- Введение
- Анализ состояния и основные направления развития технических систем и средств сортировочной станции
- Состояние вопроса
- Анализ конструкций стрелочных приводов
- Эксплуатационно-технические требования к электроприводам сортировочных станций
- Выводы по главе
Цикл статей:
Глава 1 — Введение. Цели и задачи исследований.
Глава 2 — Структурный анализ режимов работы БСП
Глава 3 — Методы защиты стрелочного перевода от ложного контроля
Глава 4 — Методы построения быстродействующих стрелочных приводов
Заключение.
Введение
Внедряемая на сети железных дорог России новая эксплуатационная модель управления перевозками ставит новые технические задачи и предъявляет более жесткие требования к средствам железнодорожной автоматики, уровню их безопасности, надежности и технологическому обслуживанию.
Стрелочные переводы являются неотъемлемой частью верхнего строения пути, обеспечивая организацию перевозочного процесса, и в то же время являются местом повышенной опасности. Многолетний опыт показывает, что применяемые технические средства, методы контроля, технология содержания в полной мере не соответствуют современным требованиям технологичности, безопасности и производительности труда в хозяйстве СПБ.
Сортировочные горки выполняют функцию переработки составов, которая состоит из операций надвига, роспуска, осаживания вагонов на путях сортировочного парка и передачу горочных локомотивов в парк приема. В дополнение к этим операциям возникает необходимость перестановки вагонов локомотивом при скатывании их на «чужой» путь, а также при пропуске через горку подвижного состава.
Среднесуточная переработка на сортировочной горке большой мощности достигает 7000 вагонов, что обуславливает высокую загрузку техники и обслуживающего персонала. Средний интервал между отцепами на вершине горки составляет менее 20 с, число переводов головной стрелки за сутки превышает 1500, а количество отцепов, одновременно движущихся по горловине горки, нередко бывает более пяти. Поэтому механизация и автоматизация сортировки вагонов является насущной необходимостью, без которой невозможно обеспечить увеличения объема и качества формирования составов.
Наибольший эффект может быть достигнут только при внедрении комплексной механизации и автоматизации процесса сортировки вагонов, когда ни одна из технологических операций не задерживает другую. При этом необходимо гармоничное единство передовой технологии, оптимального плана и профиля горки, характеристик локомотивов, устройств механизации и автоматики, чтобы при наименьших затратах обеспечить заданную переработку вагонов.
Электроприводы получили широкое применение в железнодорожной автоматике и телемеханике в качестве базового средства для механизации многих производственных процессов. Большое разнообразие стрелочных электроприводов объясняется разнообразием систем СЦБ, разными эксплуатационно- техническими требованиями, уровнем технологии и элементной базы. Несмотря на большое разнообразие конструкций стрелочных приводов, мировая практика отдает предпочтение электроприводам, хотя, надо отметить, до сих пор есть необходимость в создании быстродействующего стрелочного электропривода, отвечающего в полной мере современным требованиям надежности и безопасности движения поездов.
На базе электроприводов серии СП в 1963 году создан первый быстродействующий электромеханический привод для сортировочных горок серии СПГ, который заменил применяемый до этого электропневматический привод СЭП-55. Увеличение темпа роспуска вагонов и интенсивности работы стрелок, а также внедрение автоматизации управления расформирования составов привели к созданию в 1981 году бесконтактного стрелочного электропривода СПГБ-4, который по быстродействию, безопасности и долговечности превосходил зарубежные аналоги. Интенсивность срабатываний горочного электропривода в сутки достигает 3000.
Анализ отечественных и зарубежных стрелочных электроприводов, внешних замыкателей, контрольных устройств и гарнитуры к ним показывает необходимость перехода на новые материалы и современные технологии производства. Унифицированный подход к построению приводов, гарнитуры, схем управления, контроля и др., не учитывая специфики применения конкретного стрелочного привода, приводит к снижению уровня надежности и безопасности обработки железнодорожных составов. Совмещение различных и прежде всего ответственных функций в одном узле или блоке значительно повышает возможность возникновения и накопления опасных отказов. Увеличение массы и скоростей движения поездов, появление новых конструкций стрелочных переводов из рельсов тяжелых типов с жестко связанными между собой тягами привело к возрастанию динамических нагрузок, практически до опасных значений, и стало одной из причин ограничения скорости движения подвижного состава. Аналитическим исследованиям и практическим решениям задач повышения надежности, безопасности движения поездов и технологической эффективности сортировочной станции посвящена данная работа.
Тенденции развития сортировочных станций, сформулированные требования к функциям, устройствам и технологии средств механизации и автоматизации, доказывают необходимость создания новых быстродействующих стрелочных приводов.
Актуальность работы заключается в:
- разработке алгоритма комплексного контроля различных режимов работы стрелочного перевода, оборудованного быстродействующим стрелочным электроприводом, отвечающего современным требованиям безопасности движения по стрелке.
- корректировке времени перевода и диапазона тяговых усилий, в связи с изменившейся структурой грузопотоков и применением на горках новых марок стрелочных переводов;
- обосновании и разработке конструкторских решений, позволяющих повысить надежность работы электропривода и стрелочного перевода в целом;
Анализ состояния и основные направления развития технических систем и средств сортировочной станции
Стратегия развития горочной автоматической централизации
Внедряемая на сети железных дорог России концепция развития железнодорожного транспорта ставит новые технические задачи и предъявляет более жесткие требования к средствам железнодорожной автоматики, к их надежности, обеспечению безопасности движения, к уровню содержания технических средств, знаний обслуживающего персонала [1,9].
