- Введение
- Состояние вопроса, цели и задачи исследования
- Анализ причин отказов стрелочных переводов и их элементов
- Повышение эксплуатационных качеств стрелочных переводов за счет производства элементов повышенной надежности
- Технологические методы повышения качества элементов стрелочных переводов
- Эффективность разработок по повышению качества стрелочной продукции
- Заключение
- Список использованных источников
Введение
Современный уровень состояния конструкций и технологий изготовления стрелочной продукции для железных дорог России сложился, как результат многолетней направленной политики МПС в условиях интенсивного роста перевозок и дефицита материально- технических ресурсов для развития производства.
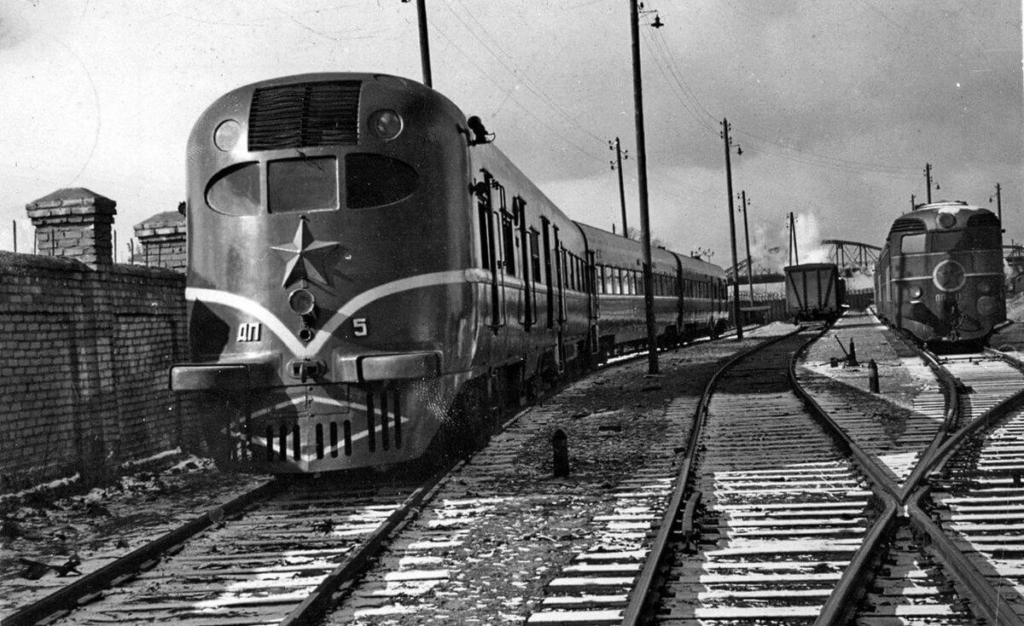
В этих условиях от стрелочных заводов в первую очередь требовалось постоянное наращивание объема выпуска продукции. Работы по совершенствованию стрелочной продукции обеспечивали рост ее качества, однако основные усилия сосредоточивались на создании дополнительных производственных мощностей. Переоснащение производства, разработка и внедрение новых технологий отодвигались на второй план.
Этому же была подчинена и направленность на максимальную унификацию конструкций стрелочных переводов и на специализацию каждого из заводов по выпуску конкретных видов продукции. В результате после ликвидации СССР сеть дорог МПС России оказалась зависимой от поставок некоторых видов стрелочных переводов из-за рубежа, а стрелочные заводы России от поставки зарубежных комплектующих.
Современный этап развития страны требует от специалистов железнодорожного транспорта решения новых задач. В области стрелочных переводов это создание надежных, долговечных и малообслуживаемых стрелочных переводов, полное удовлетворение потребностей российских железных дорог всеми видами стрелочной продукции, выход на зарубежные рынки.
Следует отметить, что сегодня российским стрелочным заводам приходиться вступать в конкурентную борьбу с иностранными конкурентами уже не только за зарубежные рынки, но и в самой России. В связи с этим вопрос повышения качеств стрелочной продукции, производимой российскими стрелочными заводами, становится первостепенным.
Улучшить качество стрелочной продукции можно за счет усовершенствования конструкции стрелочных переводов, за счет совершенствования существующих технологических процессов изготовления основных элементов стрелочных переводов и за счет внедрения принципиально новых технологий. В каждом из этих направлений специалистами-учеными, конструкторами, технологами, — ведутся серьезные работы.
За последние годы разработаны и внедрены в производство стрелочные переводы с непрерывной поверхностью катания, усиленные конструкции стрелок и крестовин, скрепления с высокими ребордами и другие усовершенствования. В настоящее время стрелочные заводы России осваивают ежегодно несколько новых видов стрелочной продукции. Сегодня они способны полностью обеспечить потребности железных дорог России как по объему, так и по номенклатуре стрелочных переводов.
Диссертационная работа посвящена обобщению опыта разработок и освоения производства стрелочной продукции и выделению основных перспективных направлений для дальнейших работ по отбору и созданию технологий для производства новых конкурентоспособных стрелочных переводов с улучшенными эксплуатационными качествами.
В качестве исходного материала проводится анализ причин отказов стрелочных переводов и их элементов.
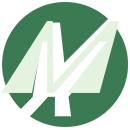
В основной части работы рассмотрены методы улучшения эксплуатационных качеств стрелочных переводов за счет производства элементов подушенной надежности, технологические методы повышения качества элементов стрелочных переводов и улучшение качества металла для изготовления стрелочных переводов, а также методов обработки. Основу материалов этих разделов составят разработки, которые ведутся на Муромском стрелочном заводе, но также использован опыт других предприятий и зарубежный опыт.
Состояние вопроса, цели и задачи исследования
Характеристика состояния стрелочного хозяйства российских железных дорог
На железных дорогах МПС России в настоящее время эксплуатируется около 215 тыс. стрелочных переводов, из них в главных путях около 65 тыс. переводов.
На главных путях преимущественным типом перевода являются переводы типа Р65. Их доля в главных путях превышает 70%. Доля стрелочных переводов типа Р50 в главных путях — около 25%. На остальные типы приходится менее 5% стрелочных переводов.
Среднее расстояние между станциями на сети дорог составляет 11 км, поэтому состояние стрелочных переводов существенно влияет на перевозочный процесс.
Из эксплуатируемых переводов в пути насчитывается в целом около 11% дефектных, требующих замены или ограничений скоростей движения. Однако по некоторым видам переводов количество дефектных значительно выше. Так дефектных двойных перекрестных стрелочных переводов , эксплуатируемых в пути, находится более 22%.
Средний ресурс стрелочного перевода в 2 и более раза меньше, чем у перегонного пути с рельсами того же типа.
Большинство работ по содержанию стрелочных переводов выполняется вручную. В настоящее время более 15% всех расходов путевого хозяйства железных дорог МПС РФ составляют расходы на содержание стрелочных переводов.
В 1993-1996 г.г. в среднем на сети вводилось около 500 ограничений скоростей движения поездов по состоянию/ стрелочных переводов.
Общесетевой статистики случаев особого учета на стрелочных переводах не ведется. По частоте повторяемости причин этих случаев можно расположить (по убыванию) в следующем порядке:
- случаи, связанные с состоянием колеи стрелочных переводов;
- случаи, связанные с вкатыванием колес на рельсовые элементы (в основном, в зоне «остряк — рамный рельс»);
- случаи, связанные с изломом элементов стрелочного перевода;
- случаи, связанные с изломами в зонах стыков и дефекты стыков.
Официальной отчетности по выходу стрелочных переводов и их основных элементов, несмотря на многолетние обращения специалистов нет. Это существенным образом затрудняет анализ причин отказов переводов.
Исследования и разработки, направленные на улучшение эксплуатационных качеств стрелочных переводов
Исследовательскии работы по улучшению эксплуатационных качеств стрелочных переводов, по созданию конструкций, отвечающих требованиям современных условий функционирования пути, находятся в центре внимания специалистов путейцев в нашей стране и за рубежом /8, 40, 45, 49, 79, 89, 90, 95, 96, 115-118, 144, 157, 159/.
Болышие исследования в этом направлении проведены научными коллективами во ВНИИЖТа под руководством докторов технических наук Н.Н.Путри, Б.Э.Глюзберга, Г.Г.Желнина, кандидатов технических наук А.М.Тейтеля, Л.Г.Крысанова, инженеров В.Г.Донца и М.И.Титаренко; в ЛИИЖТе (ПГУПСе) под руководством профессоров С.В.Амелина, В.Ф.Яковлева, М.П.Смирнова, кандидата технических наук В.И.Абросимова; в ДИИТе сотрудникми кафедры, возглавляющейся профессором М.А.Фришманом, а в настоящее время руководимой профессором В.Д. Дановичем.
Проектные работы по созданию и совершенствованию стрелочных переводов под руководством кандидата технических наук H.H. Елсакова коллективом верхнего строения пути долгие годы возглавлявшегося инженером Ю.Н. Петровым.
В настоящее время основные работы по проектированию стрелочных переводов ведутся главными конструкторами, инженерами С.О. Суриным, В.Н. Ткаченко. Руководит отделом инженер А.К. Гучков.
Как в нашей стране, так и за рубежом научные исследования и проектные работы развиваются по нескольким основным направлениям.
Важнейшие из них — создание новых конструкций, совершенствование серийно выпускаемых массовых конструкций, исследования по рациональному использованию и ремонту стрелочных переводов, их основных элементов по совершенствованию методов их укладки и текущего содержания /43, 44, 83, 98, 100, 112, 120, 138/. Ведутся работы по совершенствованию методов расчета и проектирования стрелочных переводов и их основных узлов — стрелки, переводной кривой, крестовинного узла /9, 69, 86, 106, 132, 135, 137, 154/.
Базой для всех этих исследований и разработок являются работы по совершенствованию технологии изготовления основных элементов стрелочных переводов и внедрению качественно новых технологических процессов, позволяющих получать более высокие показатели соблюдения требований конструкторской документации и обеспечивать производство принципиально новых конструктивных элементов повышенной прочности и эксплуатационной надежности.
Работоспособность стрелочного перевода во многом определяется состоянием узла стрелки. Наиболее опасным видом дефектов этого узла являются трещины в подошве остряков в зоне их прилегания к рамным рельсам, возникающие, как правило, из-за дефектов, связанных с механической обработкой. Для ликвидации этого вида дефектов ПТКБ ЦП и ВНИИЖТом при участии специалистов стрелочных заводов была разработана новая конструкция стрелки с остряком параллельным рамному рельсу в зоне его прилегания к последнему /50/. Благодаря такой конструкции стрелки удалось разработать и внедрить новые экономичные формы острякового проката /103/, не требующие обработки подошвы остряка и его головки (со стороны рамного рельса), и тем самым ликвидировать предпосылки возникновения таких дефектов.
Для улучшения сопротивляемости остряков возникновению контактных повреждений зоны перекатывания был разработан новый продольный профиль остряков, позволяющий перераспределять контактные давления колес в узких сечениях остряка на рамный рельс, а также введена закалка остряков на стрелочных заводах /103, 147/.
Важное значение для улучшения эксплуатационных качеств стрелки имело также усиление переднего вылета рамного рельса и переход к массовому выпуску стрелок с гибкими остряками, значительно улучшающими работу корневой части остряка.
В результате внедрения комплекса названных разработок удалось увеличить срок службы узла стрелки на 15-20% и повысить надежность. Следует отметить работы по созданию спецпроката для изготовления рамных рельсов. Внедрение этой разработки совместно с вышеперечисленными, позволяет свести механическую обработку узла остряк-рамный рельс к формированию рабочей поверхности остряка, его корневой части и сверлению отверстий под установку элементов креплений и упорок, однако такая конструкция рамного рельса имеет и недостатки и нуждается в дальнейших исследованиях.
Наряду с достижениями по совершенствованию конструкции узла стрелки следует отметить, что ряд параметров этого узла нуждается в дальнейшем улучшении. Это, в первую очередь, дальнейшее улучшение продольного профиля остряков, поперечного профиля острякового проката, дефектостойкости стыков: остряков с примыкающими рельсами, обоснование нормирования взаимного положения остряка и рамного рельса в прижатом положейии, обоснование ширины колеи на стрелке и норм размеров желобов между отведенным остряком и рамным рельсом, нормирование специфических форм износа системы остряк — рамный рельс.
Требует решения также и проблема повышенного бокового износа остряков (криволинейных) и рамных рельсов, обострившаяся в последние годы. Для решения этой проблемы были разработаны контррельсы-протекторы, которые, одновременно со снижением бокового износа элементов стрелки, повышают безопасность движения поездов по стрелке с изношенными остряками и рамными рельсами /32, 33/. Однако конструкция контррельсов-протекторов нуждается в дальнейшем совершенствовании и решает проблему бокового износа лишь частично.
В настоящее время для улучшения динамики взаимодействия пути и подвижного состава в горизонтальной плоскости в зоне стрелки стрелочных переводов и снижения бокового износа остряков и рамных рельсов отрабатываются конструкции стрелки с упругим прикреплением рамных рельсов. Эти конструкции проходят испытания и несмотря на полученные первые положительные результаты требуют дальнейшего усовершенствования.
На условия движения подвижного состава по стрелочному переводу большое влияние оказывает состояние соединительных путей. Исследования, проведенные ВНИИЖТом и НИИЖТом (ПГУПСом) показали, что для обеспечения стабильности зоны соединительных путей стрелочного перевода необходимо применение раздельных скреплений. Специальные раздельные скрепления для стрелочных переводов (без подуклонки) поставляются в незначительном количестве, поэтому, используя опыт путейцев, были разработаны предложения по применению в зоне соединительных путей раздельных скреплений, укладываемых в путь на перегонах.
Как показывает зарубежный опыт наилучшие результаты дают упругие скрепления типа «Фосло» или «Пендрол» /116, 146/.
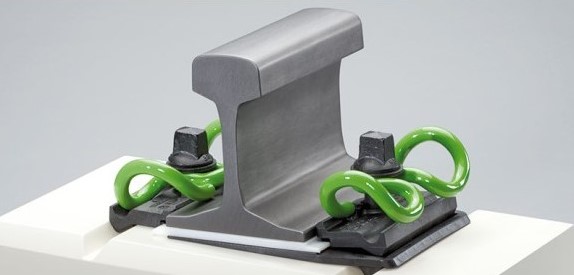
Скрепление Vossoloh
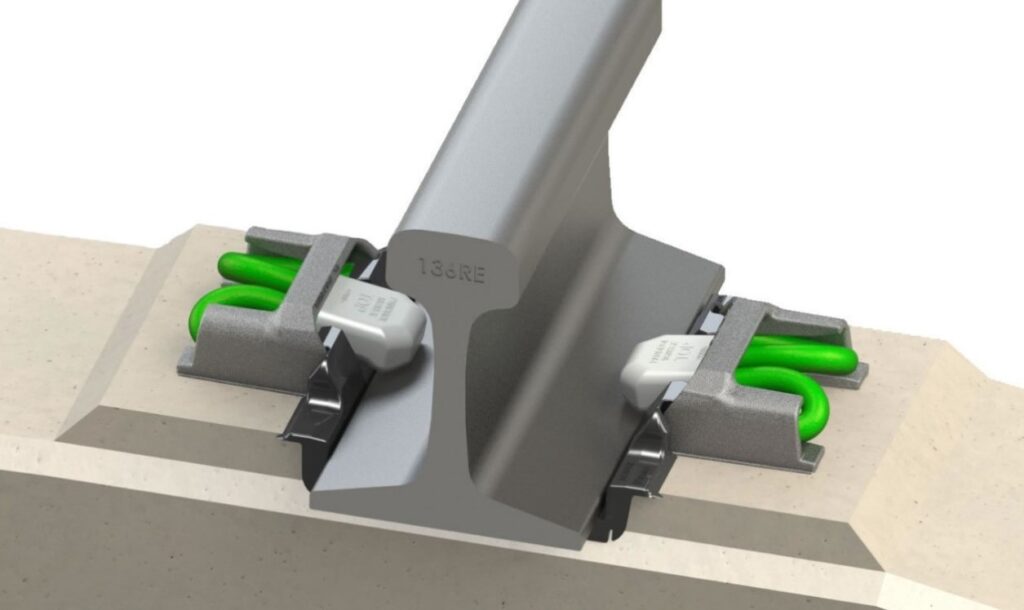
Скрепление Pandrol
Применение раздельных упругих скреплений в зоне соединительных путей позволяет улучшить работу переводной кривой /26/, однако для оптимального решения вопросов, связанных с надежностью, устойчивостью и стабильностью этой части стрелочного перевода применительно к российским условиям эксплуатации необходимо проведение дальнейших исследований и проектных разработок. В первую очередь это относится к укреплению упорной нити переводной кривой стрелочных переводов, работающих в условиях повышенного бокового воздействия.
Наименее долговечными из крупных элементов верхнего строения пути являются крестовины. Проблемы совершенствования крестовинных узлов и улучшения их эксплуатационных качеств имеет важнейшее значение.
Один из путей решения этой проблемы — разработка принципиально новых конструкций крестовинных узлов.
Необходимость разработки принципиально новых конструкций крестовин стрелочных переводов вызвана в первую очередь перспективой развития скоростного движения.
Наиболее перспективными для участков со скоростным движением являются стрелочные переводы, имеющие крестовины с непрерывной поверхностью катания. Проведенные за рубежом исследования /117, 140, 153, 58/ показали, что стрелочные переводы, имеющие такие крестовины, обеспечивают нормальную эксплуатационную работу при движении скоростных пассажирских поездов до 300-350 км/ч и более по прямому и до 220 км/ч по боковому направлениям.
В России разработана серия различных стрелочных переводов типа Р65 с непрерывной поверхностью катания /90, 92/, ведутся исследования, направленные на их дальнейшее совершенствование /3, 7,36,94,99, 119/.
Стрелочные переводы с непрерывной поверхностью катания могут иметь крестовины с гибким подвижным /93/, с поворотным и комбинированные с гибко-поворотным сердечником /4/. Переводы с подвижным сердечником обеспечивают движение скоростных пассажирских поездов со скоростью до 200 км/ч /129/. Проведенные ВНИИЖТом и ЛИИЖТом (ПГУПСом) испытания показали, что по этим переводам могут реализовываться и большие скорости движения.
Стрелочные переводы, имеющие крестовины с поворотным сердечником, укладываются на направлениях, на которых планируется повышение скоростей движения пассажирских поездов до 140-160 км/ч. Конструкции этих переводов имеют основные размеры, позволяющие укладывать их взамен обычных стрелочных переводов, что значительно облегчает их укладку на дорогах. Опыт эксплуатации этих переводов и экспериментальные работы по исследованию динамико-прочностных и эксплуатационных качеств стрелочных переводов с жесткими крестовинами и с крестовинами с поворотным сердечником /19, 68, 87,? 88, 94/, позволили рекомендовать использование таких конструкций не только для скоростных участков, но и для грузонапряженных участков с обращением подвижного состава с высокими осевыми нагрузками.
Повышение скоростей движения по прямому направлению свыше 160 км/ч требует применения более длинных сердечников и более жесткого закрепления их корневой зоны. Хорошие результаты в этом случае можно получить применяя гибко-поворотные сердечники, которые имеют по прямому направлению все преимущества гибких сердечников и в то же время за счет короткой (поворотной) ветви на боковом направлении могут быть уложены в обычные съезды.
В настоящее время т кая крестовина выпущена Муромским стрелочным заводом и проходит испытания на Октябрьской ж.д. Положительные результаты этих испытаний позволили включить такую крестовину в конструкцию скоростного стрелочного перевода на железобетонных брусьях для Октябрьской ж.д.
Первые конструкции крестовин с непрерывной поверхностью катания имели у совики, изготавливавшиеся в виде единой отливки из высокомарганцовистой стали, однако опыт эксплуатации таких переводов показал, что применение высокомарганцовистой стали в крестовинах с непрерывной поверхностью катания нецелесообразно, так как интенсивность их износа не превышает интенсивности износа зоны стрелки.
Литые усовики были сложны в изготовлении и поражались при изготовлении и в эксплуатации дефектами в виде трещин /87/. Поэтому в современных конструкциях крестовин с непрерывной поверхностью катания вместо литых усовиков используются усовики, изготовленные из специального проката.
Основными направлениями совершенствования крестовин с непрерывной поверхностью катания, по которым ведутся разработки в настоящее время, являются работы по оптимизации длины сердечника крестовины, улучшение прокатных усовиковых спецпрофилей, узлов крепления корневой зоны сердечника, а также механизма перевода и фиксации сердечника.
Важным преимуществом крестовин с непрерывной поверхностью катания являются их высокая износостойкость, значительно превышающая » износостойкость жестких крестовин, однако при определении целесообразности их использования в конкретных случаях необходимо учитывать, что цена их значительно превышает цену жестких крестовин, а их установка в путь требует реконструкции системы СЦБ станций. Не решена полностью также проблема очистки таких крестовин от снега, требует усовершенствования система фиксации и контроля взаимного положения сердечника и усовиков.
Работы по решению этих проблем в настоящее время ведутся, однако на обозримую перспективу определять влияние стрелочного хозяйства на перевозочный процесс на дорогах МПС будут переводы, имеющие крестовинные узлы с жесткими крестовинами.
Аналогичная перспектива сохраняется и на зарубежных дорогах. Обобщая анализ состояния и перспективы развития стрелочных переводов на зарубежных дорогах /46, 58, 141-143, 145, 148, 150, 155, 156/, можно сказать, что тенденция преобладающего использования крестовин с неподвижными элементами в том числе и в новейших конструкциях стрелочных переводов массового производства, сохранится на перспективу на дорогах бывших социалистических стран, США, Англии, Франции, ФРГ и других стран мира, имеющих железнодорожную сеть.
Среди различных конструкций крестовин с неподвижными элементами, используемых на дорогах России и за рубежом, наибольшее распространение имеют крестовины типа единой отливки сердечника с наиболее изнашиваемой частью усовиков и цельнолитые крестовины.
Цельнолитые крестовины не требуют сложной механической обработки. При их изготовлении отсутствуют операции сборки и подгонки. Монолитность конструкции позволяет проектировать крестовины с пониженной металлоемкостью.
Недостатки цельнолитых крестовин определяются трудностью получения литого металла с высокими прочностными характеристиками, дефицитность сырья для высокомарганцовистой стали. Из-за недостаточного качества литья в эксплуатации у цельнолитых крестовин в зонах возникновения больших изгибных напряжений развиваются усталостные трещины, что приводит к их быстрому выходу из строя, особенно под воздействием подвижного состава с высокими осевыми нагрузками.
Работы по совершенствованию цельнолитых крестовин проводились в 80-е годы специалистами ДИИТа и ЛИИЖТа /10,11, 34/.
Основное направление этих работ — создание облегченных крестовин.
Крестовины типа общей отливки сердечника с наиболее изнашиваемой частью усовиков позволяют сочетать высокую износостойкость литой высокомарганцовистой части с высокой изгибной усталостной прочностью рельсовых усовиков. Это преимущество определяет их широкое распространение, как у нас в стране так и за рубежом.
На дорогах МПС РФ доля крестовин этой конструкции превышает 95%. Конструктивным недостатком этой конструкции крестовины является необходимость стыкования хвостовой части литого сердечника с прилегающими рельсами. Недостаточная изгибная прочность металла в этой части крестовины приводит к возникновению в эксплуатации трещин, требующих замены всей крестовины.
В целях устранения этого недостатка ВНИИЖТом, ПТКБ ЦП и стрелочными заводами были разработаны варианты усиления хвостовой части сердечников крестовин различных типов. Испытания опытных партий показали, что лучшие из них позволяют снижать отказы крестовин по этому дефекту в два и более раз. В настоящее время- крестовины с усиленной хвостовой частью выпускаются серийно, однако полностью этот вопрос пока не решен.
Радикальным конструктивным решением, позволяющим устранить изломы хвостовой части крестовин, является Замена в этой зоне литого металла на рельсовые окончания. Технология соединения рельсовых окончаний с высокомарганцовистыми сердечниками освоена на ряде зарубежных фирм.
В России работы по созданию конструкции и технологии для крестовин с приварными рельсовыми окончаниями ведутся весьма интенсивно. При этом наметилось два направления — создание собственной технологии /111/ и кооперация с зарубежными фирмами по производству сварных крестовин.
Долговечность крестовин определяется, в основном, их сопротивлением износу и контактной усталости в зоне перекатывания колес с сердечника на у совик, поэтому наибольшее число работ в области совершенствования крестовин посвящено вопросам износостойкости и дефектостойкости крестовин.
На работу крестовин в пути влияют геометрические характеристики колес, конструктивные и геометрические особенности крестовин, размеры колеи и желобов крестовинного узла в целом, начальные свойства металла, упругие свойства элементов пути, условия эксплуатации и текущее содержание стрелочного перевода. Исследование влияния каждого из названных факторов на работу крестовин представляет самостоятельную задачу. Из этих задач в настоящее время в наибольшей степени исследовано влияние условий эксплуатации/1, 6, 9,85, 107, 110, 121, 123, 151/, а также размеров колеи и желобов /43,44, 47,49/.
Одним из направлений исследований по улучшению эксплуатационных качеств крестовин является совершенствование свойств металла (стали 110Г13Л) /80, 81/. Проводятся работы по улучшению технологии литья, совершенствованию химического состава стали /55, 81, 130/, местному легированию изнашиваемых зон, совершенствованию ее структуры /38, 41, 42/, до эксплуатационному упрочнению взрывом и накаткой роликом /16, 18/. На Муромском стрелочном заводе начаты работы по упрочнению сердечников крестовин методом высокотемпературного газостатирования /12-17,72/. ^
Наибольшие успехи в этом направлении достигнуты за счет упрочнения наиболее изнашиваемой части отливки крестовины энергией взрыва, которое позволяет увеличить наработку крестовин до отказа по износу в 1,2-1,4 раза. При улучшении качества литья эффект упрочнения может быть значительно выше.
