- Определение механических свойств и ударной вязкости
- Определение прокаливаемости сталей различных марок
Цикл статей:
Глава 1 — Введение. Цели и задачи исследований.
Глава 2 — Анализ причин отказов стрелочных переводов и их элементов
Глава 3 — Материалы и методика исследования
Глава 4 — Сравнительные исследования комплекса физико- механических свойств остряков из сталей марок 76хсф и м73в
Глава 5 — Разработка технологических основ двухстороннего поверхностного упрочнения остряков
Глава 6 — Работы по промышленному внедрению стали 76ХСФ и технологии двухстороннего термического упрочнения остряков
Исследуемые марки стали
В настоящей работе выполняли исследования остряков, изготовленных из серийной М73В и опытной 76ХСФ марок сталей. Сталь серийной марки выплавлена на ОАО «КМК» мартеновским способом. Сталь марки 76ХСФ для опытной партии остряков в количестве 60 т выплавлена на ОАО «КМК» в электропечи. Прокатка остряковых рельсов осуществлялась по типовой технологии комбината. Химический состав исследуемых в данной работе сталей приведен в табл. 2.1.
Определение химического состава сталей
Химический состав исследуемых сталей определяли методом спектрального анализа на установке «Spectro Lab S». Количество точек на каждом исследуемом образце — не менее трех.
Исследование макро- и микроструктуры
Исследование макроструктуры проводилось путем травления поперечных темплетов остряков толщиной 15-20 мм в 20 %-ном водном растворе №\Юз. При изучении макроструктуры дополнительное увеличение не применялось.
Исследование микроструктуры опытных и серийных остряков проводилось на образцах, вырезанных из поверхности и середины головки и подошвы механической резкой без прижогов, после их травления в 4%-ном спиртовом растворе НЫОз в течении 20 с. Микроструктуру упрочненных и неупрочненных зон головки и подошвы остряков изучали при увеличении 500 на световых микроскопах МИМ — 8М и «(Зиапйп^ 520». Тонкое строение микроструктур сталей 76ХСФ и М73В изучали при увеличениях 4000 и 10000 на сканирующем электронном микроскопе «СатеЬах».
Содержание элементов, масс. % | ||||||
С | Мп | Si | S | Р | Сг | V |
0,76 | 0,74 | 0,54 | 0,011 | 0,017 | 0,48 | 0,07 |
0,70 | 0,96 | 0,37 | 0,025 | 0,012 | 0,06 | 0,04 |
Исследование твердости
Определение твердости поверхности катания остряков проводили по методу Бринелля с нагрузкой 30000 Н в соответствии с ГОСТ 9012-59 «Металлы. Метод измерения твердости по Бринеллю». Твердость определяли по средней линии поверхности катания остряка. Для удаления окалины и обезуглерожен- ного слоя место определения твердости зачищалось на глубину около 0,5 мм без прижогов.
Твердость по сечению остряка определяли на поперечных темплетах, изготовленных механической резкой из различных сечений. Замер твердости проводили на глубину до 20 мм по оси и радиусам боковых выкружек головки рельса. Замер твердости в подошве остряка, подвергнутого двухсторонней закалке, проводили на глубину до 20 мм в направлении, перпендикулярном нижней поверхности подошвы остряка. Расстояние между отпечатками 1 мм. Определение твердости в поперечном сечении головки и подошвы остряка проводили методом Роквелла с нагрузкой 1500 Н по шкале НЕ1С (ГОСТ 9013-59 «Металлы. Метод измерения твердости по Роквеллу») и методом Виккерса с нагрузкой 100 Н (ГОСТ 2999-75 «Металлы. Метод измерения твердости по Виккерсу»). Для оценки твердости отдельных структурных составляющих проводили микродюрометрические исследования на приборе измерения микротвердости ПМТ-З с нагрузкой 0,5 Н.
Определение механических свойств и ударной вязкости
Механические свойства определяли при испытании на растяжение цилиндрических образцов диаметром 6 мм пятикратной расчетной длины в соответствии с требованиями ГОСТ 1497 — 73 «Металлы. Метод испытания на растяжение» на разрывной машине иТ8-100.