В техническом плане обеспечить выполнение современных требований в хозяйстве СЦБ можно двумя параллельными путями:
- модернизацией существующих технических средств;
- созданием новых технических средств, отвечающих современным требованиям.
Реализация концепции развития средств железнодорожной автоматизации (ЖАТ) в хозяйстве сигнализации, централизации и блокировки (СЦБ) подразумевает:
- внедрение стрелочных переводов, оборудованных внешними замыкателями с непрерывной поверхностью катания (НПК);
- создание новых конструкций стрелочных электроприводов, учитывающих специфику их применения в структуре сортировочной станции и обеспечивающих безопасность движения с необходимыми скоростями;
- использование средств диагностики и двухуровнего независимого контроля состояния и управления стрелочного привода и перевода в целом;
- применение принципиально новых схем установки электроприводов на стрелки, позволяющих разгрузить механизм запирания от динамических воздействий со стороны подвижного состава;
- разработка новых схем управления электроприводами, в том числе бесконтактными, исключающих возможность коммутационных ошибок, исключающих ложный контроль стрелки;
- переход на новые малообслуживаемые технологии и технические средства обслуживания этих устройств в эксплуатации.
Реализация изложенных основных положений концепции позволяет повысить качество переработки отцепов на горке, а также эффективность функционирования сортировочной станции в целом.
Приоритетными направлениями в области эксплуатации стрелочных электроприводов являются:
- модернизация существующих стрелочных электроприводов серии СП с применением современных технологий, материалов и др.;
- создание стрелочных электроприводов на новой элементной базе с расширением технических функций, с применением передовых технологий и последних достижений науки.
Стрелочные электроприводы серии СП применяются в нашей стране с середины 50 годов. Анализ конструкций, поломок и отказов электроприводов данной серии показал, что они морально и технически устарели. За весь период их эксплуатации они не раз подвергались техническим модернизациям, однако современным требованиям надежности, эксплуатации и условиям безопасности движения поездов они не отвечают [10-14].
В связи с изменившейся структурой грузопотоков [15-22], увеличением скоростей движения поездов, изменением жесткости пути (применение железобетонных шпал) и применением «тяжелых» стрелочных переводов (Р65 1/9), целесообразным является корректировка технических характеристик стрелочных приводов, применяемых на сортировочной станции. Повышение уровня безопасности движения и технологической эффективности сортировочной станции может быть достигнуто путем создания новых технических средств железнодорожной автоматики, в частности быстродействующих стрелочных электроприводов с техническими характеристиками, обеспечивающими перспективы расширения эксплуатационных возможностей железнодорожного транспорта.
Анализ конструкций и технических характеристик отечественных и зарубежных стрелочных электроприводов (Приложение 1) показал, что создание абсолютно унифицированного стрелочного привода, не учитывающего специфики его применения нецелесообразно.
Поэтому разработка новых стрелочных приводов, отвечающих современным требованиям эксплуатации, надежности и безопасности движения, должна проводится по трем направлениям:
- стрелочные приводы для работы на скоростных участках пути с внешними замыкателями, включая работу на крестовинах с НПК;
- стрелочные приводы для работы в системе электрической централизации;
- стрелочные приводы для работы в системе горочной автоматической централизации.
Состояние вопроса
Современные требования к функциям, устройствам и технологии работы средств механизации и автоматизации сортировочных станций за последние годы значительно возросли. Для обеспечения процесса управления сортировочной станцией на современном техническом уровне необходимо внедрение комплекса информационных средств, автоматизации и механизации технологического процесса, позволяющего осуществлять работу с системами диспетчерской централизации и контроля станционных и прилегающих участков; электрической централизации, автоматической локомотивной сигнализации, комплексной системы процесса расформирования/формирования составов.
Технические средства механизации и автоматизации сортировочных станций должны обеспечивать:
- выполнение технологического процесса на безопасном уровне;
- повышение степени сохранности вагонов и грузов;
- улучшение показателей рентабельности работы станции;
- повышение производительности труда;
- снижение эксплуатационных расходов;
- повышение пропускной и провозной способности станции.
Технологический процесс сортировочной станции охватывает операции и процедуры от момента прибытия поезда на станцию до его отправления, включая решение следующих вопросов [23-26]:
- организацию работы, в том числе управление станцией, оперативное планирование работы станции и информацию о подходе поездов, организацию технического контроля, учета и анализа работы, вопросов связи;
- технологию работы, в том числе определение наиболее рациональной структуры процесса обработки поездов и вагонов, маршрутов передвижений вагонов и локомотивов, технического и коммерческого осмотра, ремонта вагонов
Реализовать вышеперечисленные задачи невозможно без разработки и внедрения новых технических средств и технологий.
Комплексная система автоматизированного управления устройствами автоматики и телемеханики обеспечивает синхронизацию функционирования всех технических средств, при максимальной автоматизации, что обеспечивает интенсификацию работы сортировочной станции.
Используемые технические средства сортировочной станции, подразделяются на средства механизации и средства автоматизации:
R средствам механизации относятся:
- вагонные замедлители горочные и парковые;
- горочные стрелочные электроприводы;
- компрессорные установки и пневмосети со вспомогательным оборудованием;
- устройства закрепления вагонов в парках станции.
