- Метод индукционной поверхностной закалки как технология упрочнения рельсов и остряков стрелочных переводов
- Предпосылки и принципы разработки нового состава стали для остряков
- Выводы
Цикл статей:
Глава 1 — Введение. Цели и задачи исследований.
Глава 2 — Анализ причин отказов стрелочных переводов и их элементов
Глава 3 — Материалы и методика исследования
Глава 4 — Сравнительные исследования комплекса физико- механических свойств остряков из сталей марок 76хсф и м73в
Глава 5 — Разработка технологических основ двухстороннего поверхностного упрочнения остряков
Глава 6 — Работы по промышленному внедрению стали 76ХСФ и технологии двухстороннего термического упрочнения остряков
Анализ повреждаемости и причины недостаточной стойкости остряков в эксплуатации
Условия эксплуатации и повреждаемость остряков
Конструктивные особенности устройства стрелки (два рамных рельса и два остряка с деталями креплений, тяг и связей) и взаимного расположения рамного рельса и остряка таковы, что на пути качения колес возникают неровности как в вертикальной, так и в горизонтальной плоскостях, обуславливающие динамические воздействия на остряк.
Примыкание остряка к рамному рельсу как по прямому, так и по боковому пути характерно образованием геометрической неровности в вертикальной плоскости для движущегося колеса [4, 5, 6]. Влияние неровности на движение экипажа зависит от ее параметров — длины, глубины, уклона, а также от формы и характер износа поверхности катания колеса. При контакте неизношенного рамного рельса и остряка глубина неровности составляет около 2,5 мм, длина — 3,7-4,2м [4].
Неровности в горизонтальной плоскости порождают дополнительное горизонтальное динамическое воздействие.
При противошерстном движении по боковому направлению экипаж, входя в стрелочный перевод, движется прямо до момента удара первой колесной пары в остряк. Непосредственно после удара остряк испытывает большие безударные воздействия сил инерции всего экипажа, вызванные изменением направления его движения. Сила удара зависит от угла набегания колеса на остряк, скорости движения и масс соударяющихся колеса и рельса [5]. Большие силы удара колес в остряк вызывают значительный износ и расстройство стрелки и ходовых частей подвижного состава.
Движение экипажа на боковой путь по криволинейной траектории сопровождается появлением центробежной силы, которая обусловлена непогашенным центробежным ускорением. Наличие непогашенного центробежного ускорения приводит к действию боковых сил на остряк со стороны колес подвижного состава, усиливающему боковой износ [7].
Исследованиям стрелочных переводов посвящен ряд работ [8-12]. Основные возмущающие факторы при работе перевода [8]:
- прикрепление остряка, детали с ослабленным строжкой сечением и работающей на изгиб, только в его корневой части и в зоне присоединения тяг;
- вертикальная неровность в месте перекатывания колес с рамного рельса на остряк и обратно;
- набегание и удар колесной пары в остряк при движении по боковому ответвлению;
В табл. 1.1 приведены данные, характеризующие долю поврежденных различными видами дефектов остряков. Таблица составлена на основе выборки из 250 остряков, изъятых из пути на Западно-Сибирской железной дороге.
Все приведенные в табл. 1.1 дефекты классифицируются по НТД/ЦП-1, 2, 3-93 [13, 14].
№ п.п. | дефект | % от общего выхода | Описание дефекта |
1 | 2 | 3 | 4 |
1 | 0.21.2 | 33,33 | Поперечные трещины и изломы в головке по причине недостаточной контактно-усталостной прочности металла |
2 | 0.41 | 16,22 | Смятие и износ из-за недостаточной прочности металла |
3 | ДОЛ 1.2 | 10,36 | Выкрашивание гребнеобразного наплыва в сторону рамного рельса в зоне боковой строжки остряка из-за недостаточной контактно- усталостной прочности металла |
4 | О.ЗО.Г.2 О.Ю | 15,32 | Горизонтальное расслоение головки; отслоение и выкрашивание металла на поверхности катания из-за недостатков технологии изготовления |
5 | Д0.20.2 | 6,31 | Трещины в головке и изломы из-за них в зоне выпрессовки |
6 | ДО.42.2 | 5,85 | Седловины на поверхности катания |
7 | 0.11 | 4,5 | Выкрашивание металла на боковой рабочей выкружке головки из-за недостаточной контактно- усталостной прочности металла |
8 | ДО.80 | 1,8 | Неприлегание остряков к рамному рельсу и к подушкам подкладок из-за саморазгиба, вертикального выгиба и пропеллерно- сти |
Анализ данных табл. 1.1 показывает, что наиболее распространены дефекты, обусловленные недостаточной износостойкостью и контактно- усталостной прочностью остряков. К таким дефектам относятся: поперечные трещины и изломы в головке по причине недостаточной контактно-усталостной прочности металла (дефект 0.21.2); смятие и износ из-за недостаточной прочности металла (дефект 0.41); образование гребнеобразного наплыва и его выкрашивание (дефект ДО 11.2). Так же распространены дефекты, связанные с недостатками технологии производства, такие как горизонтальное расслоение головки и отслоение и выкрашивание металла на поверхности катания (дефекты О.ЗО.Г.2 и 0.10 соответственно).
Из наиболее распространенных дефектов, неуказанных в табл. 1.1, составленной по результатам исследования выборки из 250 остряков, следует отметить выкрашивание закаленного слоя в корневой зоне остряка (дефект 0.17.1).
Внешний вид выкрашивания гребнеобразного наплыва (дефект 0.11.2) и выкрашивания закаленного слоя в корневой зоне (дефект 0.17.1) представлен на рис. 1.1 (а, б).
Величина гребнеобразного наплыва в случае дефекта ДО 11.2 достигает 6 мм, а глубина последующего его выкрашивания — 5 мм и более. Как правило, этот дефект возникает в тонких сечениях головки шириной 12-20 мм. В последнее время на наиболее напряженно эксплуатируемых стрелочных переводах отмечено образование подобного дефекта после пропуска 1520 млн. т. брутто при среднесетевом нормативном сроке службы остряка 320 млн. т. брутто, что свидетельствует о низком уровне эксплуатационной стойкости остряков, изготавливаемых по действующей технологии.