В связи с этим целесообразно исследовать комбинированный метод, включающий в себя газостатирование сердечников и последующее упрочнение их рабочих поверхностей взрывом.
Разработки по совершенствованию технологии упрочнения крестовин энергией взрыва продолжаются. Испытываются различные варианты взрывчатых веществ, проводятся опыты по упрочнению крестовин на различных подстилающих слоях, под водой и ряд других исследований и разработок.
Эффективное влияние на износостойкость и дефектостойкость крестовин можно осуществить изменяя форму рабочих поверхностей, от которой зависит уровень динамических воздействий колес на нее.
Исследователями были предложены различные проектные и ремонтные формы рабочих поверхностей крестовин. Работы в этом направлении продолжаются. Они существенным образом зависят от технологических возможностей заводов и фирм-изготовителей.
Наибольшее распространение на сети дорог получил ремонт крестовин методом восстановления рабочих поверхностей наплавкой в пути, однако в последние годы все больше внимания уделяется разработке и совершенствованию методов ремонта на специализированных предприятиях — наплавка и фрезеровка в специализированных стационарных цехах и наплавка в дорожных пунктах. Существенным преимуществом этих методов является сокращение задержек поездов при восстановлении или замене крестовин.
Крестовина является частью крестовинного узла, поэтому ее работа зависит от работы других его элементов. В состав крестовиных узлов с жесткими крестовинами входят контррельсы.
Первоначально контррельсы изготавливались из обычных рельсов /139/. Однако практика эксплуатации в нашей стране и за рубежом показала целесообразность перехода на контррельсы, изготовленные из специальных прокатных спецпрофилей /5, 101, 149, 152/.
За рубежом распространение получили контррельсовые узлы с контррельсами, не связанными с ходовыми рельсами. Такая конструкция удобна в эксплуатации и позволяет легко регулировать желоба узла.
Ходовой рельс в таком узле является обыкновенным рельсом и может заменяться отдельно, без разборки всего узла. Работы над отработкой таких конструкций для российских ж.д. в настоящее время интенсивно ведутся.
Обобщая анализ выполненных и планируемых исследований и разработок по улучшению конструкции и эксплуатационных качеств стрелочных переводов, следует отметить, что их общим недостатком является недостаточная связь работ по созданию и совершенствованию конструкций стрелочных переводов с работами по совершенствованию технологии их изготовления и поиску новых технологических схем изготовления важнейших элементов перевода. В результате внедрение разработок задерживается, а некоторые из них так и остаются нереализованными.
Цели и задачи исследования
Цель диссертационной работы заключается в том, чтобы опираясь на анализ и обобщение опыта разработок и освоения производства стрелочной продукции выработать основные перспективные направления для дальнейших работ по созданию и отбору прогрессивных технологий для конкурентоспособных стрелочных переводов нового поколения с высокими эксплуатационными качествами.
Схема работ по совершенствованию стрелочных переводов представлена на рис. 1.1. Как видно из схемы, цель может быть достигнута за счет комплексного использования возможностей совершенствования конструкции, технологии, создания новых технологических схем, совершенствования материалов, применяемых для изготовления стрелочных переводов. Все эти составляющие должны быть рассмотрены во взаимосвязи.
Решение задач по созданию высоконадежных и экономичных стрелочных переводов должно основываться на опыте эксплуатационной работы стрелочного хозяйства железных дорог МПС России и в первую очередь на анализе причин отказов стрелочных переводов и их основных элементов. Этому посвящена следующая глава работы.
Анализ причин отказов стрелочных переводов и их элементов
Стрелочные переводы изымаются из пути по различным причинам.
Наиболее распространенной причиной изъятия стрелочных переводов из пути является отказ их основных элементов по износу. В данном случае под отказом понимается состояние (износ) основных элементов, не позволяющее обеспечить заданные условия эксплуатационной работы, или нарушающие условия безопасности движения поездов по стрелочному переводу.
Как правило, по износу стрелочные переводы изымают из пути в случае, если большой износ имеют одновременно несколько основных элементов перевода (стрелка, крестовина и т.д.).
Другой причиной изъятия стрелочных переводов из пути по износу их элементов является так называемое «изъятие по причине общего расстройства конструкции». Эти случаи характерны тем, что несмотря на то, что износ отдельных основных элементов еще не достиг предельных величин, однако износ элементов в их сопряжениях и стыках, а также износ подрельсового основания и промежуточных скреплений уже не позволяет эксплуатировать перевод в первую очередь содержать колею в пределах норм, установленных ПТЭ и инструктивными документами.
Часть стрелочных переводов изымается из пути по дефектам /30, 53, 59, 84/. Также, как и в случае отказа по износу, отказ стрелочного перевода по дефектам определяется отказом нескольких его основных элементов. Под отказом в этом случае понимается состояние элементов, нарушающее условия безопасности движения поездов по стрелочному переводу, или требующее введения ограничений скоростей их движения.
Кроме уже названных причин изъятия стрелочных переводов, часть переводов изымается из пути при капитальном ремонте, или сплошной смене металлических частей на участках пути, заключающих эти стрелочные переводы. Такое изъятие не определяется отказами стрелочных переводов и изъятые из пути переводы, или их основные элементы, могут с успехом быть использованы повторно, а также переложены на малодеятельные линии.
Из приведенного вышь анализа видно, что отказы стрелочных переводов возникают по причине отказов их основных элементов, или по причинам расстройства сопряжений и прикрепителей. Отказы основных элементов происходят либо по износу, либо по дефектам. Рассмотрим отказы основных элементов стрелочных переводов более подробно. Официальной статистики по выходу основных элементов стрелочных переводов не ведется, поэтому анализ отказов основных элементов стрелочных переводов выполнен с использованием данных путеобследовательских станций (совместные наблюдения с ОАО МСЗ) и данных Стрелочной лаборатории ВНИИЖТа, большой вклад в организацию сбора которых внес инженер М.И.Титаренко.
Отказы элементов стрелки
Основными элементами стрелки являются остряки и рамные рельсы. На рис. 2.1 показана зависимость изъятия стрелок типа Р65 от наработки в главных и приемоотправочных путях, построенная по данным, полученным с дорог ВНИИЖТом и путеобследовательскими станциями Департамента пути и сооружений МПС.

Как видно из рис.2.1, зависимость отказов стрелок от наработки имеет сложный вид. На момент нормативной наработки в порядке одиночной замены изымается 43,5% стрелок типа Р65.
Наиболее распространенная причина изъятия стрелок связана с состоянием остряков.
Для анализа характера зависимости отказов остряков от наработки построим, воспользовавшись данными, приведенными на рис. 2.1, зависимость, где: N — приращение числа отказов за период наработки А Т.
По определению величина р0 представляет собой удельную частость отказов остряков в период эксплуатации АТ= Тг — Ть
Зависимость р0(Т) представлена на рис. 2.2.
Анализируя представленные на рис. 2.2 данные можно отметить, что за время эксплуатации остряков имеют место три четко выраженных периода.
В начальный период эксплуатации удельная частость отказов остряков возрастает и к моменту пропуска порядка 250 млн.т брутто груза достигает 1,8% на каждые 10 млн.т бр. пропущенного груза.
Такой вид зависимости р0(Т) характерен для преобладающего механизма отказов элементов по дефектам усталостного и контактно- усталостного характера, когда по мере наработки элементы вырабатывают свой ресурс и выходят из строя /52/.
Затем до момента пропуска приблизительно 450 млн. т бр. груза удельная частость отказов остается практически неизменной — около 1,8% на каждые 10 млн.т бр. наработки.
Такому виду зависимости удельной частости отказов от наработки соответствует период равновесия между механизмами износа и дефектообразования. Развивающиеся на небольшой глубине дефекты наиболее нагруженной контактной зоны головки остряков удаляются за счет износа, работа элементов стабилизируется /57/.
В последний период эксплуатации удельная частость отказов снижается. В частности в период наработки 450-500 млн. т бр. груза она уже составляет около 1,5% на 10 млн. т бр.
Эта особенность характера для периода, когда преобладающими механизмами, формирующими отказы элементов становятся износ и образование дефектов специфического характера (местный износ подошвы и головки, расстройства корневой зоны и т.д.).
Помимо удельной частости отказов Р0(Т) важным показателем работы элементов является интенсивность их отказов — г|(Т). В соответствии с теорией надежности интенсивность отказов определяется по формуле /52/, где: Я(Т) — вероятность безотказной работы элемента.
Если удельная частость отказов характеризует выход элементов относительно их первоначального числа, то интенсивность отказов характеризует в каждый данный момент наработки Т выход элементов оставшихся в эксплуатации к этому моменту на ближайший период сГГ. Это позволяет планировать их замену и периодичность обслуживания. ;
На рис. 2.3. показана построенная с помощью данных, приведенных на рис.2.1 зависимость интенсивности отказов от наработки. Интенсивность отказов нарастает за весь период работы остряков в пути. Вид зависимости г|(Т) — пунктирная линия, свидетельствует о логарифмически нормальном характере этой зависимости /52/, однако в основной период работы остряков, как легко видеть из рис. 2.3, зависимость интенсивности отказов остряков от наработки с достаточной для практической цели точностью можно считать линейной.
Характерно, что завершение «линейного периода» интенсивности отказов совпадает с завершением периода относительного постоянства частоты отказов, что также свидетельствует о смене ведущего механизма отказов к моменту наработки 430-450 млн.т бр.
Эти обстоятельства необходимо учитывать при назначении нормативных сроков служб л стрелок и планировании текущего содержания стрелочных переводов.
Для разработки мероприятий по повышению эксплуатационных качеств остряков важное значение имеет анализ их отказов по конкретным группам дефектов. Такой анализ можно провести воспользовавшись данными, приведенными на рис. 2.4, представляющими из себя обобщение наблюдений путеобследовательских станций ЦП МПС с использованием материалов, собранных с дорог инженерами Стрелочной лаборатории ВНИИЖТа М.И.Титаренко и В.Г.Донцом.
Диаграмма распределения отказов остряков типа Р65 на главных и приемо-отправочных путях по группам дефектов
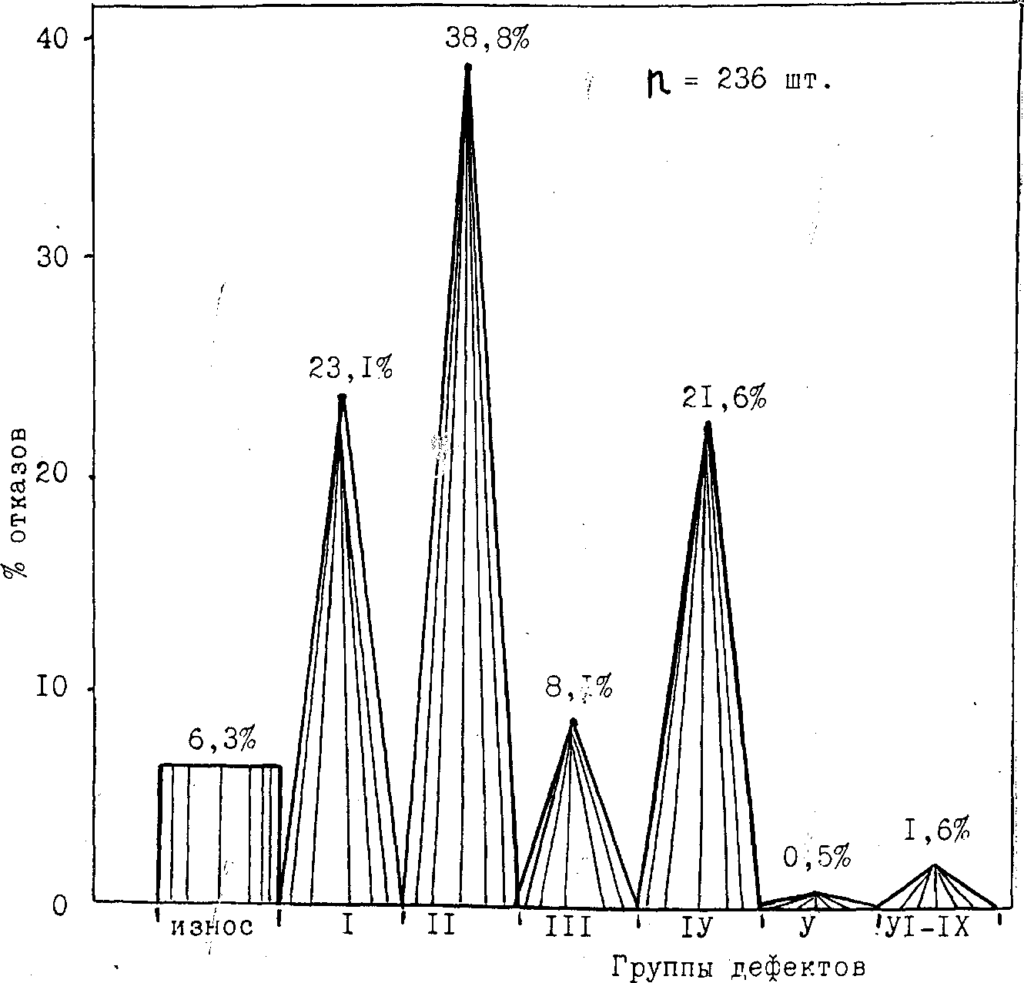
На диаграмме, представленной на рис.2.4, приведено распределение отказов остряков по группам дефектов в соответствии с действующей классификацией.
Из представленных данных (см. рис. 2.4) следует, что около 94% всех остряков, изъятых из главных и приемо-отправочных путей, вышло из строя по различного рода дефектам.
Наибольшее число остряков вышло из строя по дефектам П группы — 38%. При этом 6,3% остряков вышло по характерному для стрелочных переводов дефекту ДО.20.2 — трещины в головке остряка и изломы из-за них в зоне выпрессовки. остальные 32,5% остряков получило отказ по общему для рельсов и рельсовых элементов дефекту 21.2.
На втором месте по числу причин отказов остряков находятся дефекты I группы. По этим дефектам отказ получают 23,1% остряков. Характерным для стрелочных переводов дефектом этой группы является дефект ДОЛ 1.2 — выкрашивание гребнеобразного наплыва в зоне боковой строжки остряка. Отказы по этому дефекту составляют 9,7%. Еще 0,8% остряков выходят по другому характерному дефекту ДО. 14.2. остальные 12,6% остряков получило отказ /по общим с рельсами дефектам 10; 11; 14; 17.
Далее по числу причин отказов остряков расположены дефекты IV группы. Из этой группы характерны для стрелочных переводов дефекты ДО.41.2 и ДО.42.2, представляющие собой седловины соответственно ь зоне выпрессовки корня и в зоне до сечения остряка 50 мм. По этим дефектам отказы получают 5,4% остряков. Остальные остряки этой группы — 16,2% выходят из строя по общим дефектам 41-го рисунка.
Остряки, получившие отказы по дефектам Ш группы, получили отказ по общему с рельсами и другими рельсовыми элементами рисунку ЗОГ, связанному с наличием неметаллических включений в металле головки элемента. Их доля в общей статистике отказов составила 8,1%; 1,6% остряков получило отказ по характерному для стрелочных переводов дефекту ДО.80 — неприлегание к равному рельсу и подушкам подкладок.
Обобщая приведенные выше данные можно отметить, что по специфичным для стрелочных переводов дефектам отказы получает около 22% остряков, однако необходимо иметь в виду, что значительная часть остальные дефектов (в первую очередь дефектов I, П и Ш групп) также связано со спецификой работы и изготовления остряков.
Эта специфика объясняется повышенным уровнем вертикальной и горизонтальной динамики системы экипаж — путь в зоне стрелки, особенностью прокатки остряковых спецпрофилей и технологии изготовления из них остряков.
В целом не менее 65% остряков изымается из пути по причинам недостаточной прочности и технологии изготовления.
Основная причина отказов рамных рельсов — характерные для стрелочных переводов дефекты I и П группы ДР. 11.2 и ДР.21.2 и аналогичные им общие с рельсами дефекты рисунков 11 и 21. Оба вида дефектов связаны с недостаточной контактно-усталостной прочностью рамных рельсов.
Отказы элементов крестовинного узла
В настоящее время на железных дорогах России эксплуатируются крестовинные узлы двух видов — с -непрерывной поверхностью катания и с крестовинами с неподвижными элементами (в основном общей отливки сердечника с наиболее изнашиваемой частью усовиков).
Крестовины с непрерывной поверхностью катания
Характер работы крестовин с непрерывной поверхностью катания близок по характер)’ оабогы зоны стрелки.
Срок службы крестовин с непрерывной поверхностью катания также близок к сроку службы стрелки. Нормативный срок службы для них установлен 320 млн. т бр., однако средняя фактическая наработка до изъятия их из пути превышает 400 млн. т бр.
Основные причины отказов этих крестовин — выкрашивания на поверхностях катания усовиков и сердечников в зоне перекатывания ДУН. 14.2, ДСН.14.2. По этим причинам изымается из пути основная масса крестовин с непрерывной поверхностью катания.
Помимо этих причин наблюдается три вида дефектов, специфичных для крестовин с непрерывной поверхностью катания, которые служат причиной их выхода из строя.
Наиболее опасным этих дефектов является поперечный излом усовика из-за усталостного дефекта, возникающего и развивающегося в подошве в зоне ее обработки напротив острия сердечника (ДУН.65.2). Излом опасен тем, что возникает под колесами проходящего поезда. К настоящему времени известно 2 случая возникновения таких дефектов (один из них на Экспериментальном кольце ВНИИЖТа).
Другой дефект, приводящий к отказу крестовин с непрерывной поверхностью катания, заключается в расстройстве заклепочных соединений подушек, на которые опирается поворотный сердечник. В результате расстройства соединения под действием вибраций заклепки приподнимаются и не дают возможности сердечнику перемещаться по подушкам. Крестовину приходится изымать из пути, или искать способы закрепления заклепок непосредственно в пути (надежных способов пока не разработано).
Еще один дефект, выводящий из строя крестовин с непрерывной поверхностью катания — местные выработки подошвы сердечника и подушек, как правило, вблизи острия сердечника из-за высокого уровня сил, передаваемых колесами на узкие сечения сердечников — ДСН.61.2. При значительных величинах выработок приходится изымать крестовины из пути, или существенно ограничиь.ать скорости движения поездов по ним.
Помимо перечисленных дефектов имеют место также отказы крестовин с непрерывной поверхностью катания из-за дефекта переводного механизма. Наиболее опасными из них являются изломы рабочих тяг. Опасность этого дефекта усугубляется отсутствием замыкателей, фиксирующих положение сердечника относительно усовиков.
Относительно высокая стоимость и сложность эксплуатации крестовин с непрерывной поверхностью катания ограничивает область их применения на дорогах.
Крестовины с неподвижными элементами
Самой распространенной конструкцией крестовин на железных дорогах России является крестовина типа общей отливки сердечника с наиболее изнашиваемой частью усовиков. Доля таких крестовин превышает в настоящее время 95%.
Из всех крупных элементов верхнего строения пути такие крестовины имеют наименьший срок службы.
На рис.2.5. представлена зависимость выхода из строя крестовин типа Р65 марки 1/11 (самый распространенный вид крестовин) в зависимости от наработки. Зависимость имеет монотонно возрастающий характер. Данные, приведенные на рис. 2.5 относятся к эксплуатации крестовин производства Муромского стрелочного завода на дорогах европейской части России и получены путеобследовательскими станциями и ВНИИЖТом.
На момент нормативной наработки, как видно из зависимости, приведенной на рис.2.5, выходит из строя 33% крестовин.
Для более подробного анализа данных о выходе из строя крестовин на рис. 2.6 с помощью формулы (2.1) построена зависимость удельной частости отказов крестовин от наработки.
В отличие от аналогичной зависимости для остряков (см. рис. 2.2) удельная частость отказов крестовин возрастает в течение всего периода их эксплуатации. К моменту нормативной наработки она возрастает в 5,5 раз по сравнению с начальной и продолжает расти.
Такой характер зависимости удельной частости отказов от наработки свидетельствует о том, что ведущим процессом должен являться процесс накопления повреждений в металле /61, 82/. В случае крестовин это связано с тем, что под износом крестовин следует понимать сложный процесс, который сопровождается большими пластическими деформациями (до 40% от нормативных значений износа) и поверхностными контактными повреждениями /23,27,62/.
Зависимость интенсивности отказов крестовин от наработки построенная по (2.2) и представленная на рис.2.7 имеет монотонно возрастающий вид. Характер зависимости близок к
экспоненциальному, что также резко отличает его от аналогичной зависимости для остряков (см. рис. 2.3). Как правило, близкая к экспоненциальной зависимость интенсивности отказов от наработки возникает в случаях, когда по мере работы элементов нагрузка на них возрастает /52/. Для крестовин это подтверждается теоретическими и экспериментальными исследованиями, выполнявшимися во ВНИИЖТе и ЛИИЖТЕ (ПГУПСе) и других исследовательских организациях.
По исследованиям стрелочной лаборатории и научно- исследовательской лаборатории стрелочного хозяйства ЛИИЖТа динамические добавки контактных сил, действующих. на рабочие поверхности крестовин, в процессе работы крестовин в пути (по мере их износа) могут возрастать в 2-3 и более раз /21, 31, 35,134,136/.
Рассмотрим основные причины отказов крестовин с неподвижными элементами. На рис. 2.8 приведена диаграмма распределения отказов крестовин по видам дефектов.
Выход крестовин типа Р65 из главных и приемо-отправочных путей в зависимости от наработки (нарастающим итогом)
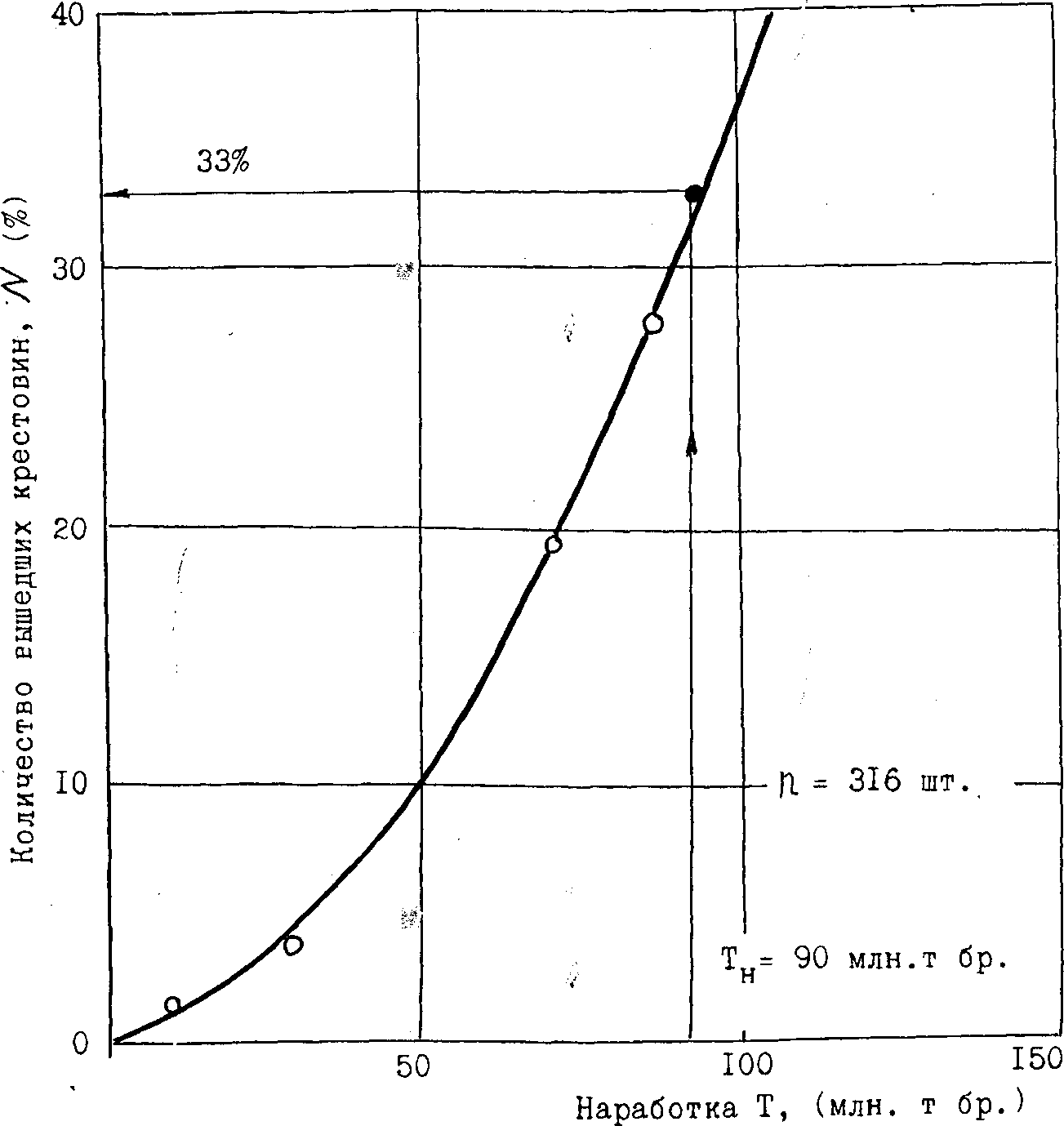
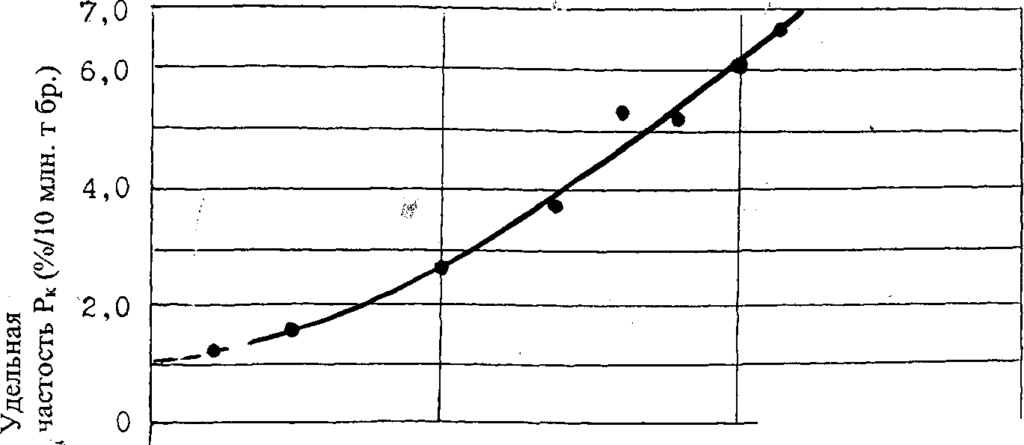
Необходимо отметить, что процентные отношения, приведенные на рис. 2.8 для крестовин, в отличие от аналогичных соотношений для других элементов стрелочных переводов, подвержены значительным колебаниям в зависимости от времени выпуска крестовин и условий, в которых они эксплуатируются. Причины этого заключаются в ряде факторов экономического и технологического характера, а также общих недостатках конструкции крестовин, которые будут рассмотрены ниже.