- средства автоматизации сортировочных станций должны быть построены на базе функциональных подсистем, используемых автономно или объединенных в комплексную систему.
Основные функции средств механизации можно разделить по следующим выполняемым категориям:
- управление стрелочным переводом;
- закрепление тележки (колеса) вагона;
- торможение отцепов (вагонов);
- компремирование воздуха.
Задачами, выполняемыми средствами автоматизации являются:
- управление скоростью надвига, роспуска и маневровых передвижений составов и групп вагонов;
- управление маршрутами движения отцепов;
- управление скоростью скатывания отцепов;
- мониторинг за перемещениями вагонов и локомотивов на путях и парках станции;
- управление компрессорной станцией и пневмосетью;
- управление закреплением и освобождением составов;
- контроль, диагностика состояния и обслуживание технических средств автоматизации и механизации сортировочной станции;
- информационный обмен с автоматизированной системой управления сортировочной станцией АСУ СС;
- информационный обмен с системами железнодорожной автоматики и телемеханики.
Выполнение этих задач призваны осуществлять напольные устройства, к которым относятся:
- Устройства контроля участка:
- рельсовые цепи;
- индуктивно-проводной датчик (ИПД);
- счетчик осей;
- комплексная защита стрелки (КЗС).
- Стрелочные приводы;
- Вагонные замедлители;
- Весомеры;
- Измерители скорости;
- Устройства контроля заполнения пути.
Комплексная система автоматизированного управления устройствами автоматики и телемеханики сортировочной станции призвана обеспечивать синхронизацию функционирования отдельных входящих в нее подсистем на основе единой модели управления и базы данных, с целью достижения интегральной эффективности управления. Комплексная система автоматизированного управления устройствами автоматики и телемеханики сортировочной станции должна строиться по блочному принципу и состоять из:
- подсистемы управления скоростью роспуска;
- подсистемы управления маршрутами движения отцепов;
- подсистемы управления маневровыми локомотивами.
При этом она должна обеспечивать выполнение следующих операций:
- непрерывность процедур управления и контроль за операциями обработки составов на станции с момента прибытия поезда до момента отправления вновь сформированных составов;
- малолюдные и безбумажные технологии реализации технологического процесса сортировки вагонов;
- создание единого контрольно-диагностического центра обслуживания аппаратуры;
- создание единой системы АРМов работников станции и обслуживающего персонала, причастных к работе станции линейных предприятий;
- автоматизированная локализация неисправностей и выбор вариантов реконфигурации системы, обеспечивающих непрерывность технологического процесса.
Подсистема управления скоростью роспуска призвана учитывать интервальные ситуации на спускной части горки, включая оперативную коррекцию скорости и остановку роспуска. Расчет скорости роспуска должен осуществляться по результатам измерения и классификации реальных интервалов на стрелках и тормозных позициях спускной части горки с учетом текущего заполнения путей сортировочного парка. Также подсистема должна учитывать результаты расцепа и отклонения фактически реализованного начального интервала от расчетного.
Подсистема управления маршрутами движения отцепов призвана обеспечивать задание и безопасность маневровых маршрутов локомотивов по спускной части горки.
Подсистема управления маневровыми локомотивами призвана информировать о зоне свободности длины пути сортировочного парка по результатам осаживания. Необходимая глубина осаживания оценивается по данным контроля заполнения путей.
Оснащение сортировочных станций новейшими средствами механизации, автоматизации и информатизации позволяет контролировать и проводить весь процесс обработки поездов единым операционным блоком — от прибытия до отправления каждой подвижной единицы.
Современный процесс управления работой сортировочной станцией не мыслим без применения новейших средств автоматизации и информатизации всего комплекса оборудования, задействованного в работе. Важнейшей задачей на данном этапе является внедрение средств диагностики напольного оборудования [27-29] с обеспечением непосредственного контроля и прогнозирования его состояния, позволяющего максимально исключить влияние «человеческого фактора».
Информационные системы [30-32] призваны увеличить скорость работы, более грамотно и четко организовать работу сортировочной станции. Но большое количество напольного оборудования не отвечает предъявляемым требованиям надежной и безопасной их эксплуатации. Налицо разрыв между возможностями информационных и технических средств механизации и автоматизации сортировочных станций.
На рисунке 1.1 представлена блок-схема основных технологических операций осуществляемых на сортировочной станции, управление которыми необходимо реализовать методами автоматизации и механизации, и предполагаемые зоны действия функциональных подсистем управления работой сортировочной станции, отвечающих современным требованиям эксплуатации.