Дефекты, связанные с недостаточной контактно-усталостной прочностью остряка
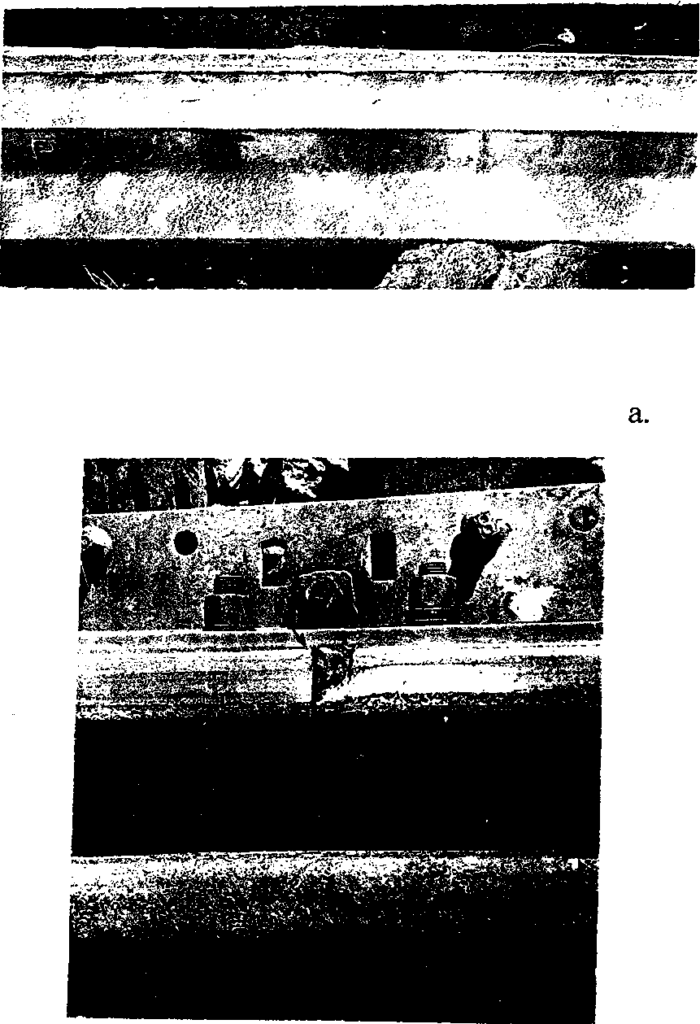
а — выкрашивание гребнеобразного наплыва, дефект О. 11.2;
б — выкрашивание закаленного слоя в корневой зоне, дефект О
При интенсивном боковом воздействии колес тонкая часть головки остряка вблизи его острия подвергается усиленному износу и затем выкрашиванию. Подобное выкрашивание происходит, как правило, от острия до первой стрелочной тяги и классифицируется как дефект ДО. 14.2. Выкрашиванию способствуют недостаточная износостойкость и контактно-усталостная прочность остряка.
Отсутствие подуклонки в стрелочном переводе приводит к тому, что колеса опираются на остряки ближе к боковой грани головки. Это вызывает в остряках быстрое развитие дефектов О. 11. 1 и О. 11.2 (выкрашивание металла на боковой рабочей выкружке головки).
В случаях наиболее интенсивной эксплуатации стрелочных переводов они наблюдаются уже после пропуска 15-18 млн. т. брутто.
К образованию выкрашиваний на поверхности катания остряка в различных его сечениях приводит, как правило, недостаток контактно-усталостной прочности металла, а так же наличие строчек неметаллических включений, вытянутых вдоль направления прокатки. Это также обуславливает появление такого дефекта как поперечные трещины и изломы в головке остряка (дефект О. 21. 2). Наиболее полно механизм контактно-усталостных повреждений рельсов, аналогичный механизму контактно-усталостных повреждений остряков, изучен в работах [15, 16].
Уязвимой в части эксплуатационных повреждений является подошва остряка, что обусловлено возникновением растягивающих напряжений в подошве при эксплуатации и взаимодействием подошвы остряка и стрелочной подушки.
Авторами работы [12] было показано, что предел выносливости подошвы остряков при испытаниях полнопрофильных остряковых проб на циклическую долговечность при коэффициентах асимметрии цикла нагружения = 0,2 — 0,8 и базе испытаний 2 млн. циклов составил 160 — 330 МПа при предельно допустимом значении растягивающих напряжений во внешней кромке подошвы 275 МПа. Отсюда следует, что усталостная прочность подошвы остряка в ряде случаев ниже уровня предельно допустимых напряжений.
Характерный пример поперечного излома остряка, образовавшегося в результате развития усталостной трещины от дефекта на наружной кромке подошвы, представлен на рис. 1.2.
Таким образом, проведенный анализ основных условий эксплуатации остряков, показывает, что конструктивные особенности стрелок и характер взаимодействия экипажа со стрелочным переводом создают крайне жесткие условия эксплуатации остряков. Это должно компенсироваться высоким уровнем механических свойств остряков. Однако, основными причинами отказа 65% остряков являются их недостаточные прочностные свойства и несовершенства технологии изготовления, снижающие надежность переводов [17].
Особенности серийной технологии производства остряков и связанные с ней дефекты
В настоящее время на Новосибирском стрелочном заводе (НСЗ) и ОАО «Муромский стрелочный завод» (ОАО «МСЗ») практикуется закалка поверхности катания остряков сжатым воздухом с индукционным нагревом с предварительным выгибом остряков головкой вверх. Данный способ внедрен в 50-60 гг [18].
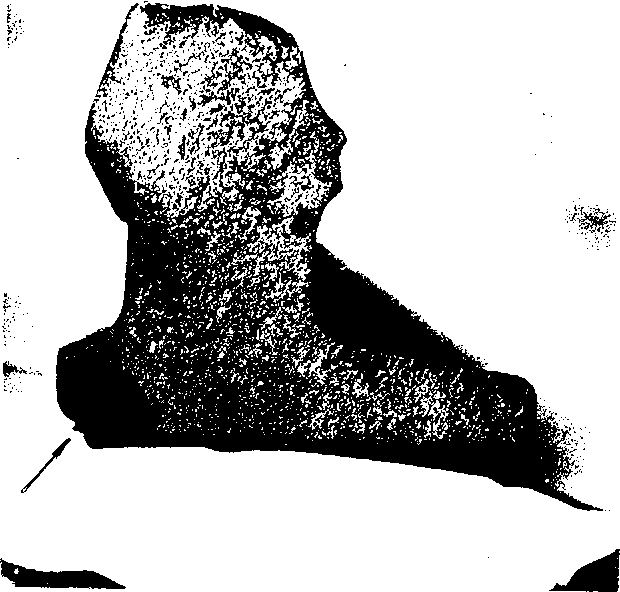
В соответствии с терминологией, принятой в металловедении, термическое упрочнение остряков по указанной технологии не является закалкой, так как в результате термической обработки в упрочненном слое головки остряка образуется сорбит, а не мартенсит, образующийся при закалке стали. Однако ввиду общепринятого использования этого термина в нормативной документации и научно-технической литературе применительно к острякам и рельсом, далее в работе будет употребляться термин «индукционная поверхностная закалка».
Усталостная трещина, развившаяся от кромки подошвы остряка
Схема и внешний вид установки для индукционной закалки с выгибом представлены на рис. 1.3 и 1.4. После остывания до температуры цеха остряк подвергается холодной механической правке на штемпельном прессе. Контроль прямолинейности непосредственно при правке осуществляется оператором пресса при помощи металлической линейки длиной 1 м.
Данные о повреждаемости остряков и рельсов различных предприятий- производителей, показывают, что на остряках и рельсах, изготовленных на заводах, где практикуется индукционная закалка с выгибом (НСЗ, ОАО «МСЗ», Азовсталь), имеет место разрушение от поверхностных трещин, развившихся от металлургических дефектов в поверхности катания типа волосовин при индукционном нагреве с выгибом. Глубина таких трещин на поверхности катания превышает предельно допустимые соответствующей нормативной документацией значения (0,5 мм для остряков и 1,0 мм для рельсов) и достигает 3,04,8 мм [19, 20]. На объемно-закаленных рельсах производства ОАО «Кузнецкий металлургический комбинат» (ОАО «КМК») и АО «Нижнетагильский металлургический комбинат» (АО «НТМК»), где применяется объемная закалка в масло без выгиба, разрушения от подобных дефектов не встречаются.
К наиболее распространенным дефектам, возникающим на металлургической стадии производства остряковых рельсов и проявляющимся на поверхности катания остряков при закалке с выгибом, следует отнести в соответствии с [21, 22]: раскатанные неметаллические загрязнения, волосовины, раскатанные пузыри, раскатанные трещины слитка.