Динамические испытания на ударную вязкость проводили на маятниковом копре КМ-03 мощностью 300 Дж при температуре +20 °С. Образцы изготавливали вдоль направления прокатки из упрочненных слоев головки и подошвы остряка и сердцевины головки. Требования к образцам по ГОСТ 9454-78 «Металлы. Метод испытания на ударный изгиб при пониженных, комнатной и повышенных температурах»: размер образца 10x10x55 мм, и — образный надрез глубиной 2 мм и радиусом закругления 1 мм.
Образцы для определения механических свойств и ударной вязкости вырезали вдоль направления прокатки из упрочненных слоев головки и подошвы остряков на расстоянии до 8 мм от поверхности и из шейки остряков.
Определение прокаливаемости сталей различных марок
Экспериментальный метод определения прокаливаемости сталей
Прокаливаемость сталей марок 76ХСФ и М73В определяли методом торцовой закалки по ГОСТ 5657 — 69 «Сталь. Метод испытания на прокаливаемость» на цилиндрических образцах диаметром 25 мм и длиной 100 мм. Перед изготовлением образцов заготовки были подвергнуты нормализации при температуре 850 °С. Перед закалкой образцы были нагреты в печи до температуры 850 °С (температура нагрева под закалку сталей исследуемых марок). При нагреве торец образца, подлежащий охлаждению водой, предохранялся от окисления и обезуглероживания слоем графита. Время выдержки образцов в печи при температуре 850 °С — 30 мин. Охлаждение торцов проводилось в течении 5 мин.
Для замера твердости по всей длине закаленных образцов сошлифовы- вали две диаметрально противоположные площадки на глубину 0,5 мм. Замер твердости проводили по Виккерсу с нагрузкой 100 Н.
Расчетная методика определения прокаливаемости сталей
Оценку прокаливаемости сталей марок 76ХСФ и М73В в условиях охлаждения остряков сжатым воздухом проводили по специально разработанной методике, включающей следующие этапы [107]:
1. Аналитический расчет распределения скоростей охлаждения по сечению головки и подошвы остряка путем решения дифференциального уравнения теплопроводности Фурье конечно-разностным методом с применением ЭВМ.
Исходные данные и допущения при расчетах были приняты следующими:
- Учитывая сложность геометрии поперечного сечения остряка и изменение сечения по длине остряка, расчет проводился для поперечного сечения в нестроганной части.
- Реальное сечение головки остряка моделировалось цилиндром диаметром 64 мм, сечение подошвы — пластиной толщиной 20 мм (рис. 2.1). Расчет проводился для головки и подошвы остряка с учетом различной интенсивности их охлаждения, т.е. моделировался режим двухсторонней закалки.
- Ввиду преобладающего превышения длины остряка над размерами элементов его поперечного сечения в расчетах использовали условия одномерного теплового потока, пренебрегая влиянием теплообмена со стороны торцов остряка. Направление теплового потока перпендикулярно продольной оси симметрии изделия.
- Температуры охлаждающего воздуха была принята постоянной и соответствующей 20°С.
- Интенсивность охлаждения характеризовалась эффективными значениями коэффициента теплоотдачи, которые составили 750 и 500 Вт/(м^-К) для головки и подошвы соответственно (скорости потока воздуха 80 и 60 м/с соответственно) [108].
- В расчетах использовали скорость охлаждения стали в интервале от температуры, близкой к равновесной точке A¡, до температуры минимальной устойчивости аустенита, т.е. в интервале 720-550°С применительно к углеродистой (М73В) и низколегированной (76ХСФ) сталям.
- Температура нагрева перед началом охлаждения принята 850°С. Для простоты расчета рассматривается сквозной нагрев цилиндра (теплотехническая модель головки остряка) и пластины (теплотехническая модель подошвы остряка).
- Теплофизические свойства стали приняты следующими:
- коэффициент температуропроводности …0,044 см^/с;
- коэффициент теплопроводности 23,2 Вт/(м-К).
