 105-111.
- Глюзберг, Б.Э. Испытания стрелочных переводов на Экспериментальном кольце ВНИИЖТ / Б.Э. Глюзберг // Вестник ВНИИЖТ. — 2002. — №4 (Спец. вып.). С. 24-25.
- Глюзберг, Б.Э. Интегральные показатели надежности стрелочных переводов и стрелочного хозяйства / Б.Э. Глюзберг // РСП ЭКСПЕРТ. — 2016. — №4. С. 22 — 23.
- Вериго, М.Ф. Взаимодействие пути и подвижного состава / М.Ф. Вериго, А.Я. Коган А.Я. — М.: Транспорт, 1986. — 560 с.
- Глюзберг, Б.Э. Применение оптимизационных алгоритмов для усовершенствования конструкции стрелочных переводов / Б.Э. Глюзберг // Вестник ВНИИЖТ. — Том 75, №2. — 2016. — С. 67 — 73.
- Глюзберг, Б.Э. Влияние нагрузок подвижного состава на сроки службы элементов стрелочных переводов / Б.Э. Глюзберг // Современные способы совершенствования работы ж.д. транспорта — М.: МГУПС, 2016. — С. 157-158.
- Радыгин, Ю.Н. Совершенствование геометрических, конструктивных параметров и норм содержания стрелочных переводов: автореф. дис… канд. техн. наук: 05.22.06. / Радыгин Юрий Николаевич. — М., 2003. — 24 с.
- Глюзберг, Б.Э. Вопросы проектирования технических средств инфраструктуры железных дорог / Б.Э. Глюзберг, Н.В. Зверкова, В.В. Королев, И.В. Шишкина // Путь и путевое хозяйство. — 2018. — №2. — С.20-22.
- Королев, В.В. Организация работ по контролю рельсовых элементов стрелочных переводов на железных дорогах России / В.В. Королев, В.А. Мальцев // «Внедрение современных конструкций и технологий в путевое хозяйство» Сб. мат. 7-ой н.-т. конф. МГУПС МИИТ, М.: ИЦ «АИСНт», 2014. — С. 45-52.
- Глюзберг, Б.Э., Королев В.В. Подготовка технических средств и нормативной документации по стрелочному хозяйству для линий высокоскоростного движения / Б.Э. Глюзберг, В.В. Королев // Конструкции железнодорожных путей и вопросы технического обслуживания высокоскоростных магистралей: сб. мат. н.-т. конф. ПГУПС. 2010.
- Певзнер, В.О. Путь и повышенные осевые нагрузки вагонов [Текст] / В.О. Певзнер, О.Ю. Белоцветова, И.Б. Петропавловская [и др.] // Железнодорожный транспорт. — 2014. — № 4. — С. 55-58.
- Шишкина, И.В. Применение стрелочных переводов с непрерывной поверхностью катания при повышении осевых нагрузок и скоростей движения поездов / И.В. Шишкина, Н.В. Зверкова, Л.А. Елесина // «Внедрение современных конструкций и технологий в путевое хозяйство» Сб. мат. 12-ой н.-т. конф. РУТ МИИТ, М.: ИЦ «АИСНт», 2018. — С. 127-129.
- Королев, В.В. Виды отказов подкладок с подушками и подкладок с упорами / В.В. Королев // «Повышение эффективности устойчивости содержания железнодорожного пути» Труды ОАО «ВНИИЖТ» ВМГ Принт, Москва. — 2014. — С.42-49.
- Королев, В.В. Совершенствование системы учета дефектов элементов стрелочных переводов / В.В. Королев // «Современные проблемы проектирования, строительства и эксплуатации железнодорожного пути» XIII Н н.-т. конф. с международным участием к 120-летию МГУПС (МИИТ) (чтения, посвященные памяти проф. Г.М. Шахунянца) Сб. мат. н.-т. конф. МИИТ, М.: 2016. — С. 195-196.
- Шишкина, И.В. Дефекты элементов стрелочных переводов подкладок с подушками и подкладок с упорами / И.В. Шишкина // Материалы научно- технического семинара. «Конструкция и техническое обслуживание железнодорожного пути при организации тяжеловесного движения» ПГУПС, СПб.: 2017. — С. 188-192.
- Гридасова, Е.А. Изменение структуры рельсовой стали при высокочастотном нагружении / Е.А. Гридасова, П.А Никифоров, А.А Локтев, В.В. Королев, И.В. Шишкина // Сборник научных докладов по материалам 134-го заседания НП «Рельсовая комиссия» — Владивосток, 2018.
- Горбунов-Посадов, М.И., Маликова Т.А. Расчёт конструкций на упругом основании / М.И. Горбунов-Посадов, Т.А. Маликова. — 2-е изд., перераб. и доп. — М.: Стройиздат, 1973. — 627 с.
- ГОСТ Р56291-2014 Прокладки рельсовых скреплений железнодорожного пути. Технические условия. — М.: Стандартинформ, 2015. — 28 с.
- Евтух, Е.С. Влияние рельсовых стыков на контактно-усталостную прочность колёс железнодорожного подвижного состава: дис… канд. техн. наук: 05.22.07 / Евтух Елена Сергеевна. — Брянск, 2014. — 111 с.
- Решетов, Д.Н. Детали машин: Учебник для студентов машиностроительных и механических специальностей вузов / Д.Н. Решетов. — 4-е изд., перераб. и доп. — М.: Машиностроение, 1989. — 496 с., ил.
- ГОСТ 1 6277-93 Подкладки раздельного скрепления железнодорожного пути. Технические условия. — М.: Стандартинформ, 2016. — 16 с.
- ГОСТ 380-2005 Сталь углеродистая обыкновенного качества. Марки. — М.: Стандартинформ, 2009. — 10 с.