Наиболее полно объясняет причины раскрытия и роста поверхностных трещин при термической обработке остряков математический расчет напряженного состояния в головке остряка при закалке с выгибом, проведенный с использованием метода конечных элементов, основные положения которого сформулированы в [23, 24, 25].
Схема установки для индукционной закалки остряков с выгибом

- — закалочный стенд;
- — индуктор;
- — воздушный распылитель
Внешний вид установки для индукционной закалки остряков с выгибом
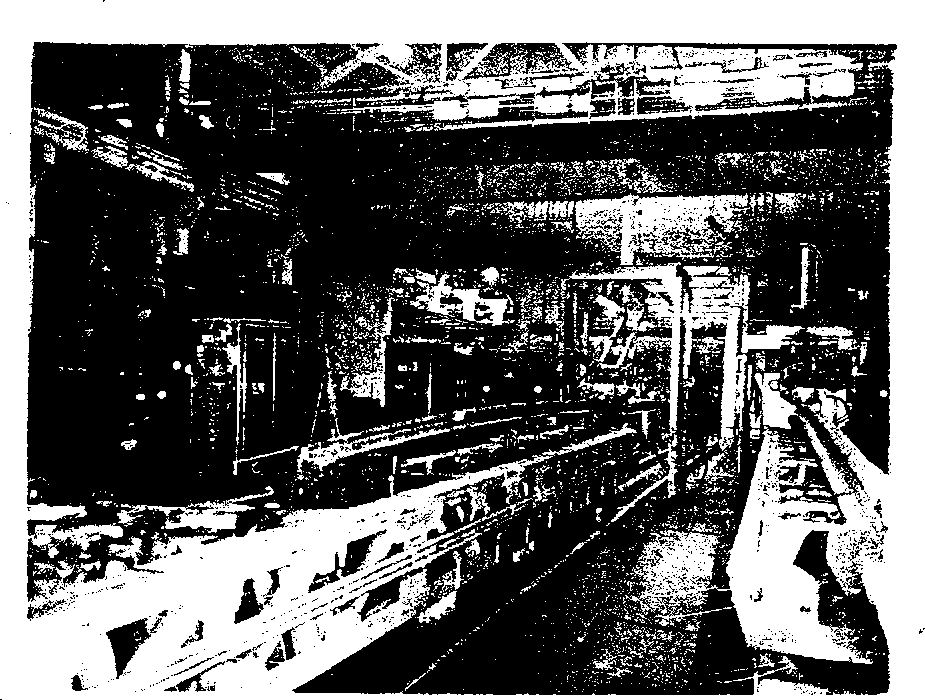
Расчет напряженного состояния остряка при индукционном нагреве с выгибом показал, что в поверхностных слоях головки остряка формируются растягивающие напряжения, уровень которых превышает пределы текучести всех используемых для производства остряков марок сталей. Эти растягивающие напряжения приводят к раскрытию и углублению описанных поверхностных дефектов. В эксплуатации наличие трещин глубиной до 3,0 — 4,8 мм, развившихся при индукционной закалке с выгибом, приводит к образованию выкрашиваний в головке и к излому всего остряка (или рельса) [26].
Закалка остряков с выгибом не обеспечивает их необходимой прямолинейности, что вынуждает прибегать к последующей механической правке на штемпельном прессе, приводящей к формированию неблагоприятной эпюры внутренних остаточных напряжений [27, 28]. После правки в головке или подошве остряка (в зависимости от направления правящего усилия) образуются растягивающие напряжения. Из исследований влияния внутреннего напряженного состояния изделий на их сопротивление разрушению при циклических и контактных нагрузках известно, что наличие внутренних остаточных сжимаю- . щих напряжений в поверхности изделия приводит к повышению предела выносливости и контактно — усталостной прочности металла, а растягивающие напряжения облегчают разрушение [29-37].
В процессе эксплуатации напряженное состояние остряков претерпевает существенные изменения, приводящие к короблению остряков за счет релаксации внутренних остаточных напряжений. Виды выгиба, встречающиеся на практике, представлены на рис. 1.5 [38].
Выгиб остряка в процессе эксплуатации приводит к нарушению норм по прилеганию граней остряка к рамному рельсу и стрелочным подушкам, что обуславливает отказ в работе стрелки. Так по данным ПС-8, на участке Ярославль Главный — Данилов выявлены остряки, выгиб которых характеризовался неприлеганием к стрелочным подушкам величиной до 14,5 мм. Всего на указанном участке было выявлено 44 остряка с выгибом, превышающим 5 мм.
Виды выгиба остряков в эксплуатации
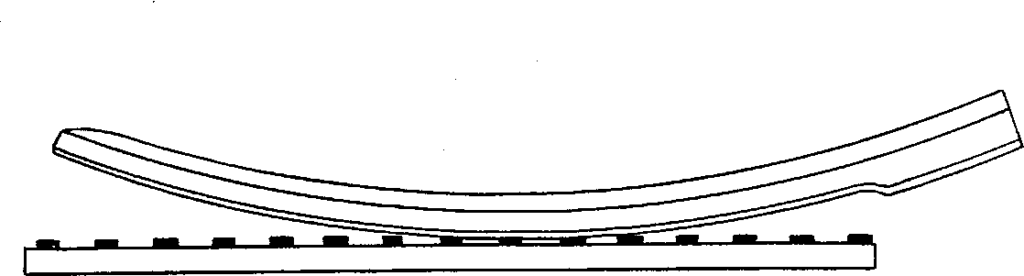
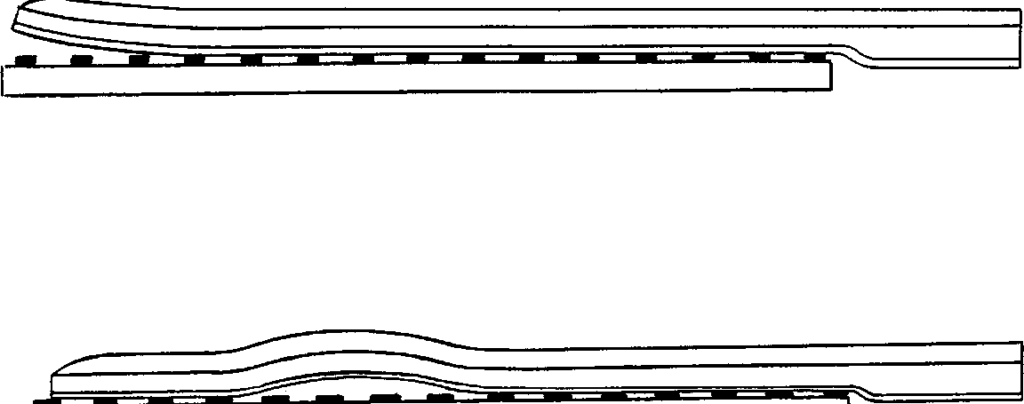
Боковой износ остряков, интенсивность которого в отдельных наиболее неблагоприятных случаях эксплуатации достигает 10 мм/10 млн. т. брутто (при предельно допустимом боковом износе остряка 6-8 мм [5]), а также интенсивная повреждаемость остряков контактно-усталостными дефектами, говорят о необходимости решения в рамках металловедческого подхода проблемы повышения прочностных свойств и твердости остряков.
В настоящее время для производства остряков применяется углеродистая сталь марок М73В, М73Т, М73Ц, марочный состав которой в соответствии с ГОСТ 9960 приведен в табл. 1.2. В табл. 1.2 так же приведен реальный химический состав стали исследованных остряков производства ОАО «ЬСМК» и ОАО «МСЗ».