Схема моделирования сечения головки и подошвы остряка для расчета температурного поля
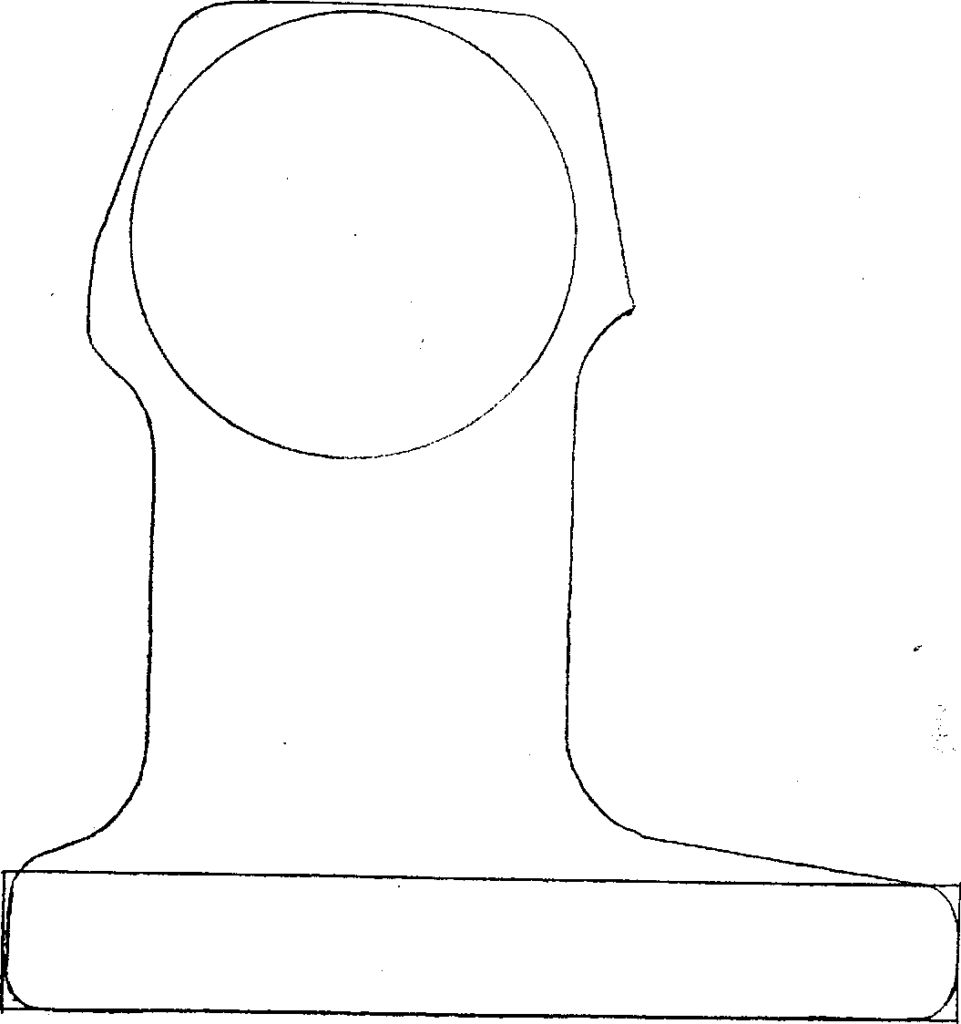
При дальнейшем изложении приняты следующие обозначения:
Т — температура в данной точке (элементарном объеме) сечения в данный момент времени, К; т — время, ч;
с — теплоемкость металла, Дж/(кГ-К); X — коэффициент теплопроводности металла, Вт/(м-К); а — коэффициент температуропроводности металла, м^/с; а — коэффициент теплоотдачи в охлаждающую среду, Тс — температура охлаждающей среды, К;
То — температура нагрева при закалке, К;
Л, Б — радиус цилиндра и толщина пластины, м;
г, х — расстояние от оси цилиндра или пластины до рассматриваемой точки, м.
Для тела типа «неограниченный» цилиндр уравнение теплопроводности Фурье в цилиндрической системе координат будет иметь вид.
В качестве начального условия принимается равномерное распределение температур по сечению цилиндра Т(г?о) = То, где То — начальная температура тела.
К
Вводя конечно-разностную сетку с шагом по координате Аг = — и по
п
времени Ат, где п — число узлов сетки и аппроксимируя производные в уравнении (2.1) конечными разностями, получим конечно-разностную аппроксимацию уравнения (2.1).
Для тела типа «неограниченная» пластина уравнение теплопроводности при одномерном тепловом потоке в случае отсутствия внутренних источников тепла.
При реальных расчетах, проводимых с заданным шагом по времени Ат значения т} и 12 невозможно определить абсолютно точно, так как даже при достаточно малом шаге по времени значения температур Т] и Т2 не будут равны значениям нижней и верхней границы температурного интервала АТ. Поэтому значения т^ и 12 определяются как время охлаждения до температур, попадающих в пределы Т}±А} и Т2±А2, где А} и А2 — заранее заданные допуски в определении верхней и нижней границы интервала АТ. При этом предельная относительная погрешность в определении скорости охлаждения 5(У0ХЛ).