Соотношения, представленные на рис. 2.8 в качестве примера являются обобщением данных, полученных путеобследовательскими станциями ЦП МПС и ВНИИЖТом на дорогах центральной части России, Уральского и Сибирского регионов для крестовин выпуска 1990- 1992 г.г.
Диаграмма распределения отказов крестовин Р65 на главных и приемо- отправочных путях по видам дефектов (1990- 1992 г.г. выпуска)
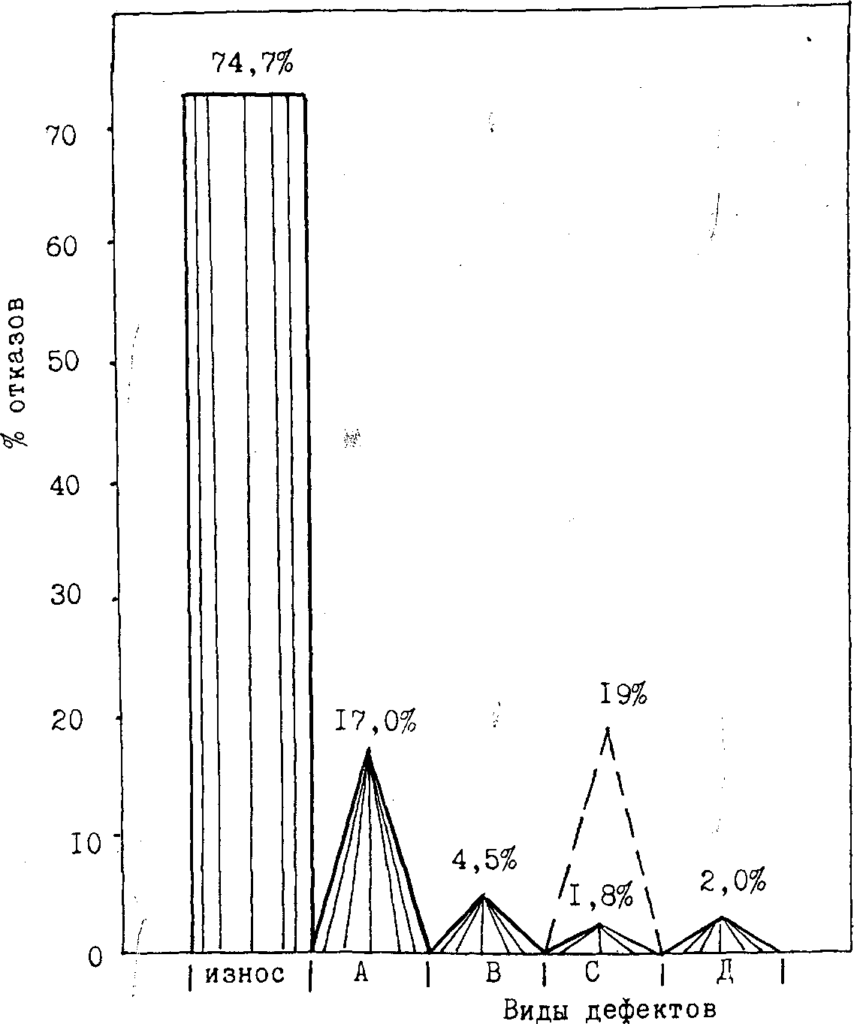
А — дефекты зоны перекатывания В — дефекты хвостовой части С — дефекты сопряжения литой и рельсовой частей Д — прочие виды дефектов
Наиболее частой причиной отказов крестовин является износ. По причине износа отказы получает большая часть крестовин — 6080%.
Как уже указывалось, «износ» крестовин представляет из себя сложный процесс. Схематическая зависимость «износа» крестовин от наработки представлена на рис. 2.9. Если под «износом» крестовины понимать регламентируемое нормативно-технической документацией изменение положения рабочих поверхностей крестовины относительно базы измерений, то крестовина в своей работе в пути проходит три ярко выраженные стадии.
Первоначальная стадия (ее при хорошо подогнанных литой и рельсовой частях крестовины может не быть) это осадка литой части относительно рельсовых усовиков. Осадка происходит в основном под первыми же проходящими поездами. Обычно величина осадки в зоне перекатывания Ъ0 колеблется от 0,5 до 1,5 мм. В отдельных случаях она может достигать 2 мм и даже более /29/.
Вторая стадия работы крестовины — период интенсивного наклепа металла. Под действием больших динамических контактных сил металл рабочих поверхностей сминается. За счет пластической деформации высокомарганцовистой стали возникает поверхностный слой уплотненного металла с твердостью на поверхности до 400 НВ единиц и более. Эта стадия длится до наработки 15-20 млн. т бр. Зависимость износа от наработки в этот период, как показали исследования ВНИИЖТа имеет экспоненциальный характер.
Ведущий процесс формирования износа пластическая деформация. Величина износа в нормируемых сечениях к концу периода наклепа-смятия Ьсм достигает 1,5-2,5 мм, иногда до 3,0 мм /37/.
Период наклепа в работе крестовины является определяющим. Если к его окончанию твердость рабочих поверхностей мала, то Зависимость износа крестовины от наработки дальнейший период характерен быстрым износом крестовины. Если же под действием слишком больших динамических сил рабочие поверхности имеют слишком большую твердость (перенаклеп), то при дальнейшей работе крестовины происходит образование выкрашиваний и других дефектов контактного и контактно- усталостного происхождения.
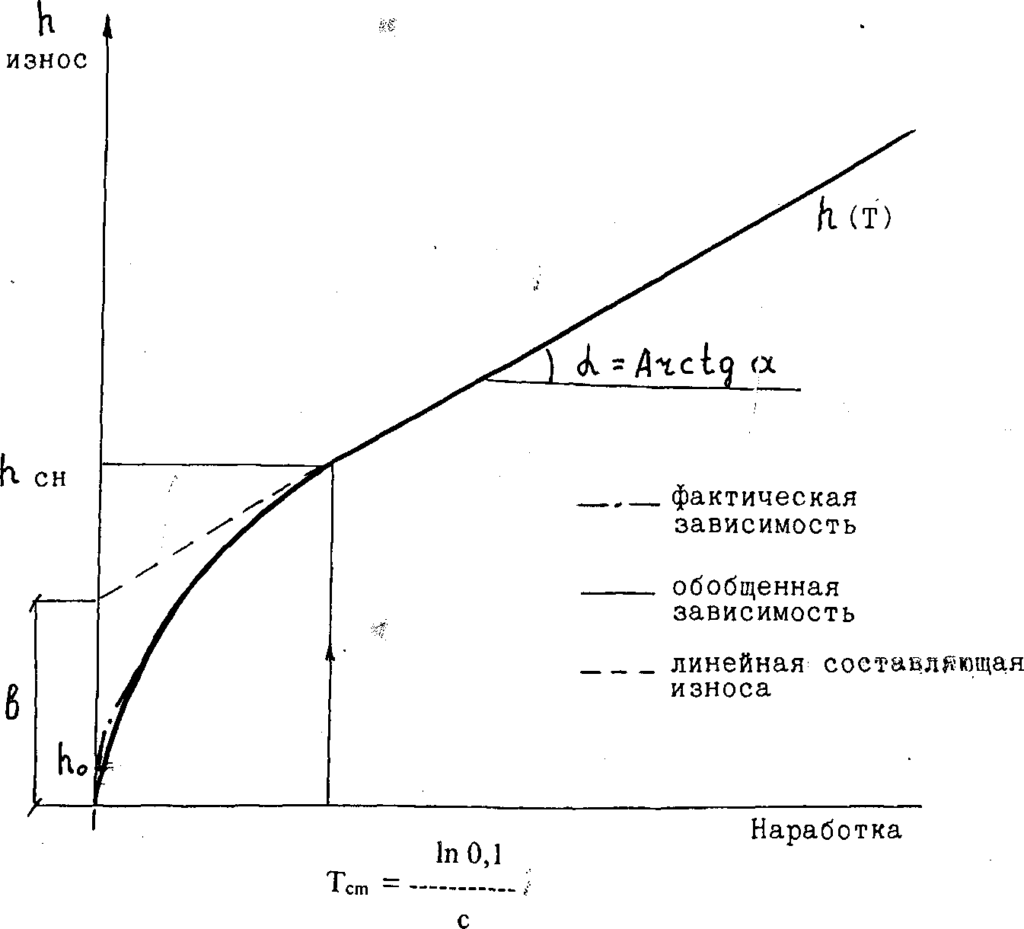
После завершения периода наклепа зависимость износа крестовин от наработки приобретает линейный или близкий к линейному вид.
Ведущими процессами, определяющими износ крестовин, являются истирание металла и образование поверхностных выкрашиваний /22, 86, 104/.
Выкрашивания на рабочих поверхностях крестовин могут быть причиной их отказов.
Выкрашивания на сердечниках и усовиках в зоне перекатывания (дефекты ДС и ДУ 14.2 и 13.2) составляют основную часть причин отказов крестовин, вышедших из строя по дефектам. Совместно с рядом других дефектов зоны перекатывания (ДУ.20.2, ДУ.30.2 и др.) число отказов крестовин по этой группе дефектов составляет около — 20%.
Вместе с тем необходимо отметить, что пэражаемость крестовин дефектами в виде выкрашиваний в зоне перекатывания значительно выше, чем число отказов по ним (см. рис. 2.10). особенно это характерно для крестовин с большим износом. Это объясняется тем, что с увеличением износа крестовин уклоны траекторий движения колес по ним резко возрастают, увеличивая нарастающими темпами уровень динамических сил, действующих на крестовину.
Другой зоной крестовины, подверженной образованию дефектов в виде выкрашиваний рабочих поверхностей, является зона передней врезки, дефект ДУЛ 2.2. Число отказов крестовин, отнесенных к этому дефекту, составляет около 2%, однако эта статистика не полностью отражает фактическое положение. В эксплуатации этим дефектом поражается значительное число крестовин, до 30-50% при больших износах крестовин (см. рис. 2.10).
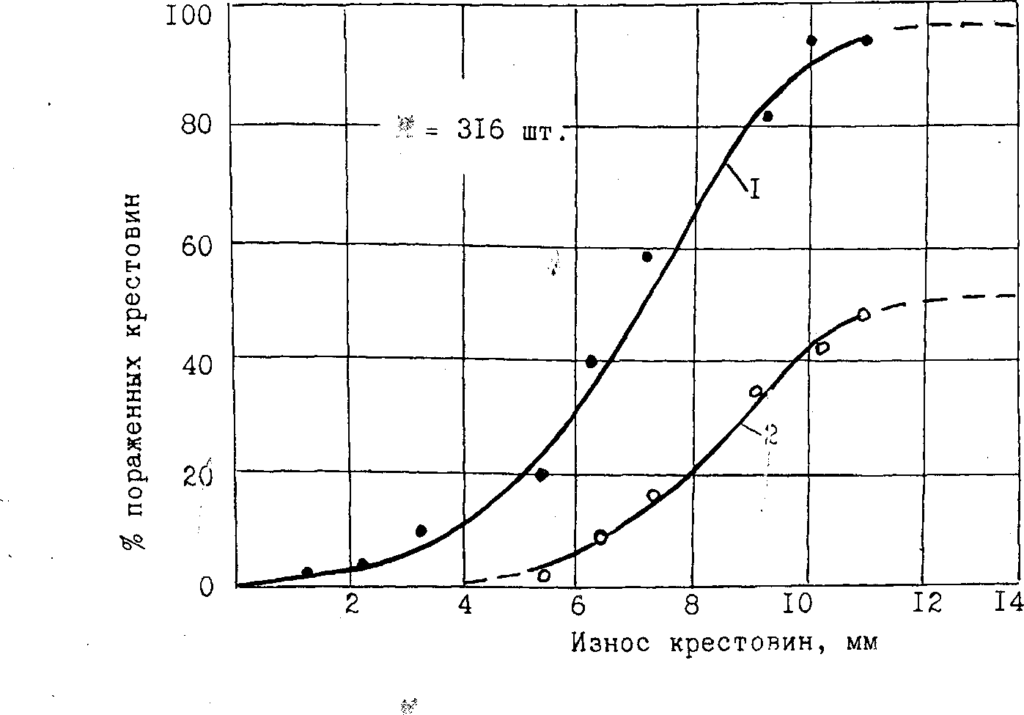
1. рабочие поверхности в зоне перекатывания, 2. зона врезки литой части в рельсовую
Дефекты в виде выкрашиваний литых и рельсовых усовиков в зоне передней врезки крестовин, как правило, возникают одновременно с дефектами в зоне перекаты ания. Получившие отказ по дефектам крестовины относятся в первую очередь к дефектам зоны перекатывания. Однако часть из них могла бы быть отнесена и к отказам по дефектам передней врезки. В отдельных случаях число таких крестовин может составлять около 20% от общего числа крестовин, получивших отказ.
Весьма опасный вид дефектов крестовин типа общей отливки сердечника с наиболее изнашиваемой частью усовиков — дефекты хвостовой части (ДС.50.1, ДС.60.1-2, ДС.63.1). В основном это трещины, возникающие в подошве и развивающиеся от дефектов литья или концентраторов напряжений, образующихся в процессе обработки литой части /114, 121, 122, 124, 131/. Такие дефекты угрожают безопасности движения поездов, так как могут приводить- к внезапным изломам хвостовой части сердечников, в том числе и непосредственно под проходящим поездом.
В крестовинах, ранее выпускаемых конструкций (часть из них еще находится в эксплуатации), таких отказов наблюдается до 7,5-8,0)% (см. рис. 2.11). Существенный вклад в усовершенствование конструкции хвостовой части крестовин внесен специалистами литейного производства стрелочных заводов, а также* инженерами В.Н.Ткаченко и М.И.Титаренко. В крестовинах усовершенствованной конструкции, выпускаемых 1 настоящее время, число отказов по этому виду дефектов снизилось до 4,5%.
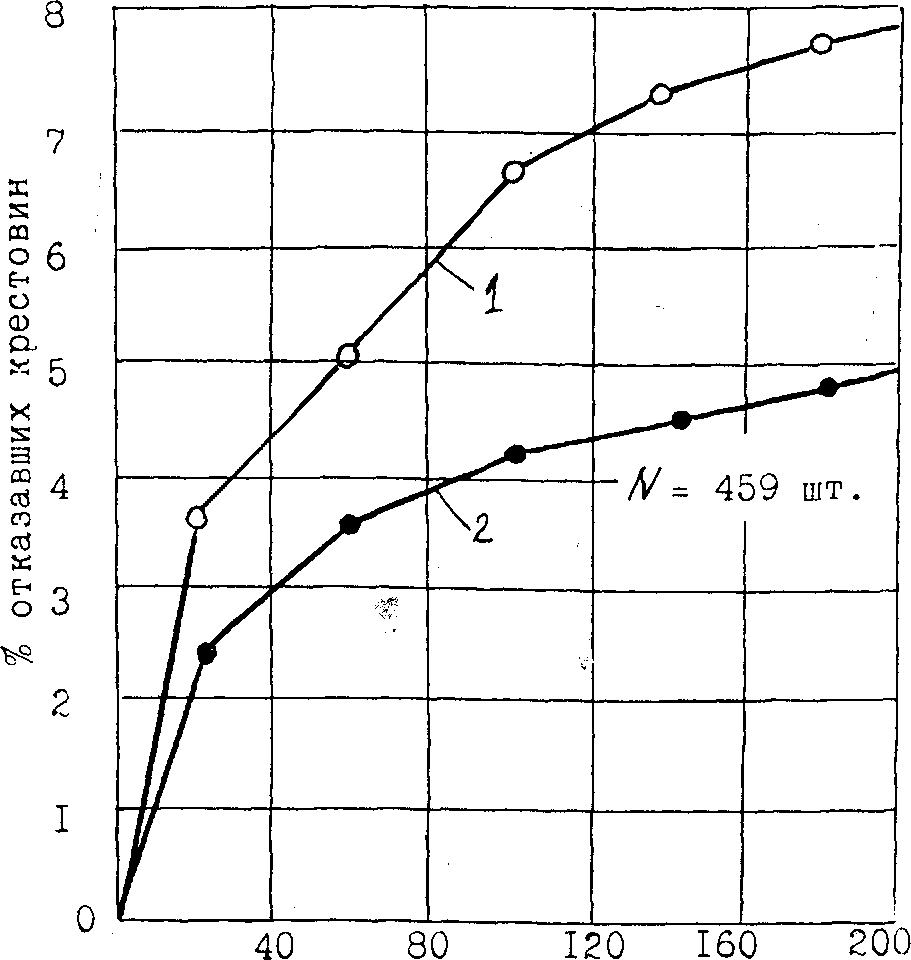
1. cтарая конструкция хвостовой части, 2. усовершенствованная конструкция хвостовой части
Полностью ликвидировать отказы крестовин по этому опасному виду дефектов для применяющегося варианта конструкции, несмотря на проделанную в последние годы работу, не представляется возможным. Необходимо радикальное изменение конструкции крестовины.
Контррельсовые узлы и ходовые рельсы при контррельсах
Безопасность движения поездов по крестовинным узлам обеспечивается за счет контррельсов, направляющих колесные пары подвижного состава при проходе вредного пространства на крестовинах с неподвижными элементами.
На дорогах России и всего бывшего СССР применяется практически единственный вид контррельсовых узлов. В качестве контррельса в таком узле используется прокатный cпец профиль, который с помощью болтов и вкладышей крепится к ходовому рельсу /101/. Специальные гибы спецпрофиля и вкладыши соответствующих габаритов обеспечивают заданные размеры желобов, а специальные упорки необходимую жесткость узла.
Наиболее часто встречающийся дефект таких контррельсовых узлов — разрыв контррельсовых болтов. В соответствии с действующей в настоящее время нормативно-технической документацией разрыв двух подряд болтов не допускает дальнейшую эксплуатацию стрелочного перевода до их замены.
Причиной разрыва контррельсовых болтов служит высокий уровень динамических сил, действующий на контррельсы при проходе колесных пар по крестовинному узлу. Исследования ВНИИЖТа показали, что напряжения в контррельсовых болтах от воздействия
подвижного состава могут превышать предел длительной выносливости для стали, из которой они изготовлены /60/.
Высокий уровень бокового динамического воздействия колес на контррельсы сопровождается также возникновением в наиболее нагруженных точках и сечениях спецпрофилей растягивающих и сдвиговых напряжений величиной до 330 МПа и более /24/, что значительно превышает наибольшие напряжения, допускаемый для рельсовых элементов.
В результате этого в эксплуатации в контррельсах могут возникать и развиваться дефекты, приводящие к их отказам.
На дорогах России имеют место три вида дефектов контррельсов, служащие причиной их отказов: дефект ДК.14.2 в виде продольных трещин головки контррельса (возникают в нижней части головки); дефект ДК.24.2 — поперечные трещины головки контррельса, развивающиеся от ее верхней кромки; дефект ДК.54.2 — трещины, развивающиеся от отверстий для крепления контррельса к ходовому рельсу.
Общий выход контррельсов по этим видам дефектов невелик. В результате внедрения новых оптимизированных спецпрофилей/101/ удалось свести его к величине менее одного процента, однако каждый такой отказ весьма опасен и представляет прямую угрозу безопасности движения поездов.
Направляющее действие контррельсов вызывает резкие сдвижки колесных пар при прохождении подвижньм составом крестовинных узлов. Это сказывается на работе ходовых рельсов при контррельсах. Дополнительные местные воздействия на ходовой рельс вызывают и динамические эффекты от прохода второго колеса колесной пары через зону перекатывания на крестовине (посредством колебаний в плоскости перпендикулярной оси пути).
В результате этого на ходовых рельсах образуются вертикальные неровности в виде седловин — дефект ДХ.44.2. Развиваясь седловины служат причиной отказов. Вместе с дефектами первой и второй групп, общей с рельсами классификации, седловины являются основной причиной изъятия ходовых рельсов из пути.
Замена ходового рельса при современной конструкции контррельсового узла требует его полной разборки, что не целесообразно выполнять непосредственно в пути, поэтому при выходе из строя ходового рельса, как правило, приходится заменять весь контррельсовый узел, что не целесообразно.
В настоящее время ведутся разработки контррельсовых узлов, позволяющих заменять ходовые рельсы без замены узла в целом.
Отказы рельсовых элементов соединительных путей и элементов скреплений
Выход рельсовых элементов соединительных путей происходит по причинам, аналогичным причинам, характерным для рельсов прямых и криволинейных участков обычного пути и укладывается в классификацию дефектов рельсов.
Частота и интенсивность отказов рельсовых элементов соединительных путей не превышает соответствующие данные для рельсов обычного пути такого же плана и профиля. Отсутствие подуклонки рельсовых нитей в пределах стрелочных переводов не вызывает образования специфических дефектов.
Анализ случаев браков и аварий на стрелочных переводах показывает, что около 2,5% всех случаев нарушения безопасности движения поездов относится к слабости подрельсового основания, а с учетом случаев нарушения норм содержания переводов, которые напрямую связаны с состоянием основания и скреплений, доля таких случаев в общей статистике нарушений безопасности движения поездов по стрелочным переводам превышает 36%.
Несовершенство конструкции и качества промежуточных скреплений на стрелочных переводах является одной из наиболее неблагоприятных особенностей современных конструкций, применяемых на российских железных дорогах. Особенно это проявляется в корневых зонах остряков и подвижных сердечников, хвостовой части крестовины, зонах стыков и переднем вылете рамных рельсов.
Основные недостатки скреплений в этих зонах — повышенная жесткость, приводящая к быстрому расстройству узлов, недостаточное закрепление рельсовых элементов от перемещений в горизонтальной поперечной плоскости и вдоль пути, ухудшающее стабильность колеи, малые опорные поверхности для клемм и болтов, устаревший (заклепочный) способ соединения элементов.
Костыльное скрепление стрелочных переводов в зоне переводной кривой не удовлетворяет современным нагрузкам, передаваемым от подвижного состава на путь, возросшим в последнее время в связи с ухудшимся состоянием ходовых частей вагонов. В результате путейцы часто вынуждены применять дополнительное закрепление упорной нити с помощью клеммно-шурупных скреплений, применяемых на перегонах.
Помимо этих общих недостатков конструкции скреплений в пути имеют место изломы башмаков, трещины лафетов, расстройство корневых стыков остряков и подвижных сердечников, ускоряющих выход из строя стрелочных переводов по причинам недостатков конструкции и технологии изготовления.
Необходимо также отметить несовершенство конструкции скреплений в хвостовом стыке крестовин типа общей отливки сердечника с наиболее изнашиваемой частью усовиков, интенсивно влияющее на надежность и безопасность эксплуатации не только самих крестовин, но и примыкающих к ним рельсов.
Все это указывает на необходимость работ по совершенствованию скреплений и технологических схем их производства.
Выводы по разделу
- Основными причинами отказов стрелочных переводов являются износ и дефекты их основных элементов, а также общее расстройство конструкции, связанное с состоянием скреплений и подрельсового основания стрелочного перевода.
- Наиболее часто встречающаяся причина отказов стрелки — выход из строя остряков. Около 94% остряков выходят из строя по дефектам. Большинство дефектов, служащих причиной отказов остряков относится к I, П и IV группам дефектов.
- Число отказов элементов стрелки по специфическим дефектам, характерным для стрелочных переводов, превышает 22%, однако фактическая доля отказов элементов стрелки, ¿вязанная со спецификой работы стрелочных переводов, значительно выше, так как высокий уровень динамики в зоне стрелки способствует ускорению возникновения и развития контактно-усталостных дефектов, относящихся к общей для рельсов и рельсовых элементов стрелочных переводов классификации.
- Не менее 65% остряков выходит из строя по причинам недостаточной прочности и недостатков технологии их изготовления.