Наблюдаемое увеличение интенсивности бокового износа и выгиба при эксплуатации показывает, что прочностные свойства по сечению остряка и твердость поверхности катания, реализуемые на сталях серийных марок, не обеспечивают эксплуатационной стойкости остряков, соответствующей современным требованиям.
Рассматривая повышение эксплуатационной стойкости остряков в рамках улучшения эксплуатационных свойств рельсовой продукции «в целом, следует отметить, что проблеме повышения качества рельсов посвящено весьма большое количество работ [39-48].
В работах [46, 47, 48] показано, что основными факторами, определяющими износостойкость и контактно-усталостную прочность рельсовой стали являются — твердость, содержание углерода в стали, микроструктура (наличие дисперсной карбидной фазы в однотипной структуре на глубине, превышающей зону действия высоких контактных напряжений с учетом запаса металла на износ, то есть на глубине 15-20 мм), чистота по неметаллическим включениям, отсутствие внешних концентраторов напряжений в виде волосовин и других дефектов на поверхности катания, а так же создание значительных сжимающих остаточных напряжений на поверхности и в зоне возникновения контактно- усталостных повреждений.
Таблица 1.2 Химический состав стали серийных остряков
Марка | Содержание элементов, масс. % | |||||||
стали | Р | 8 | ||||||
по ГОСТ 9960 | С | Мп | Б! | V | л | гг | Не более | |
М73В | 0,670,78 | 0,751,05 | 0,180,45 | 0,030,06 | — | — | 0,035 | 0,04 |
М73Т | 0,670,78 | 0,751,05 | 0,180,45 | — | 0,0070,015 | — | 0,035 | 0,04 |
М73Ц | 0,670,78 | 0,751,05 | 0,180,45 | — | — | 0,0010,05 | 0,035 | 0,04 |
Реальный химический | 0,63- | 0,83- | 0,33- | 0,03- | 0,010- | 0,001- | 0,011 | 0,012 |
состав | 0,8 | 1,02 | 0,37 | 0,06 | 0,015 | 0,002 | 0,018 | -0,032 |
Наличие однотипной структуры в закаленном слое с дисперсной равномерно распределенной карбидной фазой обеспечивается закалкой головки остряка с образованием пластинчатого сорбита. Однако повышение твердости закаленного слоя в головке остряков и его глубины при соблюдении условия отсутствия в структуре мартенсита (требование ТУ 32 ЦТВР-463-81) не представляется возможным на сталях серийного состава (см. табл. 1.2) по причине недостаточной прокаливаемости и закаливаемости этих сталей в условиях охлаждения сжатым воздухом.
Свойства рельсов и остряков и особенности технологии их производства
показатель | Россия | Украина | Япония | Германия | Великобритания | Австрия | Канада | |
НТМК, КМК | НСЗ, МСЗ Остряки | Азовсталь | Явета | БУ8Со | ||||
Способ термической обработки | Объемная закалка рельсов в масле с отдельного нагрева, отпуск | Закалка сжатым воздухом поверхности катания с нагрева твч | Поверхностная закалка головок рельсов водо- воздушной смесью с нагрева ТВЧ | Закалка головок рельсов с использованием нагрева ТВЧ и охлаждение сжатым воздухом | Закалка головки и подошвы рельса сжатым воздухом с нагрева ТВЧ | Закалка ‘ головок рельсов с использованием: 1. Тепла прокатного нагрева и охлаждения водой; 2. Нагрева ТВЧ, регулируемого охлаждения до 600 °С и последующего охлаждения водой. | Закалка головок рельсов с использованием прокатного нагрева и охлаждения водой с синтетическими добавками | Закалка головки и подошвы рельса с нагрева ТВЧ при предварительном сквозном индукционном нагреве до 760 °С |
Тип рельсовой стали | Высоко- углеродистая | Высоко- углеродистая | Высоко- углеродистая | Высокоуглеродистая и низколегированная | Высокоуглеродистая и низколегированная | Высокоуглеродистая и низколегированная | Высокоуглеродистая | Низколегированная |
Св-ва термо- упрочненных рельсов GB, Н/мм2 | 1300 | 1140 | 1400 | 1300 | 1175 | 1190 | 1210 | 1359 |
С?о,2? Н/мм 5, % HB поверхности | 960 10,0 до 405 | 795 11,0 380 | 966 9,6 до 405 | 844 19,0 до 405 | 785 10,0 351-405 | 680-770 8,0-10,0 до 400 | 770 10 360 | 924 13,4 до 404 |
Для выработки рациональных и эффективных путей повышения эксплуатационной стойкости остряков был проведен анализ основных особенностей технологий производства рельсов и остряков крупными отечественными и зарубежными производителями. Результаты анализа представлены в табл. 1.3. Часть данных табл. 1.3 взята из работы [41]. Как видно, зарубежные производители (Франция, Германия, Япония, Канада) рельсовой продукции используют низколегированные стали. В частности, для производства рельсов с упрочненной головкой фирма SYSCo(Канада) применяет сталь следующего состава: углерод — 0,75 %, марганец — 0,82%, кремний — 0,55%, хром — 0,45%, ванадий — 0,055%, фосфор — 0,013%, сера — 0,012%. К рельсам из стали указанного состава фирма SYSCo применяет непрерывно-последовательную двухстороннюю индукционную закалку (нагрев и закалочное охлаждение головки и подошвы), обеспечивающую высокие прочностные и эксплуатационные свойства рельсов за счет получения внутренних остаточных напряжений сжатия в головке и подошве рельсов до 200 МПа. В результате двухстороннего нагрева и закалочного охлаждения рельсы фирмы SYSCo не подвергаются правке и характеризуются высокой прямолинейностью.
Как показывают полигонные испытания рельсов фирмы SYSCo, проводимые на ЭК ВНИИЖТ, разрушения от поверхностных дефектов типа волосовин не происходят.
Таким образом, анализ эксплуатационной стойкости остряков, основных особенностей технологии их производства и обзор технологий производства рельсов ведущими зарубежными производителями показал наличие двух, самостоятельных путей повышения эксплуатационной стойкости: переход на новую марку стали и внедрение схемы двухсторонней закалки.
Метод индукционной поверхностной закалки как технология упрочнения рельсов и остряков стрелочных переводов
Основные особенности и общие принципы метода
Индукционная поверхностная закалка была разработана в 30-х годах В. П. Вологдиным [49, 50] и с тех пор нашла широкое применение в технологии современного машиностроения для упрочнения стальных деталей. Особенностями этого метода упрочнения являются: большая скорость индукционного нагрева (до 10000 °С/сек), позволяющая резко сократить длительность цикла термической обработки и применить ее непосредственно в потоке механической обработки; возможность полной автоматизации операций нагрева и закалки; достижение высоких прочностных свойств поверхностно закаленных изделий; снижение стоимости термической обработки [51].
Поверхностная закалка токами высокой частоты (ТВЧ) применяется в промышленности для получения изделий с твердым, износостойким поверхностным слоем и сравнительно мягкой и вязкой сердцевиной.