- Сорокин, В.Г. Марочник сталей и сплавов / В.Г. Сорокин., А.В. Волоспикова, С.А. Вяткин и др.; под общ. ред. В.Г. Сорокина. — М.: Машиностроение, 1989. — 640 с.
- Тылкин, М.А. Справочник термиста ремонтной службы / М.А. Тылкин — М.: Металлургия, 1981. — 648 с.
- Колосков, М.М. Марочник сталей и сплавов / М.М. Колосков, Е.Т. Долбенко, Ю.В. Каширский и др. — М.: Машиностроение, 2001. — 671 с.
- Пестриков, В.М. Механика разрушения твёрдых тел: курс лекций / В.М. Пестриков, Е.М. Морозов — СпБ.: Профессия, 2002. — 320 с., ил.
- ГОСТ 25.502-79 Расчеты и испытания на прочность в машиностроении. Методы механических испытаний металлов. Методы испытаний на усталость. — М.: Изд-во стандартов, 1979. — 32 с.
- ГОСТ 25.504-82 Расчеты и испытания на прочность. Методы расчета характеристик сопротивления усталости. — М: Изд-во стандартов, 1982. — 80 с.
- Гоц, А.Н. Расчёты на прочность при переменных напряжениях: монография / А.Н. Гоц — Владимир: Изд-во ВлГУ, 2012. — 138 с.
- Коренев, Б.Г. Некоторые задачи балок на упругом основании / Б.Г. Коренев, М.Н. Ручимский // Научное сообщение №120 Центрального научно- исследовательского института промышленных сооружений. М.: Стройиздат, 1955. 54 с.
- Муравский, Г.Б. Неустановившиеся колебания балки, лежащей на упругом основании, при действии подвижной нагрузки / Г.Б. Муравский // Изв. АН СССР, ОТн Мех. и машиностроения. — 1962. — №1. — 117 с.
- Муравский, Г.Б. Действие подвижной нагрузки на балку бесконечной длины, лежащую на упругом основании / Г.Б. Муравский // Тр. МИИТ. Вып.134. 1961. — С.54-84.
- Морозов, Е.М., Муйземнек А.Ю., Шадский А.С. ANSYS в руках инженера. Механика разрушения / Е.М. Морозов, А.Ю. Муйземнек, А.С. Шадский М.: ЛЕНАНД, 2008. — 456 c.
- Басов, К.А. ANSYS: справочник пользователя / К.А. Басов — М.: ДМК Пресс, 2005. — 640 с.
- Theory Reference for ANSYS and ANSYS Workbench. ANSYS Release 11.0. ANSYS Inc., January 2007.
- Глюзберг, Б.Э., А. Локтев, В. Сычев, Е. Гридасова Modeling the dynamic behavior of railway track taking into account the occurrence of defects in the system wheel-rail.
- Loktev, A. Modeling the dynamic behavior of the upper structure of the railway track / A. Loktev, V. Vadim, I. Shishkina, D. Basovsky // Transportation Geotechnics and Geoecology (TGG 2017, 17-19 May 2017). — Saint Petersburg: — 2017. — P. 133 — 137.
- Королев, В.В. Новые конструкции пути рельсошпальной решетки для наземного электрического рельсового транспорта и метрополитена / В.В. Королев, С.С. Князев, И.В. Шишкина // Межвузовский сборник научных трудов «Современные проблемы совершенствования работы железнодорожного пути» МГУПС «МИИТ» — Москва, 2017. — С.78 — 84.
- Глюзберг, Б.Э., Локтев А.А., Локтев Д.А., Гелюх П.А., Королев В.В., Шишкина И.В. Применение методов моделирования для определения скоростей движения по участкам пути, на которых расположены комбинации стрелочных переводов / Б.Э. Глюзберг, А.А. Локтев, Д.А. Локтев, П.А. Гелюх, В.В. Королев, И.В. Шишкина // История и перспективы развития транспорта на севере России, — Ярославль, 2018. — №1. — С. 73-78.
- Glusberg, B. Calculation of track component failure caused by the most dangerous defects on change of their design and operational conditions / B. Glusberg, V. Korolev, I. Shishkina, A. Loktev, J. Shukurov, P. Geluh, D. Loktev // TransSiberia 2018 (MATEC Web of Conferences). — 2018. — № 239. — Режим доступа: doi.org/10.1051/matecconf/ 201823901054
- Loktev, A. High frequency vibrations in the elements of the rolling stock on the railway bridges / A. Loktev, V. Korolev, I. Shishkina // International MultiConference on Industrial Engineering and Modern technologies (Materials Science and Engineering). — 2018 — № 463 — Режим доступа: doi: 10.1088/1757-899X/ 463/3/032019
- Riley P. The Benefits of S&C Design Convergence // Permanent Way Institution. 2007. Vol. 125. № 1. p. 23-24.
- South G. NR 60 S&C and the Way Forward // Permanent Way Institution. 2007. Vol. 125. № 1. p. 19-21.
- Special trackwork // RT&S Track Buyer’s Guide. 2007. p. 54-55.
- Глюзберг, Б.Э. Проектирование соединений путей: уч. пос./ Б.Э. Глюзберг, А.А. Локтев, А.В. Савин, В.В. Королев. Москва: Российский университет транспорта (МИИТ), 2018,- 160 с. ISBN 978-5-00122-781-6. — 30 экз.
- Методика определения стоимости жизненного цикла и лимитной цены подвижного состава и сложных технических систем железнодорожного транспорта, утвержденная Распоряжением ОАО «РЖД» от 27.12.2007 г. №2459р.
- Методические рекомендации по обоснованию эффективности инноваций на железнодорожном транспорте, утвержденные Руководителем Департамента технической политики МПС 26.04.1999 г. № ЦТех0-11.