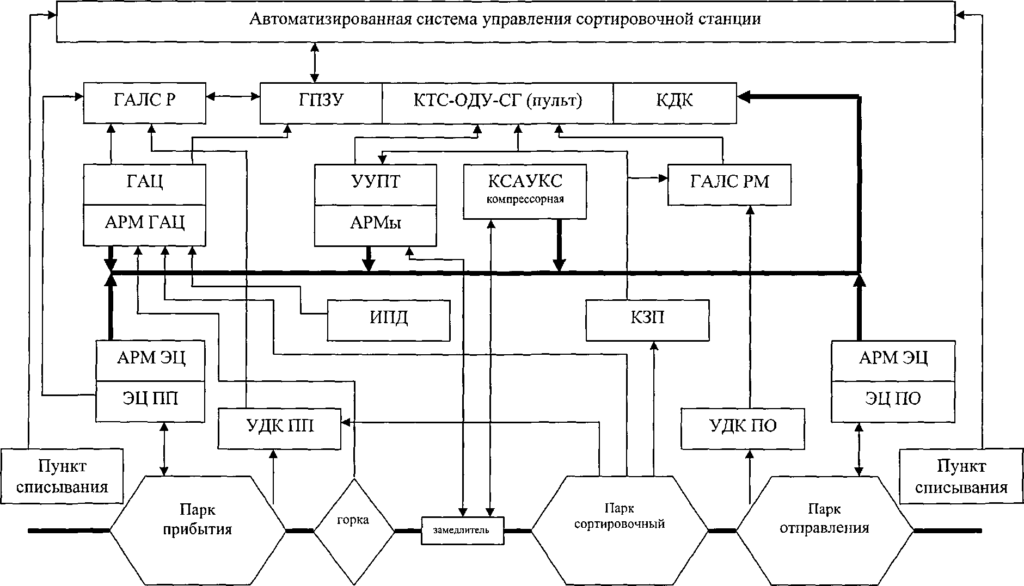
Рис. 1.1. Комплексная система автоматизации процесса расформирования/формирования составов
По функциональным задачам следует выделить следующие системы:
- системы электрической централизации парка прибытия (АРМ ЭЦ, ЭЦ-ПП);
- устройства динамического контроля и идентификации вагонов на путях парка прибытия (УДК-ПП);
- горочная автоматическая сигнализация с передачей информации по радиоканалу и телеуправлением горочных локомотивов (ГАЛС Р);
- горочное программно-задающее устройство, формирующее программу роспуска для систем горочной автоматики в реальном масштабе времени (ГПЗУ);
- горочная автоматическая централизация, обеспечивающая заданные маршруты движения отцепов (ГАЦ — АРМ ГАЦ);
- система автоматизации регулирования скорости скатывания отцепов (устройства управления прицельным торможением) У У ПТ-АРМы;
- система контроля заполнения путей сортировочного парка, обеспечивающая определение координаты точки прицеливания, наличия и протяженности окон между стоящими вагонами, скорость движения отцепов, включая скорость соударения (КЗП);
- система контроля свободности контролируемого участка, обеспечивает фиксацию незанятости участка независимо от типа подвижного состава (индуктивно-проводной датчик) ИПД;
- комплекс технических средств оперативно-диспетчерского управления сортировочной горкой (КТС-ОДУ-СГ);
- контрольно-диагностический комплекс, обеспечивающий контроль функционирования технических средств механизации и автоматизации и их диагностику с прогнозированием пред отказных состояний (КДК);
- комплексная система автоматизированного управления компрессорной станцией (КСАУ КС);
- маневровая АЛС для управления локомотивами в процессе формирования составов (ГАЛС РМ);
- система централизации парка отправления (ЭЦ ПО-АРМ ЭЦ);
- устройства динамического контроля дислокации и идентификации вагонов в парке отправления (УДК ПО);
- системы идентификации входного и выходного вагонопотока (пункт списывания).
Анализ конструкций стрелочных приводов
Одним из важнейших звеньев надежной и качественной работы горочной автоматической централизации является стрелочный перевод, и одной из его составных частей — стрелочный электропривод. Конструкции отечественных и зарубежных стрелочных приводов [33-47], независимо от их назначения и конструкционных особенностей, содержат следующие функциональные блоки (рис. 1.2):
- система управления электроприводом (ЭЦ);
- двигатель (Д);
- редуктор (Р);
- механизм замыкания (ЗМ);
- автопереключатель (АП);
- механизм сравнения положения контрольных линеек и запирающего механизма (МС).
Электрические двигатели по безопасности, надежности, экономичности и другим эксплуатационным показателям имеют значительные преимущества по сравнению с пневматическими и гидравлическими.
Наибольшее распространение получили трехфазные асинхронные электродвигатели с короткозамкнутым ротором [33,48]. В качестве основного источника электропитания для них используется системы электроснабжения станций. Резервным источником обычно служит аккумуляторная батарея с инверторным преобразователем или дизель-генераторная установка, которые позволяют исключить остановку остряка в среднем положении.
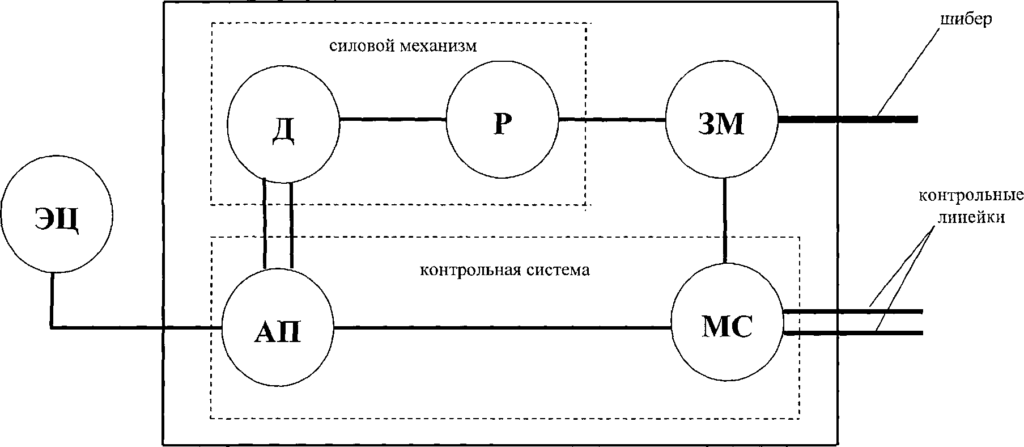
Рис. 1.2. Структурная схема стрелочного электропривода
Основным видом двигателя для быстродействующих стрелочных приводов является электродвигатель.