К основным преимуществам индукционной поверхностной закалки по сравнению со сквозной закалкой следует отнести:
- получение в деталях высокопрочного состояния, характеризующегося — градиентом свойств по сечению деталей — твердой и прочной поверхностью и вязкой сердцевиной, что создает благоприятную эпюру внутренних остаточных напряжений (напряжения сжатия в закаленном слое до 600-800 МПа [52]) и обеспечивает высокое сопротивление усталости деталей [52]. Изучение влияния поверхностной закалки на коррозионно-усталостную прочность в работе [53] показало, что она значительно повышает предел выносливости в коррозионной среде. Так предел выносливости нормализованной стали 40 в коррозионной среде снижается с 255 до 100-72 МПа, а предел выносливости поверхностно закаленных образцов в гораздо меньшей степени — с 475 до 358-265 МПа. Внутренние остаточные напряжения сжатия в поверхностном слое повышают так же стойкость изделий против контактного выкрашивания;
- практически полное устранение окисления и обезуглероживания и получение мелкого зерна аустенита при индукционном нагреве (номер 11 — 12 по шкале ГОСТ 5639 против номера 7-8 при печном нагреве [52]) за счет высокой скорости нагрева (до 100 °С/сек). При скоростях нагрева больше 100 °С/сек в сталях с улучшенной (сорбитной) исходной структурой образуется зерно размером № 14 — 15. Такое «сверхмелкое» зерно аустенита обусловливает значительное повышение характеристик пластичности стали после закалки и низкого отпуска в сравнении со сталью, закаленной с нагрева в печи. При этом для стали 45 сопротивление хрупкому разрушению увеличивается в 5 — 6 раз [52], значительно повышается запас вязкости — порог хладноломкости снижается примерно на 200 °С, коэффициент интенсивности напряжений повышается
- от 740 до 1600 — 2700 Н/мм , при испытаниях на ударный изгиб при твердости около 60 НЯС часто наблюдаются пластическая деформация, а не хрупкое разрушение образца [52].
Наличие мелкого зерна и сжимающих остаточных напряжений в поверхностных слоях позволяет повысить длительность работы деталей до начала контактного выкрашивания в 2 раза [52].
При использовании индукционного нагрева при объемно-поверхностной . закалке (ОПЗ) снижается вероятность образования трещин, что позволяет закаливать без брака детали из сталей с широким диапазоном содержания углерода -от 0,2 до 1,2%.
Особенностью высокочастотного индукционного нагрева металлов является генерирование тепловой энергии непосредственно в нагреваемом изделии. При поверхностной закалке применяют режимы, обеспечивающие нагрев до температуры закалки за время от нескольких секунд до десятых долей секунды [54]. В теории индукционного нагрева [50, 54, 55, 56] доказывается, что ток индуктора 1и и мощность, выделяемая в нагреваемой детали, Рд связаны соотношением: Рд = к]1ИЛ/у9 ¡л / , где к] — коэффициент, зависящий от размеров индуктора и нагреваемой детали; р, ц — соответственно удельное сопротивление (Ом см) и магнитная проницаемость (Гс/Э) нагреваемого материала, f — частота тока (Гц).
При поверхностном нагреве полнота и степень фазовых превращений определяется временем пребывания стали в области температур фазовых превращений — суммарным временем аустенизации.
Время пребывания металлов в области температур фазовых превращений зависит от скорости нагрева и фазовых превращений, сопровождающихся поглощением теплоты. Последние обуславливают наличие изотермической площадки на кинетической кривой индукционного нагрева [57].
Удельную мощность (кВт/см ), обуславливающую скорость нагрева, выбираются в зависимости от требуемой глубины нагрева. Глубина проникновения тока в металл А зависит от частоты тока и физических свойств металла:
Д = 5000 [58]. При частоте 2500 Гц глубина проникновения тока в сталь при температуре 800 °С составляет 10 мм.
В работе [51] проведен анализ конструктивной прочности деталей, подвергнутых объемно-поверхностной закалке при глубинном нагреве. Так как изделия, подвергаемые поверхностной закалке, в эксплуатации чаще всего испытывают изгибающие нагрузки, исследования статической прочности после поверхностной закалки и других видов термической обработки проводились на образцах, имеющих форму пластин размерами 10x70x170 мм и испытываемых на трехточечный изгиб при расстоянии между опорами 140 мм. На образцах, подвергнутых индукционной поверхностной закалке, глубина упрочненного слоя составляла 2,0 мм. На образцах, подвергнутых цементации, глубина цементованного слоя была 1,7 мм.
Результаты испытаний показали увеличение предела прочности поверхностно закаленных пластин по сравнению с цементированными больше, чем на 25 % [51]. В работе [51] также проведены статические испытания на изгиб полос из стали 58 (55ПП) после поверхностной закалки и отпуска при 180 °С в сравнении с полосами из рессорной стали 60С2 после объемной закалки, отпуска при 520 °С и дробеструйного наклепа. Результаты показали, что наряду со значительным (в 1,5-1,8 раза) увеличением статической прочности при изгибе увеличивается пластичность (прогиб увеличивается с 3 до 8 мм). Автор объясняет эти результаты более мелким зерном и большим запасом вязкости у поверхностно закаленной стали 58 (551111).
Исследование влияния индукционной поверхностной закалки на износостойкость стальных изделий проведено в работах [59,60]. В работе [59] отмечается уменьшение износа стали 50Г приблизительно на 25% при высокочастотной поверхностной закалке по сравнению с обычной. В работе [60] приводятся результаты, показывающие уменьшение износа инструментальной стали марок У10А и XI2 при высокочастотной закалке по сравнению с обычной закалкой на 40-60 % и значительное увеличение стойкости фрез из стали 9ХС, разверток, пуансонов и матриц из стали У10А при переходе от обычной к высокочастотной поверхностной закалке.
Высокочастотная поверхностная закалка дает повышение износостойкости по сравнению с обычной за счет повышения твердости поверхности и отсутствия обезуглероживания.
В работе [61] проводились сравнительные испытания колес-сателлитов трактора К-700, поверхностно закаленных и цементованных. Цементованные зубчатые колеса изготовлялись из стали 20ХГНР, поверхностно закаленные колеса — из стали 45ХН. Твердость рабочих поверхностей зубьев и в том и в другом случае 56-58 Ш1С. Результаты испытаний показали, что поверхностно закаленные сателлиты по контактной прочности и износостойкости превосходят цементованные.
Таким образом, положительное влияние индукционной поверхностной закалки фактически на весь спектр свойств закаленных изделий создает предпосылки для широкого применения описываемого вида термической обработки в машиностроении и на железнодорожном транспорте.
Упрочнение железнодорожных рельсов и остряков стрелочных переводов с индукционным нагревом
Перспективы повышения прочности рельсов и оптимальное сочетание характеристик долговечности и надежности были проанализированы Я.Р. Рау- зиным [62]. Рассматривая различные варианты решения задачи создания высокопрочных рельсов, Я.Р. Раузин отмечает, что единственным направлением получения требуемого сочетания свойств является создание в рельсе дифференцируемой прочности по сечению.
Индукционная поверхностная закалка позволяет создавать градиент свойств по сечению изделия (твердая поверхность и вязкая сердцевина), обуславливающая при правильном выборе режима термической обработки оптимальное сочетание характеристик долговечности и надежности [63, 64]. Это обстоятельство способствовало тому, что индукционная поверхностная закалка стала одним из распространенных и наиболее эффективных видов термической обработки рельсов и остряков стрелочных переводов (см. табл. 3).
Первые опыты по индукционной поверхностной закалке рельсов (концов рельсов на длине 15-20 см на глубину 5-6 мм) были проведены в 1937 г. В.П. Вологдиным [65].
В 1954 г. в Японии начались опыты по индукционной закалке головок рельсов. Рельс в упруго-изогнутом состоянии нагревали в плавающем индукторе. Охлаждение осуществлялось водой, подаваемой на поверхность головки рельса, как только она проходила через первый закалочный индуктор, в котором рельс нагревался до 830-840 °С. Закаленная часть рельса поступала во второй индуктор для отпуска, где нагревалась до 480-500 °С и отпускалась до требуемой твердости.