- Основные причины отказов крестовин с непрерывной поверхностью катания — дефекты I и П группы усовиков и сердечников в зоне перекатывания. Специфическими дефектами, характерными для этих крестовин служащими причиной их отказов, являются изломы усовиков в зоне обработки подошвы, расстройства — заклепочных соединений подушек сердечников, местные выработки металла на подошве сердечника и на подушках в зоне острия сердечника, расстройства корневого крепления ветвей сердечников и крепления ветвей сердечника у острия, расстройства и изломы элементов переводного механизма.
- Наиболее распространенной причиной отказов крестовин с неподвижными элементами служит износ сердечника и усовиков в зоне перекатывания. По этой причине отказы получают 60-80% крестовин. Однако поражаемость крестовин в этой зоне дефектами контактно- усталостного происхождения велика. К моменту достижения нормативного износа около трети всех крестовин имеют такие дефекты. При дальнейшей эксплуатации число крестовин, пораженных этим видом дефектов, возрастает нарастающими темпами.
- Значительная часть крестовин типа общей отливки сердечника с наиболее изнашиваемой частью усовиков поражается контактно-усталостными дефектами в зоне передней врезки. Несмотря на то, что такие дефекты служат причиной изъятия крестовин из пути в незначительном числе случаев, общее число крестовин, имеющих к моменту изъятия из пути такие дефекты, может достигать 40% и более.
- Несмотря на усовершенствование конструкции крестовин типа общей отливки сердечника с наиболее изнашиваемой частью усовиков, их отказы по опасному виду дефектов — изломам хвостовой части сердечника полностью не ликвидированы.
- Отказы контррельсовых узлов возникают наиболее часто по причинам разрывов контррельсовых болтов. Отказы контррельсов, изготавливаемых из оптимизированных спецпрофилей, возникают в количестве менее одного процента случаев (зафиксированы лишь отдельные случаи), однако такие отказы представляют из себя угрозу для безопасности движения поездов. Причина отказов — усталостные повреждения.
- Специфичные для стрелочных переводов отказы ходовых рельсов при контррельсе возникают из-за образования седловин, связанных с конструкцией контррельсовых узлов и динамикой прохождения подвижного состава по крестовинным узлам.
- Причины и интенсивность отказов рельсовых элементов соединительных путей стрелочных переводов близки к аналогичным для соответствующих случаев перегонных путей.
- Современные конструкции скреплений на стрелочных переводах не полностью отвечают требованиям эксплуатации и нуждаются в значительных усовершенствованиях.
- В целом не менее 65% основных элементов стрелки и до 50-60% элементов крестовинных узлов получают отказы из-за недостатков конструкции, недостатков технологии и недостаточной прочности металла.
Повышение эксплуатационных качеств стрелочных переводов за счет производства элементов повышенной надежности
Повышение надежности стрелок
Важнейшим направлением повышения надежности стрелок является совершенствование их конструкции.
Наиболее слабый конструктивный узел стрелки — корневое крепление остряка. В массовых конструкциях стрелочных переводов используются стрелки с вкладыше-накладочной конструкцией корневого крепления. Перевод стрелки осуществляется за счет поворота остряков в корневом стыке.
Относительно свободное положение остряка в корне приводит к повышенным перемещениям узла, взаимным смещениям его элементов и расстройствам в процессе эксплуатации, в том числе к разрушению распорных втулок. В результате дополнительных динамических воздействий в корне, дефекты возникают и в непосредственно примыкающей к нему зоне выпрессовки остряка.
В зимнее время в пазухи между отогнутыми накладками и остряком набивается снег, то требует дополнительных затрат на обслуживание стрелочного перевода.
Этих недостатков лишены стрелки с гибкими остряками. Массовое производство таких стрелок было освоено на стрелочных заводах России. Впервые их массовое производство было освоено на Муромском стрелочном заводе.
Корень остряков стрелок с гибкими остряками соединяется с примыкающим рельсом обычными четырехдырными стыковыми накладками. Перевод остряков осуществляется за счет изгиба остряков. От изгибных деформаций корень защищен специальным мостиком к которому остряк закрепляется высокопрочными болтами (см. рис. 3.1,а).
Освоение массового производства стрелок с гибкими остряками потребовало переработки технологии производства остряков и переделки сборочных стендов что окупилось в эксплуатации.
На рис. 3.2 показаны обобщенные данные по результатам эксплуатации больших партий стрелок различной конструкции полученные на Московской, Северной, Горьковской, Свердловской и Западно-Сибирской дорогах. На рис.3.2 видно, что преимущество стрелок с гибкими остряками является устойчивым в течение всего срока эксплуатации. На момент достижения нормативной наработки основной показатель надежности — вероятность безотказной работы таких стрелок составляет 0,595, что в 1,1 раз превышает аналогичный показатель для стрелок с поворотными остряками.
Однако применение гибких остряков не полностью решает вопросы создания высоконадежных стрелок. Остаются нерешенными вопросы повышенного бокового износа из-за высокой горизонтальной поперечной жесткости стрелки, сложность содержания переводного механизма из-за взаимных перемещений остряка и рамного рельса при угоне пути, особенностей стыкования несимметричного корня остряка с примыкающим рельсом (особенно при применении сварки).
Для решения этих вопросов была разработана стрелка с удлиненными гибкими остряками с приварными , рельсовыми окончаниями (рис. 3.1,6), технология производства которой впервые в России освоена Муромским стрелочным заводом в 1996 г.
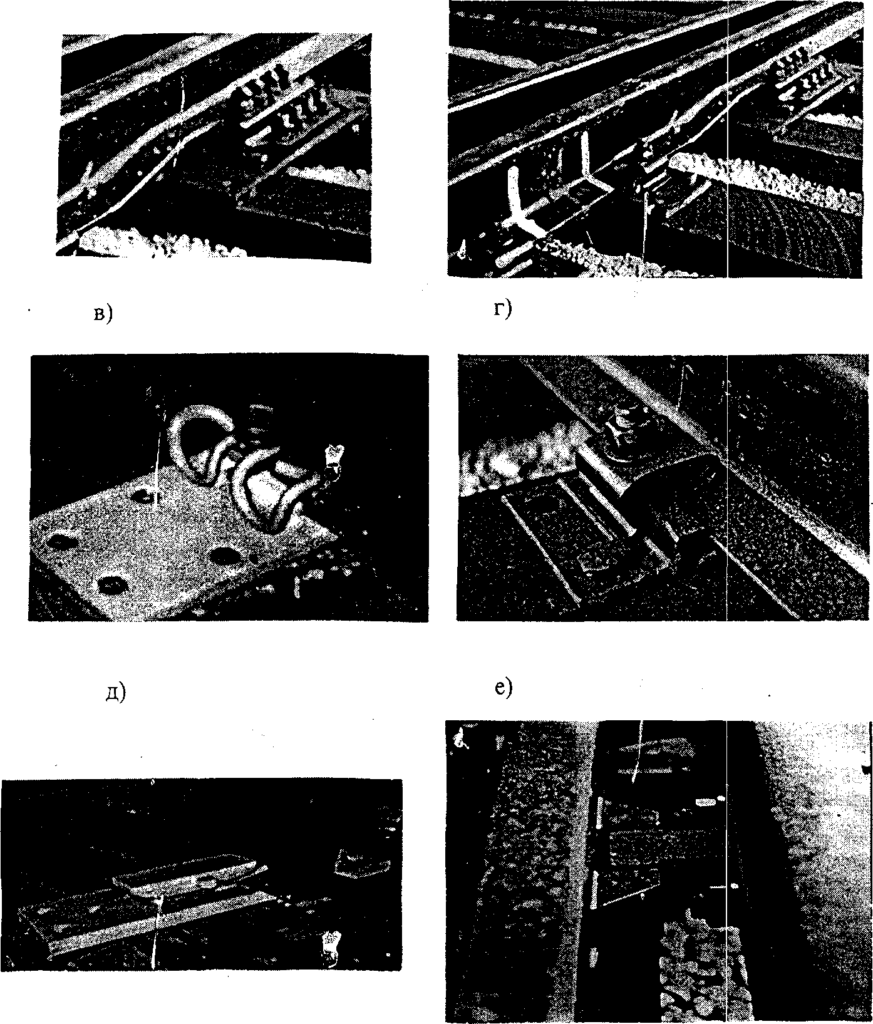
Скрепления на стрелке упругие, причем конструкция подкладок и башмаков разработана универсальной и позволяет установку как прутковых (рис. 3.1,в), так и пластинчатых (рис. 3.1,г) клемм. В случае необходимости возможна установка клемм скреплений тира «К».
Со стороны остряка рамный рельс фиксируете^ с помощью специальных «П»-образных прутковых клемм (рис.3..1,д).
Такая конструкция прикрепления рамного рельса позволяет перераспределять энергию воздействия колес в упругую деформацию, что уменьшает боковой износ и накопление расстройств колеи на стрелке в процессе эксплуатации.
На стрелке применено специальное противоугонное устройство (рис. 3.1,е), ограничивающее взаимные перемещения остряка и рамного рельса и не препятствующие его переводу.
Приварное рельсовое окончание позволяет сделать корневой стык обычным рельсовым стыком, допускающим сварку в пути и постановку изолирующего стыка в корне остряка, что позволяет разработать современную двухблочную схему стрелочного перевода.
Технология контактного способа приварки рельсового окончания находится в стадии освоения. Поэтому для ускорения внедрения прогрессивной конструкции стрелки были проведены опыты по приварке рельс вых окончаний алюмино-термитным способом, с термообработкой подошвы сварного стыка. Результаты испытаний опытных образцов представлены в табл. 3.1. Как видно из таблицы полученные результаты полностью соответствуют техническим условиям на сварку элементов стрелочных переводов /20/.
.Эксплуатационная проверка на ст. Ильино Горьковской ж.д., где стрелка проходит испытания в составе головного образца стрелочного перевода для путей 1 и 2 классов, показала работоспособность конструкции в целом и высокое качество сварных стыков рельсовых окончаний остряков.
Результаты испытаний термитных сварок рельсовых элементов из рельсов Р65 по технологии с коротким подогревом,
с термообработкой подошвы на Муромском стрелочном заводе
Показатель (образец) | Схема нагружения | Разрушающая нагрузка, кН | Прогиб, мм |
---|---|---|---|
Образец №1 | головка | 1450 | 14 |
№2 | вниз | 1310 | 13 |
№3 | 1340 | 13 | |
Среднее значение | 1367 | 13,3 | |
Стандартное отклонение | 60 | 0,47 | |
Минимальное вероятное значение | 1160 | 12 |
Более, чем за год эксплуатации, в сварных стыках не возникло дефектов, местный износ в зоне сварного соединения отсутствует.
В настоящее время все исследования по разработке технологии производства новых стрелок повышенной надежности на Муромском стрелочном заводе полностью завершены. Разработанные технологические схемы позволяют получать продукцию со стабильным качеством и обеспечивают возможность изготовления таких стрелок серийно в объеме заказа МПС РФ.
Стрелки с усиленными остряками для горочных стрелочных переводов
Симметричные горочные стрелочные переводы марки 1/6 являются основным элементом путевого развития подгорочных парков сортировочных станций российских железных дорог. Их состояние в значительной мере влияет на работу станций по формированию грузопотоков/133/.
Стрелки этих стрелочных переводов в процессе эксплуатации испытывают интенсивное боковое воздействие, что часто усугубляется плохим качеством укладки переводов в путь /28. 109/. В результате остряки и рамные рельсы стрелок таких переводов имеют большую скорость бокового износа /101/. Тонкие сечения остряков получают в эксплуатации дефекты в виде выкрашиваний от острия до сечения с шириной головки 20 мм, чаще всего в районе стрелочной тяги.
Обследования, проведенные на Северной и Горьковской ж.д. показывают (см. рис. 3.3 и 3.4), что около 61% рамных рельсов горочных стрелочных переводов поражены боковым износом различной величины в переднем вылете и 72% в острие остряков.
Боковой износ в узких сечениях имеют около 53% остряков. В более широких сечениях это число увеличивается до 64%.
Боковой износ сокращает срок службы стрелок. На отдельных интенсивно работающих стрелках замену остряков приходится производить 3-4 раза в год, а при некачественной укладке еще чаще.
Для продления срока службы стрелок горочных стрелочных переводов на Муромском стрелочном заводе создана новая конструкция стрелки для симметричных стрелочных переводов марки 1/6 /73/.
На рис. 3.5 показаны схемы остряков типовых переводов проекта 2307 и вновь разработанного перевода проекта 8307. За счет дополнительного местного изгиба рамного рельса вдоль линии прилегания к нему остряка возникает возможность «ускорить» нарастание толщины головки остряка в направлении от острия к корню. При этом основные параметры стрелки — радиус и начальный стрелочный угол остаются неизменными и совпадают с аналогичными величинами типовой стрелки.
Как видно из рис. 3.5 головка остряка в зоне наибольших выкрашиваний стала почти в 2 раза шире. Изменена также и конфигурация рамных рельсов.
На рис. 3.6 приведены фотографии типовой и опытной полу стрелок, наглядно показывающие различие в конструкции остряков и рамных рельсов.
Поскольку основные %змеры новой стрелки совпадают с размерами типовой, они являются взаимозаменяемыми, что обеспечивает их укладку в путь без реконструкции сортировочных парков.
Остряк стрелочного перевода типа Р65 марки 1/6 в зоне прилегания к рамному рельсу в плак е на уровне измерения бокового износа
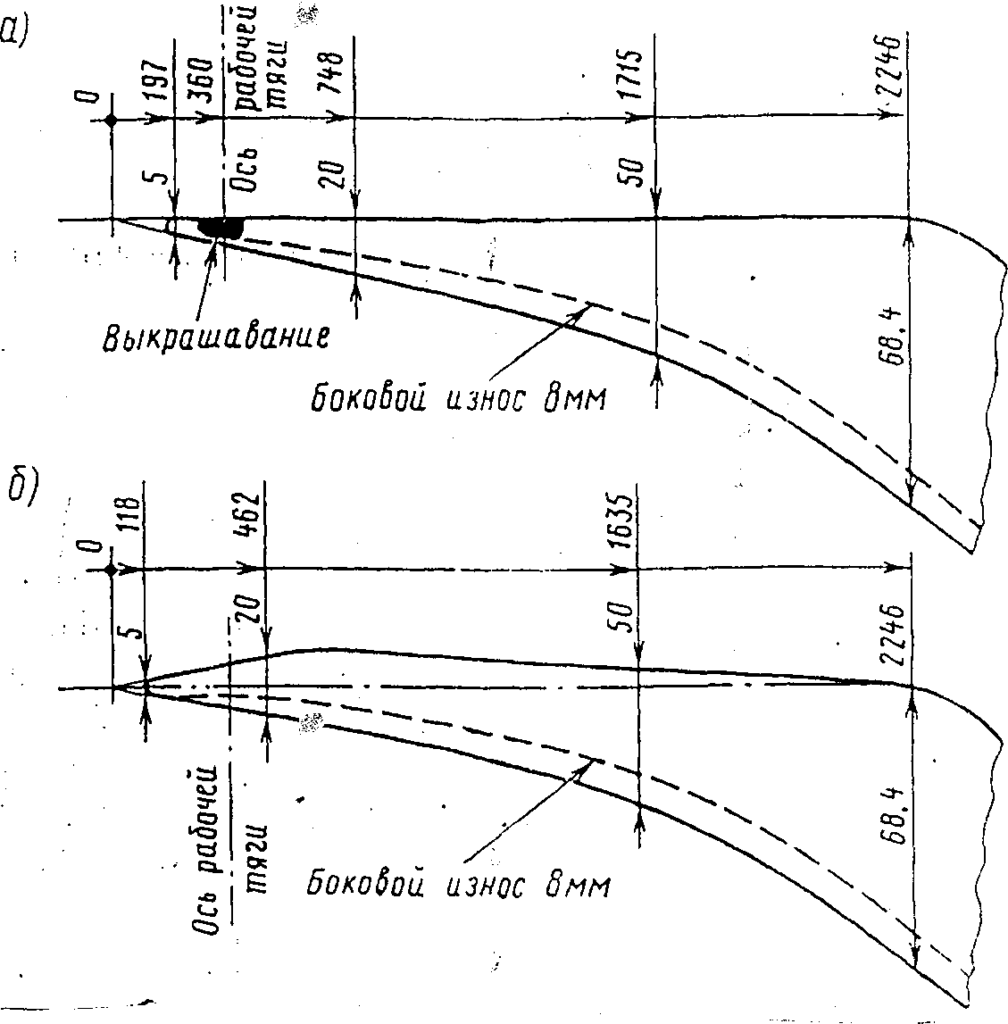
а — проекта ПТКБ 2307; б — проекта ОАО МСЗ 8307
Полустрелки горочных стрелочных переводов:

а) Типовая (проект 2307)
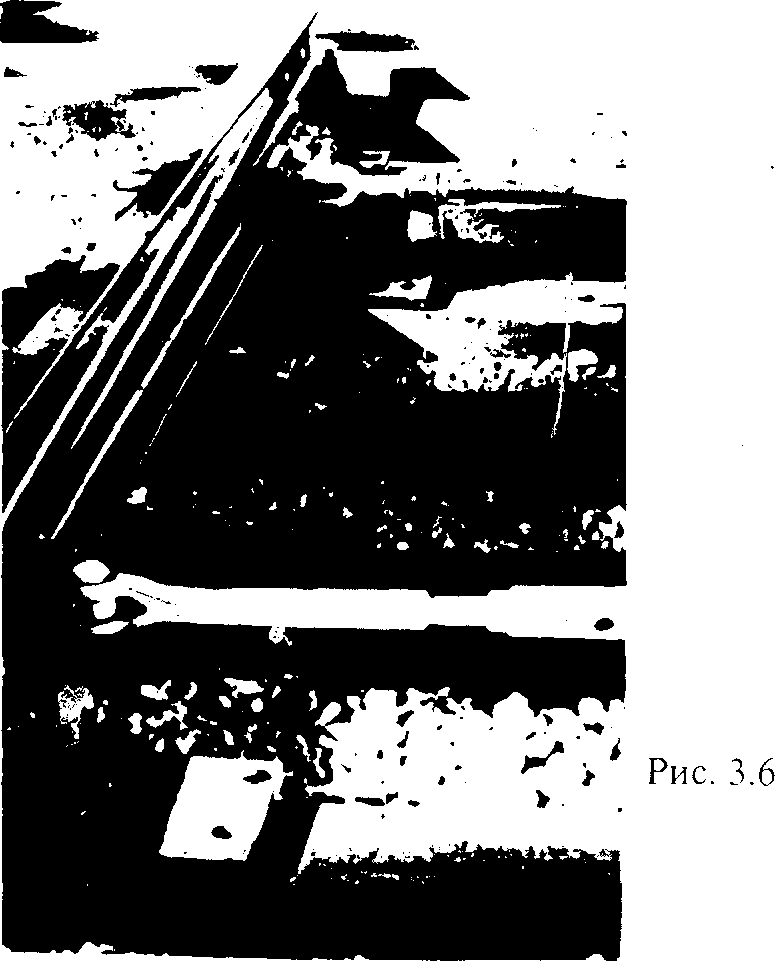
б) С уширенным остряком (проект 8307)
Стрелки новой конструкции начали поступать на дороги в 1996 г. За ними установлено наблюдение специалистами путеобследовательской станции ПС-8.
Результаты наблюдений 1996-1997 г.г. показали, что несмотря на ряд отступлений при укладке стрелочных переводов они работают устойчиво. Уширенные в тонких сечениях остряки не только имеют дополнительный запас на боковой износ, но и «прикрывают» от бокового износа рамные рельсы, что должно дать дополнительный эффект по продлению срока службы стрелки в целом.
Крестовины с улучшенной конструкцией врезки и усиленной хвостовой частью
Слабым местом современных наиболее массовых конструкций крестовин (типа общей отливки сердечника с наиболее изнашиваемой частью усовиков) являются сочленение литой части с рельсовыми усовиками — «передняя врезка» и стык хвостовой части с примыкающими рельсами.
Дефекты передней врезки ДУЛ 2.2 и близкие к ним определяются наличием динамической неровности при переходе колес с литой части на рельсовую и обратно, которая определяется наличием геометрических ступенек, люфтов сочленения и различием деформационных и пластических свойств металла литой и рельсовых частей.
Полностью ликвидировать причины возникновения дефектов передней врезки в рамках данной конструкции крестовин не представляется возможным, тем не менее вопрос ее усовершенствования остается важным.
Работы над совершенствованием конструкции передней врезки и освоением производства улучшенных конструкций ведутся уже многие годы.
Основная направленность этих работ — улучшение геометрических и динамических условий прохода колес через зону врезки и создание конструкции с жестким взаимным закреплением рельсовой и литой частей.
Помимо совершенствования стандартной конструкции врезки были выпущены и испыйшы партии крестовин с различными конструкциями врезки, в том числе по предложению инженера Росса (НСЗ) и ряд других. Каждое из этих предложений имело, как преимущества, так и недостатки, не позволившие принять его в качестве стандартного.
В настоящее время на Муромском стрелочном заводе разработана технология производства высокотехнологичной крестовины по предложению ПТКБ ЦП.
Крестовина показана на рис. 3.7. Как видно из рис. 3.7 само понятие «врезка» для этой крестовины условно. Закрепление от продольного перемещения сердечника относительно усовиков выполнено с помощью специальных выступов, входящих в «окна» выфрезерованные в усовикгЙ. Обработка усовиков минимальна. В вертикальной плоскости закрепление от взаимных перемещений сердечника и усовиков также улучшено. Оно выполнено в виде «замка» с упором в наклонные части подошвы и головки рельса.
Хорошее взаимное сочленение элементов крестовины позволило отказаться от лафета, что уменьшило металлоемкость крестовины, а применение подкладок с высокими ребордами будет способствовать увеличению стабильности колеи на крестовинном узле. Данная конструкция врезки реализована на крестовинах марок 701/6, 1/9 и 1/11, она прошла испытания на Экспериментальном кольце ВНИИЖТа и Северной ж.д. Результаты испытаний показали, что такое сочленение литой и рельсовой частей крестовин надежно обеспечивает их солидарную работу. Данная конструкция врезки включена, как вариант, в отраслевой стандарт на крестовины /67/.
В заднем стыке литая часть крестовин типа общей отливки сердечника с наиболее изнашиваемой частью усовиков непосредственно стыкуется с примыкающими рельсами. Такая конструкция приводит, как уже указывалось в разделе 2, к тому, что в эксплуатации на крестовинах возникают дефекты ДС.10.1, ДС.50.1. ДС.60.1-2, ДС.63.1. Большая часть этих дефектов требует немедленной замены крестовины.
В результате, как уже указывалось, из пути изымается около 4,5% крестовин, причем, как правило, на начальной стадии эксплуатации. Эти крестовины не ремонтопригодны и теряются безвозвратно.
Технологические особенности механической обработки хвостовой части сердечников приводят к тому, что при стыковании между крестовиной и примыкающим рельсом могут возникать ступеньки. Эти ступеньки крайне неблагоприятно сказываются на взаимодействии пути и подвижного состава при проходе по крестовинам.
На стрелочных заводах России были проведены работы по ликвидации причин, вызывающих дефекты хвостовой части крестовин. Основная направленность этих работ была следующей:
- улучшение качества металла в зоне подошвы хвостовой части крестовин за счет изменения технологии заливки и термообработки;
- увеличение момента инерции относительно горизонтальной поперечной оси в критических сечениях хвостовой части и ликвидация зон резкого изменения момента инерции сечения;
- изменение конструкции с целью ликвидации концентраторов напряжений в местах выхода режущего инструмента при обработке пазух;
- улучшение технологии обработки сердечников и закрестовинных вкладышей с целью повышения точности исполнения стыковочных размеров.
На Муромском стрелочном заводе отработка наиболее эффективной конструкции и технологии изготовления хвостовой части крестовин велась отдельно, что связано со спецификой литейного производства и различием технологических схем обработки сердечников. работы проводились по всем вышеперечисленным направлениям.
Испытания усовершенствованных крестовин были проведены в 1992-1995 г.г. Крестовины марки 1/11 испытывались на Экспериментальном кольце ВНИИЖТ под воздействием подвижного состава с осевыми нагрузками 270 кН и скоростью движения 70 км/ч.
Наработка на отказ по дефектам хвостовой части усиленных крестовин превышала аналогичный показатель для контрольных в 2-3 раза, отдельные крестовины до 6 раз.
Одновременно велась отработка конструкции крестовин марки 1/6 для горочных стрелочных переводов. Испытания проводились на подгорочных путях станции Орехово-Зуево, при скоростях движения до 40 км/ч.
Крестовины имели усовершенствованную конструкцию (см. рис. 3.7) и усиленную хвостовую часть.
Результаты сравнительных испытаний показали, что наработка усиленных крестовин до отказа по всем видам дефектов, по сравнению со стандартными, увеличилась на 15-20%. Полностью ликвидировать отказы по дефектам хвостовой части не удалось, однако средняя наработка до отказа по этим дефектам, у усиленных крестовин увеличилась более чем в два раза.
Помимо положительного эффекта — увеличения наработки до отказа крестовин по дефектам хвостовой части, в результате проведенных работ был полечен еще один важный вывод. Анализ вариантов конструкций и технологических схем показал, что достигнутый уровень качества для применяющегося в настоящее время оборудования близок к предельному. В то же время затраты на замену оборудования соизмеримы с затратами на освоение производства конструкций крестовин с более совершенной хвостовой частью.
Радикальным конструктивным решением, исключающим недостатки хвостовой части, является применение крестовин с приварными рельсовыми окончаниями.