Формула (2.9) позволяет провести расчет скорости охлаждения в конкретно заданной точке. Расчет скоростей охлаждения по сечению тела можно провести, преобразовав формулу (2.9).
где Т* — температура в пределах Т, ± А, верхней границы интервала AT, -q — время, за которое данная точка охладится до температуры Т,\ Tj — температура в текущий момент времени т попадающая в предел Т2 ± Д2 нижней границы интервала AT.
Приведенный выше математический аппарат решения задачи заложен в основу компьютерной программы Temps в системе профессиональной разработки программ на языке Бейсик — MS Basic PDS 7.1 на ПЭВМ. Программа разработана на кафедре металловедения и термической обработки МГВМИ.
2. Расчет распределения твердости от торца стандартного торцового образца (ГОСТ 5657-78 «Метод испытания на прокаливаемость») по методике американского стандарта SAE J406.
Расчет прокаливаемости исследуемых марок сталей на стандартном торцовом образце проводится по методу коэффициентов множителей. Данная методика утверждена американским стандартом SAE J406. Метод SAE J406 заключается в расчете идеального критического диаметра (Dœ) с помощью множительных коэффициентов (fi), каждый из которых зависит от абсолютного содержания легирующего элемента в стали:
Dœ = 25,42 • fc • fMn • fs, • fMo • fNl • fv • fCu • fCr. (2.11)
Стандартом предусмотрена возможность расчета кривых прокаливаемости в виде графической зависимости твердости (HRC) от расстояния от охлаждаемого торца стандартного торцового образца для определения прокаливаемости. Размеры образца и условия его охлаждения нормированы стандартом SAE J406 и совпадают с требованиями ГОСТ 5657-78 «Метод испытания на прокаливаемость».
По стандарту SAE J406 твердость на различном расстоянии от торца определяется делением максимально возможной твердости Hjqo на соответствующий делительный коэффициент Dp-, определяемый по таблицам стандарта в зависимости от значений идеального критического диаметра (DK) и расстояния от охлаждаемого торца.
- Определение зависимости твердости стали от скорости охлаждения на торцовом образце в интервале температур 700 — 500 °С с использованием литературных данных о продолжительности охлаждения в интервале 800 — 500 °С на различном расстоянии от охлаждаемого торца [96].
- Оценка распределения твердости по сечению головки и подошвы остряка на основе полученных в пунктах 1, 2 и 3 зависимостей.
Исследование неметаллических включений в сталях 76ХСФ и М73В
Анализ загрязненности неметаллическими включениями сталей марок М73В и 76ХСФ проводили по методу ASTM Е 1245 на анализаторе изображения IA — 3001 фирмы «LECO». Микрофотосъемка неметаллических включений проводилась на световом микроскопе МИМ — 8 при увеличении х200. Количественному анализу подвергались следующие типы неметаллических включений: сульфиды строчечные, оксиды алюминия, оксисульфиды, оксиды глобулярные. В процессе анализа определяли среднюю площадь, занимаемую включениями; средний размер глобулярных включений и среднюю длину строчек. Усреднение проводилось по 112 полям зрения. Площадь поля зрения 640000 мкм2.
Шлифы для анализа неметаллических включений изготавливали вдоль направления прокатки в соответствии с требованиями ГОСТ 9960 — 85.
Испытание на износостойкость
Сравнительные испытания на износостойкость проводили по методу Амслера. Из образцов серийных и опытных остряков изготавливали ролики диаметром 40 мм и толщиной 10 мм. Контрролики диаметром 40 мм и толщиной 6 мм изготавливали из колесной стали марки 2 по ГОСТ 10791 — 89. Твердость роликов из стали М73В составила НКС 37, твердость роликов из стали 76ХСФ — НЯС 37 и 44. Ролики из хромистой стали меньшей твердости моделируют износ остряков из стали 76ХСФ без термической обработки, ролики с большей твердостью — износ остряков после закалки ТВЧ. Твердость колесных роликов составляла 32 НЯС.
Для получения необходимой твердости ролики подвергались закалке в масло с нагрева до 860 °С в печи и последующему отпуску при температурах 500 — 540 °С с окончательным охлаждением на воздухе.