В результате термообработки рельсы имели на глубине до 5 мм структуру сорбита и твердость HB 320-370. Общая глубина закаленного слоя достигала 10 мм. Эксплуатационные испытания на дорогах Японии показали удовлетворительное качество этих рельсов [66].
В Германии фирма «Thyssen Stahl» производит рельсы длиной до 30 м с термоупрочненной головкой с использованием индукционного нагрева и ускоренного охлаждения сжатым воздухом [67, 68].
В нашей стране поверхностная индукционная закалка впервые была осуществлена для остряковых и рамных рельсов в 1955 году на Омском механическом заводе [69]. Особенности этой технологии описаны в п. 1.1.2.
В 1961 г. заводом «Азовсталь» изготовлена опытная установка, состоящая из механизма передвижения рельса (подводящих и отводящих рольгангов) и электрической части , включающей четыре генератора мощностью по 100 кВт (частота 2500 Гц), нагревательный индуктор и станцию управления.
Рельс свободно без изгиба и специального крепления укладывали на подвижной стенд и перемещали под индуктором в горизонтальной плоскости; при этом он проходил последовательно стадии нагрева поверхности катания, охлаждения, самоотпуска и повторного охлаждения. В качестве закаливающей среды применялся конденсат, подогретый до 35-45 °С [70].
В процессе нагрева участок рельса, находящийся в зоне индуктора, выгибался на головку (на 60-120 мм), а после окончательного охлаждения создавалось общее искривление рельса головкой внутрь, доходящее до 500-600 мм на длине 12,5 м. Такие рельсы имели повышенную износостойкость, но в целом были неудовлетворительными по причинам:
- Неоднородности структуры и твердости по глубине закаленного слоя (наличие бейнитной полосы на глубине 3-6 мм) [71];
- Высоких растягивающих остаточных напряжений, появлявшихся при правке сильно изогнутого рельса и снижавших хрупкую прочность рельса до уровня, опасного для движения поездов [72].
На первой стадии разработки указанной технологии не были учтены меры по предотвращению сильного коробления после закалки и необходимость использования мягких закалочных сред (сжатого воздуха, водовоздушной смеси) для получения однородной структуры в головке [72, 73].
Сильное коробление вынуждает прибегать к последующей холодной механической правке. Процесс образования остаточных напряжений при индукционной закалке и перераспределение их при правке описан в работах [74 — 76].
В настоящий момент заводами-производителями стрелочной продукции (НСЗ и ОАО «МСЗ») и меткомбинатом «Азовсталь» используется технология индукционной поверхностной закалки остряков и рельсов. С целью уменьшения коробления рельса при закалке применяется упруго-пластический выгиб рельса и остряка головкой вверх [19, 62, 69]. Однако как было указано в 1.1.2 данная технологическая операция помимо негативного влияния на напряженно- деформированное состояние в головке остряка и на рост поверхностных трещин не обеспечивает прямолинейности изделия, что вынуждает прибегать к холодной механический правке на штемпельном прессе. Неблагоприятная эпюра внутренних остаточных напряжений после правки, а именно наличие растягивающих напряжений в головке или подошве остряка, приводит к короблению остряка в процессе эксплуатации.
При эксплуатации возможно перераспределение внутренних остаточных напряжений по сечению остряка. Пластическая деформация слоев металла, прилегающих к поверхности катания, приводит к изменению остаточного напряженного состояния в головке. В процессе эксплуатации там могут возникать остаточные сжимающие напряжения, доходящие до 500 МПа на поверхности, быстро снижающиеся по глубине и переходящие в растягивающие на глубине 4-5 мм, которые могут достигать 200 МПа [77].
В качестве предположения следует отметить, что выявленный в работе [78] факт, что упругая часть упругопластической деформации, происходящей при доправке объемно закаленного рельса на прессе, приводит к частичному возврату коробления после некоторого времени вылеживания, возможно характерен и для поверхностно закаленных остряков.
Сравнение конструктивной прочности и механических свойств рельсов, термообработанных различным способом проведено в [79]. Для сравнения использовали рельсы упрочненные водовоздушной смесью с индукционным нагревом на меткомбинате «Азовсталь», а также рельсы без термообработки и рельсы объемно закаленные в масле.
Рельсы с дифференцированной прочностью по сечению (упрочненные индукционной закалкой) характеризуются более высокими значениями по ряду свойств. Характерными являются повышенные значения предела выносливости и живучести по сравнению с объемно-закаленными рельсами за счет более благоприятной эпюрой внутренних остаточных напряжений.
Явление коробления рельса или остряка при индукционной закалке и необходимость последующей механической правки представляют собой серьезную проблему, кардинальное решение которой откроет дальнейшие перспективы повышения потребительских свойств рельсов и остряков, упрочненных индукционной закалкой.
Наиболее эффективным решением проблемы предотвращения коробления рельсов и остряков при индукционной поверхностной закалке и устранения операции предварительного выгиба представляется реализация схемы двухстороннего нагрева и закалочного охлаждения, при которой одновременному непрерывно-последовательному нагреву и охлаждению подвергаются головка и подошва рельса и остряка.
В отечественной науке впервые было предложено упрочнять подошву рельса в конце 30-х годов Н.П. Щаповым и A.C. Маханеком [80]. Авторами предлагалось упрочнение подошвы предпочтительно с индукционным нагревом в сочетании с поверхностной закалкой головки. При этом предполагалось увеличение прочностных свойств по сечению рельса за счет наличия упрочненного слоя в подошве и повышение ударной вязкости в наиболее напряженных при эксплуатации волокнах подошвы. Кроме того, снижалась чувствительность рельсов к влиянию различных пороков подошвы, повышалась надежность.
Одним из своеобразных вариантов дифференцированного двухстороннего охлаждения следует считать разработку, проведенную Нижнетагильским металлургическим комбинатом, Уральским филиалом ЦНИИ МПС и Уральским институтом черных металлов [81], направленную на предотвращение коробления концов объемно закаленных рельсов и устранение механической правки концов рельсов и их последующей релаксации в эксплуатации. При охлаждении рельса осуществляется подстуживание подошвы рельса, нагретого до температуры закалки, специальным спрейером.
Двухсторонняя схема термической обработки принята в качестве основной у многих зарубежных производителей рельсов. Двухсторонний нагрев лежит в основе технологии индукционной поверхностной закалки рельсов на заводе фирмы «British Steel» [82]. Для нагрева используется установка мощностью 700 кВт с частотой 2 кГц с четырьмя индукторами. Три индуктора используются для нагрева головки и один для нагрева подошвы с целью коррекции прогиба рельса. После закалки отмечается незначительная величина деформации.
Двухстороннее охлаждение сжатым воздухом после сквозного индукционного нагрева применяет в качестве термической обработки рельсов фирма «Sogerail» (Франция). После такой термической обработки рельсы производства «Sogerail» не нуждаются в правке и характеризуются наличием остаточных сжимающих напряжений в головке и подошве [83].
В отечественной технике новый способ упрочнения рельсов с использованием принципа двухстороннего закалочного охлаждения разработан и опробован во ВНИИЖТ [84].