Крестовины с приварными рельсовыми окончаниями
Крестовины с приварными рельсовыми окончаниями позволяют заменить специфический задний стык крестовины на обычный рельсовый. Помимо того, что на таких крестовинах исключаются все неблагоприятные особенности заднего стыка, появляется возможность сварки крестовины с примыкающими рельсами, то есть полной ликвидации стыков в зоне крестовинного узла.
Освоение производства крестовин с приварными рельсовыми окончаниями потребовало полной переработки конструкции крестовин, технологических схем изготовления элементов крестовин и разработки принципиально новых технологий. Наиболее важной частью всего комплекса работ явились:
- разработка технологий отливки сердечника и его механической обработки;
- разработка технологии полуавтоматической сварки ветвей рельсовых окончаний между собой (продольная сварка головки и подошвы рельсовых элементов);
- разработка технологии сварки рельсового окончания с высокомарганцовистым сердечником (через хромо-никелевый промежуточный элемент) на специальной сварочной машине.
Работы велись в тесном контакте с ВНИИЖТом, ПТКБ ЦП и институтом электросварки им. Е.Патона, причем конструкция крестовин, технологические процессы сварки и конструкция сварочного оборудования отрабатывались параллельно.
Сложность разработку технологии производства крестовин с рельсовыми окончаниями иллюстрирует тот факт, что в процессе работы трижды пришлось менять конструктивную компоновку крестовины.
В настоящее время крестовины с рельсовыми окончаниями производства Муромского стрелочного завода (рис. 3.8) прошли испытания на Экспериментальном кольце ВНИИЖТа и на Горьковской ж.д. Они включены, как элемент, в конструкцию стрелочных переводов для путей 1 и 2 классов и с 1997 г. выпускаются серийно.
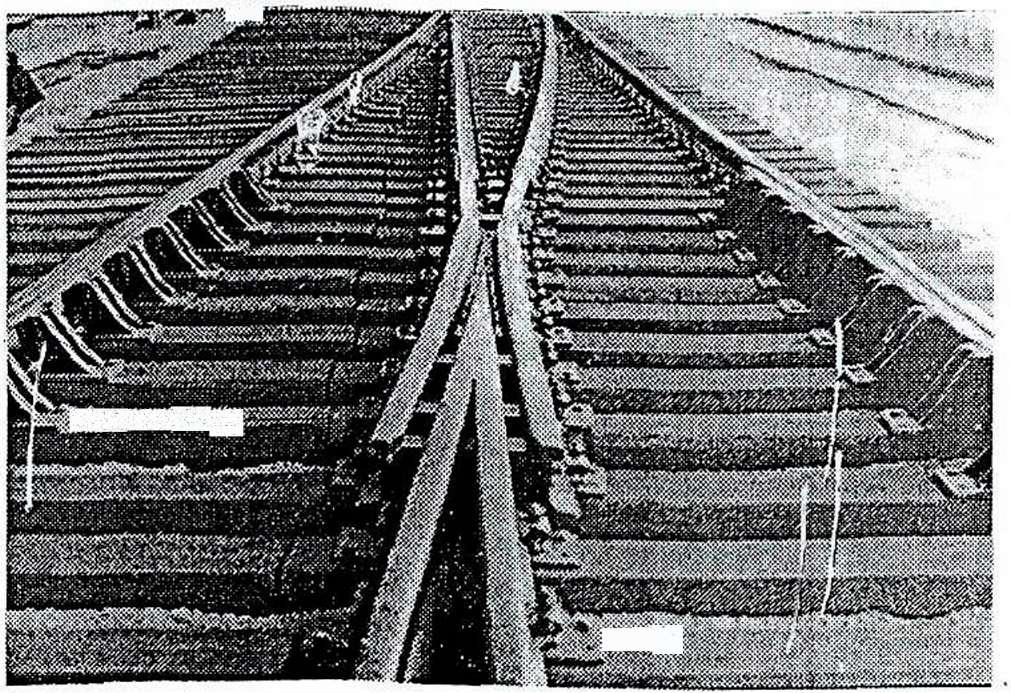
крестовина с приварными рельсовыми окончаниями
На перспективу планируется постепенный переход к массовому выпуску таких крестовин. Для ускорения их внедрения на сеть дорог разработана конструкция крестовин с укороченными рельсовыми окончаниями взаимозаменяемая с типовыми наиболее массовыми крестовинами марк 1/11. При такой конструкции в заднем стыке крестовины из-за невозможности установки болтов в отверстия накладок используется вкладыш. Наличие вкладыша несколько ухудшает качество стыка. По своим эксплуатационным характеристикам такие крестовины уступают крестовинам с рельсовыми окончаниями основного проекта и рассматриваются, как промежуточный временный вариант.
Несмотря на то, что крестовины с приварными рельсовыми окончаниями уже выпускаются серийно, работу над их конструкцией и технологией изготовления следует продолжить.
Испытания, проведенные на Экспериментальном кольце ВНИИЖТ выявили, что слабым местом конструкции таких крестовин является зона выхода сварных швов, соединяющих ветви сгрдечника.
Исследования показали, что в этой зоне имеются термические и механические концентраторы напряжений, которые могу?’ приводить к изломам и трещинам в рельсовых элементах.
Работа над ликвидацией причин этих дефектов в настоящее время ведется по двум направлениям — совершенствование технологии изготовления и изменение конструкции крестовины.
Усовершенствованные крестовины выпускаются с 1998 г. серийно в составе стрелочных переводов для путей 1 и 2 классов, в том числе на железобетонном подрельсовом основании.
Контррельсовые узлы с контррельсами не связанными с ходовыми рельсами
Главные недостатки контррельсовых узлов с контррельсами из контррельсовых спецпрофилей это невозможность регулировки желобов в процессе износа контррельса и трудность замены отдельных элементов узла в процессе эксплуатации. Практически при возникновении необходимости такой замены путейцы заменяют весь узел, включая контррельс £ и ходовой рельс, что ведет к неоправданным потерям.
Названных недостатков лишены контррельсовые узлы с контррельсами не связанными с ходовыми рельсами. Важной особенностью таких контррельсовых узлов является то, что в качестве ходового рельса в них используются обычный рельс, не требующий при изготовлении узла какой-либо механической обработки и легко заменяемый.
Разработка конструкции и технологии изготовления контррельсовых узлов не связанных с ходовым рельсом ведется с начала 90-х годов.
Основные требования к узлу такой конструкции можно сформулировать следующим образом:
- выполнение контррельсом условий безопасности и высокая прочность;
- возможность, а также простота регулировки желобов и размеров между контррельсом и элементами крестовины;
- высокая надежность скреплений и крепления контррельса (контррельсовых башмаков);
- минимальный износ контррельса;
- надежность прикрепления ходового рельса к подкладке и максимальная простота его замены в пути.
На Муромском стрелочном заводе были разработаны технологии производства нескольких вариантов контррельсовых узлов с контррельсами не связанными с ходовыми рельсами.
При производстве башмаков для контррельсо’вых узлов с контррельсами не связанными с ходовыми рельсами используется полуавтоматическая сварка по специально разработанной для этого процесса технологии.
Испытания узлов проводились на Экспериментальном кольце ВНИИЖТ. Испытания показали, что наиболее сложным является выполнение требований к прочности и надежности контррельсовых башмаков, а также требование к прикреплению ходового рельса.
Наилучшие результаты получены для сварных башмаков, показанных на рис. 3.9. Этот вариант узла был включен в конструкцию стрелочных переводов для путей 1 и 2 классов. В настоящее время он успешно эксплуатируется в главных путях Горьковской дороги в условиях движения пассажирских поездов до 100 км/ч, грузовых до 70 км/ч. Наработка по переводу на конец года составила 35 млн.т бр. Замечаний по работе узла и каких либо дефектов нет.
По результатам испытаний принято решение о серийном производстве контррельсовых узлов с контррельсами не связанными с ходовыми рельсами.
Дальнейшее усовершенствование контррельсовых узлов должно включать в себя разработку специального контррельсового прокатного профиля. В настоящее время контррельс изготавливается из профиля шин для горочных вагонных замедлителей, которые обладают избыточной металлоемкостью и повышенной боковой жесткостью, приводящей к износу и сплавам металла в зоне набегания колес на контррельс. Проект необходимого спецпрофиля разработан ВНИИЖТом. После его внедрения экономия металла на изготовление новых контррельсовых узлов составит не менее 30% по сравнению с выпускаемыми в настоящее время в массовом порядке.
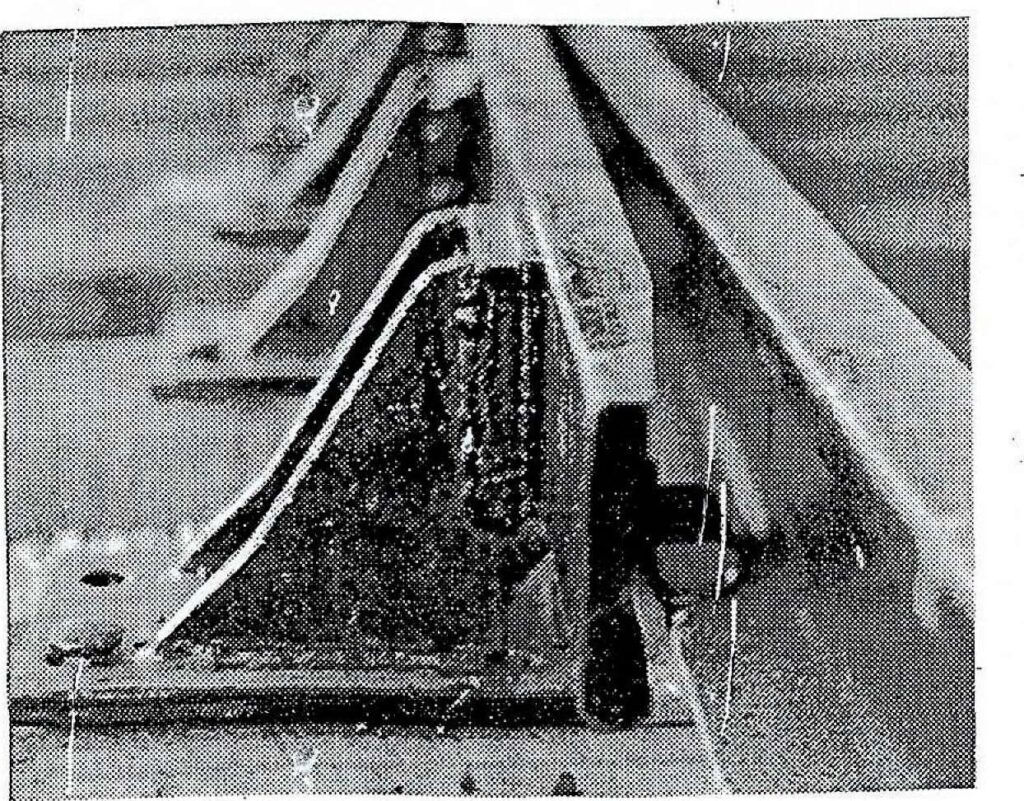
Узел крепления контррельса не связанного с ходовым рельсом
Выводы по разделу
- Переход от выпуска поворотных стрелок к стрелкам с гибкими остряками позволяет увеличить вероятность безотказной работы стрелок на момент нормативной наработки не менее, чем в 1,1 раза, а также сократить затраты на текущее содержание стрелок.
- Дальнейшее совершенствование конструкции стрелок с применением удлиненных остряков с приварным рельсовым окончанием, упругих скреплений, противоугонных устройств позволяет создать базу для оптимизации компоновки стрелочных переводов, уменьшения вертикальной и горизонтальной динамики на стрелках, обеспечения возможности создания малообслуживаемых стрелочных переводов нового поколения. Конструкция и технология изготовления таких стрелок отработана, они могут выпускаться серийно.
- Конструкция стрелки с усиленными остряками для горочных стрелочных переводов, имеющими запас на боковой износ, успешно прошла испытания.
На ее основе разработана конструкция стрелок для переводов марок 1/9 и 1/11, которая проходит испытания в настоящее время. Ведется разработка стрелки для переводов с касательными остряками . - Применение крестовин с улучшенной конструкцией передней врезки и усиленной хвостовой частью позволяют значительно уменьшить поражаемость этих зон крестовин в пути, по врезке на 2060% в зоне хвостовой части и в 2 и более раз. Тем не менее полностью ликвидировать дефекты заднего стыка при использовании современной массовой конструкции крестовин типа общей отливки сердечника с наиболее Изнашиваемой частью усовиков не представляется возможным.
- Радикальным и наиболее перспективным направлением, позволяющим решить вопросы стыкования крестовин с примыкающими элементами является переход на применение крестовин с приварными рельсовыми окончаниями, позволяющих не только перейти от специальных стыков к обычным рельсовым, но и дающим возможность сварки крестовин в пути с примыкающими к ним рельсами, тем самым создавая возможность вваривания стрелочных переводов в примыкающие плети. Конструкция и технология производства таких крестовин отработана, они могут выпускаться серийно.
- Контррельсовые узлы с контррельсами не связанными с ходовыми рельсами отвечают предъявляемым к ним требованиям. Они прошли полигонные и эксплуатационные испытания, показавшие их высокую работоспособность. Преимущества, которыми они обладают с точки зрения регулировки и обслуживания в пути, а также замены элементов позволяют рекомендовать эту конструкцию для широкого применения в стрелочных переводах различных типов и марок при условии обеспечения необходимого технологического уровня изготовления сварки башмаков.
Технологические методы повышения качества элементов стрелочных переводов
Стабилизация качества формирования рабочих поверхностей крестовин за счет технологии совместной обработки сердечника и усовиков
Практически достигаемый эффект от конструктивных усовершенствований стреловых переводов и их элементов в значительной мере зависит от реальных возможностей технологии их изготовления, а в случае массовой продукции, к которой относятся стрелочные переводы, от возможностей налаживания стабильной технологии серийного производства. Это в полной мере относится к крестовинам с неподвижными элементами.
В восьмидесятых-девяностых годах специалистами ВНИИЖТа и ПГУПСа (ЛИИЖТа) были проведены большие работы по совершенствованию форм рабочих поверхностей крестовин с целью увеличения срока их безотказной работы. Основные концепции, которые закладывались при разработке новых профилей в порядке их реализации были следующими: начальный припуск на износ; начальный припуск на накле „; минимум суммарного динамического воздействия; оптимизация баланса процессов износа и дефектообразования в контактной области зоны перекатывания /1, 6, 25,91,105, 128/.
По мере проведения исследований совершенствовался стандарт на крестовины основных типов и марок /63-67/.
В целом результаты разработок, их иллюстрируют данные, приведенные в табл. 4.1, были положительными. Было достигнуто значительное повышение наргйботки крестовин до отказа по износу 2746%, однако массовое обследование крестовин в пути показало, что к моменту наработки до нормативного износа немногим больше половины крестовин не имело выкрашиваний в зоне перекатывания (см. рис. 4.1), 41% крестовин имели выкрашивания в зоне перекатывания, еще около 20% крестовин получало отказы по этому виду дефектов не достигнув нормативной наработки.
Таблица 4.1 Сравнительная износостойкость крестовин с различными вариантами рабочих поверхностей
Варианты рабочих поверхностей | ГОСТ 101 22-72 | СП-260 | ОСТ 32.11-78 | ОСТ 32.51-83 | ГОСТ 2837-89 |
Количество крестовин, шт | 116 | 55 | 129 | 155 | 67 |
Средняя наработка на отказ по износу, млн. т бр. | 80,4 | 98,6 | 102 | 113,4 | 117,1 |
Преимущество по отношению к ГОСТ 10122-72 | — | 1,23 | 1,27 | 1,41 | 1,46 |
Технологическая схема формирования рабочих поверхностей крестовины включала в себя раздельную обработку/ каждого из усовиков и отдельно сердечника.
Усовикам придавался поперечный уклон 1:20, что соответствует наклону основной части рабочих поверхностей колес. Сердечник имел горизонтальную форму раб(шей поверхности. Усовики и сердечник имели закругления по рабочим граням.
Статистический анализ исполненных размеров рабочих поверхностей крестовин, приведенный в табл. 4.2 дает возможность проследить динамику изменения точности соблюдения основных размеров крестовин. Данные получены на основе обмеров более 500 крестовин.
Комплексным показателем, характеризующим разброс размеров, является коэффициент вариации, который представляет собой отношение среднеквадратического отклонения измеренных размеров к среднему их значению по выборке /78/, где б — среднеквадратическое отклонение по выборке размера.
Таблица 4.2 Характеристика исполнения размеров, определяющих положение рабочих поверхностей крестовин в зоне перекатывания
Как видно из таб. 4.2 за длительный период по 1983 год точность исполнения основных форм поверхностей крестовин с неподвижными элементами оставалась приблизительно одинаковой. Коэффициент вариаций возвышения литого усовика над рельсовым находился в пределах 0,18-0,16. Положение сердечника характеризуется коэффициентом вариации 0,50, а взаимное положение сердечника и литой части усовика коэффициентом вариации 0,20-0,22.
Такая высокая вариация размеров рабочих поверхностей в зоне перекатывания не обеспечивает необходимую точность изготовления крестовин.
Исследования, проведенные ВНИИЖТом показали, что при отклонениях взаимного положения сердечника и усовика, превышающих 1,0-1,2 мм динамические добавки контактных сил на крестовинах могут возрастать до 1,7-2,0 раз по сравнению с крестовинами, имеющими профили без отклонений /21/.
Это является одной из причин раннего появления выкрашиваний в зоне перекатывания крестовин. В то же время стабильность вариации размеров по годам изготовления показывает, что возможности технологии раздельной обработки усовиков сердечника исчерпаны и не могут быть улучшены без замены оборудования или коренного изменения технологии.
Для улучшения качества изготовления крестовин специалистами Муромского стрелочного завода совместно со специалистами ВНИИЖТа и ПТКБ ЦП была предложена технология совместной обработки сердечника и усовиков крестовины с упругим прогибом отливки при обработке рабочих поверхностей.
По новой технологической схеме сердечник и усовик крестовины обрабатываются совместно за одну установку.
Продольный профиль крестовины формируется за счет предварительного упругого выгиба отливки при ее закреплении перед обработкой.
Внедрение технологической схемы совместной обработки сердечника и усовика позволило снизить вариацию их взаимного положения более, чем на 30% (см. табл. 4.2). Появилась возможность регламентации размеров зоны перекатывания.
За счет того, что и усовики и сердечник крестовины имеют одинаковый уклон и обработаны совместно переход колес с одного элемента на другой стал ^олее плавным. Кроме того, за счет предварительного упругого выгиба удалось реализовать разработанный ВНИИЖТом криволинейный продольный профиль крестовин, значительно улучшающий траектории движения колес по крестовине и снижающий общий уровень динамических сил в контакте колесо-крестовина.
В результате удалось достигнуть ощутимое снижение поражаемости рабочих поверхностей крестовин выкрашиваниями. Крестовины, изготовленные по технологии совместной обработки на момент наработки до нормативного износа имеют вероятность бездефектной работы 0,705, что на 11,5% выше, чем у крестовин с раздельно обработанными рабочими поверхностями. Это позволяет повысить срок их сл^%бы и значительно увеличивает ремонтопригодность крестовин.
Полученный положительный эффект может быть отнесен к особенностям технологической схемы совместной обработки. Реализация этой схемы позволила повысить эксплуатационные качества крестовин без приобретения специального дорогостоящего оборудования и реконструкции производства крестовин.’
Анализ работы крестовин выпуска 1990-1995 г.г. полностью подтверждает полученные результаты.
Замена заклепочных соединений сварными
Одной из причин, приводящих к преждевременному изъятию стрелочных переводов и их элементов из пути, является расстройство заклепочных соединений.
В конструкции стрелочных переводов заклепочные соединения применяются в зоне стрелки для крепления стрелочных подушек к подкладкам (см. рис. 4.2) и на крестовинах с непрерывной поверхностью катания для крепления опор, на которые опираются короткая и длинная ветвь поворотного (подвижного) сердечника в крестовине с непрерывной поверхностью катания.
В процессе эксплуатации под действием динамических нагрузок заклепки обминаются, а в отдельных случаях, как это видно на рис. 4.3, выпадают, нарушая тем самым нормальную работу стрелки и крестовины. На крестовинах замечены случаи, когда «разболтавшаяся» заклепка приподнимается над поверхностью опоры. При этом создается препятствие подвижному сердечнику при переключении движения с прямого на боковой путь и обратно. Крестовины с такими дефектами приходится изымать из пути, несмотря на то, что они могли бы еще длительное время эксплуатироваться.
Для ликвидации этих дефектов были разработаны новые конструкции стрелочных башмаков и опор сердечников крестовин с непрерывной поверхностью катания а также технология их изготовления с применением сварочных полуавтоматов.
Типовой стрелочный башмак с подушкой, закреплённой заклепками
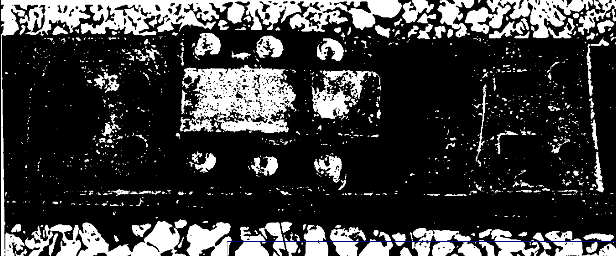
а) Вид сверху
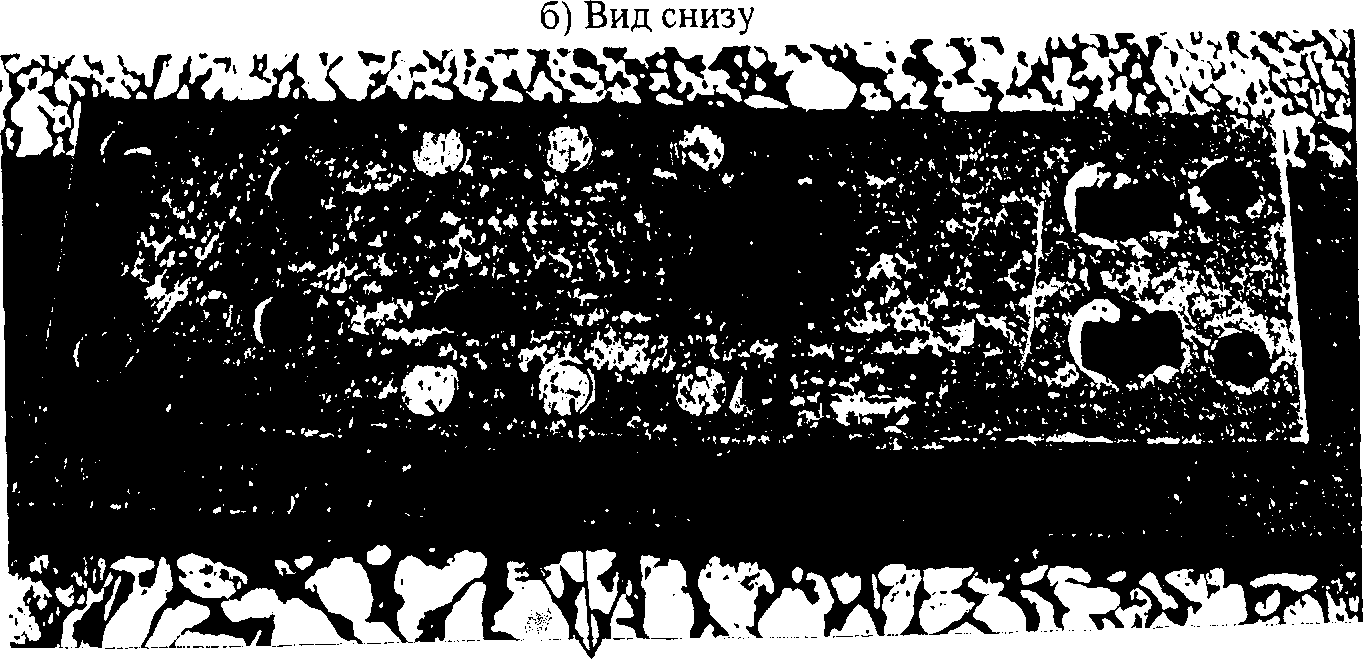
б) Вид снизу
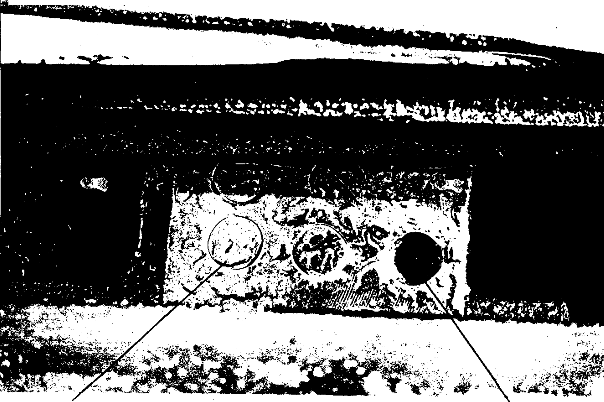
Расстройство заклепочного соединения на крестовиной подушке
В качестве примера на рис. 4.4 показан стрелочный башмак с приварной подушкой. Приварка подушки осуществляется с нижней стороны башмака через отверстия со специальной разделкой.
Необходимо также отметить, что новая технология позволяет заменить литую подушку стрелочного башмака на подушку из специального проката.
Испытания сварных башмаков были проведены на Экспериментальном кольце ВНИИЖТа под воздействием подвижного состава с осевыми нагрузками 27 т/ось. По сварным башмакам было пропущено 320 млн.т бр. груза.