По результатам моделирования различных режимов износа на роликах, представленным в работах [109-113], для проведения трех серий испытаний (для роликов из остряков различной твердости) были приняты следующие параметры режима: продольное проскальзывание 10%, угол разворота роликов 0°, нагрузка 95 кгс (давление в контакте 595 МПа), скорость вращения 500 об/мин.
Определение внутренних остаточных напряжений
Внутренние остаточные напряжения в опытных и серийных остряках определяли методом вырезки поперечного темплета с предварительно наклеенными на него тензометрическими датчиками марки 2ПКБ-10.100 В длиной 10 мм с электросопротивлением 11=99,70-99,99 Ом.
Математическая оценка напряженного состояния в головке остряка
С целью обоснования возможности развития поверхностных трещин от волосовин при закалке остряков с выгибом был проведен расчет напряженно- деформированного состояния, возникающего в головке и подошве остряка при термической обработке. Математический анализ включал в себя решение задачи нестационарной теплопроводности и расчета напряженно- деформированного состояния (НДС) в головке рельса с учетом наличия волосовины критической глубины (0,5 мм для остряков).
Задача теплопроводности или задача определения нестационарного температурного поля Т при теплопередаче теплопроводностью в произвольной трехмерной области V может быть сформулирована в виде краевой задачи, описываемой квазилинейным дифференциальным уравнением параболического. типа [25]:

где Т(х к, ^ — поле температур, требующее определения; к ; (х к, Т) — симметричный тензор коэффициентов теплопроводности; р (х к, Т) — плотность материала; с (х к, Т) — удельная теплоемкость; (3 (х к, Т) — интенсивность тепловыделения; t — время.
Задача формулируется в замкнутом виде при задании начального условия — распределения температуры в области V в начальный момент времени 1 = 0:
Т(хьО) = Ф(хк), х к е V (2.16)
Уравнение (2.12), граничные условия (2.13) — (2.15) и начальное условие (2.16) представляют собой математическую формулировку задачи теории теплопроводности, определяющей распределение температуры в произвольном трехмерном теле объема V в любой момент времени 0< 1: < т.
Упруго-пластическое поведение деформируемого твердого тела под воздействием известного температурного поля, определяемого (2.12) — (2.16) и внешних усилий при самых общих предположениях относительно условий на- гружения и поведения материала описываются уравнениями механики сплошной среды.
Уравнения (2.17) — (2.19) с добавлением уравнений состояния и соотношений Коши представляют собой математическую постановку краевой задачи упругопластичности в рамках механики сплошной среды в самой общей форме.
Для решения сформулированных задач термоупругопластичности целесообразно использовать метод конечных элементов (МКЭ) [24, 25]. В настоящее время этот метод хорошо известен и достиг высокого уровня совершенства. Сущность метода заключается в аппроксимации сплошной среды с бесконечным числом степеней свободы совокупностью подобластей (конечных элементов), имеющих конечное число степеней свободы. Конечные соотношения МКЭ хорошо известны для сформулированных выше задач [25].
Величина погрешности метода не превышает 15 %, как в задаче теплопроводности, так и в задаче определения НДС.
Испытания на циклическую долговечность
Испытания по оценке циклической долговечности остряков, изготовленных по различным технологиям, проводили по схеме трехточечного изгиба на электрогидравлическом пульсаторе ЦДМ 200/400-ПУ, позволяющем создавать нагрузки до 200 тс. Частота циклического нагружения составила 5 Гц, коэффициент асимметрии цикла 1^=0,1, что обеспечило наиболее жесткий режим нагружения [114].
Для проведения-испытаний полнопрофильные остряковые пробы длиной 1300 мм устанавливались на опоры пульсатора головкой вниз, так чтобы упрочненный слой в головке остряков находился в зоне действия растягивающих напряжений. Расстояние между опорами составляло 1000 мм.
Статистическая обработка экспериментальных данных
Обработка статистических данных проводилась с использованием известных формул математической статистики [115, 116].
Согласно проведенной оценке, для получения результатов с надежностью 0,95, минимальное количество замеров должно быть не менее пяти на точку. В работе все данные приводятся по результатам замеров 10 образцов на точку, так как это количество опытов с достаточной степенью точности обеспечивает возможность использования законов нормального распределения при обработке статистического материала [115, 116].