Для упрочнения проб рельсов типа Р65 длиной 600 мм с предварительного нагрева в газовой печи было разработано закалочное устройство, обеспечивающее подачу воды на головку и подошву рельса под углом 45°, при одновременном экранировании шейки и верхней поверхности подошвы рельса от попадания воды. В процессе отработки режима закалки регулировали соотношение подачи воды через верхнее и нижнее охлаждающие устройства и время охлаждения. Экспериментально было установлено, что для получения необходимых свойств в головке и подошве рельсов и для отсутствия искривления подача воды на головку должна быть в 4-6 раз больше, чем на подошву. Правильно подобранные режимы охлаждения головки и подошвы рельса обеспечили компенсацию напряжений и деформаций при закалке, что позволило сохранить рельс прямолинейным.
Исследование микроструктуры опытных рельсов показало, что в поверхности головки и подошвы рельсов присутствует структура сорбита отпуска, а в шейке — структура пластинчатого перлита. Уровень прочностных свойств в головке и подошве опытных рельсов выше аналогичных характеристик для рельсов, объемно закаленных в масле. При этом пластичность сохранена на том же уровне.
Оценка износостойкости по схеме трения качения с поперечным проскальзыванием на образцах-роликах, вырезанных непосредственно с поверхности рельсов и на глубине 10 мм от поверхности катания, показала, что износостойкость опытных рельсов выше, чем стандартных, как у поверхности, так и на глубине. Исследования внутренних остаточных напряжений методом вырезки поперечного темплета с наклеенными тензодатчиками показали, что применение закалки быстродвижущимся потоком воды при двухсторонней схеме закалочного охлаждения формирует более благоприятную эпюру внутренних остаточных .напряжений — напряжения сжатия в головке и подошве до 200 МПа. Последнее обстоятельство обусловило более высокую циклическую долговечность опытных рельсов. Сравнительные усталостные испытания показали, что применение новой технологии термический обработки при испытании образцов с концентраторами напряжений повышает предел выносливости рельсов типа Р65 с 400 кН при стандартной термообработке до 500 кН.
По результатам проведенных исследований новая технология двухсторонней закалки рельсов быстродвижущимся потоком воды была одобрена на научно-техническом совещании и принята в качестве приоритетной при реконструкции термического отделения Нижнетагильского металлургического комбината.
Таким образом, анализ опытных и промышленных технологий термической обработки рельсов и остряков, исследования их физико-механических свойств и конструктивной прочности позволяет сформулировать основные принципы новой технологии термической обработки остряков, закладываемые в основу разработки технологического оборудования для закалки остряков:
- Остряк устанавливается на закалочном стенде без выгиба.
- Индукционный непрерывно-последовательный нагрев и охлаждение должны проводиться одновременно для головки и подошвы остряка с использованием самостоятельных (независящих друг от друга по регулированию основных технологических параметров) индукторов и устройств воздушного охлаждения.
- С целью обеспечения прямолинейности остряка компенсация термических и структурных напряжений и деформаций в процессе нагрева и охлаждения должна осуществляться за счет регулирования мощности индукторов при нагреве и подачи сжатого воздуха при охлаждении головки и подошвы остряка. В соответствии с этим установка должна включать в себя устройство программного регулирования нагрева.
Предпосылки и принципы разработки нового состава стали для остряков
Общие принципы легирования
Основной целью легирования углеродистой рельсовой стали является повышение глубины прокаливаемости, прочностных характеристик и износостойкости поверхности катания.
В работе [85] показано, что выбор тех или иных легирующих элементов и их содержания при разработке новых составов сталей определяется влиянием легирующих элементов на физико-механические свойства стали. Так, в соответствии с теорией предельного легирования А.П. Гуляева [86 — 88] основная цель легирования конструкционных сталей — достижение требуемой прокали- ваемости. Когда содержание легирующих элементов превышает необходимое для получения сквозной прокаливаемости в данном сечении, легирование оказывает отрицательное влияние на свойства сталей, в частности на порог их хладноломкости.
М.П. Браун [89, 90] высказал другую точку зрения, согласно которой оптимальное соотношение легирующих элементов в стали позволяет за счет упрочняющего их влияния на кристаллическую решетку железа, плотность и распределение дислокаций, тонкую структуру феррита (размер и разориентировку блоков), а также вследствие изменения состава, формы и распределения карбидной фазы получить при одинаковой прочности более высокие пластичность и ударную вязкость.
К общей тенденции влияния на свойства углеродистой стали таких распространенных легирующих элементов как кремний, марганец, хром, ванадий следует отнести повышение прочностных свойств и твердости, уменьшение характеристик пластичности и вязкости, увеличение склонности к отпускной хрупкости, повышение порога хладноломкости. Испытания показали, что в стали с 0,23-0,26 % углерода никель увеличивает ударную вязкость, хром не оказывает существенного влияния на этот параметр, а марганец при увеличении его содержания от 1,6 до 4,5 % уменьшает запас вязкости [91].
Наиболее часто используемые при легировании рельсовой стали элементы, влияют на ее свойства следующим образом.
Кремний. Легирование стали кремнием сопровождается повышением показателей прочности при одновременном незначительном снижении относительного сужения и сохранении относительного удлинения примерно на одном и том же уровне.
Общий характер действия кремния на механические свойства улучшенной стали связан с влиянием на свойства феррита. Кремний сильно замедляет процесс укрупнения карбидов при отпуске и потому увеличивает устойчивость стали против отпуска, способствуя достижению при одинаковой температуре отпуска более высоких показателей прочности.
Ударная вязкость при содержании в стали кремния 1,5 % и более резко снижается [91]. Исследованиями В.Д. Садовского [92] установлено, что кремний отрицательно влияет на ударную вязкость сорбита. С увеличением содержания кремния падает температурный запас вязкости. Это особенно заметно при повышении в стали содержания углерода (свыше 0,4 %) и марганца (свыше 1,2%).
Марганец. С увеличением содержания в стали марганца временное сопротивление несколько возрастает, а относительное удлинение снижается. С возрастанием в низкоуглеродистой стали содержания марганца с 0,07 до 1,83 % порог ее хладноломкости смещается в сторону отрицательных температур. Дальнейшее увеличение содержания марганца до 2,2 % ухудшает свойства стали. Ударная вязкость образцов, содержащих 0,6-1,3 % марганца, превосходит свойства образцов с более низким (0,2 %>) или более высоким (свыше 2 %) содержанием марганца [93].
Ванадий. Присутствие ванадия в количестве 0,2 % и более вызывает значительное повышение устойчивости стали против отпуска. Ванадиевые стали обнаруживают также повышенную кратковременную и длительную прочность в нагретом состоянии. Однако этот эффект, обусловленый в основном процессами карбидообразования, наблюдается только в термически улучшенном состоянии и при условии, если рабочая температура стали не превосходит 450 °С. Хром. Исследование влияния добавок хрома на комплекс физико — механических свойств углеродистой стали достаточно широко представлено в соответствующей научно — технической литературе [94-100]. Положительное влияние хрома на прокаливаемость, прочностные характеристики и твердость углеродистой стали объясняют склонностью хрома к карбидообразованию. За счет большой энергии сродства к углероду хром затрудняет его диффузионное перемещение, что и обуславливает уменьшение склонности аустенита к диффузионному распаду в интервале температур его наименьшей устойчивости (723 — 550 °С) и снижение критической скорости охлаждения в указанном интервале температур, то есть обуславливает увеличение прокаливаемости стали [94, 96]. Наиболее резкое снижение критической скорости закалки углеродистой стали хром вызывает при содержании до 1,0-1,5 % [96]. Прокаливаемость инструментальной углеродистой стали (1,0 % С) при относительно небольших содержаниях хрома (до 0,40 %) возрастает пропорционально его содержанию [101]. На рис. 1.6 приведены диаграммы изотермических превращений хромистой стали с различным содержанием хрома [94]. При увеличении содержания хрома до 3,5 % диаграммы смещаются в сторону больших времен до начала превращения, т.е. в сторону большей устойчивости аустенита.