Результаты испытаний показали надежную работу сварных соединений и башмаков в целом. Ни один из башмаков в результате работы в пути не получил отказа по дефектам сварных соединений.
Наработка до отказа башмаков с приварными подушками по изломам подкладки не отличается от наработки типовых башмаков. По результатам испытаний новые башмаки рекомендованы к серийному производству.
В настоящее время сМи введены в качестве элементов в конструкции всех перспективных стрелочных переводов, в том числе скоростных и для путей высших классов и категорий.
На основе новой конструкции башмаков и технологии сварки разработаны упругие скрепления для стрелок нового поколения стрелочных переводов (см. рис. 4.5).
Усиленные скрепления на основе сварочной технологии
Многолетние наблюдения за работой стрелочных переводов показали неудовлетворительную работу скреплений.
Стрелочный башмак с приварной подушкой
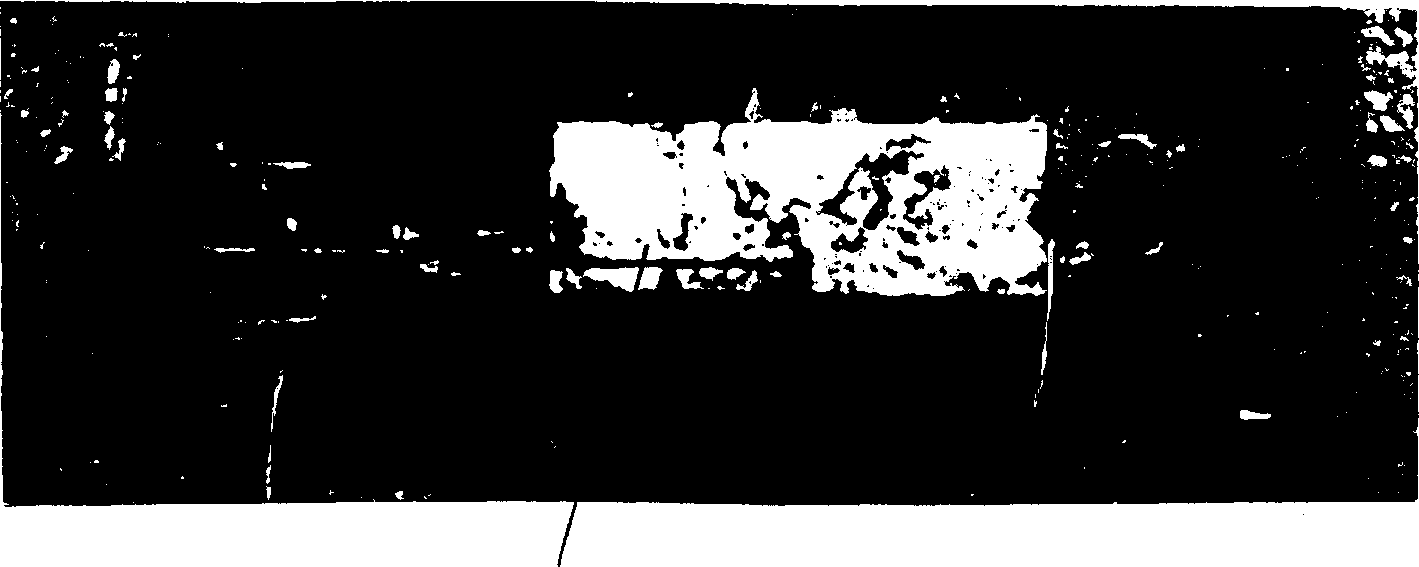
а) Вид сверху
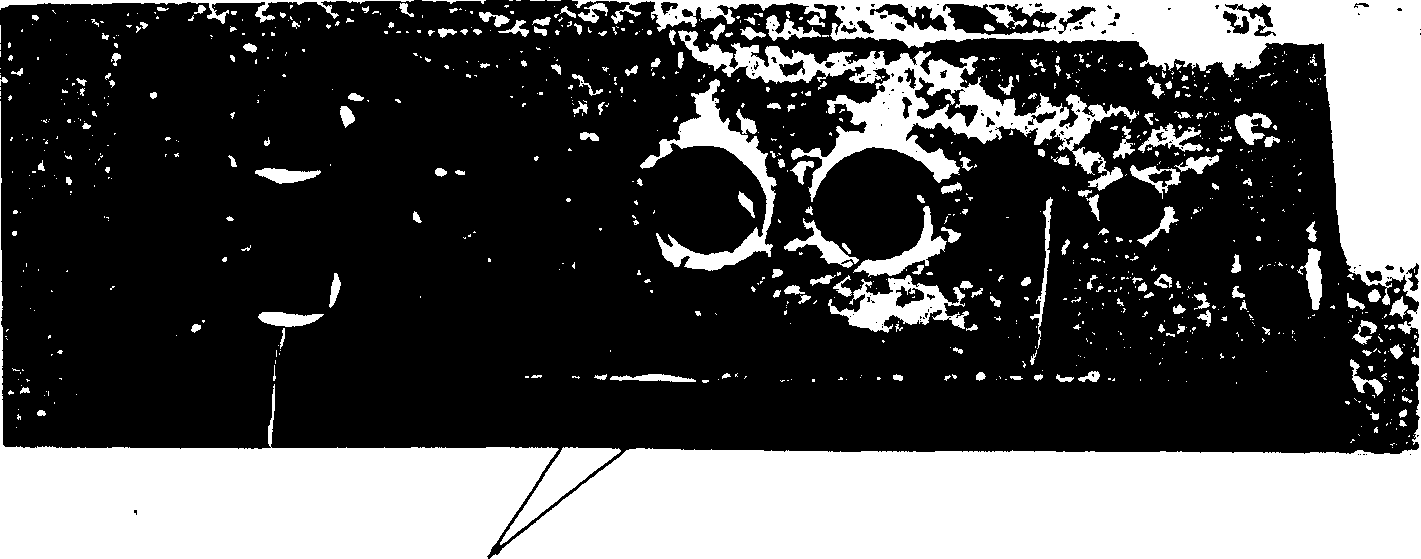
б) Вид снизу
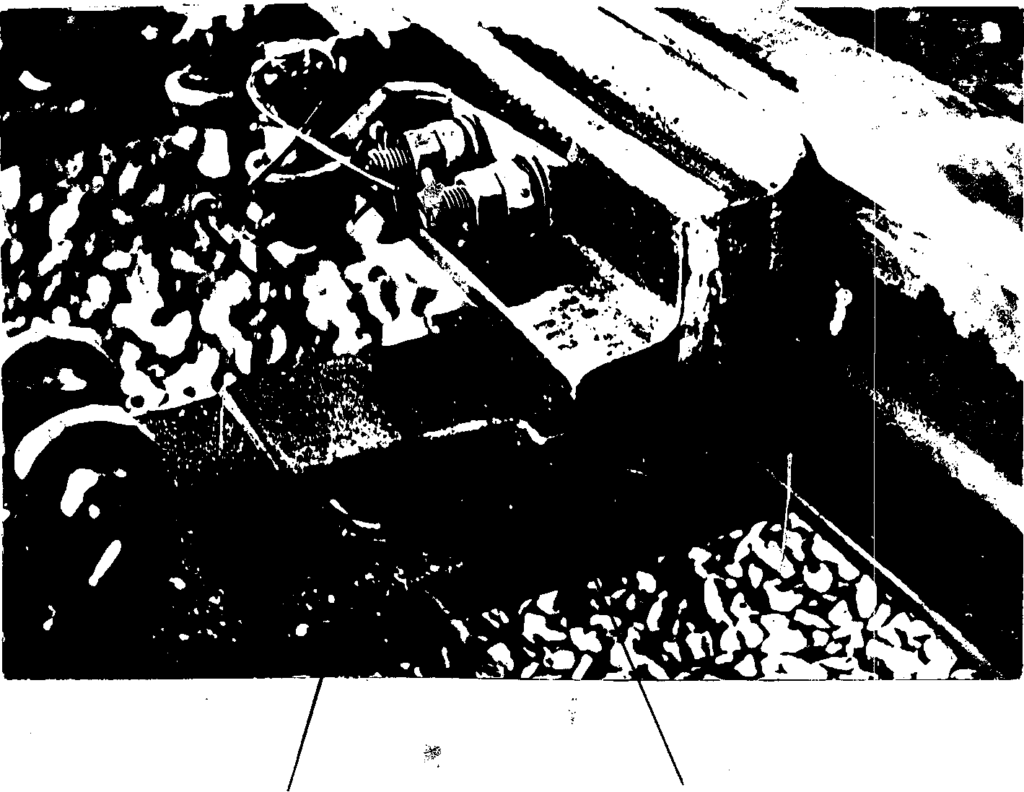
Упругая скоба Выступы подушки для крепления упругой скобы
Наибольшие расстройства колеи на стрелочных переводах из-за неудовлетворительной надежности скреплений происходит на стрелке в закорневой зоне и на крестовине преимущественно в зоне заднего стыка 121.
На рис. 4.6 показана одна из закорневых подкладок типовой конструкции. Легко видеть, что каких-либо элементов, препятствующих горизонтальному поперечному смещению рельсов, на подкладке такой конструкции нет. Вся горизонтальная поперечная нагрузка от колес подвижного состава воспринимается клеммными болтами.
Опыт эксплуатации показывает, что удерживающая сила болтов в горизонтальном поперечном направлении недостаточна. Наблюдается ослабление затяжки износ резьбы и разрывы болтов, остаточные деформации болтовых отверстий подкладок, выход из строя всего узла прикрепления. Накопление таких расстройств служит одной из причин сходов подвижного состава с рельсов из-за уширения колеи, а также причиной преждевременной смены металлических частей стрелочных переводов.
Для ликвидации эти. дефектов была разработана новая конструкция скреплений для закорневой и крестовиной зон. Основным элементом такой конструкции служит подкладка с высокими ребордами (см. рис. 4.7).
Технология изготовления новых подкладок на Муромском стрелочном заводе основана на сварке. Реборды отливаются из углеродистой стали и крепятся к подкладке с помощью полуавтоматической сварки по контуру прямоугольных отверстий с нижней стороны подкладки.
Типовая закорневая подкладка
а) Рабочая поверхность
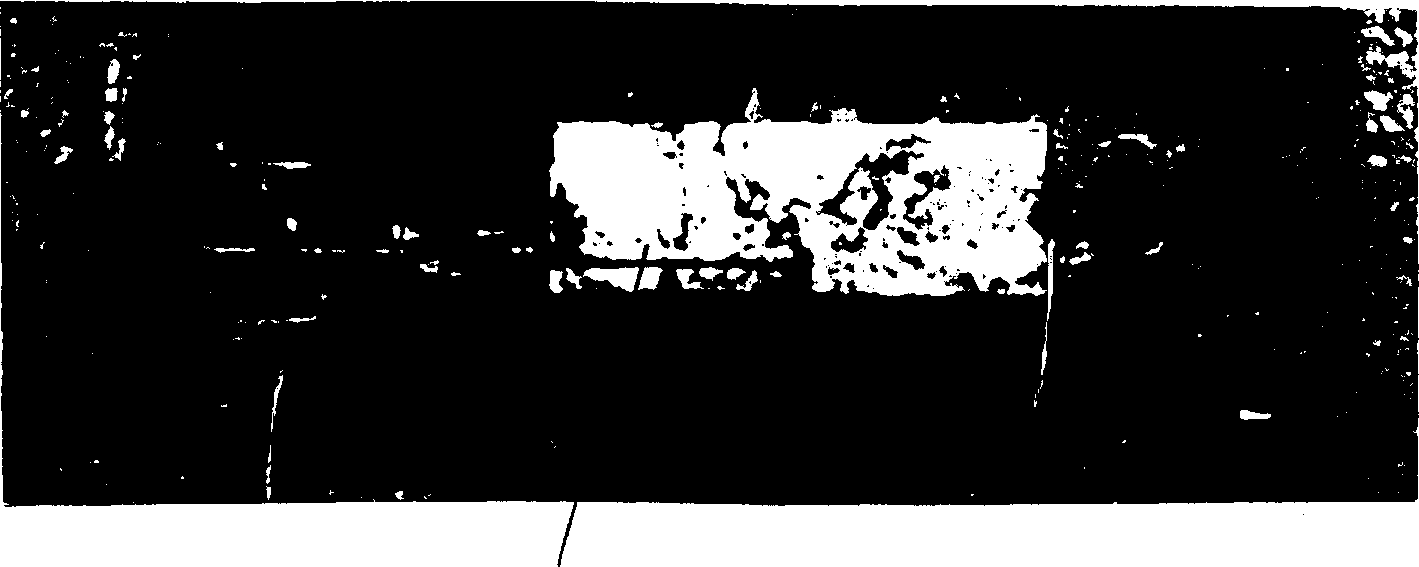
Болтовые отверстия
б) Нижняя поверхность

Обработка под головку болта
Подкладка с высокими ребордами
а) Рабочая поверхность

Паз для постановки клеммного болта Приварные реборды
б) Нижняя поверхность
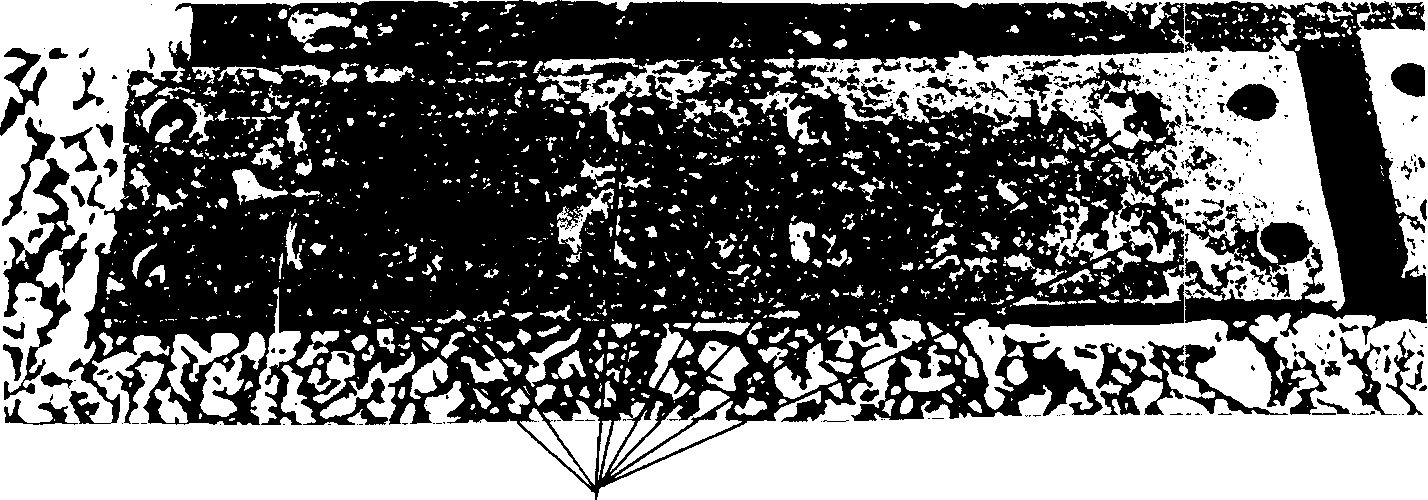
Места приварки реборд
Реборды воспринимают горизонтальную поперечную нагрузку и формируют места для постановки клеммных болтов, которые при такой конструкции работают так же, как и в обычном скреплении типа «К». Возможна постановка упругих клемм типа «Vossoloh».
Испытания подкладок были проведены на Экспериментальном кольце ВНИИЖТ. Во время испытаний по ним было пропущено 300 млн.т бр. Отказов подкладок, связанных с дефектами из-за наличия реборд, не наблюдалось.
Эксплуатационные испытания скреплений с подкладками с приварными высокими ребордами проводились на Северной ж.д.
В табл. 4.3 приведены сравнительные данные по изменению ширины колеи на стрелочных переводах с подкладками с высокими ребордами.
Из данных, приведенных в табл. 4.3 видно, что несмотря на то, что скрепления с высокими ребордами располагались в зонах наибольших возможных расстройств, средние и максимальные зафиксированные за период наблюдений расстройства колеи в этих зонах меньше в 1,2-1,6 раз. чем в прилегающих.
Это обеспечивает снижение расходов и трудозатрат на текущее содержание стрелочных переводов и увеличение сроков службы их металлических частей, а так е существенно повышает безопасность движения поездов по стрелочным переводам.
В настоящее время на Муромском стрелочном заводе освоено серийное производство скреплений с подкладками с высокими ребордами, как для переводов с деревянными брусьями, так и для переводов на железобетонном подрельсовом основании.
Улучшение качества металла для изготовления элементов стрелочных переводов
Стрелочные заводы России обладают необходимыми мощностями и самостоятельно производят высокомарганцовистое и углеродистое литье, необходимое для производства стрелочной продукции.
Таблица 4.3 Изменение ширины колеи на стрелочных переводах с высокими ребордами за период 1995-1996 г.г., мм
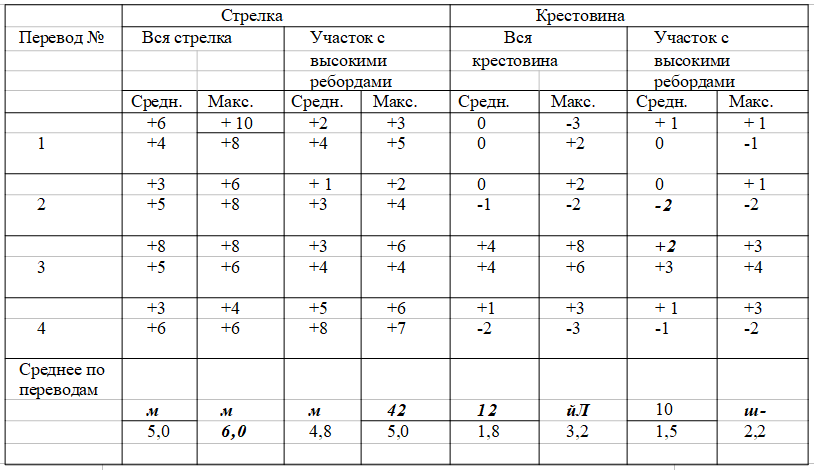
Примечание: числитель — по прямому пути, знаменатель — по боковому пути- зэ- углеродистое литье, необходимое для производства стрелочной продукции
Углеродистое литье производится для изготовления соединительных элементов (вкладышей, упорок и т.д.) и элементов скреплений, высокомарганцовистое для изготовления цельнолитых крестовин и сердечников сборных крестовин.
В связи с тем, что крестовины являются ответственными и быстроизнашивающимися элементами стрелочных переводов, качество высокомарганцовистого литья оказывает существенное влияние на эксплуатационные характеристики стрелочных переводов.
Крестовины стрелочных переводов, как уже указывалось, служат в 2-3 раза меньше стрелки. Продление сроков их службы и улучшение их эксплуатационных качеств может быть достигнуто в значительной степени за счет совершенствования технологии их изготовления.
Известны различные пути решения этой задачи. Как показали исследования ВНИИЖТ наиболее перспективные из них — уменьшение дефектов литья, совершенствование термообработки и увеличение прочностных характеристик рабочих поверхностей.
Важнейший путь улучшения качества литых сердечников крестовин — уменьшение дефектов литья.
Совершенствование технологии литья отливок из высокомарганцовистой стали для сердечников крестовин
Литейные дефекты металла под действием внешних нагрузок быстро и легко развиваются, поражают монолитность металла, что приводит к резкому прогрессивному износу, а в отдельных случаях к развитию трещин, угрожающих безопасности движения поездов /39/.
Высокомарганцовистая сталь обладает примерно в 10 раз большей, чем у рельсовой стали вязкостью, что обеспечивает замедление развития трещин, повышающее безопасность движения поездов. Однако вопрос уменьшения литейных дефектов ‘актуален для отливок из высокомарганцовистой стали, так как высокомарганцовистая сталь, по сравнению с углеродистой, примерно в 4,5 раз более склонна к образованию трещин, усадочных раковин, пор и других несплошностей.
После создания собственного литейного производства на Муромском стрелочном заводе были проведены исследования по существенному повышению качества отливок сердечников крестовин.
Анализ состояния литых сердечников при выходном контроле показал, что наиболее характерными дефектами отливок являются:
Газовая раковина. Это дефект в виде полости, образованной выделившимися из металла или внедрившимися в металл газами. Обычно располагается в пазухах под стыковые накладки, от примыкающих рельсов (у рельсовой головки хвостовика отливки, у подошвы), в желобах, углах, выемках в отливках, сформированных болванами верхней полуформы, с нижней (по заливке) стороны подошвы крестовин, под рЛрами жесткости и перемычками этих отливок, и в других местах. Причинами образования дефекта являются неудовлетворительное качество формовочной смеси (пониженная газопроницаемость, повышенная влажность). Неудовлетворительная вентиляция формы. Неудовлетворительное качество металла (окисленный и газонасыщенный металл). Неудовлетворительная сушка ковша и др.
Песчаная раковина. Дефект в виде полости, полностью или частично заполненной формовочной смесью. Выявляется наружным осмотром, внутренний дефект выявляется после механической обработки, в изломах деталей при периодических испытаниях. Располагается на нижних или верхних (по заливке) поверхностях или в других местах отливки. Рако ‘ина может сопровождаться дефектами: «нарост», «стержневой залив». Причинами образования дефекта являются небрежное исправление формы:
Не удалены остатки смеси при сборке формы. Местное разрушение формы при сборке из-за несоответствия размеров частей формы и стрежня.
Неудовлетворительно прошпилены части формы. Низкая прочность смеси. —
Небрежная сборка и транспортировка форм и др. Усадочная раковина. Дефект в виде открытой или закрытой полости с грубой шероховатой, иногда окисленной поверхностью, образовавшийся вследствие усадки металла. Дефект выявляется наружным осмотром. Може:» быть обнаружен после механической обработки. Внутренний дефект выявляется при периодических испытаниях отливок. Располагается в верхних (по заливке) участках отливки, затвердевающих в последнюю очередь, вблизи питателей, в термических узлах, в массивных частях отливки. Причинами образования этого дефекта могут быть:
Недостаточное питание отливки жидким металлом, несоврешенство литниковой системы, недостаточная подкачка металла при заливке в форму, чрезмерно высокая температура металла и др.
Горячая трещина. Дефект в виде разрыва или надрыва тела отливки усадочного происхождения, возникающий в интервале температур затвердевания. Имеет неровную окисленную поверхность (темно сизо-синего, черного цвета до термообработки отливок). Выявляется наружным осмотром. Дефект располагается на наружных кромках подошвы, ребрах жесткости крестовин, на кромках подошвы переходной зоны, на литых у совиках сердечников, на перемычках литых усовиков или других местах отливок. Причинами образования дефекта могут быть: высокая температура металла при заливке, недостаточная податливость формы, ранняя выбивка отливок, неудовлетворительная раскисленность стали.
Холодная трещина. В отличие от горячей трещины имеет светлую поверхность или цвета побежалости. Располагается на наружных кромках подошвы»ребрах жесткости крестовин, на кромках подошвы переходной зоны, на литых усовиках сердечников, на перемычках литых усовиков или других местах отливки. Причинами образования дефекта могут быть: несоблюдение технологии формовки, преждевременная выбивка отливок, неисправность или чрезмерная жесткость выбивной решетки, механические повреждения отливки при транспортировке (до термообработки), небрежное выполнение операций обрубки (до термообработки).
Термическая трещина. Трещина, обнаруженная после термической обработки отливки, может и не являться собственно термической трещиной, а быть горячей или холодной трещиной, возникающей в отливке до термообработки, но не замеченной до термообработки. При этом,горячие трещины имеют более рваную поверхность со следами крупных кристаллов, а иногда и различными дендритами (во вскрытой трещине). Разделение холодных и термических трещин после термической обработки затруднительно. Причинами образования могут быть: нарушение графика термообработки, неблагоприятная макроструктура стали (транскристаллизация), повышенное содержание углерода и кремния в стали и др.
Коробление. Дефект в виде искажения конфигурации отливки под влиянием напряжений, возникающих по различным причинам, выявляется наружным осмотром и проверкой прямолинейности и плоскости отливок при помощи приспособлений. Располагается по длине (продольное коробление) детали в направлении, перпендикулярном продольной оси детали (поперечное коробление). На отливках сердечников^ встречается коробление в виде «пропеллерности», когда опорные плоскости подошвы отливок в разных ее сечениях развернуты друг относительно друга на различные углы, тем больше, чем больше растяжение между этими сечениями. Причинами образования дефекта могут быть: недостаточная податливость формы, ранняя выбивка отливок, неправильная укладка отливок в садке печи при термообработке, неправильная укладка отливок при вылеживании и др.
Ужимина. Дефект в виде углубления с пологими краями, заполненного формовочной смесью и покрытого слоем металла, образовавшегося вследствие отслоения формовочной смеси при заливке. Располагается на широкой части подошвы переходной зоны, в желобах зоны перекатывание, в пазухах детали (со стороны верхней полуформы, стержней) или других местах, причинами образования дефектов могут быть: неравномерная набивка формы, недостаточная податливость смеси, неудовлетворительная просушка формы и др./7-1/.
В 1989-1991 г.г. брак отливок сердечников различных типов и марок составлял в среднем по году 7-9%.
Выход отливок низших групп качества (3 и 4 груп’йы по ГОСТ 7370-86) составлял 70-75% от общего числа произведенной продукции.