Для запирания стрелок применяются внешние запирающие механизмы — замыкатели, устанавливаемые внутри железнодорожной колеи, и внутренние, встраиваемые в привод.
Основными видами внешних замыкателей являются крюковые и клиновые, применяемые в Германии, Чехии, Словакии, Венгрии, Польше и в ряде других стран, и шарнирно-упорные, применяемые в частности, у нас в стране. В Бельгии и Франции получили распространение пружинные замыкатели.
Подробно внешние замыкатели проанализированы в [34], поэтому отметим лишь их недостатки:
- уход за ними вследствие расположения их в колее сложен и небезопасен для обслуживающего персонала, что особенно проявляется при интенсивном движении с повышенными скоростями;
- наружная установка приводит к быстрому засорению и, как следствие, к частым заклиниваниям замыкателей;
- тяговые и опорные элементы быстро изнашиваются из-за отсутствия постоянной смазки на трущихся поверхностях;
- для замыкания остряков требуется дополнительная величина хода шибера, необходимого для размыкания и замыкания механизмов внешнего замыкателя и, как следствие большое время перевода стрелки.
Внутренние запирающие механизмы лишены этих недостатков благодаря расположению вне колеи и простоте их герметизации. При этом надежность запирания стрелки через рабочую тягу механизмом, находящимся в самом приводе выше, чем с внешними замыкателями.
Основными видами внутренних запирающих механизмов являются: кулачковые, применяемые в большинстве стран, и пружинные (Франция и Бельгия).
Учитывая изложенное, на сортировочных горках почти повсеместное распространение получило внутреннее запирание электроприводов ввиду их достаточно высокой надежности и устойчивости восприятия внешних климатических и других дестабилизирующих факторов.
В устройствах ГАЦ отсутствует функция замыкания маршрутов, поэтому способ восприятия взреза стрелки или взрезаемость электропривода имеет важное значение. На практике нашли применение как взрезные, так и невзрезные приводы.
Взрезные приводы строятся в основном фиксаторного типа или реже — с гибкой связью. В последних обычно устанавливаются специальные взрезные механизмы (например СПВ-6), или их функции выполняют фрикционные сцепления.
Взрезные приводы с гибкой связью в основном строятся с двумя шиберами, каждый из которых присоединяется к определенному остряку стрелки. Это требует раздельного хода остряков, что вполне допустимо благодаря небольшой длине парковых стрелок. Применение двух рабочих тяг и раздельного хода остряков позволяет отделить запирающее усилие от взрезного. В этом случае запирающее усилие прикладывают к прижатому остряку, а взрезное — к отведенному.
При взрезе стрелки первым всегда перемещается отжатый остряк, преодолевая взрезное усилие привода и затем отпирая прижатый остряк прежде момента начала воздействия на него гребней колес движущегося состава. Применение приводов с раздельным ходом остряков приводит к усложнению конструкции привода, в результате введения отдельно запирающего и взрезного механизмов. Однако по сравнению с фиксаторным у такого привода есть несомненное преимущество: при повреждении врезной пружины стрелка остается запертой.
Взрезной механизм в целях упрощения конструкции привода иногда совмещают не с запирающим механизмом, а с фрикционным сцеплением. В этом случае между валами электродвигателя и фрикциона приходится помещать стопорящий элемент (обгонную муфту, центробежный или храповый тормоз, самотормозящуюся червячную передачу и др.). Следует отметить, что величина усилия взреза в таком приводе сильно зависит от коэффициента трения фрикционных элементов. Кроме того, совмещение взрезного и фрикционного механизмов привода для стрелок, требующих сравнительно небольших переводных усилий, как показали результаты исследования, оказывается невыгодным с точки зрения долговечности самого привода. Это объясняется тем, что величина регулировочного усилия фрикционного сцепления должна быть не ниже величины взрезного усилия. Обычно достаточно, чтобы регулировочное усилие лишь несколько превышало переводное, величина которого значительно меньше взрезного.
Фиксаторные приводы обычно имеют одну рабочую тягу, и поэтому величина взрезного усилия у них устанавливается, исходя из соображений надежного удержания остряков в замкнутом состоянии при проходе отцепов по стрелке. Все без исключения фиксаторные приводы создают это усилие за счет пружин. Следовательно, при усталостной деформации или поломке пружин запирание либо ослабляется, либо отсутствует совершенно, что является серьезным недостатком таких приводов. Однако их преимуществом является простота конструкции за счет совмещения запирающего и взрезного механизмов в одном устройстве.