Хром — сильный карбидообразующий элемент, однако при содержании хрома менее 1 % специальные карбиды Сг2зСб и Сг7С3 практически не образуются. Хром полностью переходит в твердый раствор, образуя при распаде легированный цементит (Fe,Сг)3С, пластины которого входят в состав перлитных колоний [97]. На этом основано упрочняющее действие хрома. При увеличении содержания хрома в твердом растворе на 1 % предел текучести углеродистой стали увеличивается на 30 МПа, а временное сопротивление на 28 МПа [98].
В нормализованном состоянии пластичность стали под влиянием хрома не меняется до его содержания 0,9 %, после чего происходит снижение относительного удлинения, сужения и ударной вязкости. Влияние хрома на ударную вязкость в нормализованном состоянии при отри i отельных температурах не замечено до его содержания 0,9 %, после чего вязкость снижается [102]. Контактная усталость стали с ростом содержания хрома так же, как и твердость, повышается.
Влияние хрома на микроструктуру углеродистой стали, полученную в результате охлаждения с различными скоростями изучено в работе [99]. Были исследованы стали, содержащие 0,62, 0,96 и 1,0 % хрома.
Установлено, что в отличие от углеродистых сталей, где структурно свободный феррит располагается в виде сетки по границам зерен, в хромистой стали феррит образует отдельные зерна — конгломераты.
Структуры промежуточного превращения характеризуются для хромистой стали большей степенью дисперсности.
Сравнительное исследование микротвердости в работе [99] показало, что хром, являясь карбидообразующим элементом, упрочняет перлитную составляющую.Так уровень микротвердости перлита в хромистой стали равен 2740 — 3240 МПа, а в углеродистой стали — 2550 — 2840 МПа.
Предпосылки применения низколегированных рельсовых сталей
Ранее проведенными во ВНИИЖТ исследованиями установлено, что наилучшее сочетание свойств, определяющих надежность и долговечность рельсов, достигается в результате термической обработки их на структуру сорбит закалки с твердостью 341-388 НВ. Дальнейшее повышение прочности возможно за счет создания структуры троостита отпуска с твердостью 420-450 НВ. В соответствии с поставленными требованиями и особенностями термической обработки рельсов на различных предприятиях — производителях были предложены различные химические составы рельсовой стали. УралНИИчермет применительно к существующей на НТМК технологии объемной закалки рельсов в масло с отпуском предложил для производства высокопрочных рельсов сталь типа 35-40Х2ФА, в которой пониженное содержание углерода было частично компенсировано введением в сталь азота и нитридообразующих элементов (ванадия и алюминия). Присутствие в стали около 2 % хрома обеспечивало при этом достаточную прокаливаемость головки рельса при термической обработке [103]. После закалки в масло и отпуска твердость поверхности таких рельсов составила 420-440 НВ. Однако полигонные испытания на Экспериментальном кольце ВНИИЖТ показали, что рельсы характеризуются низкой контактно-усталостной прочностью из-за загрязненности стали строчечными включениями оксидов и нитридов и недостаточного содержания углерода.
Для производства рельсов с их последующей изотермической закалкой были предложены стали, легированные хромом (0,5-1,0 %), кремнием (0,6 — 0,9 %) и одновременно марганцем, кремнием и хромом (0,8-1,2% Мп, 0,5-0,9 % Si, 0,5-1,0 % Сг) [104]. После изотермической закалки в соли при температуре 280-320 °С рельсы имели высокую усталостную прочность при изгибном нагружении.
Наилучшие результаты в отечественной практике были получены при легировании рельсовой стали 1% хрома [105] и 0,5 — 0,7 % кремния [106]. Повышение прочностных свойств хромистой рельсовой стали по сравнению с углеродистой достигается только при достаточно высоком содержании углерода и марганца. Снижение температуры перлитного превращения при охлаждении за счет легирования хромом приводит к увеличению дисперсности получаемой структуры. Так величина средних межпластиночных расстояний в» перлите хромистой стали составляет 0,6 мкм, а в углеродистой — примерно 1,2 мкм [62]. Это повышает твердость хромистых рельсов в сравнении с углеродистыми (без термической обработки) с 260-270 НВ до 300-310 НВ, временное сопротивление с 900 — 1000 до 1020 — 1100 МПа. Износостойкость и контактно- усталостная прочность хромистых рельсов была на 20-25% выше, чем у стандартных углеродистых. Срок службы хромистых рельсов, лимитируемый их одиночным изъятием из пути в основном из-за дефектов контактной усталости, был на 20-25%) выше, чем у рельсов стандартного производства.
Анализ технологии производства рельсов ведущими зарубежными производителями (см. табл. 1.3) показывает, что наиболее высокие значения твердости и прочностных свойств характерны для рельсов из низколегированных марок сталей. Исследования химического состава рельсов производства фирмы SYSCo (Канада) показали, что основным легирующим элементом является
хром (0,45 %). Химический состав рельсов фирмы 8У8Со позволяет получать в результате индукционной закалки с охлаждением сжатым воздухом упрочненной слой со структурой сорбита закалки глубиной около 10 мм и твердость поверхности катания 400 НВ.
Таким образом, наиболее перспективным решением проблемы повышения износостойкости и прочностных свойств представляется внедрение низколегированной хромом стали.
Выводы
- Анализ повреждаемости остряков в эксплуатации показал, что основными видами повреждений являются боковой износ, выгиб, образование и выкрашивание гребнеобразного наплыва.
- Серийная технология не обеспечивает соответствие прочностных. свойств остряка современным требованиям эксплуатации по причинам: недостаточной прокаливаемости серийной марки стали М73В и низких прочностных свойств и твердости упрочненного слоя остряков; наличия вредной технологической операции упруго-пластического выгиба, приводящей к развитию поверхностных трещин, формированию неблагоприятной эпюры внутренних остаточных напряжений и короблению остряка в эксплуатации.
- Анализ литературных данных по исследованию влияния термической обработки на напряженное состояние и прямолинейность рельсов и изучение опыта термической обработки рельсов в промышленно развитых странах показали, что наиболее перспективным способом получения остряков с повышенной прямолинейностью и напряжениями сжатия в головке и подошве является технология двухсторонней поверхностной закалки, которая применима для остряков из любых марок сталей.
- Сформулированы общие принципы и технические требования к процессу двухсторонней индукционной закалки остряков без предварительного изгиба, включающие:
- установку остряка на закалочном стенде без выгиба;
- одновременный непрерывно-последовательный индукционный нагрев и охлаждение сжатым воздухом головки и подошвы остряка с контролем температуры нагрева и регулированием электрических параметров нагрева по длине остряка;
- разработку режимов нагрева и охлаждения, обеспечивающих получение внутренних остаточных напряжений сжатия в головке и подошве остряка и минимизацию последующей механической правки.
5. Анализ результатов проведенных ранее исследований по влиянию легирующих элементов на физико-механические свойства конструкционных углеродистых сталей с учетом экономических аспектов массового производства рельсов и остряков показал, что с целью повышения износостойкости и прочностных свойств остряков целесообразно использовать низколегированную рельсовую сталь с повышенным содержанием хрома (0,35-0,55%).