Наибольший процент брака падал на следующие виды дефектов:
- Рыхлоты, обвалы -18,8%;
- Газовые раковины -18,1%;
- Усадочные трещины и раковины -12,5%;
- Засоры -10,3%;
- Уход металла — 7,6%;
- Несоответствие химического состава стали — 7,5%;
- Ужимины — 6,2%;
- Холодные трещины — 5,6%;
- Окисные плены и несплошности — 1,2%.
Другой характерной неблагоприятной особенностью была нестабильность литейного производства. На рис. 4.8 показан выход брака по сердечникам типа Р50 марки 1/11 в течение 1990 г.
Как видно из рис. 4.8 годовые колебания выхода брака по наиболее часто встречающимся дефектам и суммарные по всем дефектам изменяются в несколько раз.
Проведенные на опмгных плавках исследования выявили основные направления работ по снижению дефектности отливок и повышению качества литого металла. Наибольший эффект может быть достигнут за счет:
- улучшения качества подготовки присадочных материалов;
- повышения эффективности раскисления стали;
- дефосфации;
- увеличения интенсивности охлаждения при закалке, ликвидации причин попадания кремнезема в процессе плавки.
Отдельные дефекты могут быть ликвидированы заваркой /54/.
Практическая реализация разработанных направлений улучшения качества высокомарганцовистой стали выражалась во введении комплекса технических мероприятий, которые были проведены в 1994-1997 г.г.
Распределение брака отливок Р50 1/11 по дефектам в течение 1990 г.

—•— засоры —X— газовые раковины —О— рыхлоты, обвалы —*— трещины
За это время были выполнены работы:
- введена прокалка и просушка всех материалов, присаживаемых в период доводки, что снизило газонасыщенность стали;
- повышена эффективность деформации за счет присадки в завалку железной руды и известняка, раннего скачивания шлака плавления;
- повышена эффективность раскисления стали за счет введения предварительного раскисления углеродом электродов с последующей присадкой кускового алюминия в количестве 1 кг на тонну металлозавалки; т
- был изменен состав раскислительной смеси с заменой дробленного ферросилиция на дробленый силикокальций и алюминиевой стружки на порошкообразный алюминий;
- изменен порядок дачи раскислительной смеси для обработки восстановительного шлака: введена дополнительная обработка коксиком в случае простоев, задержек при выплавке;
- произведена модернизация сталеплавильных печей в части внедрения трубчатых водоохлаждаемых экономайзеров й трубчатых сводовых колец, уплотнения рабочих окон. Это позволило устранить перекисление металла вследствие избыточного поступления в печь кислорода воздуха, избежать аварийных плавок с обрушившейся центральной частью свода, повысить устойчивость технологии;
- внедрены вместо шамотных хромомагнезитовые своды, это исключило попадание из свода в шлак во время плавки кремнезема и понижение вследствие этого основности шлака, что отрицательно сказывалось как на удалении фосфора, так и на снижении окисленности шлака;
- произведена модернизация закалочных ванн, что позволило усилить интенсивность охлаждения закаливаемых отливок и исключить появление карбидов подстуживания, снижающих уровень механических свойств стали;
- введен 100% контроль содержания алюминия в готовой стали, что практически исключило случаи его неправильной дозировки.
В результате этих работ, которые были дополнены также организационными мероприятиями, уровень брака отливок по дефектам, начиная с 1995 г. не превышает 1,0-1,7% (рис. 4.9).
Многократно вырос выход высококачественной стали. В настоящее время доля плавок, в которых сталь получена соответствующей наивысшим 1 и 2 группам качества приближается к 90% (см. рис. 4.9).
Выход металла самой низкой 4 группы практически прекратился. i
Значительное повышение качества литья сделало возможным постановку задачи внедрения специальных технологий, повышающих эксплуатационные свойства крестовин.
Высокотемпературная газостатическая обработка сердечников крестовин
Одним из направлений, позволяющих решать в комплексе задачи уменьшения дефектов литья, совершенствования технологии термообработки и увеличения прочностных характеристик рабочих поверхностей является высокотемпературная газостатическая обработка металла.
Эффективность технологии высокотемпературной газостатической обработки достигается за счет обеспечения сталь I и 2 групп по ГОСТ 7370-86 сталь 3 группы ; сталь 4 группы брак-диффузионной пластической деформации металла отливок, которая позволяет залечивать литейные дефекты — несплошности отливок, усадочные трещины и т.д., яв.)«5ющиеся очагами разрушения металла, особенно в зонах повышенного износа.
Процесс залечивания дефектов металла путем диффузионной пластической деформации реализуется за счет использования высоких температур и приложенных постоянно больших давлений. При этом залечивание приповерхностных литейных дефектов происходит путем «жесткого» сдвига поверхностного слоя металла до обеспечения контактирования «берегов» дефекта и их сварки за счет диффузионных процессов. Залечивание объемных дефектов, расположенных внутри отливок, происходит путем вязко- пластического течения металлов в полость дефекта и диффузионных процессов.
Исследования по отработке технологического процесса и режимов высокотемпературной газостатической обработки для сердечников крестовин были выполнены на газостатической установке К-345.
На первом этапе параметры технологического процесса отрабатывались на образцах (топориковых пробах).
Варьировались температура и скорость подогрева, величина давления и время выдержки образцов под давлением в газостатической камере в атмосфере инертного газа, параметры охлаждения и закалки.
Оценка результатов опытов производилась на основании анализа макро и микроструктуры стали и механических свойств. Характеристики изнашивания определялись на установке по схеме ударно-вращательного взаимодействия ролика из бандажной стали и образца, вырезанного из «топорика» высокомарганцовистой стали /5, 72/.
Результаты исследований на образцах показали, что в процессе высокотемпературной газостатической обработки не только происходит залечивание литейных дефектов (раковин, пустот, микротрещин и т.д.). Одновременно с этим макро и микроструктура литой стали 110Г13Л становятся более плотными, неметаллические включения уплотняются и вытягиваются вдоль границ зерен, изменяется субмикроструктура. Все это приводит к увеличению качества высокомарганцовистой стали и повышению ее механических характеристик.
В таблице 4.4. приведены сравнительные результаты испытаний образцов, изготовленных из стали 110Г13Л, прошедшей термическую обработку, и подвергнутых высокотемпературной газостатической обработке по режиму, который на основании вариантных опытов, может быть рекомендован для сердечников крестовин.
Как видно из табл. 4.4 механические свойства образцов в результате высокотемпературной газостатической обработки возрастают. Причем, деформационные характеристики возрастают в 1,18 раз (относительно удлинение) — 1,40 раз (относительное сужение), а ударная вязкость в 1,23 раза. .Относительная величина накопленного износа уменьшается на 19% /51/.
Полученные на образцах положительные результаты дали возможность окончательно уточнить режим обработки для сердечников (его параметры приведены в табл. 4.5) и провести обработку опытной партии сердечников для натурных эксплуатационных испытаний крестовин непосредственно в пути.
Таблица 4.4 Сравнительные результаты испытаний механических свойств образцов из стали 110 Г13Л, подвергнутых различным видам обработки
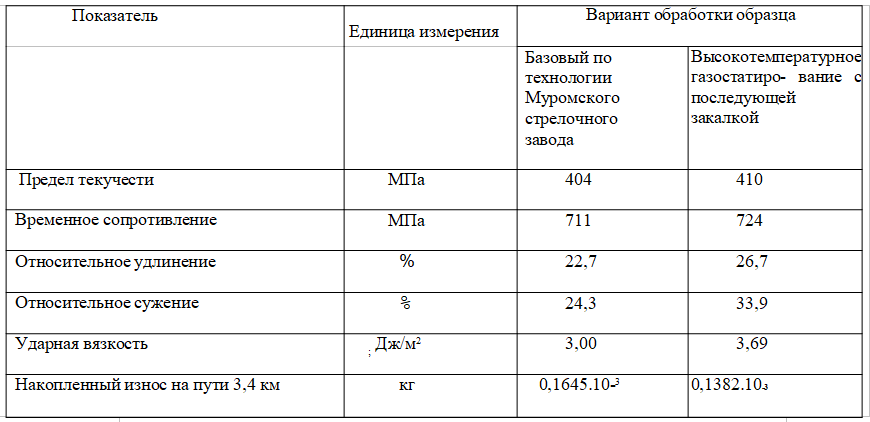
Таблица 4.5 Основные параметры технического процесса высокотемпературной газостатической обработки сердечников крестовин из высокомарганцовистой стали
№ | Параметр | Ед. измерения | Значение |
1. | Температура предварительного нагрева | °С | 700 |
2. | Скорость предварительного нагрева | °С/ч | 100 |
3. | Выдержка после предварительного нагрева | ч | 6 |
4. | Температура обработки | °С | 1150 |
5. | Скорость нагрева до % достижения температуры обработки | °С/ч | 150 |
6. | Время выдержки при 1150° | ч | 3,5 |
7. | Давление в газостате | МПа | 150 |
8. | Температура закалки | °С | 950 |
Для проведения таки испытаний Муромским стрелочным заводом была выпущена опытная партия крестовин типа Р65 марк 1/6 с сердечниками, прошедшими высокотемпературную газостатическую обработку и усовершенствованной конструкцией передней врезки по типу, показанному на рис 3.7.
Две из них проходили испытания на подгорочных путях станции Орехово-Зуево Московской ж.д. и пять на станции Ярославль-Главный Северной ж.д.
На станции Орехово-Зуево одна из опытных крестовин была уложена в голове сортировочной горки на участке с грузонапряженностью 60 млн.ткм/км брутто в год, по ней происходит полный роспуск составов. Вторая опытная крестовина была уложена в средней части горки, по ней происходит роспуск составов с меньшей интенсивностью. Грузонапряженность этого участка составляет 16 млн.ткм/км брутто в год. Скорости движения отцепов до 25 км/ч, скорости при маневровых работах до 40 км/ч.
Общая наработка опытных крестовин пока невелика (крестовина в голове горки пропустила 70 млн.т брутто груза, в средней части 20 млн.т брутто груза), однако более, чем семилетние наблюдения за работой стандартных крестовин на этой станций позволяют провести сравнительную оценку.
Опытная крестовина, работающая в средней части горки, после пропуска 20 млн.т бр.груза не имеет каких-либо дефектов. Наибольший износ в нормируемых сечениях составляет 1,6 мм по сердечнику и 2,4 мм по усовику.
Опытная крестовина, работающая в голове горки, после пропуска 70 млн.т бр. груза имела износ в нормируемых сечениях усовиков 6,1 мм, сердечника 4,3 мм. Рабочая поверхность сердечника этой крестовины имела небольшие выкрашивания глубиной 1 -2 мм в сечениях 12-30 мм, не препятствующие ее дальнейшей эксплуатации. Дефекты возникли после прописка 42 млн.т бр. груза и в дальнейшем не развивались.
Интенсивность износа опытных крестовин после периода наклепа и приработки составила 0,046 мм/млн.т бр. по усовику и 0,032 мм/млн.т бр. по сердечнику. Сопоставление данных по износу с аналогичными для стандартных крестовин показывает преимущество опытных по износу сердечника 28% и по износу усовиков на 18% (см. рис. 4.10).
Заметно преимущество опытных крестовин и по стойкости к поражению дефектами в зоне перекатывания и передней врезке усовершенствованной конструкции.
Многолетние наблюдения за крестовинами, работавшими в тех же условиях, показали, что все стандартные крестовины в процессе эксплуатации поражались контактно-усталостными дефектами в виде выкрашиваний. Средняя наработка до возникновения дефектов в зоне перекатывания составляет около 20 млн.т бр., причем каждая четвертая крестовина поражалась выкрашиваниями уже после пропуска 2-10 млн. т бр. На трех крестовинах возникли трещины в сердечнике, более половины крестовин имели выкрашивания и выколы в передней врезке.
На станции Ярославль-Главный четыре опытные крестовины были уложены в составе глухого пересечения в голове горки и одна после второго замедлителя. За 6 месяцев эксплуатации наибольший износ крестовин в нормируемых сечениях не превысил 4,1 мм. На рабочих поверхностях одной из крестовин имеются небольшие выкрашивания сердечника в сечениях 1—12 мм глубиной до 1 мм. Других дефектов за время эксплуатации не возникло.
Износостойкость типовых и упрочненных высокотемпературной газостатической обработкой крестовин типа Р65 марки 1/6
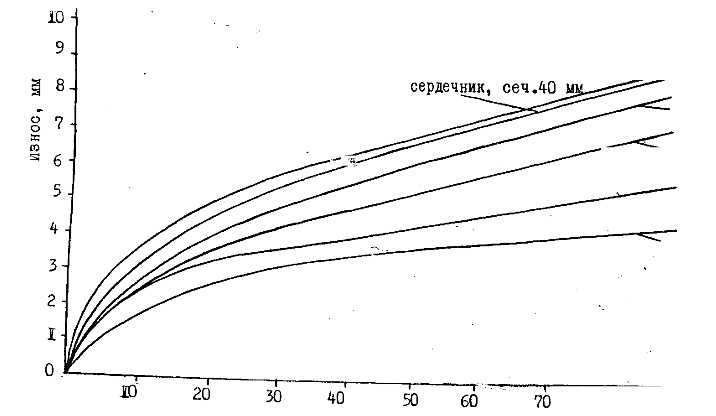
Результаты испытаний крестовин с сердечниками, прошедшими высокотемпературную газостатическую обработку, и передней врезкой улучшенной конструкции показывают, что это целесообразные направления улучшения качества крестовин, дающие повышение эксплуатационных показателей и особенно дефектостойкости /74/.
Выводы по разделу
- Внедрение технологической схемы совместной обработки рабочих поверхностей крестовин позволило снизить вариацию взаимного положения сердечников и усовиков более чем ча 30%, без замены оборудования. Это позволило значительно улучшить условия прохода колесами зоны перекатывания на крестовинах.
В результате вероятность бездефектной работы крестовин на момент нормативной наработки увеличилась на 11,5%. - Замена заклепочных соединений на стрелке и крестовинах с непрерывной поверхностью катания на сварные позволила ликвидировать в эксплуатации дефекты, которые приводили к необходимости замены элементов в пути по причине недостаточной прочности заклепочных соединений, приводивших к преждевременному выходу из строя стрелок и крестовин.
- Усиленные за счет приварных высоких реборд скрепления в значительной мере позволяют увеличить стабильность колеи на стрелочных переводах. Их применение создает возможность’ разрабатывать стрелочные переводы с упругим прикреплением рельсовых элементов к основанию, что уменьшает затраты на текущее содержание пути.
Разработанная на Муромском стрелочном заводе технология отливки сердечников крестовин позволяет увеличить выход сердечников из стали 1 и 2 группы до величины около 90% , в несколько раз снизить брак при литье и повышает безопасность движения поездов. - Применение высокотемпературного газостатического упрочнения металла сердечников крестовин прошло апробацию в пути, показавшую преимущество упрочненных крестовин по износу и дефектообразованию на рабочих поверхностях врезки и зоны перекатывания. На опытных крестовинах преимущество по износу усовиков достигало 18%, сердечников 28%. Полученные результаты позволяют рекомендовать технологию высокотемпературной газостатической обработки к Широкой эксплуатационной проверке.
- Разработка и широкое использование крестовин с приварными рельсовыми окончаниями позволяют использовать высокотемпературную газостатическую обработку для стрелочных переводов массовых конструкций.
Эффективность разработок по повышению качества стрелочной продукции
Основным результатом изложенных в настоящей работе исследований и разработок является создание производственно- технологической базы по выпуску нового поколения стрелочных переводов для российских железных дорог и повышению качества массовой стрелочной продукции.
Практические разработки доведены до возможности обеспечения серийного производства в объемах заказов МПС РФ и промышленности России. Сроки освоения новых видов стрелочных переводов сокращены в 3-5 раз.
Положительные результаты получены по всем трем направлениям совершенствования стрелочной продукции (см. рис. 1.1).
Разработка и внедрение технологии массового производства стрелок повышенной надежности (с гибкими остряками) увеличили вероятность безотказной работы стрелок в 1,1 раза, уменьшили затраты на их текущее содержание на 15-20%.
Переход на производство удлиненных стрелок с остряками, имеющими окончание в виде обычных рельсов, еще более увеличит этот эффект.
Усовершенствование конструкции и технологии изготовления крестовин типа общей отливки сердечника с наиболее изнашиваемой частью усовиков позволило уменьшить поражаемость их дефектами по врезке на 20-60%, по хвостовой части в 2 раза и более.
Применение технологии совместной обработки сердечника и усовиков крестовин увеличивает стабильность качества изготовления рабочих поверхностей крестовин, что приводит к увеличению вероятности их бездефектной работы в среднем на 11,5%, увеличивает срок службы и ремонтопригодность крестовин.
Комплекс мероприятий по совершенствованию технологии литья высокомарганцовистой стали позволил повысить выход высококачественной стали для изготовления сердечников крестовин до 90% от общего объема выпускаемой продукции.
Разработанная технология высокотемпературной газостатической обработки сердечников крестовин повышает износостойкость металла крестовин на 19%, деформационные характеристики на 18-40% и прочностные в 1,23 раза.
Освоение массового производства крестовин с приварными рельсовыми окончаниями позволяет полностью решить проблему заднего стыка крестовины, вплоть до его ликвидации за счет сварки крестовины с примыкающими рельсами, что снизит затраты на текущее содержание стрелочных переводов на 10-15% , увеличит стабильность колеи на крестовинных узлах и повысит безопасность движения поездов.
Включение в состав стрелочных переводов конррельсовых узлов с контррельсами не связанными с ходовыми рельсами дает возможность использовать в качестве ходовых рельсов обычные рельсы и значительно упростить замену в пути ходовых рельсов, в случае возникновения в них дефектов.
Наиболее слабым местом стрелочной продукции российского производства являются скрепления. Разработка сварочных и других необходимых технологий для производства усиленных скреплений, в том числе с упругими прикрепителями, позволяет не только снизить затраты на текущее содержание стрелочных переводов на 25-30%, но и дает возможность разрабатывать и производить стрелочные переводы конкурентоспособные с лучшими мировыми образцами.
Образцом такого стрелочного перевода является стрелочный перевод для путей I и 2 классов. Впервые выпуск новых переводов был освоен на Муромском стрелочном заводе.
Срок создания переводов для путей 1 и 2 классов на базе описанных в настоящей работе технологий, от идеи укладки в главные пути с движением пассажирских поездов, составил всего 7 месяцев.
В настоящее время эти переводы приняты к серийному производству. Их уровень соответствует уровню переводов известных зарубежных фирм. Они успешно конкурируют с переводами австрийского производства на рынках СНГ, не уступая им по качеству и эксплуатационным показателям.
Заключение
На основании выполненных работ можно сделать следующие основные выводы:
- Не менее 65% основных элементов стрелки и до 60% элементов крестовинных узлов получают отказы из-за недостатков конструкции, недостатков технологии изготовления и недостаточной прочности металла.
Причины отказов элементов соединительных путей стрелочных переводов аналогичны причинам отказов элементов перегонных путей, работающих в близких условиях.
Конструкции скреплений, широко применяющихся в настоящее время на типовых стрелочных переводах, не полностью отвечают требованиям эксплуатации и нуждаются в значительном усовершенствовании.
- Основным направлением повышения эксплуатационных качеств стрелок стрелочных переводов, исходя из особенностей их работы в настоящее время, следует считать расширение производства стрелок с гибкими и удлиненными гибкими (с рельсовыми окончаниями) остряками, применение в конструкции стрелок упругих скреплений, башмаков и подкладок с приварными подушками и высокими ребордами, противоугонных устройств в корневой зоне.
В рамках разработок, описанных в настоящей диссертации, созданы технологии изготовления всех этих элементов конструкций, производство подготовлено к серийному их выпуску.
- Для повышения стабильности колеи в зоне соединительных путей целесообразно использовать скрепления с упругими клеммами. Поставка стрелочных переводов, укомплектованных такими скреплениями, может быть осуществлена по заявкам МПС.
- Наиболее перспективное направление повышения эксплуатационных качеств массовых конструкций крестовин — переход к широкому выпуску крестовин с приварными рельсовыми окончаниями, установка в зонах соединения крестовин с примыкающими элементами специальных скреплений с высокими ребордами, применение упругих клемм прикрепления крестовин к подкладкам.
Технологии производства таких крестовин и скреплений разработаны, они могут быть включены, как элементы, в массовыеконструкции и выпускаться серийно.
- Внедрение разработок по повышению качества металла для сердечников крестовин позволило повысить выход отливок с металлом наивысших групп качества (1 и 2 группы) до 90%.
Дальнейшее повышение качества стали, снижение интенсивности износа крестовин и уменьшения их псражаемости дефектами может быть достигнуто за счет расширения применения высокотемпературной газостатической обработки сердечников по технологии, разработанной на Муромском стрелочном заводе, на крестовины массового производства и крестовины с приварными рельсовыми окончаниями.
- Повышение качества крестовин с непрерывной поверхностью катания включает в себя замену заклепочных соединений лафета с подушками на сварные, совершенствование переводного механизма и корневых зон ветвей сердечника.
В тех конструкциях, где это возможно, целесообразно ветвь прямого пути сердечника делать гибкой. Технология изготовления таких крестовин разработана на Муромском стрелочном заводе. Крестовины в настоящее время проходят эксплуатационные испытания на Октябрьской ж.д. Предварительные результаты испытаний крестовин положительные.
- Значительное сокращение затрат на изготовление и замену ходовых рельсов контррельсовых узлов может быть достигнуто за счет применения контррельсов не обязанных с ходовыми рельсами.
Конструкция и технология изготовления контррельсовых узлов с контррельсами не связанными с ходовыми рельсами прошли апробацию в составе стрелочных переводов для путей I и 2 классов. Такие узлы могут быть включены в состав стрелочных переводов массового производства.
- Реализация перечисленных в выводах 2-7 разработок позволяет уменьшить затраты на текущее содержание стрелочных переводов на 25-30% , повысить их надежность и ремонтопригодность.
Список использованных источников
- Абросимов В.И. Неровности на крестовинах Р50 марки 1/11 и динамические силы взаимодействия колеса и рельса // Вопросы пути и путевого хозяйства: Сб. научн. тр. Л.: Транспорт. 1966. С. 15-29.
- Абросимов В.И., Агафонов Г.Ф., Трофимов А.Н., Фролов Л.Н. Скрепления крестовины // Путь и путевое хозяйство. 1993. №8. С.13-14.
- Абросимов В.И., Андреев Г.Г., Трофдмов А.Н., Фролов Л.Н.Донторин В.В. Содержание крестовин с непрерывной поверхностью катания // Путь и путевое хозяйство. 1987. №12, С. 18.
- Абросимов В.И., Даниленко Э.И., Трофимов А.Н., Фролов Л.Н., Агафонов Г.Ф. Крестовина с поворотным сердечником // Путь и путевое хозяйство. 1981. №5. С. 26-28.
- Абросимов В.И., Семенов И.И., Фролов Л.Н., Полетаев В.И., Лисков А.И. Работа контррельсового узла под поездной нагрузкой // Исследование движения экипажей на боковой путь: Сб. научн. тр. Л.: Транспорт. 1971. С. 102-124.
- Абросимов В.И., Трофимов А.Н. Износ сердечников и усовиков // Путь и путевое хозяйство. 1982. №1. С. 14.
- Абросимов В.И.. Тейтель A.M., Трофимов А.Н., Глюзберг Б.Э., Конторин В.В.. Кривошеев C.B. Крестдвина новой конструкции //Путь и путевое хозяйство. 1989. №9. С. 18.
- Альбрехт В.Г., Путря H.H. Дальнейшее совершенствование стрелочных переводов // Железнодорожный транспорт. 1973. № 10. С.67-71.
- Амелин C.B., Абросимов В.И. Исследование упругих неровностей рельсовых нитей-стрелочных переводов с применением ЭЦВМ .Минск -1 // Исследование взаимодействия пути и подвижного состава с применением ЭВМ: Сб. научн.тр. Л.: Транспорт. 1964. С.23-37.
- Амелин C.B., Абросимов В.И., Трофимов А.Н., Фролов Л.Н., Елсаков H.H., Агафонов Г.Ф. Исследование конструкции цельнолитой крестовины типа Р65 марки 1/11 // Вестник ВНИИЖТ. 1978. №8. С. 45-49.
- Амелин C.B., Даниленко Э.И. Конструирование железнодорожных цельнолитых крестовин с учетом прочности // Вестник ВНИИЖТ. 1977. №8. С. 41-45.
- Блурцян Р.Ш., Ларкин A.B., Селихов Г.Ф., Залазинский М.Г. Высокотемпературная газостатическая обработка — новая эффективная технология повышения износостойкости и герметичности литых изделий из высокомарганцовистых и углеродистых сталей // В сб. трудов «Научные достижения Муромских ученых». Владимир. 1997. С. 12 -14.
- Блурцян Р.Ш., Ларкин A.B., Залазинский М.Г., Селихов Г.Ф., Никитин А.М., Блурцян Д.Р. Высокотемпературное газостатическое прессование отливок из высокомарганцоь.истой стали // В сб. «Ресурсосберегающие технологии, связанные с / обработкой материалов давлением». Владимир. 1996. С. 17 -18.
- Блурцян Р.Ш., Селихов Г.Ф., Залазинский М.Г., Ларкин A.B., Никитин А.М., Блурцян Д.Р. Опыт высокотемпературной газостатической обработки отливок из высокомарганцовистой стали // Литейное производство. 1996. № 6, С. 8-9.
- Блурцян Р.Ш., Ларкин A.B., Залазинский М.Г., Никитин А.М., Блурцян Д.Р. Установка и пакет программ для определения технологических остаточных напряжений // Информационный листок № 142 — 94. ЦНТИ. Владимир. 1994. 2 с.