Анализ различных конструктивных решений взрезных механизмов показывает, что все они обладают определенными недостатками, влияющими как на качество выполнения ими своих функций, так и на качество работы привода в целом. Однако в настоящее время, ввиду проявления опасных последствий взрезов стрелок, на многих сортировочных горках мира применяют взрезные стрелочные приводы.
Связь между электродвигателем и стрелкой может быть как непосредственной (безредукторный привод), так и через редуктор.
Применение в электроприводе редуктора позволяет:
- снизить масса-габаритные размеры привода;
- улучшить компановку, более рационально разместить узлы и блоки;
- повысить унификацию, перейдя на серийные типовые конструктивы двигателя и других стандартизованных узлов;
- получить основные определяющие технические характеристики.
Критерием выбора между редукторным и безредукторным приводом при одинаковом быстродействии и надежности могут служить различные факторы:
- габаритные размеры,
- вес приводов;
- стоимость того и другого.
Сравнение электроприводов по весу и стоимости, принимая во внимание повышенный расход цветных металлов и электротехнической стали, также показывает преимущества редукторного привода. Характерно, что редукторный привод, в частности, за счет быстроходного электродвигателя, имеет более высокий пусковой момент, коэффициент полезного действия и меньший момент инерции.
Таким образом, преимущества редукторного привода над безредукторным позволяют сделать вывод о том, что быстродействующий стрелочный привод (БСП) целесообразно выполнить по схеме «электродвигатель — редуктор — стрелка» (ЭД-Р-С).
Контактный автопереключатель, используемый в стрелочных электроприводах серии СП, обладает рядом недостатков, что делает его применение в конструкциях быстродействующих стрелочных электроприводов проблематичным. Совмещение функций контроля и переключения силовой цепи отрицательно сказывается на надежной работе привода в целом.
Наиболее характерными причинами отказов контактного автопереключателя являются — подгорание, механический износ или излом контактов, их обледенение или индевение, поломка контактных колодок или пружин автопереключателя [11-14]. Следует также отметить сложность ухода и регулировки автопереключателя [48, 49]:
- необходимость поддержания заданного контактного давления;
- наличие частых разрегулировок;
- удаление металлической пыли, образующейся в следствии износа контактных пружин и др.
Значительный износ, как следствие большого среднесуточного числа переводов стрелок, восприимчивость к воздействию климатических факторов ввиду напольных условий работы электроприводов и т.п. свойственны любым контактным системам автопереключателей.
Уменьшение числа контактов автопереключателя до минимума и передача их функций реле схемы управления стрелкой приводит к увеличению числа проводов между постом централизации и стрелочным электроприводом, и, в целом, не повышает надежности устройства.
Повышение надежности и долговечности автопереключателя можно достигнуть разделением функций контроля и коммутации и использованием бесконтактных датчиков. Назначенный ресурс бесконтактного переключателя больше, чем у контактного не менее чем в 10 раз [50, 51], колебания температур не препятствуют его функционированию, эксплуатационные расходы минимальны. Переключение электродвигателя должно обеспечиваться схемой и происходить на посту.
Особенностью контроля положения остряков стрелочного привода для горочной автоматической централизации является контроль крайних положений остряков. Остановка остряка в промежуточном положении недопустима из- за непрерывного движения отцепов при роспуске составов.
Поэтому контрольная система быстродействующего стрелочного привода для ГАЦ должна быть следящего типа и строиться на базе бесконтактного датчика контроля положения остряков.
Вопрос снижения воздействия остряка на рамный рельс в конце перевода стрелки практически никогда не рассматривался. Считалось, что увеличение усилия в конце перевода стрелки возникает только при попадании постороннего предмета между остряком и рамным рельсом либо, если не выдержана ширина колеи. Проведенные исследования силовых характеристик отечественных стрелочных приводов позволяет говорить о том, что из-за конструктивных особенностей замыкающих механизмов наблюдается увеличение усилия прижатия остряка к рамному рельсу в конце перевода стрелки [52, 53]. Кроме того, запасенная энергия движущихся масс привода и стрелки оказывает негативное воздействие на рамный рельс (отжим). Причем чем больше скорость перевода остряков, тем больше оказываемое негативное воздействие. Все это приводит к преждевременному износу деталей привода, гарнитуры, отжиму рамного рельса и, в конечном итоге, к нештатной ситуации.
Впервые в отечественных стрелочных электроприводах серии ВСП, за счет специальной конфигурации кулачков механизма замыкания и применения демпфирующих устройств исключено воздействие на рамный рельс со стороны остряков в конце перевода стрелки. Недостатком этого технического решения является сложность, высокая точность изготовления кулачков и необходимость периодическои регулировки демпфирующих устройств.
В быстродействующих стрелочных электроприводах вопрос гашения кинетической энергии движущихся масс в конце перевода стрелки стоит чрезвычайно остро, и поэтому решение данной проблемы особенно актуально.
По характеру возникновения отказов технических средств их подразделяют на:
- внезапные, возникающие в следствие скачкообразного изменения одного или нескольких заданных параметров объекта;
- постепенные, возникающие из-за плавного изменения параметров объекта.
Из-за непредвиденного скачкообразного возникновения внезапных отказов их невозможно предсказать. Напротив, постепенные отказы в силу длительного влияния причин их возникновения и плавного, постепенного изменения характеристик объекта, приводящего к его отказу, предсказать можно. Таким образом, в отличие от внезапных отказов, прогнозирование постепенных отказов возможно. Прогнозирование постепенных отказов позволяет предупредить их возникновение с помощью применения современных средств диагностики и профилактического ремонта, и тем самым увеличить наработку на отказ эксплуатируемых устройств.