- Блурцян Р.Ш., Ларкин A.B., Селихов Г.Ф., Залазинский М.Г., Никитин А.М., Блурцян Д.Р. Способ изготовления деталей из высокомарганцовистой стали // Информационный листок № 95 — 96. ЦНТИ. Владимир. 1996. 2 с.
- Блурцян Р.Ш., Селихов Г.Ф., Ларкин A.B., Никитин A.B. Высокотемпературная газостатическая обработка ‘сердечников стрелочных переводов // В сб. «Научные исследования института — техническому и культурному прогрессу». Муром. 1992. С. 6.
- Власов В.И., Комолова Е.Ф., Асатуров A.A. Повышение эксплуатационной стойкости железнодорожных крестовин // Пути повышения работоспособности рельсов и крестовин: Сб. научн. тр. М.: Транспорт. 1968. С. 4-18. *
- Воробейчик Л.Я. Стрелочные переводы при повышенной осевой нагрузке // Путь и путевое хозяйство. 1990. №2. С. 15.
- Генкин И.З., Глюзберг Б.Э., Гудков A.B., Теятель A.M., Богородский Н.В. Сварные стрелочные переводы // Вестник ВНИИ ж.-д. трансп. 1997. №3. С. 23-29.
- Глюзберг Б.Э. Исследование воздействия колес подвижного состава на крестовины стрелочных переводов // Вестник ВНИИЖТ. 1977. №2. С.37-39.
- Глюзберг Б.Э. Изменение геометрических форм рабочих поверхностей крестовин стрелочных переводов в процессе износа. М.: ВНИИЖТ. 1983. С.14. (Рукопись деп. в ЦНИИТЭИ МПС, 10 окт. 1983 г., №2407 ж.-д. Д. 83).
- Глюзберг Б.Э. Особенности износа крестовин стрелочных переводов // Вестник ВНИИЖТ. 1984. №3. С. 39-42.
- Глюзберг Б.Э. Напряженное состояние и особенности работы контррельсов стрелочных переводов // Вестник ВНИИЖТ. 1985. №6. С. 49-52.
- Глюзберг Б.Э. Совершенствуется профиль крестовин // Путь и путевое хозяйство. 1991. №7. С. 11 -12.
- Глюзберг Б.Э., Колонина H.A., Тейтель A.M., Крысанов Л.Г. Сроки службы металлических подкладок стрелочных переводов на железобетонных брусьях // Вестник ВНИИЖТ. 1986. №2. С. 46-48.
- Глюзберг Б.Э., Красиков К.И., Титаренко М.И. Особенности наклепа в пути сердечников крестовин из высокомарганцовистой стали 110Г13Л// Вестник ВНИИЖТ. 1984. №7. С. 50-52.
- Глюзберг Б.Э., Наркевич В.В. Стрелочный перевод для горок // Путь и путевое хозяйство. 1989. №12. С.24.
- Глюзберг Б.Э., Путря H.H., Михайлова В.П. Осадка усовкиов и сердечников // Путь и путевое хозяйство. 1983. №11. С.36.
- Глюзберг Б.Э., Радыгин Ю.Н. Новые нормативно- технические документы // Путь и путевое хозяйство. 1997. №12. С.18-19.
- Глюзберг Б.Э., Тейтель A.M., Донец В.Г., Евсенев B.C. Определение вертикальных динамических сил воздействия на остряки стрелочных переводов // Вестник ВНИИЖТ. 1981. №5. С.48-51.
- Глюзберг Б.Э., Тейтель A.M., Титаренко М.И., Хвостик М.Ю., Радыгин Ю.Л. Контррельсы-протекторы // Путь и путевое хозяйство. 1995. №11. С. 12.
- Глюзберг Б.Э., Тейтель A.M., Титаренко М.И., Хвостик М.Ю. Новая конструкция контррельса-протектора // Вестник ВНИИЖТ. 1997. №3. С.29-32.
- Гниломедов В.В., Даниленко Э.И., Мналймов Т.М. Определение сил взаимодействия на крестовинах с различной массой и жесткостью. Л.: ЛИИЖТ. 1983. С. 16.(Рукопись деп. в ЦНИИТЭИ МПС 10 июня 1983 г. № 2328 ж.-д. — Д.83).
- Даниленко Э.И., Абросимов В.И., Трофимов А.Н., Фролов Л.Н., Агафонов Г.Ф. Неровности на крестовинах типа Р65 марки 1/11с непрерывной поверхностью катания и обоснование норм износа // Исследование расчетных характеристик и динамики железнодорожного пути: Сб. научн. тр. Днепропетровск: Транспорт. 1985. С.63-75.
- Даниленко Э.И., Гниломедов В.В., Абросимов В.И. Силовое взаимодействие подвижного состава и крестовин с непрерывной поверхностью катания // Исследование взамиодействия пути и подвижного состава: Сб. научн. тр. Днепропетровск: Транспорт. 1983. С.98-107.
- Данилов В.А., Трофимов А.Н., Агафонов Г.Ф. Результаты эксплуатационных наблюдений за крестовинами с припуском сердечника на наклеп // Вопросы путевого хозяйства: Сб. научн. тр.,Л.: Транспорт 1975. С.75-83.
- Девяткин В.Н., Бескровный Г.Г. О возможности повышения эксплуатационной стойкости литых сердечников крестовин стрелочных переводов // Вестник ВНИИЖТ. 1981. №5. С.51-54.
- Дель Г.Д. Технологическая механика. М.: Машиностроение. 1978.174 с.
- Дитце Х.У., Мюллер Х.П. Меры по уменьшению износа стрелочных переводов // Железные дороги мира. 1991. №4. С.64-65.
- Дусевич В.М. Анализ связи эксплуатационной стойкости железнодорожных крестовин с механическими свойствами высокомарганцовистой стали. М.: ВНИИЖТ. 1985. С. 11 (Рукопись деп. в ЦНИИТЭИ МПС 20 мая 1985 г., № 3144 ж.-д. — Д 85).
- Дусевич В.М. Конструктивная прочность аустенитных сталей для крестовин стрелочных переводов // Вестник ВНИИЖТ. 1985. №8. С. 46-48.
- Елсаков H.H. Изменение норм содержанид крестовин // Железнодорожный транспорт. 1974. №4. С. 65-67.
- Елсаков H.H. Новые нормы содержания крестовин//Путь и путевое хозяйство. 1974. №7. С. 32-34.
- Елсаков H.H. Повышение прочности и долговечности стрелочных переводов // Железнодорожный транспорт. 1978. №6. С. 49-54.
- Елсаков H.H., Белый В.И. Стрелочные переводы ФРГ //Путь и путевое хозяйство. 1979. №8. С. 44-47.
- Елсаков H.H., Крысанов Л.Г. Ширина желоба в горле крестовины // Путь и путевое хозяйство. 1976. №9. С.29-30.
- Елсаков H.H., Петров Ю.Н., Демидов В.П., Ильич A.M. Крестовина для пересечения железнодорожных путей, j ПТКБ ЦП МПС. Авт. св. СССР кл. Е 01 В 7/14, № 652254, заявл. 15.04.77, № 2474347, опубл. 18.03.79.
- Елсаков H.H., Радыгин Ю.Н. Стрелочные переводы колеи 1520 мм // Путь и путевое хозяйство. 1977. №5. С. 15-17.
- Елсаков H.H., Сурин С.О., Демидов В.П., Петров Ю.Н., Глюзберг Б.Э., Путря H.H.,«Донец В.Г. Остряк для соединений и пересечений железнодорожного пути. Авт. св. СССР, кл. Е 01 В 7/00, 7/02 № ‘1273424 опубл. 30.11.86. Бюл. №44.
- Зелинский В.В., Ларкин A.B., Блурцян Р.Ш., Никитин A.M. Результаты исследования износостойкости рабочих поверхностей сердечников стрелочных переводов, подвергнутых высокотемпературной газостатической обработке // В сб. «Наука в ВУЗе». Владимир. 1996. с.23.
- Капур К., Ламберсон Л. Надежность и проектирование систем. М.: Мир. 1980. 604 с.
- Каталог дефектов и повреждений элементов стрелочных переводов. Дополнение к НТД/ЦП-2-93. М.: Транспорт. 1996. 47 с.
- Кац Р.З., Царенко А.Г., Лейцингер A.A., Петров И.А. Заварка дефектов крестовин // Путь и путевое хозяйство. 1988. №6. С.26-27.
- Коган А.Г., Наркевич В.В. Влияние качества металла крестовин на их износостойкость в эксплуатации // Вестник ВНИИ ж.-д. трансп. 1994. №2. С. 25-27.
- Коган А.Я. Вертикальные динамические силы, действующие на путь. М.: Транспорт. 1969. 206 с.
- Коллинз Д. Повреждение материалов в конструкциях. Анализ, предсказание, предотвращение. М.: Мир. 1984. 624 с.
- Коуи Д., Докинс А. Современные конструкции стрелок и крестовин // Железные дороги мира. 1985. №6. С. 51-55.
- Классификация дефектов и повреждений элементов стрелочных переводов. Дополнение к НТД/ЦП-1-93. М. Транспорт. 1996. 10 с.
- Клинов С.И., Кондратьев A.A., Хвостик М.Ю. Высокопрочные болты на стрелочных переводах // Путь и путевое хозяйство. 1993. №4. С.15-17.
- Крагольский Н.В., Добычин М.Н., Камбалов B.C. Основы расчетов на трение и износ. М. Машиностроение. 1977. 526 с.
- Красиков К.И., Беловодский В.Б., Титаренко М.И., Виницкий A.A., Штремель М.А. Зернограничное разрушение, как фактор износа сердечников крестовин из стали 110Г13Л // Вестник ВНИИЖТ. 1985. №1. С. 50-52.
- Крестовины сборные марок 1/11 и 1/9. Основные размеры. ГОСТ 10122-72. М.: Издательство стандартов. 1976. 6 с.
- Крестовины сборные марок 1/11 и 1/9. Основные размеры. ОСТ 32.11-76. М.: ПТКБ ЦП МПС. 1977. 8 с.
- Крестовины сборные марок 1/11 и 1/9. Основные размеры. ОСТ 32.51-63. М.: ПТКБ ЦП МПС. 1982. 9 с.
- Крестовины сборные марок 1/11 и1/9. Основные размеры. ГОСТ 28370-89. М.: Издательство стандартов. 1990. 9 с.
- Крестовины сборнще марок 1/11 и 1/9. Основные размеры. ОСТ 32.89-97. М.: МПС. 1997. Î2 с.
- Крысанов Л.Г., Титаренко М.И. Влияние средних статических осевых нагрузок вагонов на срок службы крестовин // Вестник ВНИИЖТ. 1981. №7. С.52-55.
- Крысанов Л.Г., Тейтель A.M., Глюзберг Б.Э. Взаимодействие колес с крестовиной при изменении характеристик ее основания // Вестник ВНИИЖТ. 1977. №7. С.43-46.
- Кучеренко В.Д. Крестовинам — вторую жизнь // Путь и путевое хозяйство. 1977. №4. С. 13. ‘
- Ларкин A.B., Блурцян Р.Ш., Селихов Г.Ф., Залазинский М.Г. // Способ определения податливости стержневых или формовочных смесей. Авт. св. СССР №1677574. Опубл. 15.09.91. Бюл. №64.
- Ларкин A.B., Блурцян Р.Ш., Селихов Г.Ф., Залазинский М.Г., Никитин A.M., Овсов Н.С.,Пелевин Ю.Ф. Способ изготовления деталей из высокомарганцовистой стали // Пат. РФ №2033436. Опубл. 24.02.93. Бюл. №37.
- Ларкин A.B., Никитин A.M. Стрелочный перевод с усиленными остряками // Путь и путевое хозяйство. 1996. 39. С. 12.
- Ларкин A.B., Никитин A.M., Наркевич В.В. Результаты обнадеживают // Путь и путевое хозяйство. 1994. №5. С.23.
- Лоули Д. Статистический метод анализа. М.: .Мир. 1967.
- Меджи Г. Дефекты рельсов при высоких осевых нагрузках // Железные дороги мира. 1987. №1. С. 29 — 38.
- Методика расчетной оценки износостойкости поверхностей трения деталей машин. М.: Издательство стандартов. 1979. 100 с.
- Митропольский A.K. Техника статистических вычислений. М.: Наука. 1971. 576 с. ^
- Митчел Ф. Стрелочные переводы на железных дорогах США // Железные дороги мира. 1987. №9. С.58-60.
- Михалев М.С., Кац Р.З., Путря H.H. Дефекты крестовин // Путь и путевое хозяйство. 1969. №3. С.38-40.
- Михалев М.С., Путря H.H., Кац Р.З. Причины образования и пути ликвидации дефектов контактной усталости литой части крестовин // Совершенствование конструкции, параметров и качества стрелочных переводов: Сб. научн. тр. М.: Транспорт. 1971 С.39-49.
- Охрименко Я.М., Тюрин В.А. Теория процессов ковки. М.: Высшая школа. 1977. 295 с.
- Пасько C.B., Хорошева H.H. Новый стрелочный перевод // Путь и путевое хозяйство. 1996. № 10. С.7.
- Признаки дефек: ных и остродефектных элементов стрелочных переводов. Дополнение к НТД/ЦП-3-93. М.: Транспорт. 1996.4 с.
- Путря H.H. Улучшение условий эксплуатации крестовин // Вестник ВНИИЖТ. 1965. 3:. С. 29-30.
- Путря H.H., Глюзберг Б.Э., Тейтель A.M., Титаренко М.И. Изменение геометрических и динамико-прочностных характристик крестовин // Вестник ВНИИЖТ. 1980. №4. С. 47-51.
- Путря H.H., Глюзберг Б.Э., Тейтель A.M., Шахов В.И., Петров Ю.Н. Долговечность крестовин с подвижным сердечником // Вестник ВНИИЖТ. 1983. 3№. С. 48-51.
- Путря H.H., Крысанов Л.Г. Стрелочные переводы для грузонапряженных линий // Путь и путевое хозяйство. 1975. №8. С.11-12.
- Путря H.H., Крысанов Л.Г., Елсаков H.H. Улучшение геометрических параметров стрелочных переводов // Железнодорожный транспорт. 1973. №6. С.69-72.
- Путря H.H., Крысанов JI.Г., Тейтель A.M., Глюзберг Б.Э. Стрелочные переводы // Перспективы развития техники путевого хозяйства: Сб. научн. тр. М.: Транспорт. 1976. С. 111-120.
- Путря H.H., Михайлова В.П. Результаты эксплуатационных испытаний крестовин различных типов и марок // Совершенствование конструкции параметров и качества стрелочных переводов: Сб. научн. тр. М.: Транспорт. 1971. С. 35-30. (
- Путря H.H., Тейтель A.M. Крестовина новой конструкции // Путь и путевое хозяйство. 1983. №10. С.27.
- Путря H.H., Тейтель A.M., Крысанов Л.Г. Перспективные крестовины // Путь и путевое хозяйство. 1982. №7. С. 7.
- Путря H.H., Тей ¿ль A.M., Крысанов Л.Г. Динамико- прочностные испытания стрелочного перевода Р65 марки 1/11 с подвижным сердечником // Вестник ВНИИЖТ. 1983. №8. С. 40-43.
- Радыгин Ю.Н. О качестве стрелочной продукции // Путь и путевое хозяйство. 1976. №2. С. 42-43.
- Радыгин Ю.Н. Номенклатура и сроки службы стрелочных переводов // Путь и путевое хозяйство. 1992. №8. С. 38-39.
- Радыгин Ю.Н. Номенклатура стрелочных переводов // Путь и путевое хозяйство. 1994. №10. С. 16-17. !
- Радыгин Ю.Н. Новый стрелочный перевод // Путь и путевое хозяйство. 1995. №5. С.6-8.
- Радыгин Ю.Н., Сурин С.О. Усилен поворотный сердечник // Путь и путевое хозяйство. 1993. 3?. С. 16-17.
- Радыгин Ю.Н., Ткаченко В.Н. Новый стрелочный перевод // Путь и путевое хозяйство. 1994. №5. С. 17-18.
- Рельсы контррельсовые РК50 и РК65. Размеры. ГОСТ 9797-86, ГОСТ 9798-86. М.: Издательство стандартов. 1986. 8 с.
- Рельсы остряковые ОР65. Размеры. ГОСТ 17507-85. М.: Издательство стандартов. 1986. 4 с.
- Решетилов С.И., Донец В.Г. Увеличить срок службы остряков // Путь и путевое хозяйство. 1987. №12. С. 21.
- Рыбкин В.В. Интенсивность износа крестовин стрелочных переводов // Исследование взаимодействия пути и подвижного состава: Сб. научн. тр. Днепропетровск: Транспорт. 1979. С. 84-87.
- Рыбкин В.В. Учет влияния величины динамических сил при оптимизации продольного профиля крестовин // Исследование взаимодействия пути и пйрижного состава: Сб. научн. тр. Днепропетровск: Транспорт. 1981. С. 54 -59.
- Рыбкин В.В., Васильев А.К. Динамические вертикальные силы, действующие на рельс в зоне крестовины // Исследование взаимодействия пути и подвижного состава: Сб.. тр. Днепропетровск: Транспорт. 1982. С.69-74.
- Симон A.A. Анализ работы крестовин // Путь и путевое хозяйство. 1981. №8. С.26.
- Симон A.A. Боковой износ остряка // Путь и путевое хозяйство. 1991. №10. С.35.
- Симон A.A. Сборка и укладка переводов на железобетонных брусьях // Путь и путевое хозяйство. 1992. №11. С. 19-20.
- Симон A.A. Результаты науглероживания крестовин //Путь и путевое хозяйство. 1994. №9. С.6-8.
- Синадский H.A., Генкин И.З., Турбина JI.A., Галунин А.П., Рукавишников Г.Ф., Богорский М.В. Сварка крестовин с рельсами // Путь и путевое хозяйство. 1994. №4. С. 11-14.
- Сливец Д.П. Переводы с железобетонными брусьями надежны // Путь и путевое хозяйство. 1994. №4. С.6-7.
- Сливец Д.П., Крутиков A.M. Профиль и срок службы крестовин // Путь и путевое хозяйство. 1988. №6. С. 18-19.
- Стадниченко A.B. Исследование напряжений в крестовине при воздействии на нее высоких осевых нагрузок // Вопросы взаимодействия подвижного состава с верхним строением пути и искусственными сооружениями: Сб. научн. тр. Днепропетровск: Транспорт. 1977. С. 14-18.
- Стрелочный перевод, допускающий движение на боковой путь со скоростью 220 кшч. Конструкция, укладка, испытания //Железные дороги мира. 1977. №8. С.54-60.
- Стрелочные переводы нового поколения // Железные дороги мира. 1994. №12. С.52-54.
- Сэмба Сеити, Танака Кэндаи. Стрелочные переводы японских национальных железных дорог // Тэнудо сэнро. 1984. №11. С.592-598.
- Стрелочные переводы на железных дорогах Северной Америки // Железные дороги мира. 1993. №11. С.67-70.
- Тейтель A.M. Осадки крестовин с подвижным сердечником // Путь и путевое хозяйство. 1987. №4. С.21.
- Тейтель A.M., Кузьмина И.Г. Соблюдать размеры тупых крестовин // Путь и путевое хозяйство. 1989. №6. С.25.
- Титаренко М.И. Стойкость крестовин при повышенных нагрузках // Путь и путевое хозяйство. 1980. №12. С. 19-20.
- Титаренко М.И. Совершенствуем конструкции жестких крестовин // Путь и путевое хозяйство. 1994. №8. С.23-25.
- Титаренко М.И., Тейтель A.M., Крысанов Л.Г. Сроки службы элементов стрелочных переводов // Путь и путевое хозяйство. 1994. №10. С.18-19.
- Титаренко М.И., Ткаченко В.Н. Влияние отклонений размеров торца сердечника крестовины на его напряженное состояние // Вестник. ВНИИЖТ. 1986. №2. С.44-46.
- Трофимов А.Н., Фролов Л.Н., Агафонов Г.Ф. Испытание крестовин с подвижным сердечником // Путь и путевое хозяйство. 1980. №11. С.26-27.
- Угодников Ю.А., Петров Ю.Н., Радыгин Ю.Н. Стрелочные переводы с железобетонными брусьями // Путь и путевое хозяйство. 1991. №9. С.15-17.
- Фридман Я.Б. Механические свойства металлов. Деформация и разрушение. М.: Машиностроение. 1974. 472 с.
- Фришман М.А., Рыбкин В.В. Методика отыскания рационального профиля крестовин стрелочных переводов II Исследование взаимодействия пути и подвижного состава: Сб. научн. тр. Днепропетровск. Транспорт. 1979. С 40-45.
- Фролов JI.H. Крестовина для высокоскоростного движения поездов с подвижным сердечником и двумя гибкими ветвями // Вопросы путевого хозяйства: Сб.научн. тр. JI.: Транспорт. 1968. С.82-102.
- Шахов В.И., Асатуров A.A., Темиш О.С. Влияние содержания фосфора и режима термообработки на свойства высокомарганцовистой стали для крестовин // Вестник ВНИИЖТ. 1982. №4. С. 42-44. «
- Шахов В.И., Путря H.H., Титаренко М.И., Балленков Б.А. Повышение усталостной прочности сердечников крестовин // Вестник ВНИИЖТ. 1983. №6. С 42-44.
- Шахунянц Г.М. Железнодорожный путь. М.: Транспорт. 1969. 536 с.
- Щетиниин J1.A. Новый стрелочный перевод для горок // Путь и путевое хозяйство. 1988. №12. С.8.
- Яковлев В.Ф. О нормах допустимого износа крестовин при повышении скоростей движения поездов // Железнодорожный транспорт. 1958. №10. С.27-29.
- Яковлев В.Ф., Семенов И.И. Геометрические неровности рельсовых нитей // Вопросы расчета на прочность элементов пути и стрелочных переводов: Сб. наурн. тр. JL: Транспорт. 1964. С.29-67.
- Яковлев В.Ф., Семенов И.И. Исследование упруго- динамических характеристик пути и определение динамических вертикальных сил в крестовине // Вопросы расчета на прочность элементов пути и стрелочных переводов: Сб. научн. тр. Д.: Транспорт. 1964. С.94-105.
- Яковлев В.Ф., Семенов И.И., Абросимов В.И. К оценке сил взамиодействия пути и подвижного состава посредством эксплуатационных измерений траекторий перекатывай![я колес по неровностям пути // Исследование напряженного состояния рельсов и элементов стрелочных переводов: Сб. научн. тр. Л.: Транспорт. 1967. С.27-41. ;
- Янковский А.К. Укладка и содержание стрелочных переводов. М.: Трансжелдориздат. 1939. 138 с.
- Янковский А.К., Шлыгин М.И., Литвин Г.А. Проектирование стрелочных переводов. М.: Трансжелдориздат. 1948. 319 с.
- Appareils de voie // Roilet monde. 1982. №21. P.54-59.
- Busse F. Entwicklung der Weichen der Deutshen Reichsbahn // Signal und Schiene. 1979. №5. P.215-219.
- Davis D., Kalay S., Lo Presti J., Tajaddini A. Advanced turnouts offer life-cycle saving under heavy haul loadings // «Railway Gaz. Int. 1996. №6. P. 345-348.
- Frank E.E. Evolution of the reil-bound mangance frog //Transp. Res. Ree. 1986. № 1071. P.43-48.
- Klauser P.E. Assesing the benefits of Tangential-geometry turnauts // Railway Track and Struct. 1991. № 1. P. 21-23.
- Kramer J. Getting the maximum ont of in turnouts // Railway Track and Struct. 1995. № 7. P. 15-16.
- Kramer J. Worring to improve mainline turnouts // Railway Track and Struct. 1994. №4. P. 16-21.
- Lamek J. Hartovanie powierzehniove iglic lukowych eksploatowanych na PKP// Drogi Kolej. 1991. №6. P. 179-180.
- Lockwood С., Thornton P. Development work on switches and crossings by British Rail //Transp. Res. Ree. 1986. №1071. P.48-56.
- Muller H-P., Shulz P. Einfuhrung von Radlenkern mit kurzen Einlauflangen bei der DR // Signal und Schine. 1980. №4. P. 172-174.
- Oeconomos J. Les nouveaux appareils de voie VIG 60 de la SNCF // Rev. gen. chem. fer. 1987. №3. P.5-13.
- Read D.M. FAST/NAL turnout performance experiment// Bull. Amer. Railway Eng. Assoc. 1990. №728. P.392-401.
- Review and update on performance of frogs, switches, guard rails // Railway Track and Struct! 1978. №9. P.38-39.
- Rousse R. Les appareils de voie aux grandes vitesses // Rev. gen. chemins fer. 1970. №89. P.422-440.
- Srafranski W. Vertical dinamic deformations of railway turnouts //Arch. Civ. Eng. 1995. №2. P.267-299.
- Taylor E.M. Innovations in frog and switch design // Bull. Amer. Railway Eng. Assoc. 1976. №658. P.652-664.
- Webb H.G. A hard look at turnout problems // Prog. Railroad. 1989. №9. P.65.
- Webb H. G. Economics of railway construction and maintenance // Bui. Amer. Railway Eng. Assoc. 1990. №727. P.336-337, 339, 341,343,345-346.
- Zarembski A.M. improved performance from premium turnouts // Railway Track and Struct. 1991. №6. P. 10-11.
- Zarembski A.M. The effects of heavy axle loads on turnout maintenance // Railway Track and Struct. 1995. №4. P. 10-11.