Устройства СЦБ отличаются от других технических средств высокой ответственностью за обеспечение безопасности движения поездов, поэтому для них принято выделять особый класс отказов — опасные отказы [50, 54^-56]. К таким отказам относятся — получение ложного контроля или неконтролируемый выход из строя элементов, обеспечивающих безопасность движения поездов.
Основой системы технического обслуживания устройств СЦБ на отечественных железных дорогах являются периодические работы по осмотру, проверке и регулировке устройств. В ближайшей перспективе — диагностика технического состояния объекта, что позволит перейти от регламентных работ к ре- монтно-восстановительным методам обслуживания по состоянию.
Изменения в техническом обслуживании подразумевают:
- увеличение периодичности обслуживания;
- внедрение элементов восстановительного обслуживания;
- диагностика состояния с необходимым ремонтом.
Повышение надежности работы стрелочного привода и стрелочного перевода в целом достигается за счет:
- обоснования периодичности проверок и ремонта;
- повышения безотказности устройств;
- введения непрерывной диагностики состояния привода и всего стрелочного перевода в целом.
Эксплуатационно-технические требования к электроприводам сортировочных станций
Электропривод
Электропривод является частью комплекса стрелочного перевода и предназначен выполнять следующие функции:
- создание достаточного усилия и необходимой величины хода шибера для перевода остряков стрелки из одного крайнего положения в другое, а также из среднего в любое крайнее.
- надежное замыкание шибера в крайних положениях в сторону, противоположную предшествующему движению, и обеспечение свободного хода замкнутого шибера в сторону ближайшего рамного рельса на нормированную величину;
- обеспечение неизменными силовых факторов замкнутого шибера в статическом (пассивном) режиме эксплуатации, а также в динамическом режиме при проходе неограниченного числа подвижного состава по стрелке с установленной скоростью до полной выработки своего нормированного ресурса;
- обеспечение постоянного и достоверного контроля положения остряков стрелки, механизма замыкания шибера, состояния взреза, целостности и исправности силовой и контрольно-механической связей и электрических цепей;
- для взрезных электроприводов — сохранение целостности и работоспособности узлов и деталей электропривода и гарнитуры при взрезе стрелки, предсказуемость и наглядность последствий взреза стрелки при обеспечении устойчивости подвижного состава против выдавливания колесной пары из колеи;
- обеспечение исправного работоспособного или защитного состояний независимо от времени суток, погодных условий и других внешних дестабилизирующих факторов.
В зависимости от восприятия взреза стрелки электроприводы делятся на два варианта исполнения:
- взрезной;
- невзрезной.
Электроприводы должны разрабатываться, как правило, с электродвигателями переменного тока, т.к. они обладают рядом преимуществ перед остальными типами двигателей.
Электроприводы должны иметь возможность регулировки усилия в пределах необходимых для перевода стрелки и ограничения усилия передаваемого на шибер, исключающих изгиб остряков при замыкании шибера в случае попадания посторонних предметов между остряком и рамным рельсом.
Электроприводы специального назначения, усилие перевода шибера которых не превышает 4000 Н, могут не иметь устройства регулировки передаваемого на шибер усилия. При этом работа электропривода на упор (фрикцию) должна ограничиваться интервалом времени, обеспечивающим автовозврат остряков, т.е. равным двойному времени перевода, и отключаться схемой управления.
Электропривод при воздействии механических нагрузок и климатических факторов должен соответствовать требованиям для классификационных групп МС4 и К4 [57].
Электропривод должен удовлетворять требованиям габарита приближений строений «С» и обеспечивать существующие строительные нормы по установке стрелки в междупутье.
Установка электропривода на стрелку, как правило, должна осуществляться на специальные полосы (каркас), не имеющие прямого крепления с рамными рельсами, что позволит снизить динамические воздействия при движении поездов и улучшить изоляцию рельсовых цепей.
Прочностные параметры звеньев силовой цепи электропривода должны обеспечивать механическую устойчивость в рабочем и динамическом режимах, обеспечивать сохранность кинематической цепи, быть предсказуемыми при воздействии максимальных нагрузок при проходе подвижного состава, не допускать остаточных или сверхнормативных упругих деформаций или смещений отдельных звеньев, корпуса привода и несущего каркаса.
Для повышения безопасности движения поездов, получение достоверного контроля стрелки достигается применением независимой двухуровневой системой контроля фактического положения остряков с распределенными контрольными точками, и передачей информации на пост ЭЦ двумя независимыми каналами, где:
- 1-й уровень — контрольная система электропривода на базе автопереключателя (контактного или бесконтактного);
- 2-й уровень — контрольно-диагностические устройства — датчики положения остряков, аналоговые бесконтактного типа, устанавливаемые на стрелочном переводе в точках, распределенных по длине остряков;
- диагностика основана на контроле изменения фактического положения остряков стрелки относительно рамного рельса при проходе подвижного состава по стрелке, а также на изменении положения остряков в процессе перевода стрелки.
Электропривод должен ограничивать динамическое воздействие остряка на рамный рельс в конце перевода за счет снижения скорости движения шибера (торможения) вплоть до полной его остановки в конечной точке, не допуская динамических ударов остряка о рамный рельс.
Конструкция электропривода должна обеспечивать возможность замены отдельных блоков в условиях эксплуатации без снятия электропривода со стрелочного перевода.
Электроприводы для маневровых районов
- электропривод должен обеспечивать перевод остряков в интервале времени 1,5-3,5 секунды;
- номинальное усилие перевода должно быть не более 4000 Н;
- схема управления электроприводом должна предусматривать наряду с управлением от ЭЦ и управление от поста (колонки) местного управления стрелками;
- скорость движения по таким стрелкам должна быть ограничена до 60 км/ч.
Электроприводы горочной централизации
Конструкция электропривода ГАЦ должна включать в себя:
- силовой механизм;
- механизм фиксации и удержания шибера;
- автопереключатель;
- вспомогательные устройства;
- механизм взреза (для взрезного варианта исполнения);
- устройство демпфирования кинетической энергии вращающихся и поступательно движущихся масс в конце перевода.
Электропривод ГАЦ должен обеспечивать надежную фиксацию и удержание шибера в крайних положениях.
Электропривод ГАЦ должен иметь автопереключатель бесконтактного типа.
Электропривод ГАЦ должен иметь конструкцию блочного типа.
Конструкция электропривода ГАЦ должна обеспечивать демпфирование кинетической энергии движущихся масс и снижать их воздействие через остряки на рамный рельс, а также обеспечивать безударную работу всего механизма в конце перевода.
Электропривод ГАЦ должен обеспечивать перевод остряков за время не более 0,5 секунды.
Максимальное усилие перевода должно быть не более 4000 Н.
Электропривод ГАЦ должен иметь защиту электродвигателя и силового механизма при работе на упор (фрикцию). Время работы на упор должно быть ограничено (не более 0,8 с), по истечении которого электропривод автоматически (схемное решение) должен быть переведен в обратное крайнее положение (автореверс). Полное время перевода с функцией автовозврата стрелки должно составлять не более 1,2 секунды.
Наличие фрикционной муфты в электроприводе ГАЦ не обязательно.
При оборудовании стрелок контрольно диагностическим устройством (КДУ) наличие контрольных линеек в электроприводах ГАЦ не обязательно.
Контрольно-диагностическое устройство стрелки (КДУ)
Развитие современной техники и технологий позволяет осуществлять комплексную диагностику и контроль состояния привода и стрелочного перевода в целом. Все электроприводы должны работать в комплексе с контрольно- диагностическими устройствами стрелок (далее КДУ). Контрольно- диагностическое устройство стрелок предназначено выполнять следующие функции:
- контроль фактического положения прижатого и отведенного остряков по отношению к рамным рельсам в пределах установленных нормативных зазоров в данной контрольной точке [48];
- контроль целостности прижатого остряка на случай его излома как минимум в 2-х точках;
- контроль и диагностика изменения зазора между остряком и рамным рельсом при проходе подвижного состава;
- контроль и диагностика величины суммарного зазора в шарнирных соединениях гарнитуры;
- контроль и диагностика уширения колеи;
- контроль и диагностика ослабления крепления рамных рельсов.
Контрольно-диагностическое устройство стрелки не должно требовать обогрева в зимних условиях.
Конструкция КДУ должна быть максимально унифицирована с учетом типов рельсов, марки стрелочного перевода и возможности различных конфигураций схемы контроля на стрелке.
Контрольно-диагностическое устройство стрелок должно находиться вне электропривода.
Выводы по главе
- Анализ условий эксплуатации и требований к уровню автоматизации, механизации и информатизации сортировочных станций доказывает актуальность задачи создания нового быстродействующего стрелочного электропривода, характеристики которого отвечали бы требованиям надежности и безопасности движения поездов.
- По результатам эксплуатации быстродействующих стрелочных электроприводов типа СПГБ установлено, что их надежность не отвечает современным требованиям эксплуатации и безопасности движения поездов по стрелке, что снижает технологическую эффективность сортировочной станции.
- Рассмотренные конструкции электроприводов и стрелочных переводов не имеют диагностики технического состояния, что допускает возникновение неконтролируемых отказов. Применение диагностических устройств обеспечит качественно новый подход к контролю электропривода и стрелочного перевода, как единого технического комплекса, что особо актуально в современных условиях эксплуатации.
- Анализ стрелочных приводов (Приложение 1) свидетельствует о большом разнообразии как конструкций в целом, так и конструктивных решений отдельных узлов. Рассмотренные технические решения являются достаточно сложными, дорогостоящими и ни одно из них в полной мере не отвечает требованиям надежности и безопасности, предъявляемым к быстродействующему стрелочному электроприводу.
- Требования, предъявляемые к конструкции быстродействующего стрелочного привода должны обеспечиваться синтезом следующих условий:
- требуемое быстродействие;
- надежное запирание прижатого остряка к рамному рельсу при самых неблагоприятных условиях эксплуатации;
- исключение возможности остановки остряка в среднем положении при возникновении внештатных ситуаций;
- надежный контроль крайних положений стрелки;
- диагностику состояния электропривода и стрелочного перевода;
- уменьшение времени восстановления работоспособности электропривода при взрезе стрелки;
- оптимизацию конструкции и масса-габаритных показателей электропривода;
- продление срока службы стрелочного привода и стрелочного перевода в целом.